Discover Premium Ceramic Products | Durability & Elegance United | Advanced Ceramics
PRODUCT PARAMETERS
Description
Overview of Aluminum Nitride Ceramic Substrate
Aluminum nitride (AlN) ceramic substrates are specialty components designed for high-performance electronics and semiconductor applications. These substrates leverage the unique properties of aluminum nitride to provide superior thermal management, electrical insulation and mechanical stability. Here is a comprehensive overview of aluminum nitride ceramic substrates:
Main characteristics of Aluminum Nitride Ceramic Substrate
1. High thermal conductivity: One of the most significant advantages of aluminum nitride substrates is their excellent thermal conductivity, which can range from 170 to 220 W/m-K. This makes it ideal for efficient cooling applications.
2. Excellent electrical insulation properties: Despite its high thermal conductivity, aluminum nitride substrates can still maintain excellent electrical insulation properties, making them suitable for environments that require high dielectric strength.
3. Low coefficient of thermal expansion (CTE): The thermal expansion coefficient of aluminum nitride (approximately 4.5-5.0 ppm/°C) is very close to that of silicon, which can minimize thermal mismatch stress and improve thermal stability affected by temperature fluctuations. Semiconductor device reliability.
4. Chemical stability: Aluminum nitride substrates have excellent chemical resistance, including acid, alkali and molten metal resistance, ensuring durability even in corrosive environments.
5. Mechanical strength: Although aluminum nitride substrate is a brittle material, its hardness and strength are sufficient to meet the needs of many industrial applications. However, they need to be handled with care to avoid damage from impact or excessive stress.
6. Density: The density of AlN is approximately 3.26 g/cm3, making it lightweight compared to some other ceramic materials.
7. Purity: High purity options are available, often exceeding 99%, to improve thermal and electrical performance.
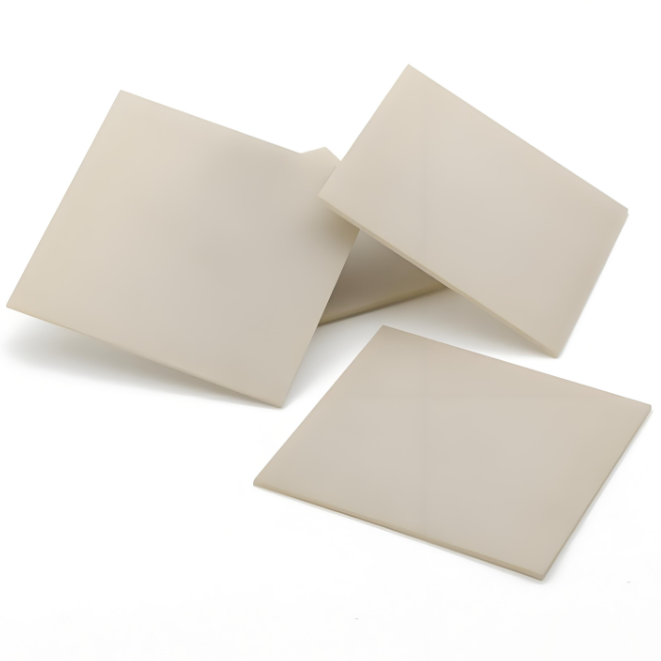
Specification of Aluminum Nitride Ceramic Substrate
Property | Typical Specification |
Material Composition | AlN (Aluminum Nitride) |
Thermal Conductivity | 170-220 W/m·K |
Coefficient of Thermal Expansion | ~4.5-5.0 ppm/°C (similar to silicon) |
Dielectric Strength | >20 kV/mm |
Dielectric Constant (1 MHz) | ~8.4 – 9.6 |
Volume Resistivity | >10^14 Ω·cm at 25°C |
Mechanical Strength (Bending) | ~350-450 MPa |
Hardness (Vickers) | ~12-14 GPa |
Density | ~3.26 g/cm³ |
Porosity | <1% |
Operating Temperature Range | -269°C to +1000°C |
Chemical Stability | Excellent resistance to acids, alkalis, and molten metals |
Surface Finish | Can be polished to optical quality or left with a machined finish |
Dimensions | Customizable; typical thickness ranges from 0.5 mm to several millimeters, with various length and width options |
Purity | High purity options available (e.g., >99%) |
Thermal Shock Resistance | Good thermal shock resistance due to low CTE and high thermal conductivity |
Outgassing Characteristics | Low outgassing, suitable for vacuum applications |
Applications of Aluminum Nitride Ceramic Substrate
Electronics and Semiconductors
1. Radiator: Effectively dissipates heat for sensitive electronic components in power modules, LEDs, laser diodes, RF equipment and microwave equipment.
2. Power module substrate: As the substrate of the power module, efficient heat dissipation and electrical isolation are crucial to ensure reliable operation under thermal stress.
3. Insulating layer: Provides electrical insulation while allowing efficient heat transfer between electronic components, improving performance and service life.
4. High-power LED: Used in high-power LED packaging to effectively manage heat and improve brightness and lifespan.
5. Laser diode For laser diode packaging, it has excellent thermal management characteristics to ensure stable operation and service life.
6. RF devices: Used in RF devices such as filters and resonators because they have low dielectric loss and excellent thermal stability, which are critical to maintaining high-frequency signal integrity.
Automotive industry
1. Sensor assembly: protects sensors in harsh environments such as exhaust systems, fuel lines, and engine compartments. They can withstand high temperatures and corrosive environments.
2. Ignition system: used in ignition systems that must withstand extreme temperatures and provide reliable electrical insulation.
3. Power Electronics: Used in power electronic components such as inverters and converters, effective thermal management is critical to reliability and performance.
telecommunications
1. Microwave devices: Used in microwave devices such as filters and resonators because they have low dielectric loss and excellent thermal stability, which is critical to maintaining signal integrity at high frequencies.
2. Satellite communications systems: Used in satellite components because they are lightweight and can withstand extreme heat, helping to improve the reliability of space-based communications equipment.
medical equipment
1. Implants and diagnostic devices: Due to its biocompatibility and resistance to body fluids, AlN substrates can be used in certain medical implants or diagnostic devices that require stable thermal and electrical properties.
2. Laser Surgery Tools: Surgical tools and equipment used in laser surgery benefit from their thermal stability and durability.
High temperature applications
1. Furnaces and Kilns: Used as structural components, supports, or gaskets in furnaces and kilns, utilizing their thermal stability and chemical resistance to withstand high temperatures and corrosive environments.
2. Metallurgical Processes: Used in processes involving molten metal as they are resistant to chemical attack by the molten material.
Optoelectronics
1. Optical Windows and Lenses:Benefiting from their transparency in certain wavelengths and thermal stability, AlN substrates can be used in optoelectronic devices like optical windows and lenses.
Laser Technology
1. Laser Components:As substrates or components in laser technology, benefiting from their thermal conductivity and mechanical strength.
Aerospace and Defense
1. Avionics and Spacecraft Components:Utilized in avionics and spacecraft components where reliable operation under extreme conditions is critical.
2. Radar Systems:Used in radar systems for their electromagnetic compatibility and thermal stability.
Company Profile
Advanced Ceramics founded on October 17, 2012, is a high-tech enterprise committed to the research and development, production, processing, sales and technical services of ceramic relative materials and products.. Since its establishment in 2012, the company has been committed to providing customers with the best products and services, and has become a leader in the industry through continuous technological innovation and strict quality management.
Our products includes but not limited to Aluminum Nitride Ceramic Products, Boron Carbide Ceramic Products, Boron Nitride Ceramic Products, Silicon Carbide Ceramic Products, Silicon Nitride Ceramic Products, Zirconium Dioxide Ceramic Products, Quartz Products, etc. Please feel free to contact us.(nanotrun@yahoo.com)
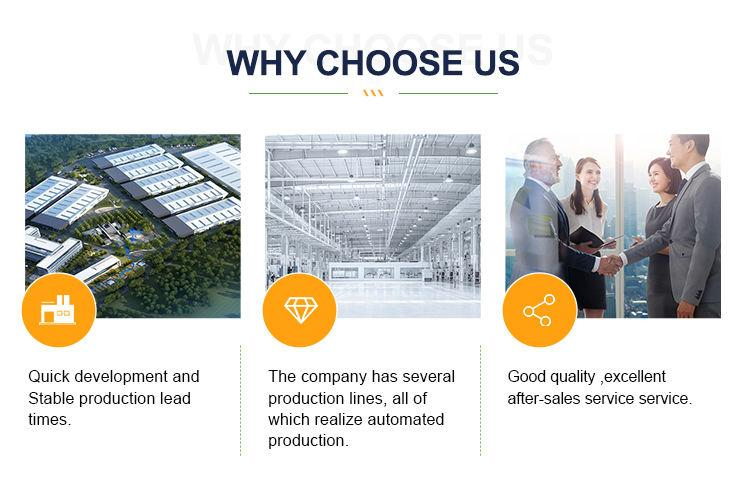
Payment Methods
T/T, Western Union, Paypal, Credit Card etc.
Shipment Methods
By air, by sea, by express, as customers request.
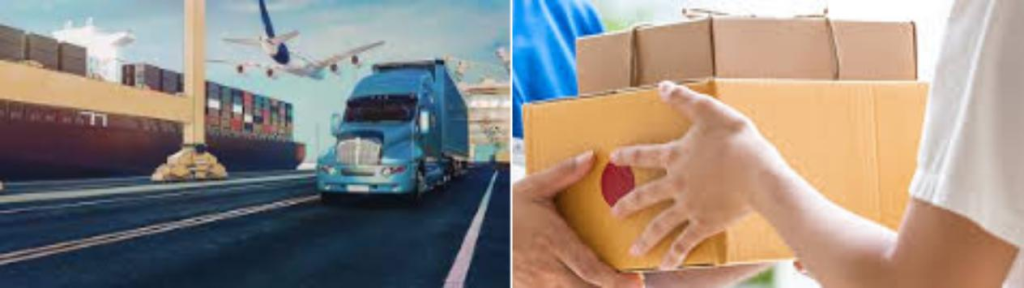
FAQs of Aluminium Nitride Ceramic Substrate Plate:
Q1: Why are AlN ceramic substrate plates superior to other ceramics?
A1: AlN ceramic substrate plates offer higher thermal conductivity compared to materials like aluminum oxide (Al₂O₃), making them better for heat dissipation. They also provide excellent electrical insulation, chemical stability, and a CTE close to silicon, minimizing thermal mismatch stresses.
Q2: Where are AlN ceramic substrate plates commonly used?
A2: Common applications include:
- Heat sinks
- Substrates for power modules, LEDs, laser diodes, RF devices, and microwave devices
- Automotive sensors and ignition systems
- Microwave devices and satellite communication systems
- Medical implants and diagnostic equipment
- Furnaces, kilns, optical windows, and laser technology components
Q3: Can AlN ceramic substrate plates be customized?
A3: Yes, AlN ceramic substrate plates can often be customized in terms of dimensions (length, width, thickness), surface finish, and even material composition to suit specific application requirements.
Q4: Are AlN ceramic substrate plates expensive?
A4: Generally, AlN ceramic substrate plates are more expensive than simpler ceramics due to their superior properties and complex manufacturing process. Costs can vary based on size, shape, and customization.
Q5: What surface finishes are available for AlN ceramic substrate plates?
A5: Surface finishes can vary from rough to polished to optical quality, depending on the application needs. Polished surfaces are common for applications requiring high precision and minimal surface roughness.
REQUEST A QUOTE
RELATED PRODUCTS
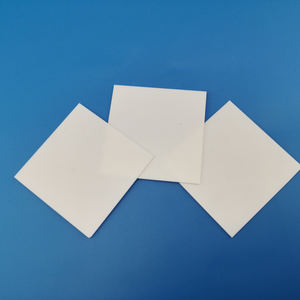
Industry Electrical CNC Machining Ceramic Parts Aluminum Nitride Ceramic ALN Heat Sink for CPU LED
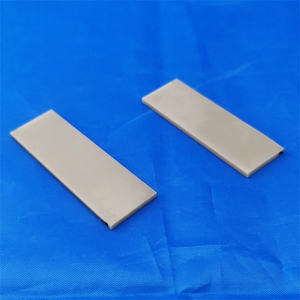
High Heat Conductivity AlN Aluminum Nitride Ceramic Sheet
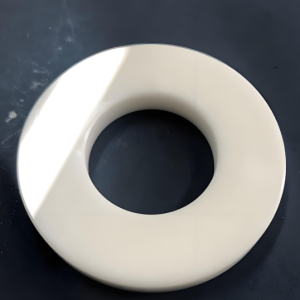
High Thermal Conductivity AlN Aluminum Nitride Ceramic Rings
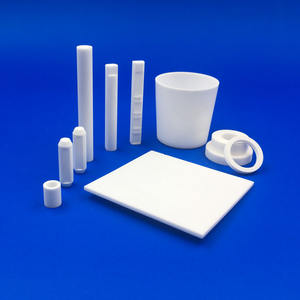
AlN Heater with TC Aluminum Nitride Heat Element Ceramic Plates 220V
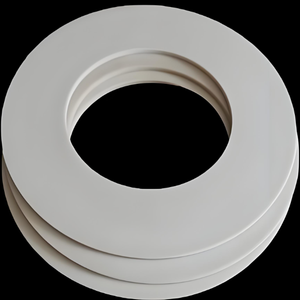
High Purity 99.95% Aluminum Nitride AlN Spherical Powder 3-5um Ceramic Microspheres Durable Heat Conductive Material
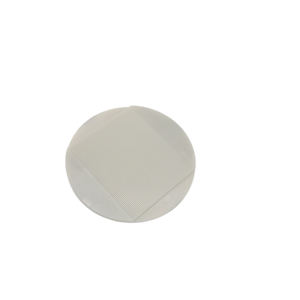