Discover Premium Ceramic Products | Durability & Elegance United | Advanced Ceramics
PRODUCT PARAMETERS
Description
Overview of Zirconia ball
Zirconia balls, also known as zirconium dioxide (ZrO2) balls or ceramic balls, are spherical objects made from a type of ceramic material that is primarily composed of zirconium oxide.
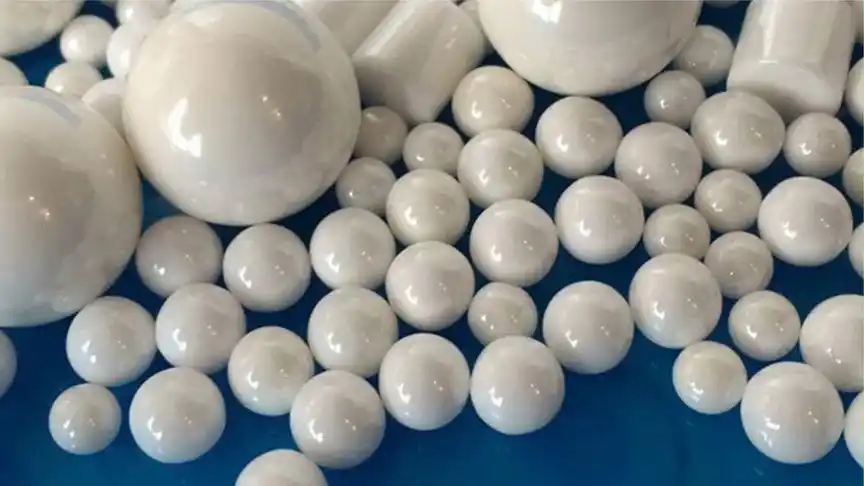
Features of Zirconia ball
High Hardness and Wear Resistance:Zirconia balls have excellent hardness and wear resistance, which makes them suitable for use in applications where there is a lot of friction or abrasive conditions.
Chemical Stability:These balls show good chemical stability and resistance to corrosion by many acids and alkalis, making them useful in harsh chemical environments.
High Temperature Resistance:They can withstand high temperatures without losing structural integrity, which is beneficial for high-temperature applications.
Low Thermal Expansion:Zirconia has a low coefficient of thermal expansion, which means it expands minimally when heated. This property helps to minimize the risk of cracking or deformation under temperature changes.
Biocompatibility:Due to their biocompatibility, zirconia balls are sometimes used in medical applications, such as artificial joints.
Density:Zirconia balls are relatively dense, which can be advantageous for certain grinding and milling applications where weight contributes to the effectiveness of the process.
Electrical Insulation:They provide good electrical insulation properties.
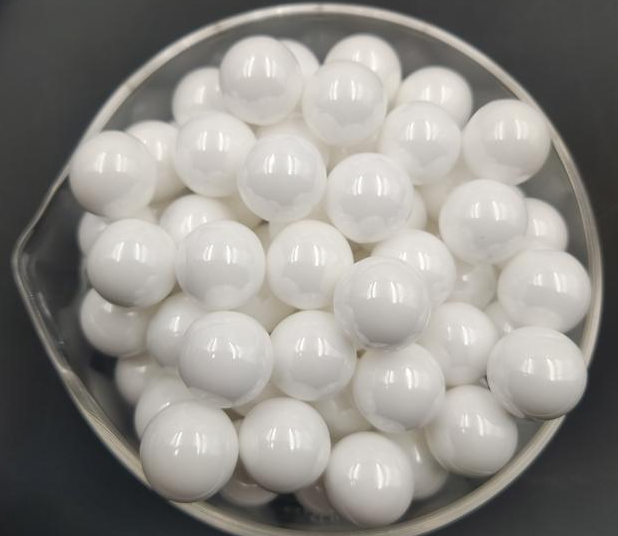
Specifications of Zirconia Ball
Parameter | Description | Typical Values/Range |
Chemical Composition | Primary component is ZrO2, with possible stabilizers added | ZrO2 ≥ 95%, Stabilizers like Y2O3 |
Density | Mass per unit volume of the material | 5.8 – 6.1 g/cm³ |
Hardness | Resistance to permanent deformation | Vickers Hardness: 1200 – 1400 HV |
Corrosion Resistance | Ability to resist chemical attack | Resistant to most acids and bases |
Size Range | Diameter of the spheres | 1mm, 3mm, 5mm, 10mm, 15mm, 20mm, etc. |
Roundness | Precision of spherical shape | High precision, minimal error |
Surface Finish | Surface roughness | Ra < 0.05 μm |
Thermal Stability | Stability under high temperatures | Excellent thermal stability |
Color | Appearance color | White or off-white |
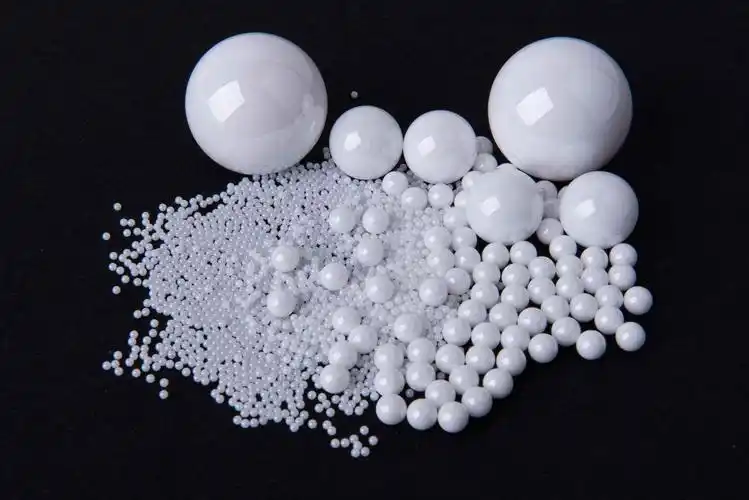
Zirconia ball
Manufacturing Methods of Zirconia Ball
1. Powder Metallurgy Process
This is one of the most widely used methods for manufacturing zirconia ceramics, including zirconia balls.
Mixing: The process begins with mixing high-purity zirconia powder with stabilizers (like yttria or magnesia) and sometimes binders to improve processing.
Forming: The mixed powder is then shaped into spherical forms through various techniques such as:
Pressing: Cold isostatic pressing (CIP) or dry pressing can be used to form green bodies with precise dimensions.
Injection Molding: A method that allows for complex shapes but is less common for simple spheres.
Slurry Dropping: A slurry of zirconia powder in a liquid medium is dropped into a coagulating bath to form spherical particles.
Sintering: The formed green bodies are sintered at very high temperatures (typically around 1400°C to 1600°C). This process densifies the material, enhancing its mechanical properties and achieving the final hardness.
Grinding and Polishing: After sintering, the balls may undergo grinding and polishing to achieve the required size, shape accuracy, and surface finish.
2. Sol-Gel Process
A chemical process that involves the transformation of monomers into a solid via a sol (solution) and gel state.
Solution Preparation: Zirconium alkoxide is dissolved in a solvent, and water is added to initiate hydrolysis and polycondensation reactions.
Gel Formation: As the reaction progresses, a gel network forms.
Drying and Calcination: The wet gel is dried and then calcined at high temperatures to remove any organic components and consolidate the structure.
Milling and spheroidization: The calcined material is milled and shaped into spheres, often followed by further sintering.
3. Hot Isostatic Pressing (HIP)
Used for creating extremely dense and strong ceramic components.
Loading: Pre-formed zirconia parts are loaded into a pressure vessel.
Pressurizing and Heating: The vessel is filled with an inert gas and heated while applying isotropic pressure. This process helps eliminate porosity and enhances density and strength.
Cooling: After reaching the desired density and properties, the parts are cooled under controlled conditions.
4. Spray Pyrolysis
A method suitable for producing fine, uniform spherical particles.
Spraying: A solution containing zirconia precursors is sprayed into a hot furnace.
Instant Solidification: The droplets solidify instantly upon contact with the hot atmosphere, forming spherical particles.
Collection and Post-processing: The particles are collected and may undergo additional processing like sintering for increased density.
Applications of zirconia ball
Bearing Balls:
Zirconia balls are used in precision bearings where they provide superior performance over traditional metal bearings in corrosive or abrasive environments.
Grinding Media:
They are extensively used in ball mills for fine grinding of materials like paints, pigments, chemicals, and pharmaceuticals due to their hardness and density.
Valves and Seals:
Utilized in severe service valves and seals where resistance to wear and corrosion is critical.
Pumps:
Components like pump balls, seats, and plungers benefit from the wear-resistant properties of zirconia.
Machinery Components:
Used in parts that require high wear resistance and low friction, such as guides, rollers, and bushings.
Grinding Balls:
Commonly used as grinding media in laboratory-scale ball mills for sample preparation.
Mixing and Homogenization:
Employed in mixing and homogenizing compounds for research and development purposes.
Analytical Instruments:
Used in components of analytical instruments where contamination must be minimized.
Medical and Dental Applications
High-Performance Bearings:
Utilized in aerospace bearings where reliability under extreme conditions is paramount.
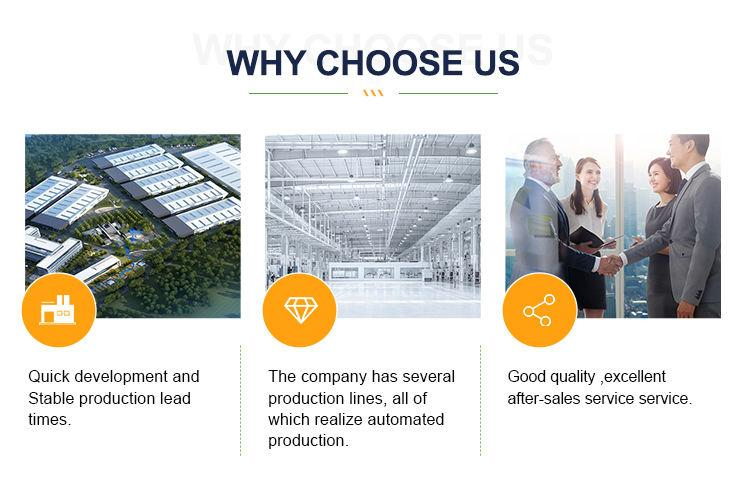
Company Profile
Advanced Ceramics founded on October 17, 2014, is a high-tech enterprise committed to the research and development, production, processing, sales and technical services of ceramic relative materials and products.. Since its establishment in 2014, the company has been committed to providing customers with the best products and services, and has become a leader in the industry through continuous technological innovation and strict quality management.
Our products includes but not limited to Silicon carbide ceramic products, Boron Carbide Ceramic Products, Boron Nitride Ceramic Products, Silicon Carbide Ceramic Products, Silicon Nitride Ceramic Products, Zirconium Dioxide Ceramic Products, Quartz Products, etc. Please feel free to contact us.(nanotrun@yahoo.com)
Payment Methods
T/T, Western Union, Paypal, Credit Card etc.
Shipment Methods
By air, by sea, by express, as customers request.
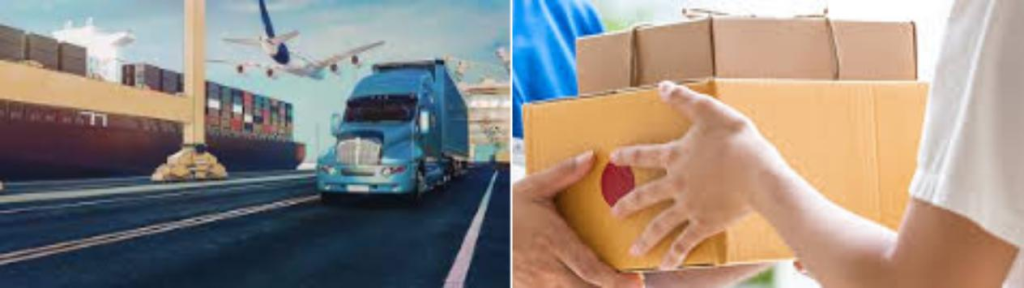
FAQs of Zirconia ball
1. Why is zirconia used in ball form?
A: The spherical shape maximizes the material’s hardness, wear resistance, and density, making it ideal for applications requiring precision and durability, such as bearings and grinding media.
2. Can zirconia balls withstand high temperatures?
A: Yes, zirconia balls can withstand extremely high temperatures, with a melting point of around 2700°C, and maintain structural integrity under thermal stress due to their low coefficient of thermal expansion.
3. Can zirconia balls be used in medical implants?
A: Yes, zirconia balls are biocompatible and are used in orthopaedic implants and dental materials due to their durability and compatibility with human tissue.
4. How are zirconia balls manufactured?
A: They are typically manufactured through processes like injection moulding, isostatic pressing, and sintering, which involve shaping the material into spheres and then firing them at high temperatures to achieve the desired properties.
5. Do zirconia balls require special maintenance?
A: Generally, no special maintenance is required; however, they should be inspected periodically for signs of wear or damage, especially in critical applications.
REQUEST A QUOTE
RELATED PRODUCTS
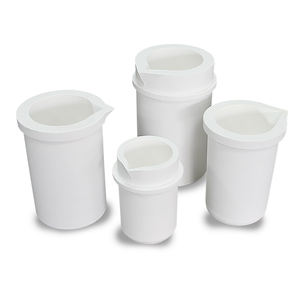
ZrO2 Zirconium Oxide Powder Ceramic Material for the Production of High Grade Yttrium Stabilized Zirconia Powder
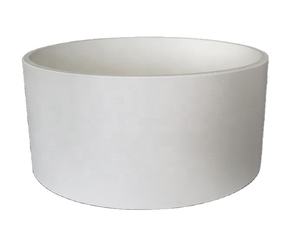
ZrO2 Zirconia Cageless All Ceramic Full Complement Balls Ceramic Bearing 6012 6013 6014 6015
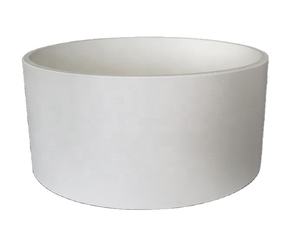
Yttria Stabilized Zirconia YSZ Yttrium Stabilized Zirconium Oxide Powder for Industrial Ceramic
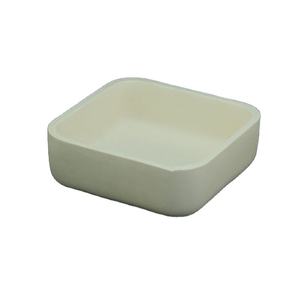
Wear Resistant Zirconia ceramic Heat-insulation Pipe

Yttria Stabilized 95 ZrO2 Zirconium Oxide Zirconia Ceramic
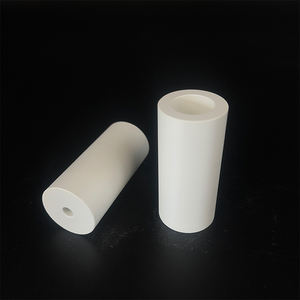