Discover Premium Ceramic Products | Durability & Elegance United | Advanced Ceramics
PRODUCT PARAMETERS
Description
Overview of Alumina Crucible
An alumina crucible is a high-temperature, heat-resistant container made primarily from alumina (aluminum oxide, Al₂O₃). Alumina is known for its excellent thermal stability, resistance to chemical reactions, and ability to withstand extreme temperatures, making it an ideal material for a variety of industrial and laboratory applications. Alumina crucibles are commonly used in processes that require high-temperature heating, such as metal melting, material testing, and chemical reactions.
Alumina crucibles come in various sizes and shapes, depending on the specific application. They are typically used in industries like metallurgy, ceramics, glass production, and scientific research.
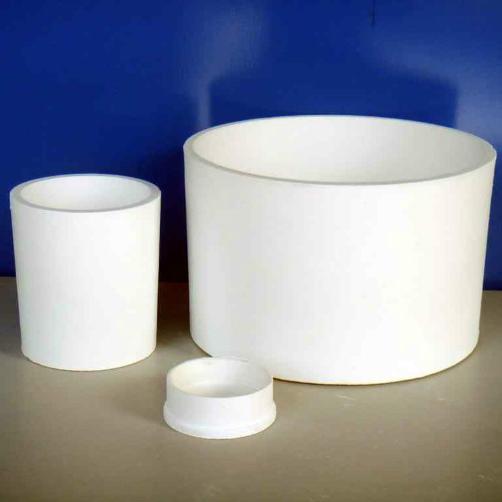
Features of Alumina Crucible
- High Temperature Resistance: Alumina crucibles can withstand temperatures up to 1700°C (3092°F), making them suitable for a wide range of high-heat applications.
- Chemical Resistance: Alumina is highly resistant to most acids, alkalis, and other corrosive materials, ensuring the crucible does not react with the substances being processed.
- Thermal Shock Resistance: Alumina crucibles can handle rapid changes in temperature without cracking or breaking, which is crucial when working with extreme heat.
- Electrical Insulation: Alumina has excellent electrical insulating properties, which is important in certain electrical and electronic applications.
- Durability: The high mechanical strength of alumina ensures that the crucible is durable and can endure prolonged use without significant degradation.
- Non-reactive Surface: Alumina’s inert surface prevents contamination of the materials being heated, making it ideal for high-purity processes.
- Lightweight: Despite their strength, alumina crucibles are relatively lightweight, which makes handling easier.
Specifications of Alumina Crucible
Specification | Description |
Material | High-purity Alumina (Al₂O₃) |
Purity | 99.5% – 99.99% (depends on the manufacturer) |
Temperature Resistance | Up to 1600°C (varies by grade, some can withstand higher) |
Density | 3.90 – 4.00 g/cm³ |
Porosity | Low, typically ≤ 0.1% (varies by manufacturing process) |
Size Range | From 1 mL to several liters (custom sizes available) |
Shape | Typically cylindrical, but can also be square, rectangular, or custom shapes |
Wall Thickness | Generally 3-6 mm, but can vary based on size and application |
Thermal Conductivity | 15 – 30 W/m·K at room temperature |
Expansion Coefficient | 7.5 × 10⁻⁶ /°C (from 25°C to 1200°C) |
Electrical Resistivity | High resistance, non-conductive |
Application | Melting and holding metal, chemical analysis, high-temperature synthesis, lab use, etc. |
Strength | High mechanical strength, especially at high temperatures |
Chemical Resistance | Excellent resistance to most acids and alkalis |
Ease of Cleaning | Easy to clean, typically requires minimal maintenance |
Production Process of Alumina Ceramic Crucible
Raw Material Selection:
The primary material used is aluminum oxide (Al₂O₃), which can be sourced from calcined alumina or other refined forms. The purity level of alumina directly affects the quality and performance of the final product.
Formulation:
Depending on the desired properties of the crucible, additional materials such as binders, plasticizers, and sometimes other ceramic powders may be added to the alumina powder. These additives help improve the workability of the mixture during forming and contribute to the strength and durability of the finished product.
Mixing:
The raw materials are thoroughly mixed to ensure a homogeneous blend. This step is critical for achieving consistent quality throughout the batch.
Forming:
There are several methods to form the crucible, including pressing, slip casting, and injection molding.
Pressing: Dry powder is placed into a mold and pressed under high pressure to form the shape.
Slip Casting: A liquid suspension of the ceramic material (slip) is poured into a porous mold. The water is absorbed by the mold, leaving a solid layer of ceramic material.
Injection Molding: The ceramic material is mixed with a thermoplastic binder and injected into a mold under heat and pressure.
Drying:
After forming, the green (unfired) crucible is dried to remove any residual moisture. Drying can be done using air drying, oven drying, or microwave drying techniques, depending on the method used for forming.
Firing (Sintering):
Once dried, the crucibles undergo firing at very high temperatures (typically between 1400°C and 1800°C). During this phase, the ceramic particles fuse together, increasing density and mechanical strength. The temperature and duration of firing depend on the specific formulation and intended use of the crucible.
Finishing:
After firing, some crucibles may require additional machining or grinding to achieve precise dimensions or smooth surfaces. Surface treatments might also be applied to enhance certain properties like corrosion resistance.
Quality Control:
Finally, each crucible is inspected for defects such as cracks or imperfections that could compromise its integrity. Testing might include visual inspection, dimensional checks, and sometimes non-destructive testing methods.
Packaging:
Proper packaging is essential to prevent damage during transportation and storage. Packaging materials should protect against physical impacts and environmental factors that could degrade the crucible’s quality.
Applications of Alumina Crucible
- Metal Melting: Alumina crucibles are commonly used in the melting of metals, especially those with high melting points, such as gold, silver, and certain alloys. The crucible’s ability to withstand high temperatures without reacting with the metals makes it ideal for these processes.
- Laboratory Research: In scientific labs, alumina crucibles are used for sample heating, sintering, and conducting chemical reactions at elevated temperatures. They are often used in material science, chemistry, and physics research.
- Glass Manufacturing: Alumina crucibles are utilized in the production of glass and ceramics due to their high heat resistance and ability to withstand molten materials without degradation.
- Casting and Foundry Work: In foundries, alumina crucibles are used to melt metals for casting processes, where their thermal properties ensure precise temperature control during metal pouring.
- Ceramic Firing: In ceramics, alumina crucibles are used in kiln firing processes, where they support the high-temperature heating needed for glazing or sintering ceramics.
- Chemical Processing: In the chemical industry, alumina crucibles can be used in various processes, including the production of catalysts and other high-temperature reactions.
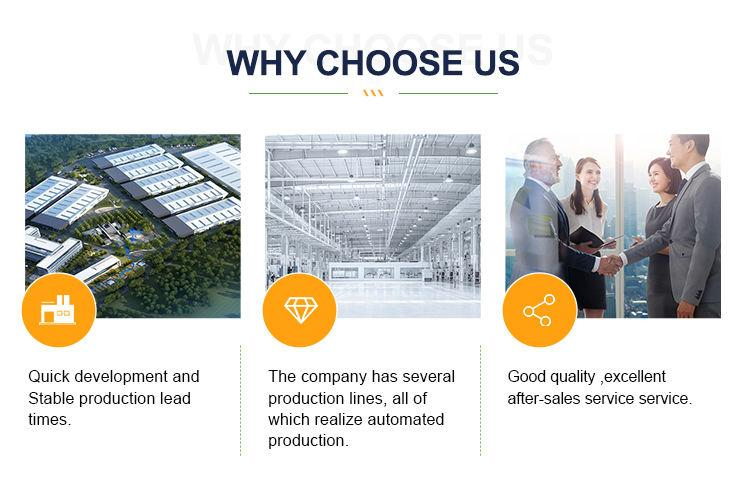
Company Profile
Advanced Ceramics founded on October 17, 2012, is a high-tech enterprise committed to the research and development, production, processing, sales and technical services of ceramic relative materials and products.. Since its establishment in 2012, the company has been committed to providing customers with the best products and services, and has become a leader in the industry through continuous technological innovation and strict quality management.
Our products includes but not limited to Aluminum Nitride Ceramic Products, Boron Carbide Ceramic Products, Boron Nitride Ceramic Products, Silicon Carbide Ceramic Products, Silicon Nitride Ceramic Products, Zirconium Dioxide Ceramic Products, Quartz Products, etc. Please feel free to contact us.(nanotrun@yahoo.com)
Payment Methods
T/T, Western Union, Paypal, Credit Card etc.
Shipment Methods
By air, by sea, by express, as customers request.
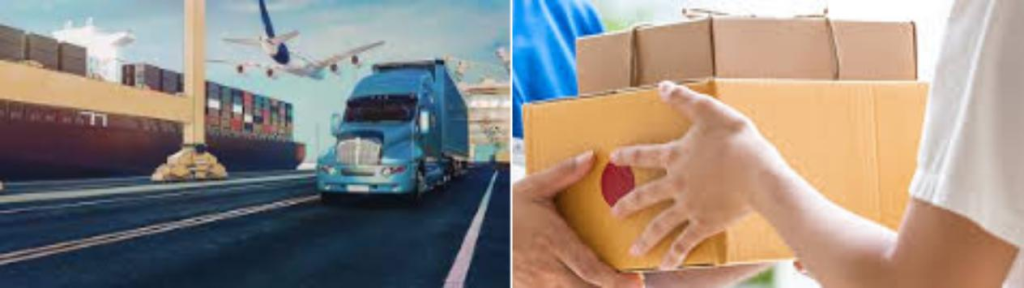
FAQs about Alumina Crucible
- How do you clean an alumina crucible?
- To clean an alumina crucible, it’s important to allow it to cool down completely. You can clean it with a soft brush to remove any residue. For stubborn stains, a mild abrasive or cleaning solution may be used. Avoid using harsh chemicals that could damage the crucible.
- What is the maximum temperature an alumina crucible can withstand?
- Alumina crucibles can typically withstand temperatures up to 1700°C (3092°F), though the exact temperature limit may vary depending on the specific grade and quality of the alumina used.
- Can alumina crucibles be used for melting all metals?
- While alumina crucibles are ideal for melting many metals, especially non-ferrous metals like gold, silver, and copper, they may not be suitable for some reactive metals like sodium or lithium, which could react with alumina at high temperatures.
- How long do alumina crucibles last?
- The lifespan of an alumina crucible depends on its usage. In high-temperature and high-stress environments, it can last for several uses before signs of wear or degradation appear. Proper handling and care can extend its life significantly.
- Are alumina crucibles safe to use in ovens or furnaces?
- Yes, alumina crucibles are safe to use in industrial ovens, furnaces, or laboratory kilns that reach high temperatures. They are designed to withstand thermal shock and resist degradation at high heat.
- Can alumina crucibles be used in a microwave furnace?
- Alumina crucibles are generally not recommended for use in microwave furnaces unless they are specifically designed for that purpose, as the microwave heating process can affect their structure. Always verify compatibility with your equipment.
- Do alumina crucibles require any special storage?
- Alumina crucibles should be stored in a dry, clean environment to avoid contamination. They should be kept away from mechanical stress or impact, as they are brittle and could crack under pressure.
REQUEST A QUOTE
RELATED PRODUCTS
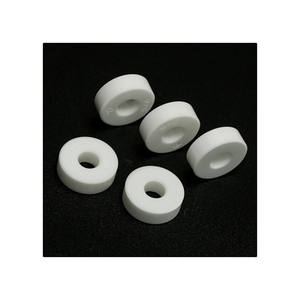
Customization 99% Alumina Ceramic Tube For Furnace Heater
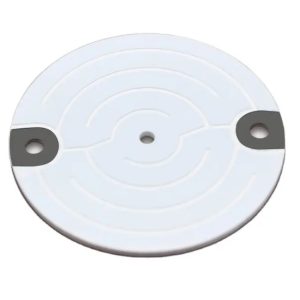
Al2O3 Ceramic Large size aluminium oxide ceramic plates and discs Alumina ceramic round plate
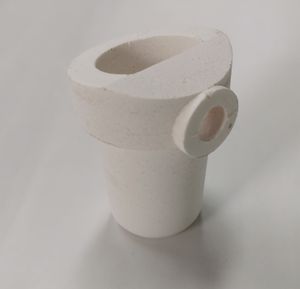
Heat-resistant and Impact-resistant Alumina Ceramics for Sintering Kilns
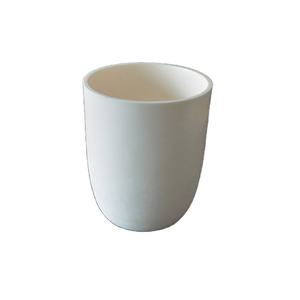
Customization Industrial Insulation High Precision High Purity Ceramics 95% 99% 99.5% Structural Parts Alumina Ceramic
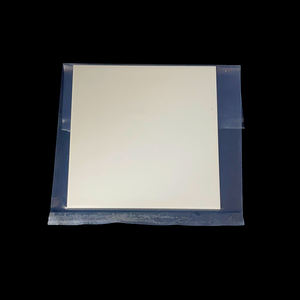
Porous Semiconductor Ceramics/insulating Electronic Ceramics/995 Alumina Ceramics
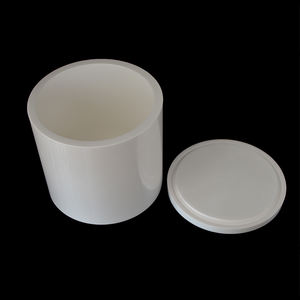