Discover Premium Ceramic Products | Durability & Elegance United | Advanced Ceramics
PRODUCT PARAMETERS
Description
Overview of zirconia ceramic crucible
Zirconia crucibles are specialized containers used in high-temperature laboratory and industrial processes. They are made from zirconium dioxide (ZrO2), which is known for its excellent thermal stability, resistance to chemical attack, and ability to withstand temperature changes without deforming or breaking.
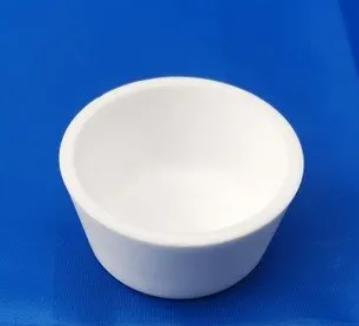
Features of zirconia ceramic crucible
High Melting Point
Feature: Zirconia has a very high melting point (~2700°C).
Benefit: This allows zirconia crucibles to withstand extremely high temperatures without deforming or melting, making them ideal for processes like metal melting, sintering, and calcination.
2. Excellent Chemical Inertness
Feature: High resistance to acids, bases, and molten metals.
Benefit: Ensures minimal contamination of samples and extends the lifespan of the crucible in corrosive environments.
3. Thermal shock resistance
Features Ability to withstand sharp temperature changes.
Benefits Reduces the risk of cracking or fracturing during heating and cooling cycles, which is common in laboratory environments where thermal shock is frequent.
4. Low Thermal Expansion
Characteristics: Low coefficient of thermal expansion: Low coefficient of thermal expansion.
Advantage: Minimizes the possibility of damage caused by thermal stress, thereby extending service life and reliability under varying temperature conditions.
5. High purity
Features Available in high purity form with minimal impurities.
Benefits: Ensures that the crucible does not introduce impurities into the sample, which is critical for accurate analytical results and high-purity material handling.
6. Mechanical Strength and Toughness
Characteristics High hardness and fracture toughness, especially when stabilized with additives such as yttrium.
Benefits: Durability and resistance to mechanical wear ensure that the crucible can withstand rough handling and retain its shape over time.
7. Dimensional stability
Features Minimal shrinkage during sintering and excellent dimensional control.
Benefits: Ensures exact fit and function in precision applications and reduces variability in experimental results.
8. Electrical insulation
Features Excellent electrical insulation at room temperature.
Benefits: Ideal for electrical applications requiring isolation, such as certain sensors and components in electronic devices.
9. Oxygen Ion Conduction at High Temperatures
Feature: Conducts oxygen ions efficiently at elevated temperatures.
Benefit: Useful in applications like solid oxide fuel cells (SOFCs) and oxygen sensors, enhancing performance in these devices.
10. Environmental Stability
Feature: Stable under a wide range of environmental conditions.
Benefit: Reliable performance in diverse laboratory and industrial settings, including those with varying humidity and atmospheric compositions
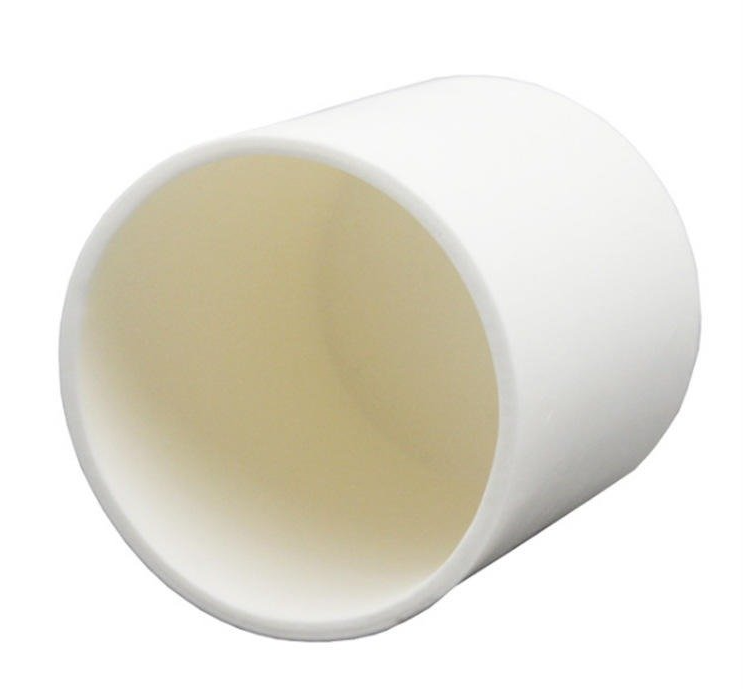
Specifications of zirconia ceramic Crucible
Specification | Description |
Material Composition | ZrO2 with stabilizers (e.g., Yttria, Magnesia) |
Purity (%) | Typically 95% to 99.95%, depending on grade |
Density (g/cm³) | Approximately 5.60 to 6.10 g/cm³ |
Melting Point (°C) | ~2700°C |
Max Service Temperature (°C) | Up to 2200°C in oxidizing atmospheres |
Thermal Conductivity (W/m·K) | Low, around 1.5 to 3.5 W/m·K at room temperature |
Coefficient of Thermal Expansion (CTE) (10^-6/K) | ~10.5 at room temperature |
Chemical Resistance | Excellent resistance to acids, bases, and molten metals |
Electrical Resistivity (Ω·cm) | High, >10^12 Ω·cm at room temperature |
Surface Finish (Ra µm) | May vary; often specified as <0.4 µm for precision applications |
Tolerance (mm) | Usually ±0.1 mm for dimensions, depending on size and application requirements |
Volume Capacity (ml) | Available in various sizes, from small capacities (<1 ml) to larger ones (several hundred ml) |
Diameter (mm) | Can range from a few millimeters to several centimeters |
Height (mm) | Varies based on capacity and design |
Weight (g) | Depends on dimensions and wall thickness |
Wall Thickness (mm) | Typically ranges from 1 to 3 mm |
Shape | Commonly cylindrical, but also available in other shapes like boats or dishes |
Thermal Shock Resistance | Good, able to withstand rapid heating and cooling |
Fracture Toughness (MPa·m^½) | Around 7 to 12 MPa·m^½ |
Flexural Strength (MPa) | Can range from 800 to 1200 MPa at room temperature |
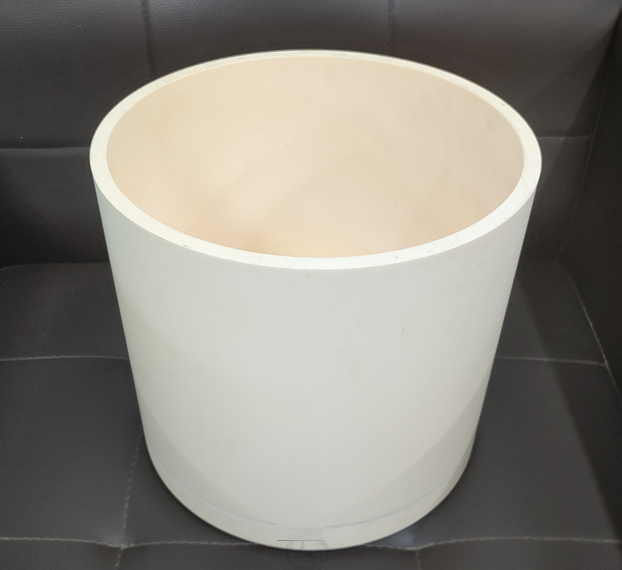
Zirconia ceramic Crucible
Manufacturing Methods of Zirconia ceramic Crucible
1.Powder Preparation
Material Selection: High-purity zirconium dioxide (ZrO2) powder is selected as the base material. Depending on the application, stabilizers like yttria (Y2O3), magnesia (MgO), calcium (CaO), or ceria (CeO2) may be added.
Mixing: The powders are thoroughly mixed using either wet or dry mixing processes to ensure homogeneity. Wet mixing often involves organic binders or dispersants to improve flowability and sintering behaviour.
2. Shaping
Several techniques can be employed to shape the zirconia powder into crucible forms:
Pressing:
Dry Pressing: The powder mixture is compacted in a mould under high pressure. This method is suitable for simple geometries and allows for good dimensional control.
Isostatic Pressing: Both cold isostatic pressing (CIP) and hot isostatic pressing (HIP) use fluid pressure to form the green bodies. CIP uses rubber moulds at room temperature, while HIP applies heat during the pressing process, which can enhance the density and reduce porosity.
Slip Casting:
A liquid suspension of zirconia powder (slip) is poured into a porous plaster mould. The mould absorbs water from the slip, allowing a solid layer to build up against the mould surface. Once sufficient thickness is achieved, the remaining slip is poured out, and the formed crucible is allowed to dry.
Injection Molding:
This method is used for more complex shapes where a heated mixture of ceramic powder and polymer binder is injected into a mold. After cooling, the binder is removed by thermal decomposition or solvent extraction, leaving a molded green blank.
3. Drying
The blanks (unfired parts) are carefully dried to remove any moisture or organic solvents used in the molding process. This step is essential to prevent cracking during subsequent firing.
4. Sintering
The dried billet is then fired in a kiln or furnace at very high temperatures (typically between 1400°C and 1600°C). During this process, the particles are fused together to increase the density and strength of the material. Stabilizing additives help maintain the cubic or tetragonal phase of zirconia and enhance its mechanical properties.
Controlled Atmosphere: Sintering can be carried out in a controlled atmosphere (e.g., air, oxygen, or inert gas) to avoid unwanted reactions and ensure optimum material properties.
5. Processing and polishing
Grinding and polishing: After sintering, the crucible may need to be machined to obtain precise dimensions and surface finish. Due to the hardness of zirconia, diamond tools are often used.
Surface treatment: Additional treatments such as grinding or polishing may be performed to achieve the desired surface finish and to improve aesthetic appearance and functionality.
6. Quality control
Quality control measures are taken throughout the manufacturing process to ensure that the crucible meets specified standards for purity, density, strength and other physical properties. This includes testing for chemical composition, mechanical strength, thermal stability and dimensional accuracy.
Applications of zirconia ceramic Crucible
1. Laboratory Research
Sample Preparation: Used for preparing samples for analysis, such as ashing organic materials, digesting samples in acids, or calcining materials.
Synthesis Reactions: Ideal for conducting synthesis reactions at high temperatures due to their chemical inertness.
THERMAL ANALYSIS: For techniques such as Thermogravimetric Analysis (TGA) and Differential Scanning Calorimetry (DSC) where precise temperature control and minimal contamination are essential.
2. Metallurgy
Metal melting and casting: Zirconia crucibles hold and melt a wide range of metals and alloys at high temperatures without reacting with the material, ensuring purity and quality.
Alloy Preparation: Used in the preparation of special alloys that require high-temperature processing.
3. Ceramics and Glass Manufacturing
Firing Ceramics: Essential for firing ceramics, especially those requiring high-temperature treatments.
Melting Glass: Used in glass manufacturing processes where the crucible must withstand high temperatures and resist chemical attack from molten glass.
Glaze Preparation: Useful for preparing glazes and enamels that need to be heated to high temperatures.
4. Material Science
Sintering: Commonly used in sintering processes to consolidate powders into solid forms without melting.
Calcination: Employed for calcining materials, which involves heating below the melting point to induce phase transitions or decompositions.
6. Electronics and Sensors
Oxygen Sensors: Widely used in automotive exhaust systems to monitor oxygen levels for efficient engine operation.
Solid Oxide Fuel Cells (SOFCs): Acts as an electrolyte in SOFCs, conducting oxygen ions at high temperatures.
7. Medical and Dental Applications
High-Temperature Sterilization: Used in sterilization processes that require high temperatures.
Dental Prosthesis Fabrication: Utilized in the fabrication of dental prostheses, where precision and heat resistance are critical.
8. Chemical Processing
Corrosive Environments: Valves, piping, and other components exposed to aggressive chemicals benefit from the superior corrosion resistance of zirconia crucibles.
Reaction Vessels: Used in reactors where high temperatures and pressures are involved, ensuring durability and safety.
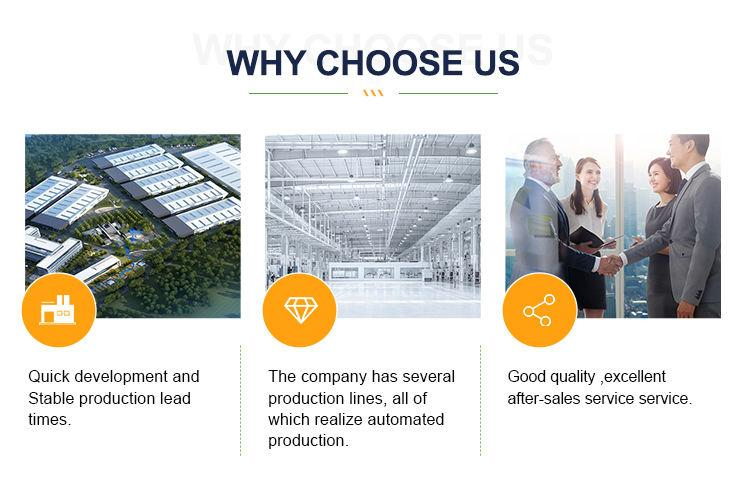
Company Profile
Advanced Ceramics founded on October 17, 2014, is a high-tech enterprise committed to the research and development, production, processing, sales and technical services of ceramic relative materials and products.. Since its establishment in 2014, the company has been committed to providing customers with the best products and services, and has become a leader in the industry through continuous technological innovation and strict quality management.
Our products includes but not limited to Silicon carbide ceramic products, Boron Carbide Ceramic Products, Boron Nitride Ceramic Products, Silicon Carbide Ceramic Products, Silicon Nitride Ceramic Products, Zirconium Dioxide Ceramic Products, Quartz Products, etc. Please feel free to contact us.(nanotrun@yahoo.com)
Payment Methods
T/T, Western Union, Paypal, Credit Card etc.
Shipment Methods
By air, by sea, by express, as customers request.
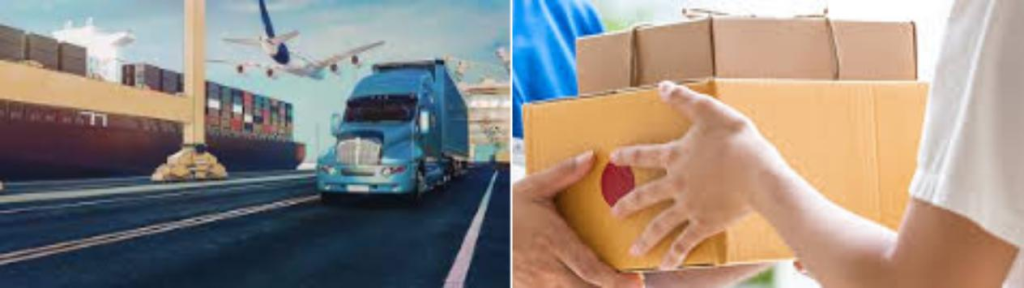
FAQs of Zirconia ceramic Crucible
1. What is the maximum operating temperature of a zirconia crucible?
A: Zirconia crucibles can withstand temperatures up to 2200°C in oxidizing atmospheres. However, the exact maximum temperature depends on factors like stabilization additives and the specific application environment.
2. Are zirconia crucibles resistant to chemicals?
A: Yes, zirconia crucibles exhibit excellent resistance to acids, bases, and molten metals, making them suitable for corrosive environments. This property minimizes contamination of samples and extends the crucible’s lifespan.
3. Can zirconia crucibles handle rapid temperature changes?
A: Yes, zirconia crucibles have good thermal shock resistance, meaning they can endure rapid heating and cooling cycles without cracking or breaking. This makes them reliable for dynamic laboratory settings.
4. How should zirconia crucibles be handled and maintained?
A: Handle carefully to avoid mechanical damage. Clean thoroughly after each use to prevent contamination. Store in a dry environment to avoid moisture absorption, which can affect material integrity. Follow manufacturer guidelines for maximum operating temperatures and recommended practices.
5. Can zirconia crucibles be customized?
A: Many manufacturers offer customization services for zirconia crucibles, including different sizes, shapes, tolerances, and surface finishes, to meet specific application requirements.
REQUEST A QUOTE
RELATED PRODUCTS
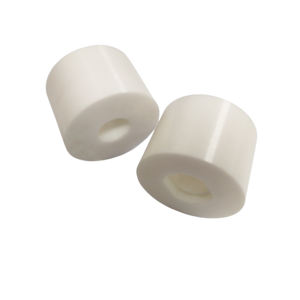
Ceramic Raw Material Zrsio4 Zirconia Silicate Powder 65% White Zirconium Silicate Powder for Ceramic
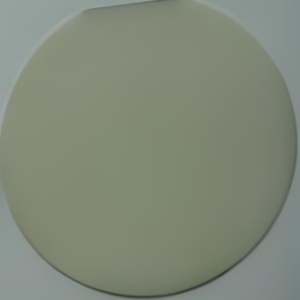
Very Thin Zirconia Black Ceramic Sheet Substrate Surface Polishing Round Zirconium Oxide Ceramic Plate
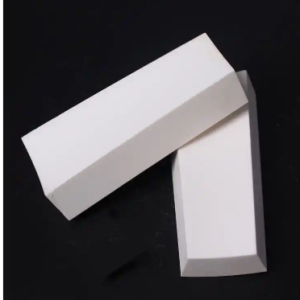
Zirconia AZS Refractory Brick sintered zirconia brick
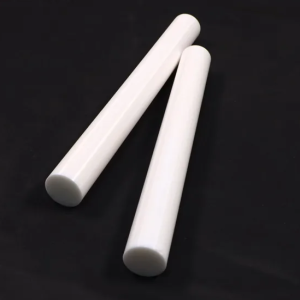
zirconia ceramic high hardness zirconia rod
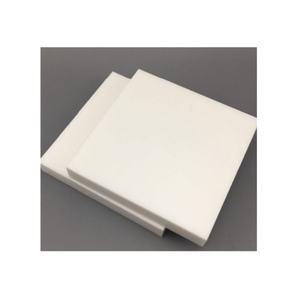
ZrO2 Ceramic Ring/zirconia Industrial Ceramic Parts Sold Directly By s/zirconia Wear-resistant Ceramic
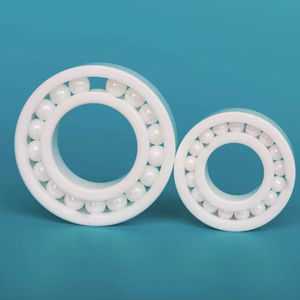