Discover Premium Ceramic Products | Durability & Elegance United | Advanced Ceramics
PRODUCT PARAMETERS
Description
Overview of Zirconia Ceramic Tube
Zirconia tubes offer unique advantages that make them essential in environments requiring thermal stability, chemical inertness, and sometimes ionic conductivity. Their use spans automotive, energy, laboratory, and industrial sectors, contributing to efficiency and reliability in numerous applications.
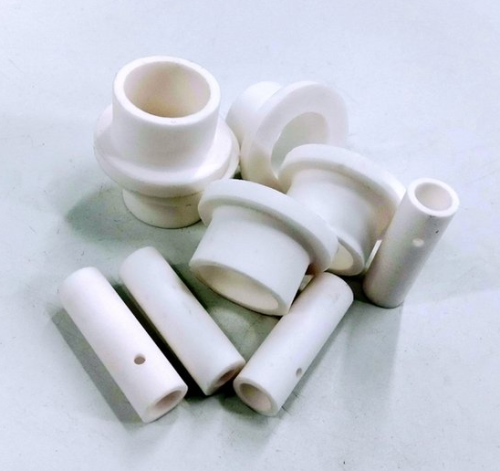
Features of zirconia ceramic Tube
Mechanical and Physical Properties
High-Temperature Stability: Zirconia can withstand very high temperatures without significant degradation or phase changes, making it ideal for use in environments with extreme heat.
Chemical Inertness: Highly resistant to chemical attack by acids, alkalis, and molten metals, which is crucial for maintaining integrity in corrosive conditions.
Mechanical Strength: Offers relatively good mechanical strength and toughness compared to other ceramics, though it remains somewhat brittle.
Low Thermal Expansion: Has a low coefficient of thermal expansion, reducing the risk of cracking due to thermal shock.
Electrical and Ionic Properties
Ionic Conductivity: Certain types of stabilized zirconia exhibit ionic conductivity at elevated temperatures, particularly for oxygen ions. This property is critical for its use in solid oxide fuel cells (SOFC) and oxygen sensors.
Electrical Insulation: Acts as an excellent electrical insulator at room temperature, which can be beneficial in various electrical applications.
Optical Properties
Transparency to Infrared Radiation: Some forms of zirconia are transparent to infrared radiation, which can be useful in specific optical applications.
Environmental Resistance
Resistance to Thermal Shock: Due to its low thermal expansion coefficient, zirconia can resist thermal shock better than many other materials.
Durability: Long-lasting performance under harsh conditions, contributing to reduced maintenance and replacement costs.
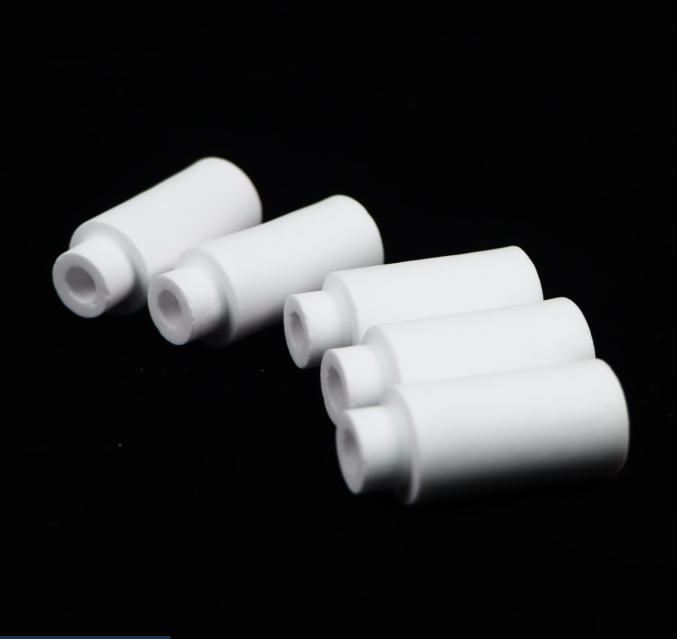
Specifications of zirconia ceramic tube
Specification | Typical Range / Value |
Material Composition | Zirconium dioxide (ZrO2), stabilized with Yttria (Y2O3) or Magnesia (MgO) |
Density | 5.6–6.1 g/cm³ |
Outer Diameter (OD) | 1 mm to 100 mm |
Inner Diameter (ID) | Dependent on OD and wall thickness |
Wall Thickness | 0.5 mm to 5 mm |
Length | Customizable, typically from 50 mm to several meters |
Flexural Strength | 800 – 1200 MPa at room temperature |
Fracture Toughness | 7 – 10 MPa·m^(1/2) |
Vickers Hardness | 12 – 14 GPa |
Young’s Modulus | 200 – 220 GPa |
Coefficient of Thermal Expansion (CTE) | 10.5 x 10^-6 K^-1 (room temp to 1000°C) |
Maximum Service Temperature | Up to 2200°C in non-reducing atmospheres |
Thermal Conductivity | 2.0 – 3.0 W/m·K at room temperature |
Electrical Resistivity | >10^12 Ω·cm at room temperature |
Ionic Conductivity | Significant at temperatures above 600°C |
Chemical Resistance | Excellent resistance to most acids, alkalis, and molten metals |
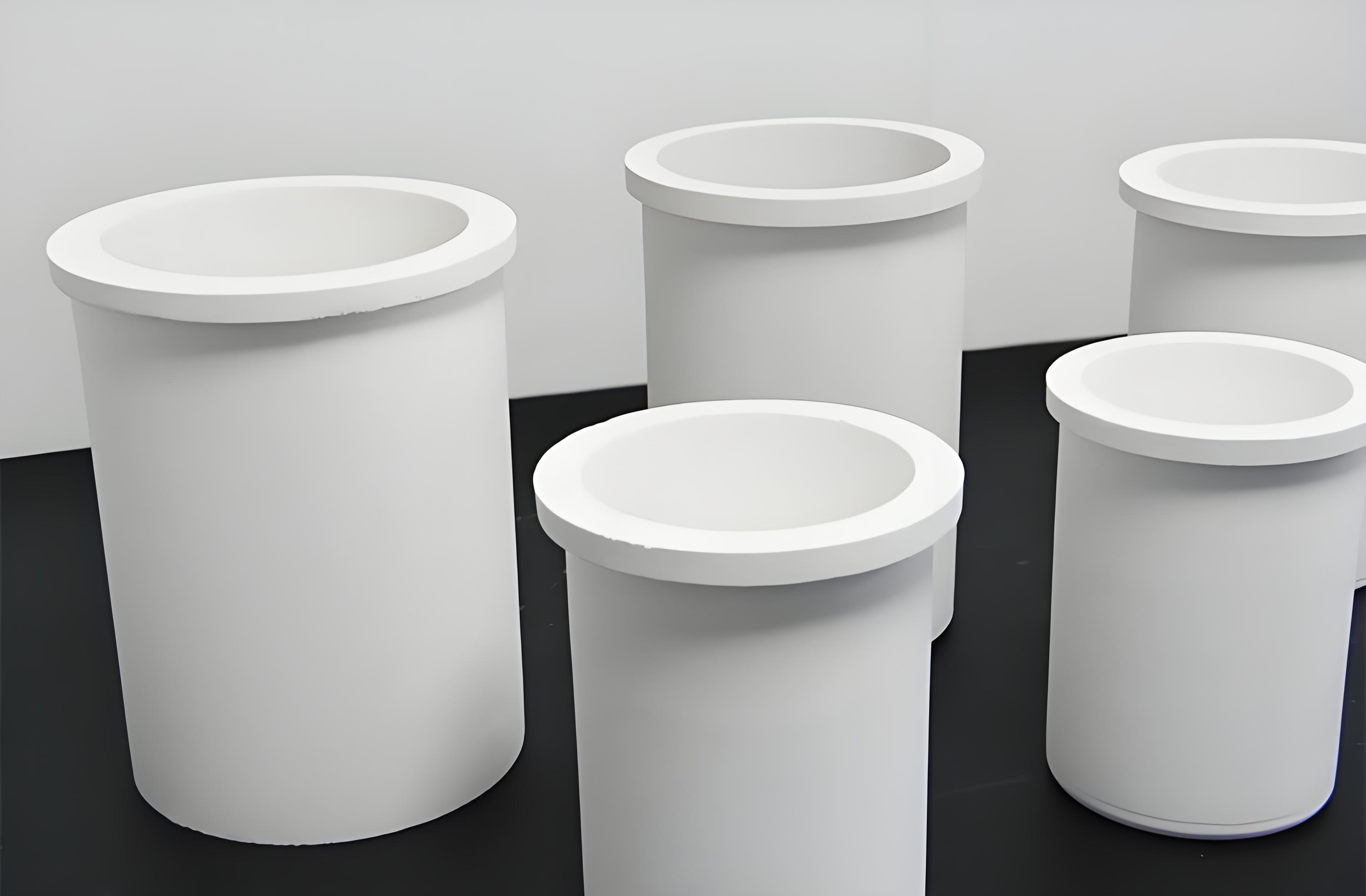
Zirconia ceramic Tube
Manufacturing Methods of Zirconia ceramic Tube
1.Powder Preparation
Material Selection: High-purity zirconium dioxide (ZrO2) powder is selected, often stabilized with additives like yttria (Y2O3) or magnesia (MgO).
Mixing: The zirconia powder is mixed with stabilizers and sometimes binders or plasticizers to enhance processability.
2. Shaping Methods
Extrusion
Process: A ceramic paste or slip made from the mixed powder is forced through a die to form a continuous tube.
Advantages: Suitable for producing long, uniform tubes with consistent wall thickness.
Applications: Commonly used for oxygen sensors and laboratory equipment.
Injection Molding
Process: Zirconia powder is mixed with a binder and injected into the mould under high pressure.
Advantages: Complex shapes and tight tolerances.
Application: For parts requiring precise dimensions and complex designs.
Isostatic pressing
Cold Isostatic Pressing (CIP): Powder is placed in a flexible mould, which is then subjected to a high-pressure fluid to produce a homogeneous part.
Hot Isostatic Pressing (HIP): Similar to CIP but performed at elevated temperatures, which can also densify the material.
Advantages: Produces dense, homogeneous parts with good mechanical properties.
Applications: Used when very high density and strength are required.
Tape Casting
Process: A slurry of zirconia powder is cast onto a moving carrier film, forming a flat sheet that can be rolled into a tube.
Advantages: Enables production of thin-walled tubes with controlled thickness.
Applications: Suitable for applications where thinness and uniformity are critical.
3. Drying
After shaping, the green (unfired) zirconia tube is dried to remove any remaining moisture or solvents. This step is crucial to prevent cracking during sintering.
4. Sintering
Process: The dried green body is heated to high temperatures (typically between 1400°C and 1600°C) in a furnace to fuse the particles and achieve full density.
Atmosphere: A controlled atmosphere (such as air or inert gas) may be used to prevent unwanted reactions.
Shrinkage: During sintering, the part shrinks significantly, so oversizing must be accounted for in the initial shaping process.
5. Machining and Finishing
After sintering, the tube may undergo machining to achieve final dimensions and tolerances.
Surface finishing techniques such as grinding or polishing can be applied to improve surface quality and dimensional accuracy.
Applications of zirconia ceramic tube:
Automotive Industry
Oxygen Sensors (Lambda Probes):
Function: Monitor oxygen levels in exhaust gases to optimize the air-fuel mixture for efficient combustion.
Benefit: Improves fuel efficiency and reduces emissions.
Exhaust Gas Recirculation (EGR) Valves:
Application: Used in components exposed to high temperatures and corrosive environments.
Energy Sector
Solid Oxide Fuel Cells (SOFC):
Role: Act as electrolytes, facilitating the movement of oxygen ions from the cathode to the anode, generating electricity.
Advantage: High efficiency and suitability for stationary power generation.
Gas Sensors:
Use: Detect harmful gases like CO, SO₂, and NOx in industrial settings or residential areas.
Benefit: Enhances safety and environmental monitoring.
Laboratory and Scientific Research
Furnace Components:
Application: Liners, sample holders, and other equipment requiring resistance to high temperatures and corrosive environments.
Benefit: Ensures durability and reliability in experimental setups.
Analytical Instruments:
Use: In instruments where thermal and chemical stability is critical.
Benefit: Provides accurate and consistent results over time.
Industrial Processing
Thermocouple Protection Tubes:
Purpose: Protect thermocouples used in high-temperature measurements.
Benefit: Extends the life of temperature sensors in harsh conditions.
Crucibles and Muffle Furnaces:
Application: For melting metals or conducting high-temperature reactions.
Benefit: Resistant to thermal shock and chemical attack.
Corrosion-Resistant Parts:
Use: Manufacturing parts for chemical processing environments.
Benefit: Long-lasting performance under aggressive conditions.
Medical Applications
Dental Implants:
Feature: Biocompatibility, aesthetic appearance, and durability.
Benefit: Preferred material for crowns, bridges, and implants.
Orthopaedic Implants:
Application: Hip and knee replacements.
Benefit: Wear resistance and compatibility with biological tissues.
Aerospace and Defense
High-Temperature Insulators:
Use: Insulating aerospace components exposed to extreme temperatures.
Benefit: Enhances heat resistance and structural integrity.
Protective Coatings:
Application: Applied on turbine blades and engine components.
Benefit: Reduces wear and increases operational lifespan.
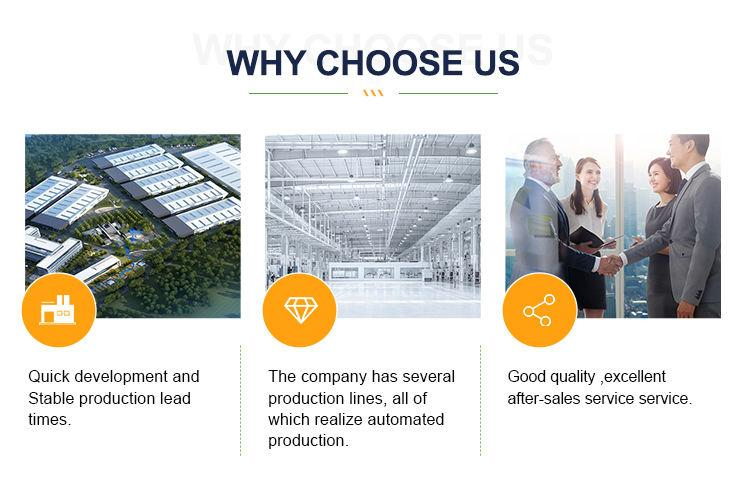
Company Profile
Advanced Ceramics founded on October 17, 2014, is a high-tech enterprise committed to the research and development, production, processing, sales and technical services of ceramic relative materials and products.. Since its establishment in 2014, the company has been committed to providing customers with the best products and services, and has become a leader in the industry through continuous technological innovation and strict quality management.
Our products includes but not limited to Silicon carbide ceramic products, Boron Carbide Ceramic Products, Boron Nitride Ceramic Products, Silicon Carbide Ceramic Products, Silicon Nitride Ceramic Products, Zirconium Dioxide Ceramic Products, Quartz Products, etc. Please feel free to contact us.(nanotrun@yahoo.com)
Payment Methods
T/T, Western Union, Paypal, Credit Card etc.
Shipment Methods
By air, by sea, by express, as customers request.
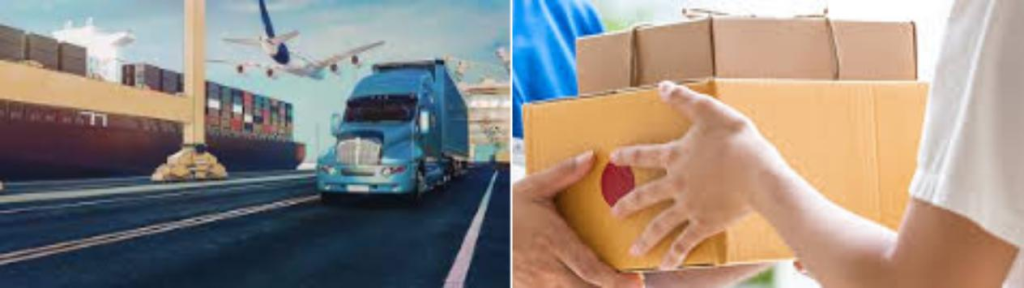
FAQs of Zirconia ceramic Crucible
What are the common applications of zirconia tubes?
A: Common applications include automotive oxygen sensors, solid oxide fuel cells (SOFC), laboratory equipment, industrial processing components, medical implants, aerospace insulators, and environmental monitoring devices.
2. Why are zirconia tubes used in oxygen sensors?
Zirconia tubing is ideal for oxygen sensors because zirconia conducts oxygen ions at high temperatures, allowing accurate measurement of the oxygen content of exhaust gases, which helps optimize engine performance and reduce emissions.
3. How durable are zirconia tubes?
A: Zirconia tubes are highly durable under harsh conditions, offering excellent resistance to thermal shock, corrosion, and wear. However, like most ceramics, they can be brittle and susceptible to catastrophic failure if subjected to sudden impacts or excessive stress.
4. What is the maximum operating temperature for zirconia tubes?
A: Zirconia tubes can typically withstand temperatures up to 2200°C in non-reducing atmospheres. The exact maximum temperature depends on the stabilization method and atmosphere.
5. Do zirconia tubes conduct electricity?
A: At room temperature, zirconia tubes act as electrical insulators. However, certain types can conduct oxygen ions at elevated temperatures, which is useful in electrochemical applications like fuel cells and oxygen sensors.
REQUEST A QUOTE
RELATED PRODUCTS
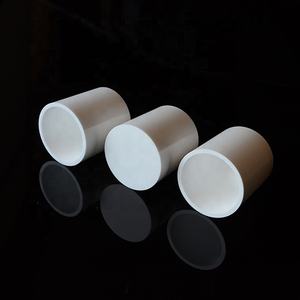
Professional High Quality Advanced Pure Zirconia Structural Ceramics ZrO2 Industrial Ceramic Parts
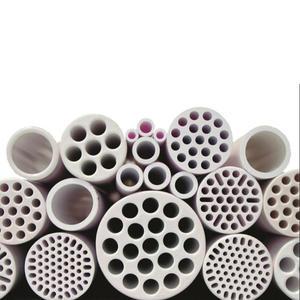
95% 99% 99.5% 99.6% 99.8% Al2O3 Alumina Zirconia ZTA Ceramic Piece Sheet Substrate High Quality
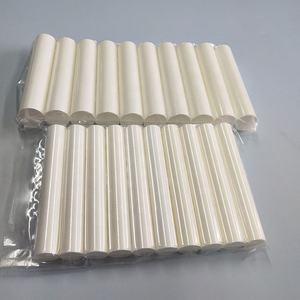
ZrO2 Factory Top Grade Thin Wall Zirconia Ceramic Tube
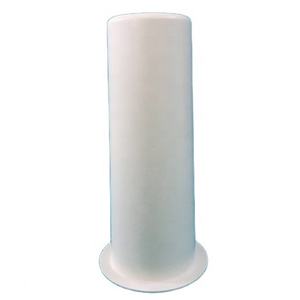
Customized Advanced Ceramics Zro2 Zirconia Ceramic Products Precision Machining Custom Bending Cutting Processing For Industrial
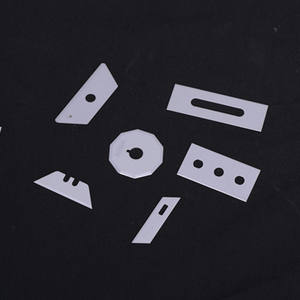
Ultra Precise Machining White Zirconia ZrO2 Tiny Ceramic Tube High End Zirconium Oxide Ceramic Small Components
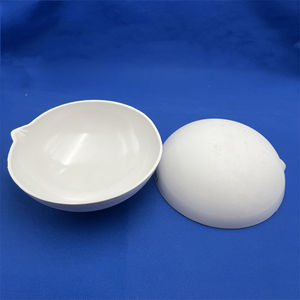