Discover Premium Ceramic Products | Durability & Elegance United | Advanced Ceramics
The global industrial materials market thrives on precision. For procurement specialists and engineers, choosing between boron nitride (BN) and silicon carbide (SiC) ceramics often defines project success. While both materials excel in extreme environments, their hidden differences in thermal management, wear resistance, and cost-efficiency reshape industrial outcomes. Let’s cut through the technical noise to reveal what truly matters for your sourcing strategy.
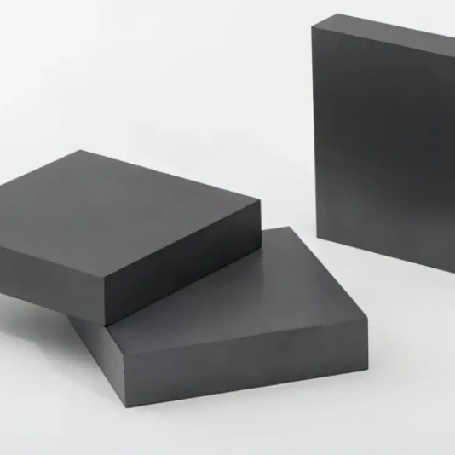
Boron carbide ceramic
Boron nitride ceramics owe their magic to hexagonal crystal frameworks. These layers slide easily, offering BN self-lubricating properties uncommon in ceramics. Think of graphite yet tougher. On the other side, silicon carbide types inflexible tetrahedral bonds. This creates a Mohs solidity of 9.5, closer to the diamond. For mining devices dealing with consistent abrasion, SiC’s unrelenting structure comes to be non-negotiable.
Here’s where BN shines unexpectedly. Its in-plane thermal conductivity hits 400 W/mK—outperforming many metals. This makes BN ideal for insulating yet heat-dissipating roles, like crucibles in semiconductor foundries. But SiC plays a different game. Though less conductive (120 W/mK), it handles 1600°C without breaking down. Steel mills using SiC thermocouple tubes gain months of extra service life in molten metal environments.
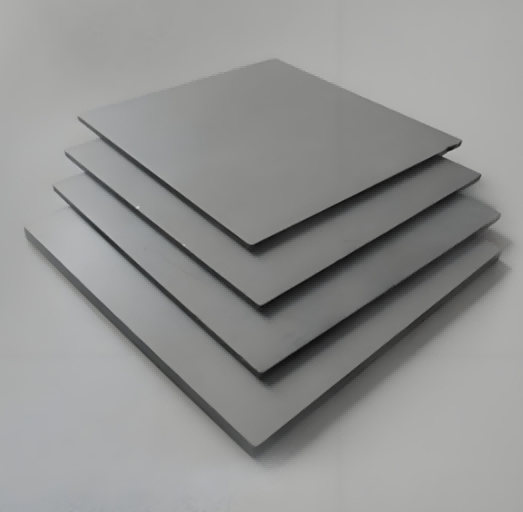
Silicon carbide ceramic
Acid resistance separates these materials starkly. BN laughs off hydrofluoric acid at 100°C, a feat unmatched by SiC. Chemical plant engineers lean on BN for pump seals in corrosive slurry transfer. However, SiC dominates where molten salts or alkalis rule. Aluminum smelters using SiC immersion heaters report 60% less downtime compared to metal alternatives.
BN’s softness cuts both ways. Yes, it’s easier to machine into complex shapes, saving 30% on tooling costs. But its lower hardness means faster wear in grinding applications. SiC’s extreme hardness demands diamond tools, raising initial machining costs by 40-50%. Yet for components like mechanical seal faces, SiC’s longevity offsets this premium within 18 months.
BN’s dielectric strength (35 kV/mm) makes it indispensable in high-voltage equipment. Electric vehicle battery manufacturers increasingly adopt BN insulators for thermal runaway prevention. Contrastingly, SiC’s semiconductor properties are revolutionizing power electronics. Its bandgap enables devices to handle 10x the voltage of silicon chips—a key enabler for next-gen renewable energy systems.
Density differences create niche advantages. BN’s featherlight of 2.1 g/cm³ allows thinner thermal barriers in satellites without compromising insulation. Meanwhile, SiC’s 3.2 g/cm³ density provides the heft needed for drone motor bearings to survive 20,000 RPM vibrations. Aviation OEMs now mix both BN for thermal management modules and SiC in propulsion systems.
BN’s dependence on boron—a geopolitically sensitive mineral—leads to 15-20% price swings during trade disputes. Savvy suppliers now stockpile grades like HP-BN during stable periods. SiC faces different pressures: 80% of global silicon comes from China, but new quartzite mines in Canada promise to rebalance this by 2026.
Recycling capabilities tilt scales. SiC’s durability allows 7-8 reuse cycles in kiln furniture applications before downgrading. BN’s lower melting point enables full reclamation through thermal decomposition—a growing priority for EU manufacturers facing strict landfill taxes.
A Brazilian cement producer swapped traditional alumina ceramics with BN-SiC hybrids in clinker cooler plates. Result? Maintenance intervals stretched from 6 weeks to 5 months. The hybrid design used BN’s thermal shock resistance on hot faces and SiC’s abrasion resistance on particle-impact sides.
Emerging composite technologies blend BN and SiC. For instance, SiC-reinforced BN matrices boost fracture toughness by 200% while retaining thermal conductivity. Early adopters in nuclear fusion research have already prototyped these for plasma-facing components.
Many buyers overlook this: BN grades vary wildly. ISO 22259-2 certification separates industrial-grade (95% purity) from semiconductor-grade (99.99%). Similarly, SiC’s α-phase vs. β-phase determines suitability for laser optics vs. armor systems. Partnering with suppliers offering mill test reports prevents costly mismatches.
Leading Chinese suppliers now offer laser-drilled BN components with ±5μm precision for semiconductor wafer handling. Meanwhile, German engineers developed porous SiC filters capturing 99.97% of PM2.5 emissions in steel plants. The takeaway? Tier-1 suppliers now compete on application-specific engineering, not just material specs.
BN’s sensitivity to moisture demands nitrogen-packed shipping—a 12-15% freight cost adder. SiC’s robustness allows standard container shipping, but its weight inflates charges. Smart procurement contracts now split orders: BN by air for urgent needs and SiC by sea for bulk orders.
Conscious buyers now demand conflict-free boron sourcing. Over 60% of BN’s boron comes from Turkey’s Eti Mine Works, which recently achieved ESG compliance certification. For SiC, traceability to quartzite (not beach sand) sources becomes a selling point amid ecological concerns.
Top suppliers offer mobile hardness testers for incoming SiC shipments. A quick Vickers test spots subpar sintering. For BN, simple thermal imaging during trial runs exposes delamination risks—a $500 test preventing $50,000 downtime.
Misapplication often stems from knowledge gaps. A Vietnamese plant reduced BN seal failures by 80% after supplier-led workshops on proper mounting techniques. Similarly, SiC’s brittleness demands torque-controlled installation—a detail overlooked in 40% of first-time installations.
Advanced suppliers now provide 3D simulation files showing thermal stress distribution in BN/SiC components. This allows virtual testing against your specific operating conditions—a game changer for remote technical validation.
Your selection between BN and SiC ceramics isn’t about material superiority. It’s about lining up atomic-scale homes with functional realities. The actual win hinges on vendors who don’t simply sell porcelains but engineer failure-proof remedies customized to your profit margins and run the risk of limits.
Supplier
If you need high quality Boron carbide ceramic and Silicon carbide ceramic, please feel free to contact us. You can click on the product to contact us. (sales8@nanotrun.com)
Tags:Boron carbide ceramic,Silicon carbide ceramic