Discover Premium Ceramic Products | Durability & Elegance United | Advanced Ceramics
PRODUCT PARAMETERS
Description
Introduction to Alumina Ceramics
Alumina ceramics are known for their high hardness, wear resistance, corrosion resistance, good electrical insulation and high temperature stability. According to the different alumina content, it can be divided into different grades, such as 95 porcelain, 99 porcelain, etc., among which 99 porcelain refers to ceramic materials with an alumina content of 99%. As the alumina content increases, its mechanical strength and electrical insulation properties will also increase accordingly.
Characteristics of Alumina Ceramics
High Hardness: Alumina ceramics have extremely high hardness, which makes it very wear-resistant and suitable for manufacturing abrasive tools and parts that require wear resistance.
Wear resistance: Due to its high hardness, alumina ceramics show excellent wear resistance and are suitable for manufacturing parts for long-term use.
Corrosion resistance: Alumina ceramics have good resistance to most acids and alkalis, making them widely used in the chemical industry.
Good electrical insulation: As an excellent electrical insulating material, alumina ceramics are widely used in electronic and electrical products.
High temperature stability: Ability to withstand extremely high temperatures without significant physical or chemical changes, which makes it an ideal choice for applications in high temperature environments.
Biocompatibility: In the medical field, certain grades of alumina ceramics are used to make medical devices such as artificial joints due to their good biocompatibility.
(Customization Industrial Insulation High Precision High Purity Ceramics 95% 99% 99.5% Structural Parts Alumina Ceramic)
Specifications of Customization Industrial Insulation High Precision High Purity Ceramics 95% 99% 99.5% Structural Parts Alumina Ceramic
Customization Industrial Insulation High Accuracy High Purity Ceramics are engineered for requiring industrial applications. These structural components make use of alumina ceramic with pureness levels of 95%, 99%, and 99.5%. The product ensures outstanding efficiency in extreme problems. High alumina content directly improves mechanical stamina and thermal stability. Components withstand temperature levels as much as 1600 ° C. This makes them suitable for high-heat settings like heating systems or kilns. The porcelains resist chemical rust from acids, alkalis, and molten metals. This extends their life-span in severe industrial settings. Accuracy production warranties tight tolerances. Components are personalized to fulfill specific specs. Options include intricate forms, openings, threads, or surface finishes. Advanced sintering technology makes certain uniform density and marginal porosity. This boosts resilience and insulation buildings. The 99.5% alumina grade offers the highest purity. It is fit for semiconductor manufacturing or vacuum cleaner systems. Lower contaminations protect against contamination in delicate processes. The 95% and 99% grades balance cost and efficiency. They are commonly made use of as a whole industrial insulation or mechanical components. All qualities offer outstanding electrical insulation. This prevents energy loss in high-voltage applications. Customized sizes and geometries decrease waste. They fit effortlessly into existing machinery or systems. Surface grinding and brightening enhance wear resistance. This lowers rubbing in moving parts. The porcelains work with fast temperature level changes. They stay clear of cracking or contortion under thermal stress. Checking includes look for density, firmness, and dimensional accuracy. Quality assurance ensures uniformity across batches. Industries like aerospace, energy, and chemical processing count on these porcelains. They change steel components in corrosive or high-wear locations. The product’s light-weight nature reduces total system weight. This boosts efficiency in automation or robotics. Customized layouts are supported from model to mass production. Technical support aids enhance part layouts for specific requirements. Lead times vary based on intricacy and order volume. Examples are available for performance validation. The porcelains satisfy international requirements for commercial products. They are a cost-efficient remedy for long-term usage. Efficiency data and product accreditations are provided upon demand.
(Customization Industrial Insulation High Precision High Purity Ceramics 95% 99% 99.5% Structural Parts Alumina Ceramic)
Applications of Customization Industrial Insulation High Precision High Purity Ceramics 95% 99% 99.5% Structural Parts Alumina Ceramic
Personalization commercial insulation high-precision high-purity porcelains are crafted for requiring applications throughout numerous markets. These structural components made from alumina ceramic deal purity degrees of 95%, 99%, and 99.5%, guaranteeing integrity in severe conditions. The material’s high thermal security, electric insulation, and resistance to chemical rust make it suitable for sectors requiring accuracy and longevity.
Semiconductor producing counts on these ceramics for critical components like wafer handling arms and process tubes. The high-purity alumina stops contamination throughout production, maintaining the stability of microelectronic devices. In aerospace, alumina ceramic parts are made use of in engine elements and thermal defense systems. The product stands up to heats and mechanical stress, enhancing performance and safety and security.
The energy market take advantage of these porcelains in power generation and storage space systems. They function as insulators in turbines, gas cells, and atomic power plants, where security under warm and radiation is non-negotiable. Clinical equipment suppliers make use of high-purity alumina for surgical tools and implants. The material’s biocompatibility and resistance to use guarantee long-term functionality in sterile atmospheres.
Personalization is a key benefit. Manufacturers tailor alumina ceramic parts to exact requirements, including complex forms and tight tolerances. Advanced machining methods like grinding, polishing, and laser cutting accomplish exact measurements. This flexibility permits assimilation into specialized machinery or unique commercial setups without jeopardizing performance.
Higher purity qualities (99% and 99.5%) are chosen for applications calling for very little contaminations. These qualities master atmospheres where also trace impurities can disrupt processes. Lower pureness (95%) matches less vital usages, stabilizing expense and functionality. All qualities maintain core buildings like solidity and thermal shock resistance.
The versatility of alumina porcelains encompasses chemical processing tools, where they line reactors and pumps. Their resistance to acidic or alkaline atmospheres minimizes downtime and upkeep expenses. Electronic devices makers use these porcelains as substratums for circuits, leveraging their electrical insulation to stop short circuits.
Longevity guarantees a long life span, even in rough or high-wear settings. This reduces replacement frequency, reducing functional costs. Industries focus on these porcelains for their capacity to meet stringent regulative and efficiency requirements. Custom remedies attend to one-of-a-kind challenges, providing reliable efficiency throughout diverse applications.
Company Introduction
Advanced Ceramics founded on October 17, 2014, is a high-tech enterprise committed to the research and development, production, processing, sales and technical services of ceramic relative materials and products.. Since its establishment in 2014, the company has been committed to providing customers with the best products and services, and has become a leader in the industry through continuous technological innovation and strict quality management.
Our products includes but not limited to Silicon carbide ceramic products, Boron Carbide Ceramic Products, Boron Nitride Ceramic Products, Silicon Carbide Ceramic Products, Silicon Nitride Ceramic Products, Zirconium Dioxide Ceramic Products, Quartz Products, etc. Please feel free to contact us.(nanotrun@yahoo.com)
Payment Methods
T/T, Western Union, Paypal, Credit Card etc.
Shipment Methods
By air, by sea, by express, as customers request.
5 FAQs of Customization Industrial Insulation High Precision High Purity Ceramics 95% 99% 99.5% Structural Parts Alumina Ceramic
What are high-purity alumina ceramics?
High-purity alumina ceramics are advanced materials made from aluminum oxide. They come in purity levels like 95%, 99%, and 99.5%. These ceramics are known for being strong, resistant to heat, and durable in harsh environments. They are used in industries needing reliable performance under extreme conditions.
Where are these ceramics commonly used?
These ceramics are used in electronics, aerospace, medical devices, and industrial machinery. They work well for electrical insulation, cutting tools, and parts exposed to high temperatures. Their resistance to wear and chemicals makes them ideal for demanding applications.
What is the difference between 95%, 99%, and 99.5% purity?
Higher purity means better performance. The 95% alumina offers good strength and cost-effectiveness for general uses. The 99% and 99.5% grades provide higher thermal stability, electrical resistance, and durability. They suit applications needing precision, like semiconductor manufacturing or lab equipment.
Can these ceramics be customized?
Yes. They are often tailored to specific needs. Custom shapes, sizes, and features like holes or threads can be added. Surface treatments or special coatings are available to improve performance. Custom designs ensure the parts fit exact requirements.
Do these ceramics handle high temperatures?
They do. Alumina ceramics withstand temperatures up to 1750°C. They keep their shape and strength even under thermal stress. This makes them suitable for furnaces, engines, or any high-heat environment. Their low thermal expansion reduces cracking risks.
How durable are they in corrosive environments?
These ceramics resist most acids, alkalis, and solvents. They do not corrode like metals. This makes them last longer in chemical processing, oil and gas, or medical settings. Their non-reactive nature ensures stability over time.
What sizes and shapes are possible?
Parts range from small components like washers to large industrial plates. Complex geometries are achievable through advanced molding and machining. Precision grinding ensures tight tolerances for critical applications.
Are they electrically insulating?
Yes. Alumina ceramics are excellent electrical insulators. They prevent current leakage in high-voltage systems. This property is vital for electronics, power transmission, and sensors.
How do I choose the right purity level?
Consider the application’s demands. Use 95% for cost-sensitive, less harsh environments. Opt for 99% or 99.5% when higher thermal, mechanical, or electrical performance is needed. Consult suppliers to match the material to your project.
What industries benefit most from these ceramics?
Industries like semiconductor manufacturing, energy, automotive, and healthcare rely on them. Their versatility in insulation, precision, and durability supports advanced technologies and harsh operational conditions.
(Customization Industrial Insulation High Precision High Purity Ceramics 95% 99% 99.5% Structural Parts Alumina Ceramic)
REQUEST A QUOTE
RELATED PRODUCTS
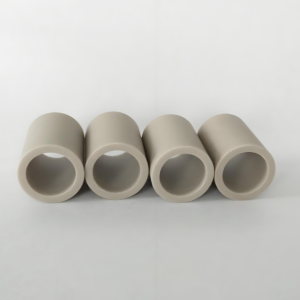
Al2O3 Ceramic mutiple size aluminium oxide ceramic tubes
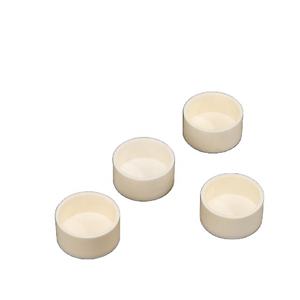
High Temperature Alumina Ceramic And Temperature Resistant For Alumina Ceramic Tube
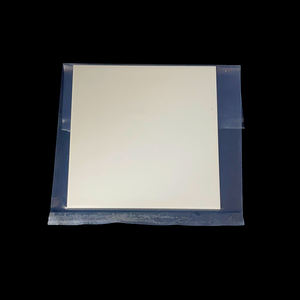
Porous Semiconductor Ceramics/insulating Electronic Ceramics/995 Alumina Ceramics
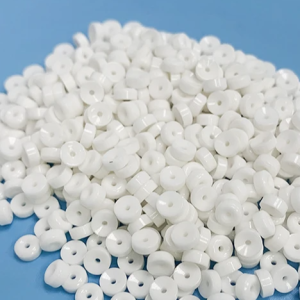
Long Service Life Materials Made of Ceramics 95 99 Al2o3 Insulator Alumina Ceramic Ring
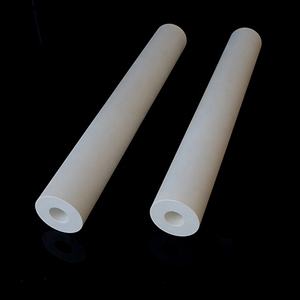
Industrial Electrical Technical Machinery Custom High Heat Resistant Ceramics Alumina Structural Parts
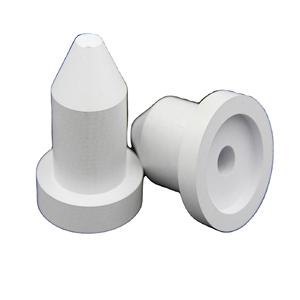