Discover Premium Ceramic Products | Durability & Elegance United | Advanced Ceramics
PRODUCT PARAMETERS
Description
Introduction to Alumina Ceramics
Alumina ceramics are known for their high hardness, wear resistance, corrosion resistance, good electrical insulation and high temperature stability. According to the different alumina content, it can be divided into different grades, such as 95 porcelain, 99 porcelain, etc., among which 99 porcelain refers to ceramic materials with an alumina content of 99%. As the alumina content increases, its mechanical strength and electrical insulation properties will also increase accordingly.
Characteristics of Alumina Ceramics
High Hardness: Alumina ceramics have extremely high hardness, which makes it very wear-resistant and suitable for manufacturing abrasive tools and parts that require wear resistance.
Wear resistance: Due to its high hardness, alumina ceramics show excellent wear resistance and are suitable for manufacturing parts for long-term use.
Corrosion resistance: Alumina ceramics have good resistance to most acids and alkalis, making them widely used in the chemical industry.
Good electrical insulation: As an excellent electrical insulating material, alumina ceramics are widely used in electronic and electrical products.
High temperature stability: Ability to withstand extremely high temperatures without significant physical or chemical changes, which makes it an ideal choice for applications in high temperature environments.
Biocompatibility: In the medical field, certain grades of alumina ceramics are used to make medical devices such as artificial joints due to their good biocompatibility.
(Heat-resistant and Impact-resistant Alumina Ceramics for Sintering Kilns)
Specifications of Heat-resistant and Impact-resistant Alumina Ceramics for Sintering Kilns
Heat-resistant and impact-resistant alumina ceramics for sintering kilns are crafted for high-performance industrial applications. These porcelains deal with severe temperature levels and mechanical tension. The product structure includes high-purity light weight aluminum oxide (Al two O FIVE) with marginal ingredients. This guarantees security in severe settings. The alumina material generally ranges from 95% to 99.9%. Higher pureness grades use better thermal and chemical resistance.
Physical buildings include a density of 3.6-3.9 g/cm FOUR. This adds to structural stability under hefty loads. The firmness gauges 8-9 on the Mohs range. This makes the material resistant to abrasion and wear. Surface area finishes are smooth to lessen rubbing during kiln procedures. Personalized shapes and sizes are readily available to fit details kiln styles.
Thermal properties are important. The optimum solution temperature gets to 1650 ° C. The material stands up to rapid temperature level changes without fracturing. Thermal shock resistance is achieved via controlled microstructure. Low thermal growth decreases anxiety during heating cycles. Warmth distribution continues to be uniform across ceramic parts.
Mechanical strength is a vital feature. Flexural stamina varieties from 300 to 400 MPa. Compressive toughness surpasses 2000 MPa. Impact resistance is improved by fine-grained structures. This stops cracking or damage under abrupt pressure. The product withstands deformation also under prolonged exposure to high loads.
Chemical inertness guarantees compatibility with hostile atmospheres. Alumina porcelains stand up to oxidation and rust. They stay secure in acidic or alkaline conditions. This expands life span in responsive sintering atmospheres.
Requirement measurements consist of thicknesses from 5 mm to 50 mm. Custom arrangements accommodate intricate kiln formats. Elements like kiln racks, setters, and linings prevail. The ceramics sustain constant item high quality by lessening contamination.
Surface therapies like brightening or glazing improve efficiency. These alternatives minimize fragment adhesion and simplify cleansing. Accuracy machining guarantees tight resistances for smooth combination.
The ceramics are optimal for industries needing reliability under extreme conditions. Applications span metallurgy, electronics, and aerospace. They lower downtime by surpassing typical products. Upkeep costs decrease because of long-lasting durability. Energy effectiveness improves through optimized thermal monitoring.
(Heat-resistant and Impact-resistant Alumina Ceramics for Sintering Kilns)
Applications of Heat-resistant and Impact-resistant Alumina Ceramics for Sintering Kilns
Alumina ceramics stand out in high-temperature commercial setups as a result of their special buildings. These products handle extreme warm and physical tension properly. Sintering kilns depend heavily on alumina ceramics for essential elements. Kiln furnishings like racks and setters often utilize high-purity alumina. This ensures security under heavy loads and duplicated thermal cycles. Alumina’s reduced thermal growth stops breaking also throughout rapid temperature level adjustments.
Heat resistance makes alumina ideal for shielding layers in kiln walls. These layers minimize power loss while maintaining inner temperatures. Alumina’s high melting factor (over 2000 ° C) permits kilns to run at peak performance without architectural damage. Influence resistance is just as important. Moving parts inside kilns deal with constant mechanical wear. Alumina porcelains withstand collisions and abrasion far better than standard metals or refractories.
Protective linings made of alumina expand kiln lifespans. They protect prone locations from straight fire direct exposure and chemical rust. This is important in procedures including responsive products or gases. Alumina’s non-reactive nature guarantees purity in delicate applications like electronics or aerospace element sintering.
Thermocouple sheaths in kilns typically utilize alumina tubes. These safeguard sensors from severe warmth while offering precise readings. Alumina’s electrical insulation properties stop signal interference. This assures accurate temperature level control throughout sintering.
Thick alumina elements are utilized for heater nozzles and gas injectors. Their smooth surface areas withstand buildup of down payments. This keeps constant gas flow and combustion efficiency. Alumina’s solidity likewise minimizes erosion from high-velocity gases.
Cost-effectiveness drives the adoption of alumina ceramics. Their sturdiness reduces downtime for substitutes. Suppliers reduce maintenance and energy prices over time. Alumina’s flexibility supports diverse sintering procedures throughout industries.
Company Introduction
Advanced Ceramics founded on October 17, 2014, is a high-tech enterprise committed to the research and development, production, processing, sales and technical services of ceramic relative materials and products.. Since its establishment in 2014, the company has been committed to providing customers with the best products and services, and has become a leader in the industry through continuous technological innovation and strict quality management.
Our products includes but not limited to Silicon carbide ceramic products, Boron Carbide Ceramic Products, Boron Nitride Ceramic Products, Silicon Carbide Ceramic Products, Silicon Nitride Ceramic Products, Zirconium Dioxide Ceramic Products, Quartz Products, etc. Please feel free to contact us.(nanotrun@yahoo.com)
Payment Methods
T/T, Western Union, Paypal, Credit Card etc.
Shipment Methods
By air, by sea, by express, as customers request.
5 FAQs of Heat-resistant and Impact-resistant Alumina Ceramics for Sintering Kilns
1. What materials make alumina ceramics heat-resistant?
Alumina ceramics mainly use aluminum oxide. Aluminum oxide has high melting points. It handles extreme heat without breaking down. The material’s dense structure stops heat from passing through easily. This makes it ideal for sintering kilns where temperatures stay very high.
2. How do these ceramics resist impacts?
The manufacturing process matters. Alumina ceramics are sintered at high temperatures. This makes their structure tight and hard. Tiny cracks or weak spots get reduced. Even under heavy force, they don’t shatter easily. Their toughness suits them for kiln parts exposed to mechanical stress.
3. Can alumina ceramics handle sudden temperature changes?
Yes. They have low thermal expansion rates. Sudden heating or cooling causes less stress inside the material. This prevents cracks. For sintering kilns, this is critical. Kilns often cycle between high and room temperatures quickly.
4. What kiln parts use alumina ceramics most?
Common parts include kiln shelves, setters, and protective tubes. Shelves hold items during firing. They need to stay stable under heat. Setters support delicate products. Protective tubes shield thermocouples. All these parts face high heat and physical wear. Alumina ceramics extend their lifespan.
5. How to maintain alumina ceramics in kilns?
Avoid dropping them. Check for chips or cracks before use. Clean them regularly. Remove dust or debris. Don’t expose them to extreme temperature shifts too fast. Proper handling keeps them working well for longer.
(Heat-resistant and Impact-resistant Alumina Ceramics for Sintering Kilns)
REQUEST A QUOTE
RELATED PRODUCTS
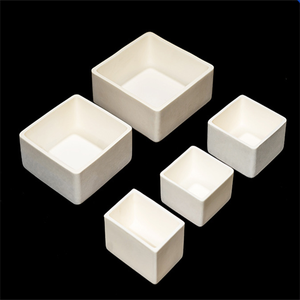
Ceramic C795 95% Alumina Ceramic Top Smoking Rolling Smoking Accessories
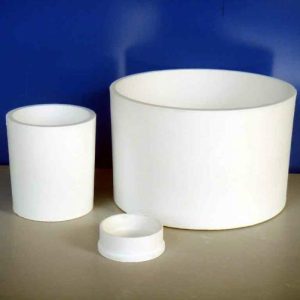
Al2O3 Ceramic HIgh Temperature Thermal Alumina Ceramic Crucible For Sale
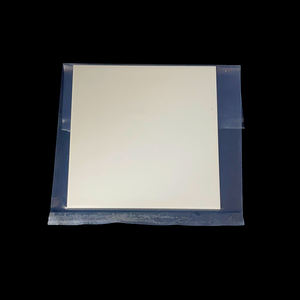
Porous Semiconductor Ceramics/insulating Electronic Ceramics/995 Alumina Ceramics
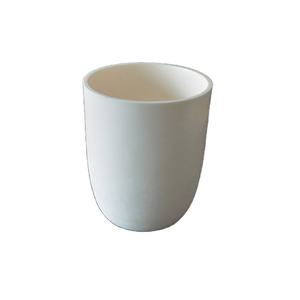
Customization Industrial Insulation High Precision High Purity Ceramics 95% 99% 99.5% Structural Parts Alumina Ceramic
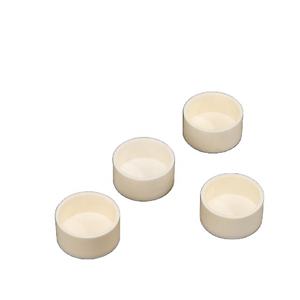
Corrosion Resistance Insulating Al2O3 Alumina Ceramic Plunger Shaft Ceramic Rod Zirconia Ceramic Pipe
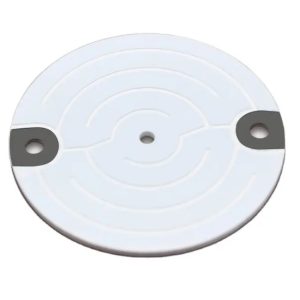