Discover Premium Ceramic Products | Durability & Elegance United | Advanced Ceramics
PRODUCT PARAMETERS
Description
Introduction to Alumina Ceramics
Alumina ceramics are known for their high hardness, wear resistance, corrosion resistance, good electrical insulation and high temperature stability. According to the different alumina content, it can be divided into different grades, such as 95 porcelain, 99 porcelain, etc., among which 99 porcelain refers to ceramic materials with an alumina content of 99%. As the alumina content increases, its mechanical strength and electrical insulation properties will also increase accordingly.
Characteristics of Alumina Ceramics
High Hardness: Alumina ceramics have extremely high hardness, which makes it very wear-resistant and suitable for manufacturing abrasive tools and parts that require wear resistance.
Wear resistance: Due to its high hardness, alumina ceramics show excellent wear resistance and are suitable for manufacturing parts for long-term use.
Corrosion resistance: Alumina ceramics have good resistance to most acids and alkalis, making them widely used in the chemical industry.
Good electrical insulation: As an excellent electrical insulating material, alumina ceramics are widely used in electronic and electrical products.
High temperature stability: Ability to withstand extremely high temperatures without significant physical or chemical changes, which makes it an ideal choice for applications in high temperature environments.
Biocompatibility: In the medical field, certain grades of alumina ceramics are used to make medical devices such as artificial joints due to their good biocompatibility.
(Industrial Alumina Ceramic Part Custom Made 95% 99% Alumina Ceramic Products)
Specifications of Industrial Alumina Ceramic Part Custom Made 95% 99% Alumina Ceramic Products
Industrial alumina ceramic components are personalized services designed for demanding applications. These products been available in 95% and 99% alumina compositions, each offering distinctive advantages. The 95% alumina ceramic gives strong mechanical efficiency, good wear resistance, and thermal stability as much as 1600 ° C. It is economical for general commercial use. The 99% alumina ceramic delivers greater thickness, exceptional firmness, and enhanced deterioration resistance. It operates dependably at temperatures going beyond 1700 ° C, ideal for extreme conditions. Both qualities master electric insulation, making them ideal for high-voltage settings.
These ceramic components are customized to satisfy certain requirements. Customization includes forms, sizes, and surface area finishes. Precision machining makes certain limited tolerances for elements like tubes, plates, insulators, or complex geometries. Surface treatments such as polishing or covering enhance efficiency in rough or chemically hostile settings. The manufacturing process uses innovative strategies like dry pressing, isostatic pushing, or shot molding, depending upon part intricacy.
Applications span several industries. In electronic devices, alumina porcelains shield substratums and circuit components. Automotive systems utilize them for sensing units and wear-resistant components. The chemical industry depends on their resistance to acids and alkalis. Medical tools benefits from their biocompatibility and sterilizability. Aerospace applications require their lightweight durability under stress.
Quality assurance is extensive. Each batch goes through examinations for density, firmness, and dimensional precision. X-ray and ultrasonic inspections find inner imperfections. Efficiency checks validate thermal shock resistance and dielectric stamina. Conformity with ISO and ASTM requirements ensures consistency.
These ceramics outshine metals and plastics in high-temperature or destructive setups. Their durability lowers replacement expenses. Very little maintenance is needed as a result of fundamental stability. Customized designs address one-of-a-kind challenges, boosting system performance. Lead times differ with complexity, yet basic orders ship within weeks. Technical support aids optimize layouts for specific functional requirements.
(Industrial Alumina Ceramic Part Custom Made 95% 99% Alumina Ceramic Products)
Applications of Industrial Alumina Ceramic Part Custom Made 95% 99% Alumina Ceramic Products
Industrial alumina ceramic parts personalized in 95% and 99% purity grades offer crucial duties across multiple markets. These components are understood for their high solidity, outstanding warm resistance, and solid electrical insulation. They manage extreme conditions much better than lots of steels or plastics. This makes them excellent for demanding applications.
In equipment and production, alumina porcelains are used for wear-resistant components. They work well in pumps, shutoffs, and seals. Their durability decreases downtime brought on by constant part replacements. High-temperature environments like heating systems or kilns depend on alumina elements. They maintain security under thermal tension.
The electronic devices sector gain from alumina’s electrical insulation. Ceramic substratums and insulators are common in motherboard and sensing units. The 99% purity quality uses superior performance for high-frequency applications. It minimizes signal loss in innovative digital systems.
Medical tools utilizes alumina porcelains for their biocompatibility. They are risk-free for implants and medical tools. Components like dental braces or prosthetic joints utilize their resistance to rust. Sanitation processes do not degrade their residential properties.
Aerospace and auto fields make use of custom-made alumina parts for high-stress applications. They are discovered in engine parts, sensors, and insulation systems. Their lightweight nature enhances fuel effectiveness. They hold up against severe vibrations and temperatures in engines or exhaust systems.
Modification is essential for these porcelains. Producers adjust measurements, forms, and surface finishes to meet particular needs. Complex geometries are achievable via sophisticated molding and sintering techniques. This adaptability guarantees precise assimilation right into specialized equipment.
95% alumina ceramics balance price and performance for general industrial usage. 99% alumina is selected for high-precision tasks calling for optimum wear resistance or thermal security. Both qualities are chemically inert. They withstand acids, antacid, and destructive gases in rough environments.
Industrial alumina ceramics enhance functional effectiveness. They expand equipment lifespan and decrease upkeep costs. Their flexibility across sectors highlights their significance in contemporary design options.
Company Introduction
Advanced Ceramics founded on October 17, 2014, is a high-tech enterprise committed to the research and development, production, processing, sales and technical services of ceramic relative materials and products.. Since its establishment in 2014, the company has been committed to providing customers with the best products and services, and has become a leader in the industry through continuous technological innovation and strict quality management.
Our products includes but not limited to Silicon carbide ceramic products, Boron Carbide Ceramic Products, Boron Nitride Ceramic Products, Silicon Carbide Ceramic Products, Silicon Nitride Ceramic Products, Zirconium Dioxide Ceramic Products, Quartz Products, etc. Please feel free to contact us.(nanotrun@yahoo.com)
Payment Methods
T/T, Western Union, Paypal, Credit Card etc.
Shipment Methods
By air, by sea, by express, as customers request.
5 FAQs of Industrial Alumina Ceramic Part Custom Made 95% 99% Alumina Ceramic Products
Industrial Alumina Ceramic Part Custom Made 95% 99% Alumina Ceramic Products FAQs
What is alumina ceramic?
Alumina ceramic is a material made mainly from aluminum oxide. It is known for high hardness, heat resistance, and electrical insulation. Products are available in 95% and 99% purity grades. Higher purity means better performance in extreme conditions.
Why pick 95% or 99% alumina ceramic?
The choice depends on application needs. 95% alumina offers good strength and cost efficiency for general industrial use. 99% alumina provides superior wear resistance and thermal stability. It suits high-performance environments like semiconductor manufacturing or aerospace.
What shapes can be customized?
Custom parts include tubes, plates, rods, and complex geometries. Precision machining techniques shape raw materials into required forms. Tolerances as tight as ±0.1mm are achievable. Surface finishes or coatings are added based on function.
How long does production take?
Production time varies. Simple designs take 2-3 weeks. Complex orders require 4-6 weeks. Factors include part size, quantity, and finishing steps. Prototypes are available for testing before full-scale production.
How to maintain alumina ceramic parts?
Avoid sudden temperature changes to prevent cracking. Clean parts with non-abrasive tools and mild solvents. Check for surface damage regularly. Proper handling reduces wear. Store parts in dry conditions to avoid moisture absorption.
(Industrial Alumina Ceramic Part Custom Made 95% 99% Alumina Ceramic Products)
REQUEST A QUOTE
RELATED PRODUCTS
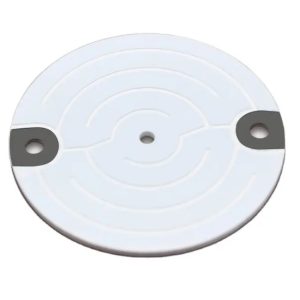
Al2O3 Ceramic Large size aluminium oxide ceramic plates and discs Alumina ceramic round plate
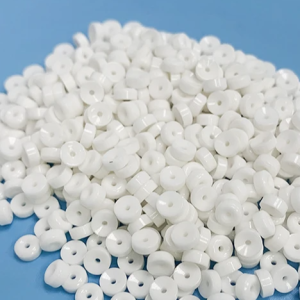
Long Service Life Materials Made of Ceramics 95 99 Al2o3 Insulator Alumina Ceramic Ring
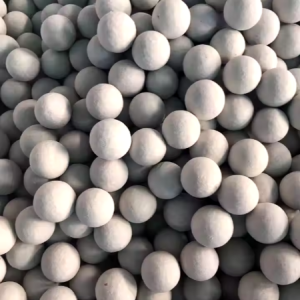
Al2O3 Ceramic 6mm,20mm Inert Alumina Ceramic Ball as Catalyst Support Media Ceramic Ball
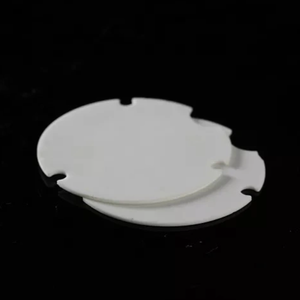
Fine Ceramic 99% Alumina Ceramic Tube
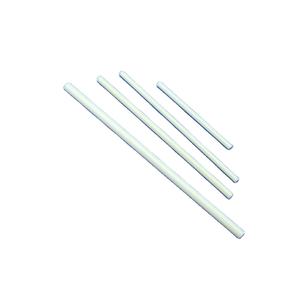
Al2o3 High Precision 95 99 Ceramic Plate Wear Resistant Alumina Ceramic Plate
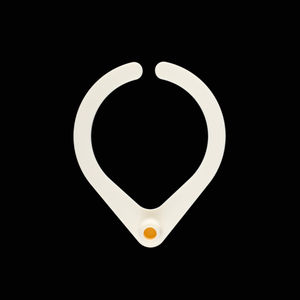