Discover Premium Ceramic Products | Durability & Elegance United | Advanced Ceramics
PRODUCT PARAMETERS
Description
Introduction to Alumina Ceramics
Alumina ceramics are known for their high hardness, wear resistance, corrosion resistance, good electrical insulation and high temperature stability. According to the different alumina content, it can be divided into different grades, such as 95 porcelain, 99 porcelain, etc., among which 99 porcelain refers to ceramic materials with an alumina content of 99%. As the alumina content increases, its mechanical strength and electrical insulation properties will also increase accordingly.
Characteristics of Alumina Ceramics
High Hardness: Alumina ceramics have extremely high hardness, which makes it very wear-resistant and suitable for manufacturing abrasive tools and parts that require wear resistance.
Wear resistance: Due to its high hardness, alumina ceramics show excellent wear resistance and are suitable for manufacturing parts for long-term use.
Corrosion resistance: Alumina ceramics have good resistance to most acids and alkalis, making them widely used in the chemical industry.
Good electrical insulation: As an excellent electrical insulating material, alumina ceramics are widely used in electronic and electrical products.
High temperature stability: Ability to withstand extremely high temperatures without significant physical or chemical changes, which makes it an ideal choice for applications in high temperature environments.
Biocompatibility: In the medical field, certain grades of alumina ceramics are used to make medical devices such as artificial joints due to their good biocompatibility.
(96 Alumina Ceramic Substrate)
Specifications of 96 Alumina Ceramic Substrate
The 96 alumina ceramic substratum is a high-performance product widely used in electronic devices, vehicle systems, and commercial equipment. It has 96% light weight aluminum oxide (Al2O3) and 4% various other oxides, which aid improve sintering and mechanical toughness. This composition ensures superb thermal security, electric insulation, and resistance to use. The material functions well in rough settings due to its capacity to handle severe temperature levels and chemical exposure.
The substrate has a density of 3.7 g/cm ³, making it sturdy yet light-weight. It supplies high mechanical stamina, with a flexural strength of 300-400 MPa. This makes it resistant to bending or damaging under stress. The firmness is around 15 GPa, which is more than lots of metals and plastics. This hardness minimizes wear over time, even with constant usage.
Thermal residential or commercial properties are a crucial advantage. The substratum has a low thermal expansion coefficient (7.0 x 10 ⁻⁶/ ° C), meaning it doesn’t increase a lot when heated. It additionally has high thermal conductivity (24 W/m · K), enabling reliable heat transfer. These characteristics protect against splitting or buckling throughout rapid temperature level changes. The material operates accurately from -50 ° C to 500 ° C, making it appropriate for high-heat applications like power components or LED lighting.
Electrical insulation is an additional significant benefit. The dielectric stamina exceeds 10 kV/mm, guaranteeing very little current leak. The dielectric constant is 9.8 at 1 MHz, with a low loss tangent (0.0002 ). These homes make it excellent for circuits needing steady signal transmission.
Surface finish options include brightened or lapped surfaces, with Ra values as reduced as 0.1 µm. This smoothness ensures proper bonding with metalized coverings or thin-film circuits. Customized sizes and shapes are available, consisting of holes, ports, or complicated geometries. Thickness arrays from 0.1 mm to 5 mm, relying on application needs.
The substratum withstands most acids, alkalis, and solvents, preserving performance in harsh problems. It works with thick-film and thin-film printing processes, supporting precise circuit patterns. Applications include semiconductor product packaging, sensing units, heating units, and RF components. Its durability and integrity make it a recommended selection for engineers seeking lasting remedies sought after settings.
Personalization options cover metallization layers (gold, silver, platinum), laser machining, and limited dimensional tolerances. These attributes make certain compatibility with specific style demands.
(96 Alumina Ceramic Substrate)
Applications of 96 Alumina Ceramic Substrate
96% alumina ceramic substratum is a high-performance material widely made use of in numerous industries. This material uses excellent thermal conductivity, electrical insulation, and mechanical toughness. It works well in environments with heats, deterioration, or use.
In electronics, 96% alumina ceramic substratums prevail in circuit boards and semiconductor packaging. They handle warmth successfully, preventing overheating in gadgets like LED lights and power components. Their electrical insulation properties make sure parts run securely without short circuits.
The automobile market counts on this material for sensing units and control systems. Modern vehicles utilize alumina substrates in oxygen sensors, engine control units, and exhaust gas sensors. These components face extreme heat and vibration. The ceramic substrate maintains security, guaranteeing precise analyses and lasting dependability.
Commercial tools benefits from alumina ceramic substratums in high-power applications. They are utilized in resistors, insulators, and burner. Equipment calling for specific temperature control, such as furnaces or welding systems, utilizes these substrates to deal with thermal stress without deteriorating.
Telecom framework utilizes alumina substrates for elements like antenna substratums and RF components. The product’s low signal loss at high regularities makes it ideal for 5G gadgets and radar systems. It sustains stable signal transmission, critical for interaction networks.
Clinical gadgets incorporate alumina ceramic substratums in imaging equipment and surgical devices. The material’s biocompatibility and resistance to sanitation processes make it suitable for MRI equipments and laser surgery instruments. It ensures safety and security and durability in sensitive medical atmospheres.
Renewable resource systems, such as photovoltaic panels and wind generators, utilize alumina substrates in power electronics. They enhance performance in inverters and converters by taking care of heat and electric flow. This aids take full advantage of energy output while decreasing maintenance needs.
The adaptability of 96% alumina ceramic substrates makes them crucial in advanced innovations. Their capability to do under severe problems sustains development across electronic devices, auto, industrial, telecommunications, medical, and energy fields.
Company Introduction
Advanced Ceramics founded on October 17, 2014, is a high-tech enterprise committed to the research and development, production, processing, sales and technical services of ceramic relative materials and products.. Since its establishment in 2014, the company has been committed to providing customers with the best products and services, and has become a leader in the industry through continuous technological innovation and strict quality management.
Our products includes but not limited to Silicon carbide ceramic products, Boron Carbide Ceramic Products, Boron Nitride Ceramic Products, Silicon Carbide Ceramic Products, Silicon Nitride Ceramic Products, Zirconium Dioxide Ceramic Products, Quartz Products, etc. Please feel free to contact us.(nanotrun@yahoo.com)
Payment Methods
T/T, Western Union, Paypal, Credit Card etc.
Shipment Methods
By air, by sea, by express, as customers request.
5 FAQs of 96 Alumina Ceramic Substrate
What is 96 alumina ceramic substrate? It is a material made mostly of aluminum oxide. Around 96% of its content is alumina. It is produced by sintering high-purity alumina powder at high temperatures. This makes it hard and durable. It is widely used in electronics, heaters, and circuits.
What are the main properties of 96 alumina ceramic substrate? It has high mechanical strength. It resists wear and corrosion well. It handles high temperatures up to 1600°C. It insulates electricity effectively. It stays stable in harsh chemical environments. These features make it reliable for tough applications.
Where is 96 alumina ceramic substrate commonly used? It is found in electronic parts like circuit boards. It works in high-power LED lights. It serves as a base for heating elements. It is used in automotive sensors. Industrial machinery uses it for insulation parts.
How does 96 alumina ceramic substrate perform in thermal conductivity? It conducts heat better than many ceramics. It is lower than metals like aluminum. It moves heat evenly across its surface. This prevents hotspots. It handles sudden temperature changes without cracking.
How should 96 alumina ceramic substrate be handled and machined? It is brittle. Handle it carefully to avoid chips. Use diamond tools for cutting or drilling. Avoid heavy mechanical stress. Clean it with non-abrasive methods. Leave complex machining to professionals.
(96 Alumina Ceramic Substrate)
REQUEST A QUOTE
RELATED PRODUCTS
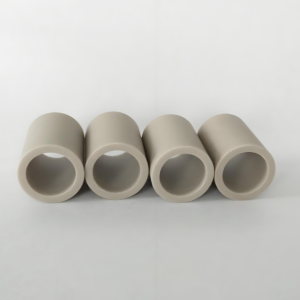
Al2O3 Ceramic mutiple size aluminium oxide ceramic tubes
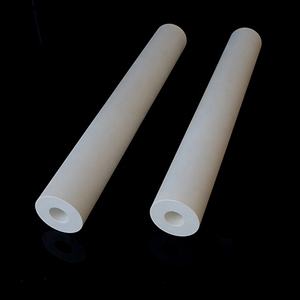
Industrial Electrical Technical Machinery Custom High Heat Resistant Ceramics Alumina Structural Parts
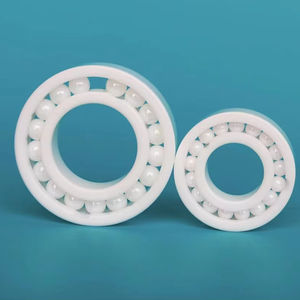
Industrial High Purity High Temperature Resistance 99% Alumina Ceramic Structural Component
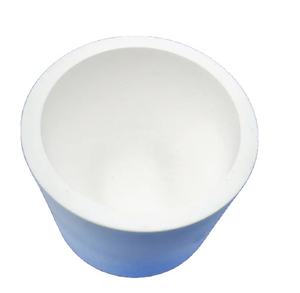
High Strength 99 Alumina Textile Ceramic for Factory Use
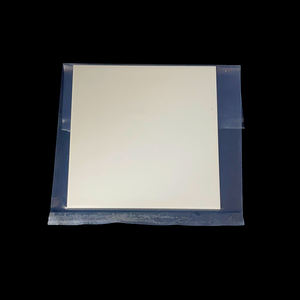
Porous Semiconductor Ceramics/insulating Electronic Ceramics/995 Alumina Ceramics
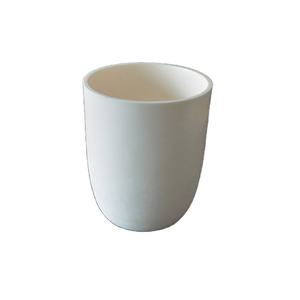