Discover Premium Ceramic Products | Durability & Elegance United | Advanced Ceramics
PRODUCT PARAMETERS
Description
Introduction to Alumina Ceramics
Alumina ceramics are known for their high hardness, wear resistance, corrosion resistance, good electrical insulation and high temperature stability. According to the different alumina content, it can be divided into different grades, such as 95 porcelain, 99 porcelain, etc., among which 99 porcelain refers to ceramic materials with an alumina content of 99%. As the alumina content increases, its mechanical strength and electrical insulation properties will also increase accordingly.
Characteristics of Alumina Ceramics
High Hardness: Alumina ceramics have extremely high hardness, which makes it very wear-resistant and suitable for manufacturing abrasive tools and parts that require wear resistance.
Wear resistance: Due to its high hardness, alumina ceramics show excellent wear resistance and are suitable for manufacturing parts for long-term use.
Corrosion resistance: Alumina ceramics have good resistance to most acids and alkalis, making them widely used in the chemical industry.
Good electrical insulation: As an excellent electrical insulating material, alumina ceramics are widely used in electronic and electrical products.
High temperature stability: Ability to withstand extremely high temperatures without significant physical or chemical changes, which makes it an ideal choice for applications in high temperature environments.
Biocompatibility: In the medical field, certain grades of alumina ceramics are used to make medical devices such as artificial joints due to their good biocompatibility.
(Factory Customized High Precision 95% Alumina Ceramic Parts Structural Member)
Specifications of Factory Customized High Precision 95% Alumina Ceramic Parts Structural Member
Factory Custom-made High Accuracy 95% Alumina Ceramic Components Structural Participant offers trusted performance for industrial applications. The material consists of 95% light weight aluminum oxide, guaranteeing high purity and uniformity. It incorporates exceptional mechanical strength with superior wear resistance. This makes it suitable for demanding environments needing sturdiness. The ceramic components include a dense structure, achieving a density of 3.6 g/cm ³. They maintain stability under high temperatures, running properly approximately 1600 ° C. Thermal shock resistance avoids fracturing during quick temperature modifications.
Customization alternatives cover a wide range of sizes and shapes. Parts consist of rods, tubes, plates, and complicated geometries. Accuracy machining strategies make sure limited resistances, generally within ± 0.1 mm. Surface finishes vary from brightened to matte, depending on application demands. The material’s hardness reaches 85 HRA, surpassing most metals and polymers. This decreases wear in high-friction settings. Electric insulation buildings protect against current leakage in digital parts.
Applications cover several sectors. In machinery, these parts serve as wear-resistant liners or overviews. Semiconductor producing utilizes them for wafer handling as a result of their non-contaminating nature. Clinical equipment take advantage of their biocompatibility and chemical inertness. High-temperature furnaces utilize alumina ceramics as insulation parts. Automotive systems use them for sensors and seals revealed to severe conditions.
Trick specs consist of a flexural strength of 300 MPa and compressive strength of 2200 MPa. The dielectric strength goes beyond 15 kV/mm, ideal for electrical insulation. Chemical resistance guarantees compatibility with acids, antacid, and organic solvents. Surface roughness can be regulated to Ra ≤ 0.4 μm for accuracy assemblies. Personalized metallization choices enable brazing or welding to steel components.
Quality assurance includes extensive testing. Each batch goes through dimensional verification making use of coordinate determining equipments. Product pureness is validated through X-ray fluorescence analysis. Mechanical homes are verified with third-party lab testing. Lead times vary based on complexity, with conventional orders finished in 2-4 weeks. Product packaging uses anti-static materials to stop damage during transportation.
The product satisfies ISO 9001 standards, making certain consistent production procedures. Technical assistance assists with design optimization for specific usage instances. Personalized prototypes are readily available for performance examination before major manufacturing.
(Factory Customized High Precision 95% Alumina Ceramic Parts Structural Member)
Applications of Factory Customized High Precision 95% Alumina Ceramic Parts Structural Member
Factory-customized high-precision 95% alumina ceramic components offer critical roles across markets due to their one-of-a-kind homes. These elements combine high hardness, wear resistance, and thermal stability, making them perfect for demanding settings. Manufacturing facilities produce these parts with tight tolerances to meet specific application demands.
In electronic devices producing, alumina ceramic structural participants serve as insulators and substrates. Their high electric insulation prevents present leak. They stand up to high temperatures throughout soldering or circuit operation. Semiconductor equipment uses them for wafer-handling arms. Their smooth surfaces prevent contamination.
The automobile field depends on these parts for sensors and ignition systems. Alumina ceramic stands up to corrosion from fuels and exhaust gases. Engine elements like shutoff seats benefit from their warm resistance. Electric vehicles use them in battery components to isolate high-voltage components.
Industrial equipment utilizes alumina ceramic components in wear-prone areas. Pump seals and bearings made from this product last longer under friction. Chemical processing equipment utilizes them for corrosion-resistant linings. Their security in acidic or alkaline problems decreases upkeep prices.
Clinical tools integrate these porcelains for their biocompatibility. Surgical tools utilize them for precision reducing edges. Imaging devices relies upon their X-ray openness. Dental implants use alumina ceramic for toughness and compatibility with body cells.
Aerospace applications require materials that handle severe problems. Alumina ceramic parts work in wind turbine sensors and thermal barrier. Their light-weight nature lowers airplane gas consumption. Satellite components utilize them for thermal monitoring precede vacuum cleaners.
Customization permits manufacturing facilities to form alumina ceramic into complex geometries. Laser cutting and accuracy grinding accomplish specific measurements. Post-processing options like brightening or finish boost efficiency. This flexibility guarantees parts fit specialized equipment or models.
Environmental innovation take advantage of alumina ceramic’s durability. Water treatment systems utilize them in shutoffs exposed to rough particles. Photovoltaic panel production devices uses ceramic parts to manage liquified silicon.
The combination of high purity (95% alumina) and customized manufacturing ensures dependability. Factories test each set for thickness and thermal shock resistance. Quality control warranties parts fulfill market standards. These porcelains address difficulties where metals or plastics fall short.
Company Introduction
Advanced Ceramics founded on October 17, 2014, is a high-tech enterprise committed to the research and development, production, processing, sales and technical services of ceramic relative materials and products.. Since its establishment in 2014, the company has been committed to providing customers with the best products and services, and has become a leader in the industry through continuous technological innovation and strict quality management.
Our products includes but not limited to Silicon carbide ceramic products, Boron Carbide Ceramic Products, Boron Nitride Ceramic Products, Silicon Carbide Ceramic Products, Silicon Nitride Ceramic Products, Zirconium Dioxide Ceramic Products, Quartz Products, etc. Please feel free to contact us.(nanotrun@yahoo.com)
Payment Methods
T/T, Western Union, Paypal, Credit Card etc.
Shipment Methods
By air, by sea, by express, as customers request.
5 FAQs of Factory Customized High Precision 95% Alumina Ceramic Parts Structural Member
What are high precision 95% alumina ceramic parts? These parts are industrial components made from 95% aluminum oxide. They are designed for extreme conditions. They resist high heat, corrosion, and wear. Their high hardness and stability make them ideal for machinery requiring tight tolerances and long-lasting performance.
Why choose 95% alumina ceramic over other materials? This material balances cost and performance. It handles temperatures up to 1600°C. It outperforms metals and plastics in harsh chemical environments. It maintains shape under stress. This reduces part replacement frequency. It is cheaper than higher-purity alumina but still reliable for most industrial uses.
Can these parts be customized? Yes. Factories adjust sizes, shapes, and features to meet specific needs. Complex geometries, holes, slots, or threads are possible. Custom surface finishes or coatings are available. Technical drawings or samples help ensure accuracy. Production timelines depend on design complexity.
Where are these parts commonly used? They are used in electronics, automotive, and aerospace industries. Examples include semiconductor processing equipment, furnace linings, cutting tools, and medical devices. They function as insulators, bearings, or structural supports. Their electrical insulation and thermal properties suit high-stress applications.
How should alumina ceramic parts be handled? Avoid mechanical shock or sudden temperature changes. These parts are hard but brittle. Use proper packaging during transport. Clean them with non-abrasive methods. Store them in dry areas to prevent moisture absorption. Follow factory guidelines for installation and maintenance. This ensures optimal performance and lifespan.
(Factory Customized High Precision 95% Alumina Ceramic Parts Structural Member)
REQUEST A QUOTE
RELATED PRODUCTS
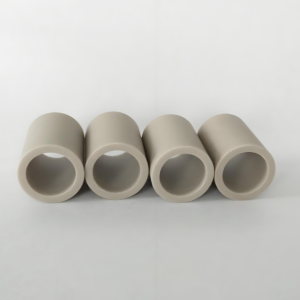
Al2O3 Ceramic mutiple size aluminium oxide ceramic tubes
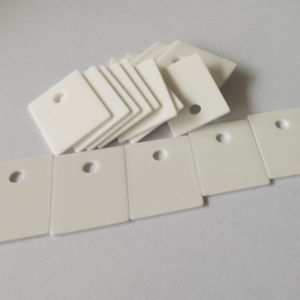
High Quality Alumina Ceramic Tiles 99.9% Purity
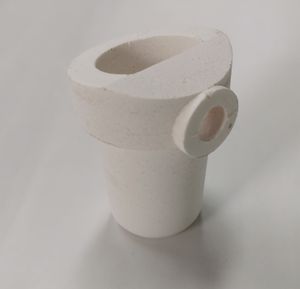
Heat-resistant and Impact-resistant Alumina Ceramics for Sintering Kilns
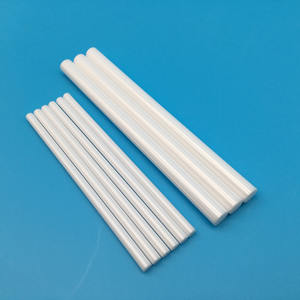
High Alumina Ceramic Heater Rod Porcelain Components 95
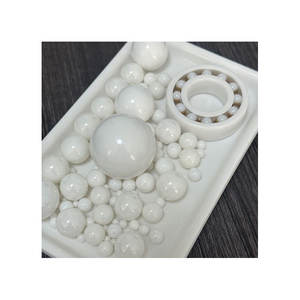
Wear-resistant Alumina Ceramic Sheets Industrial Wear-resistant Ceramics Alumina Ceramics
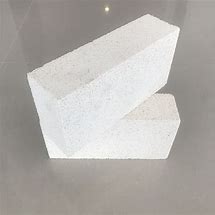