Discover Premium Ceramic Products | Durability & Elegance United | Advanced Ceramics
PRODUCT PARAMETERS
Description
Overview of Silicon Carbide Ceramics
Silicon Carbide (SiC) ceramics are renowned for their outstanding mechanical properties, including high hardness, strength at elevated temperatures, and excellent thermal shock resistance. These materials are pivotal in cutting-edge industrial applications, from abrasives to aerospace components, due to their unique combination of properties.
Features of Silicon Carbide Ceramics
High Hardness: Exceptional wear resistance.
Thermal Shock Resistance: Can withstand rapid temperature changes.
Chemical Stability: Resistant to most chemicals.
High Thermal Conductivity: Efficient heat dissipation.
Low Density: Lightweight for its strength.
(Carbide Customization Ceramic Parts OEM Silicon Carbide High Temperature Resistance Sic Silicone Precision)
Specification of Carbide Customization Ceramic Parts OEM Silicon Carbide High Temperature Resistance Sic Silicone Precision
Carbide Personalization Ceramic Parts deal high-performance solutions for markets needing resilient materials. These OEM silicon carbide (SiC) elements are crafted for severe conditions. They withstand temperatures up to 1650 ° C without losing architectural integrity. This makes them optimal for applications in furnaces, aerospace, and power systems. The material’s low thermal expansion makes certain stability under fast temperature changes. It stands up to oxidation and deterioration also in aggressive atmospheres.
Precision is a crucial emphasis. Advanced machining techniques develop parts with limited tolerances. Complicated geometries are possible. Components like nozzles, seals, and bearings keep accuracy under stress and anxiety. Surface surfaces can be customized to lower rubbing or improve wear resistance. This versatility suits automobile, semiconductor, and chemical processing markets.
Silicon carbide’s hardness goes beyond most metals and porcelains. It supplies exceptional abrasion resistance. Parts last much longer in high-wear circumstances. Electric conductivity choices are offered for specialized uses. The product is chemically inert. It executes reliably touching acids, alkalis, and molten metals.
Personalization drives the solution. Requirements match client demands. Measurements, forms, and efficiency features are customized. Prototyping support makes certain styles meet application requirements. Little or large manufacturing runs are accommodated. Quality control includes strenuous screening. Density, porosity, and toughness are confirmed. Each set fulfills sector requirements.
The manufacturing procedure utilizes premium-grade SiC powder. Sintering approaches enhance density and purity. Post-processing steps like grinding or covering add capability. Preparations are competitive. Technical support assists with product selection and design optimization.
These ceramic components decrease downtime in harsh operations. They manage thermal shock far better than conventional materials. Power efficiency enhances as a result of reduced warmth loss. Maintenance expenses drop as a result of prolonged service life. Compatibility with automated systems guarantees easy assimilation.
Industries gain from the equilibrium of performance and customization. High-temperature resistance paired with precision machining addresses vital obstacles. OEM collaborations concentrate on delivering options that boost functional integrity. Technical expertise backs every task from idea to final product.
(Carbide Customization Ceramic Parts OEM Silicon Carbide High Temperature Resistance Sic Silicone Precision)
Applications of Carbide Customization Ceramic Parts OEM Silicon Carbide High Temperature Resistance Sic Silicone Precision
Carbide customization ceramic parts made from silicon carbide (SiC) are utilized widely in markets needing high performance under severe problems. These components are understood for their extraordinary warmth resistance. They manage temperature levels over 1600 ° C without shedding strength. This makes them suitable for high-temperature settings like aerospace engines, commercial heaters, and power generation systems.
Silicon carbide parts are adjustable. Makers shape them into complicated styles to meet details needs. This flexibility fits sectors requiring accuracy components. Instances include semiconductor production equipment, chemical handling devices, and automotive stopping systems. The material’s firmness makes sure long-lasting performance even in abrasive setups.
OEM silicon carbide parts are prominent in the energy industry. Photovoltaic panel production counts on SiC elements for wafer handling. Wind turbines use them in bearings and seals because of their deterioration resistance. The electronic devices market benefits from SiC’s thermal conductivity. It aids manage warm in devices like LED lighting and power electronics.
Accuracy is essential for silicon carbide ceramic components. Limited tolerances guarantee they fit completely in innovative equipment. This accuracy reduces wear and downtime. Medical tools utilize these components for their biocompatibility and stability in sanitation processes.
Silicon carbide’s low thermal development prevents splitting under quick temperature level adjustments. This dependability is important in applications like rocket nozzles or metallurgical crucibles. The product stands up to chain reactions too. It works well in harsh environments with acids, alkalis, or molten steels.
Customization choices consist of layers or surface area therapies. These boost properties like electrical conductivity or put on resistance. OEMs companion with providers to establish tailored services. This collaboration ensures parts satisfy precise standards for performance and resilience.
Industries pick silicon carbide for its mix of toughness, warm resistance, and flexibility. It supports development in areas pushing the restrictions of technology. From electrical lorry parts to advanced ceramics in aerospace, SiC parts supply under pressure. Their function in enhancing efficiency and dependability makes them a key product for modern-day design obstacles.
Company Introduction
Advanced Ceramics founded on October 17, 2014, is a high-tech enterprise committed to the research and development, production, processing, sales and technical services of ceramic relative materials and products.. Since its establishment in 2014, the company has been committed to providing customers with the best products and services, and has become a leader in the industry through continuous technological innovation and strict quality management.
Our products includes but not limited to Silicon carbide ceramic products, Boron Carbide Ceramic Products, Boron Nitride Ceramic Products, Silicon Carbide Ceramic Products, Silicon Nitride Ceramic Products, Zirconium Dioxide Ceramic Products, Quartz Products, etc. Please feel free to contact us.(nanotrun@yahoo.com)
Payment Methods
T/T, Western Union, Paypal, Credit Card etc.
Shipment Methods
By air, by sea, by express, as customers request.
5 FAQs of Carbide Customization Ceramic Parts OEM Silicon Carbide High Temperature Resistance Sic Silicone Precision
What is Silicon Carbide (SiC) ceramic?
Silicon Carbide is a synthetic ceramic material. It combines high hardness, excellent thermal conductivity, and strong chemical resistance. These properties make it ideal for high-stress environments like aerospace, energy, and industrial manufacturing.
What are the benefits of OEM SiC ceramic parts?
OEM SiC parts offer custom shapes, sizes, and surface finishes. The material resists extreme temperatures, wear, and chemical reactions. Production methods like grinding, machining, and polishing ensure precise dimensions. Rigorous quality checks guarantee reliability in critical applications.
How does SiC handle high temperatures?
SiC withstands temperatures up to 1650°C without losing strength. Its low thermal expansion reduces cracking under rapid temperature changes. This stability suits applications like furnace components, heat exchangers, and turbine parts exposed to intense heat.
Can SiC parts be customized for specific needs?
Yes. Engineers work closely with clients to tailor parts to exact requirements. Customization covers complex geometries, tight tolerances, and specialized surface finishes. Advanced machining tools achieve precise results for industries needing high-performance solutions.
Where are SiC ceramic parts commonly used?
These parts serve aerospace, energy, semiconductor, and automotive sectors. Examples include components in semiconductor manufacturing tools, kiln furniture, and pump seals. The material’s durability ensures long-term performance in corrosive or high-wear environments.
Why choose SiC over other ceramics?
SiC outperforms materials like alumina or zirconia in thermal and mechanical stress. Its higher thermal conductivity improves heat management. Superior chemical inertness extends lifespan in aggressive environments, reducing replacement costs.
How is quality maintained during production?
Each batch undergoes strict testing for density, hardness, and dimensional accuracy. Non-destructive methods like X-ray inspection detect internal flaws. Certifications like ISO 9001 ensure processes meet global standards.
What industries benefit most from SiC parts?
Industries requiring heat-resistant, durable components rely on SiC. These include metal processing, chemical plants, and renewable energy systems. The material’s reliability supports efficient operations in harsh conditions.
Are SiC parts cost-effective long-term?
Initial costs may exceed traditional materials. Reduced downtime, lower maintenance, and longer service life offset this. The balance between performance and expense makes SiC a practical investment for demanding applications.
How to order custom SiC components?
Provide detailed specifications or consult with engineers for design support. Prototyping validates functionality before full-scale production. Lead times vary based on complexity, with standard options available for common requirements.
(Carbide Customization Ceramic Parts OEM Silicon Carbide High Temperature Resistance Sic Silicone Precision)
REQUEST A QUOTE
RELATED PRODUCTS
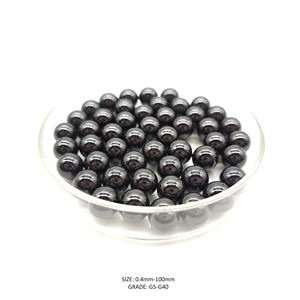
High Quality Factory Custom Alumina PE Plate Silicon Carbide Hard PE Ceramic Plate 10×12” III&IV Armor Plate
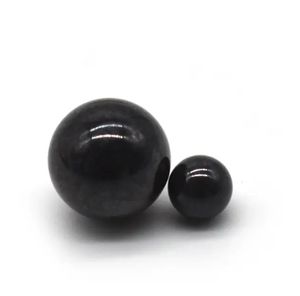
High Temperature Sic Pipe Roller Rod Heat Resistant Refractory Kiln Furniture Ceramic Silica Silicon Carbide Tube
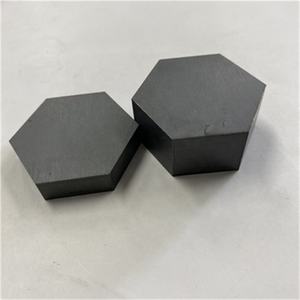
Hot ing SIC Ceramic Ceramic/SSIC Silicon Carbide Ceramic Plate Tile
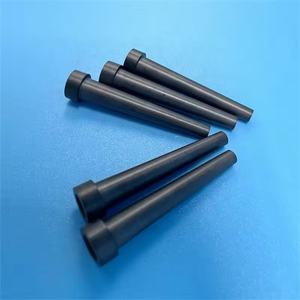
Hard Plate with B4C Silicon Carbide Tiles Polyethylene Ceramic SiC Ceramic Discs
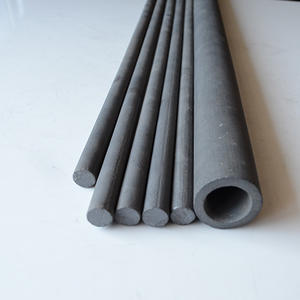
Customized Surface Polished Silicon Carbide Ceramic Rod Sic Ceramic Shaft
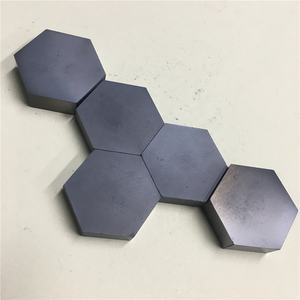