Discover Premium Ceramic Products | Durability & Elegance United | Advanced Ceramics
PRODUCT PARAMETERS
Description
Introduction to Alumina Ceramics
Alumina ceramics are known for their high hardness, wear resistance, corrosion resistance, good electrical insulation and high temperature stability. According to the different alumina content, it can be divided into different grades, such as 95 porcelain, 99 porcelain, etc., among which 99 porcelain refers to ceramic materials with an alumina content of 99%. As the alumina content increases, its mechanical strength and electrical insulation properties will also increase accordingly.
Characteristics of Alumina Ceramics
High Hardness: Alumina ceramics have extremely high hardness, which makes it very wear-resistant and suitable for manufacturing abrasive tools and parts that require wear resistance.
Wear resistance: Due to its high hardness, alumina ceramics show excellent wear resistance and are suitable for manufacturing parts for long-term use.
Corrosion resistance: Alumina ceramics have good resistance to most acids and alkalis, making them widely used in the chemical industry.
Good electrical insulation: As an excellent electrical insulating material, alumina ceramics are widely used in electronic and electrical products.
High temperature stability: Ability to withstand extremely high temperatures without significant physical or chemical changes, which makes it an ideal choice for applications in high temperature environments.
Biocompatibility: In the medical field, certain grades of alumina ceramics are used to make medical devices such as artificial joints due to their good biocompatibility.
(Corrosion Resistance Custom Ceramic 99% Alumina Ceramic Product)
Specifications of Corrosion Resistance Custom Ceramic 99% Alumina Ceramic Product
This product is made from 99% alumina ceramic, a high-purity material made for extreme rust resistance. It does well in acidic, alkaline, and high-temperature environments, preserving architectural honesty under extreme conditions. The make-up makes certain marginal chemical sensitivity, making it suitable for use with strong acids like sulfuric acid and hydrochloric acid, as well as strong bases such as salt hydroxide.
The material supplies high mechanical strength, with a Vickers hardness rating over 1500 HV. It withstands wear and abrasion properly, expanding service life popular applications. The flexural stamina surpasses 300 MPa, supplying dependability under hefty lots. Thermal stability is an essential function, with a maximum operating temperature of 1650 ° C. It manages quick temperature modifications without splitting, ideal for commercial procedures including thermal biking.
Customization alternatives include customized shapes, sizes, and surface finishes. Components like tubes, plates, and nozzles can be precision-machined to fulfill certain demands. Surface sprucing up or grinding is offered to achieve wanted roughness levels, enhancing performance in securing or friction-sensitive applications. Limited dimensional resistances are kept, making sure compatibility with existing systems.
Applications span industries such as chemical processing, semiconductor production, and metallurgy. It is made use of in pump seals, shutoff components, and activator cellular linings where corrosion resistance is critical. The electrical insulation buildings make it ideal for electronic substrates and protecting parts in high-voltage settings.
Quality assurance consists of strenuous testing for thickness, porosity, and chemical stability. Each set undertakes examination to validate conformity with sector requirements. The product fulfills ISO and ASTM specifications for alumina porcelains, ensuring regular performance. Product packaging is tailored to avoid damage throughout delivery, with safety materials customized to component size and fragility.
Technical assistance is offered for style optimization and material selection. Personalized remedies resolve special operational difficulties, from chemical direct exposure to mechanical tension. Examples can be attended to testing before massive orders. Lead times differ based upon complexity, with conventional designs normally shipped within two weeks.
(Corrosion Resistance Custom Ceramic 99% Alumina Ceramic Product)
Applications of Corrosion Resistance Custom Ceramic 99% Alumina Ceramic Product
Corrosion-resistant personalized ceramic items made from 99% alumina are utilized in many markets where products deal with harsh problems. These porcelains stand up to damages from chemicals, heats, and use. They function well in settings where steels or plastics fail.
In chemical handling, 99% alumina ceramic parts handle acids, antacid, and solvents. Shutoffs, pumps, and activator liners made from this material last much longer. They lower downtime and maintenance prices. These parts keep chemical reactions steady even under severe stress or heat.
Semiconductor making usages these ceramics for wafer carriers, insulators, and reducing devices. The product’s high purity prevents contamination during manufacturing. It takes care of high temperatures in heaters and plasma environments. This makes certain regular high quality in microchips and digital elements.
Medical tools benefit from alumina porcelains. Surgical devices, implants, and lab tools need materials that stand up to body liquids and sterilization. These porcelains are non-reactive and long lasting. They meet rigorous health requirements in medical facilities and labs.
Power generation depends on alumina ceramics for elements in wind turbines, central heating boilers, and warm exchangers. The product endures steam, combustion gases, and thermal cycling. It enhances effectiveness and decreases tools failure in power plants.
Mining and oil boring use alumina porcelains for wear-resistant parts. Pump seals, nozzles, and valve components deal with rough slurries and harsh liquids. This prolongs devices life in rough operating problems.
These porcelains are also made use of in automotive and aerospace. Sensors, bearings, and engine parts made from alumina handle high anxiety and temperature level. They boost efficiency and integrity in lorries and aircraft.
Custom-made sizes and shapes are possible with 99% alumina ceramics. Manufacturers tailor items for details requirements. This versatility makes the material suitable for special commercial obstacles.
The high firmness and stamina of alumina porcelains prevent scrapes and splits. They keep efficiency over time. Industries pick this material to cut prices and improve efficiency.
Company Introduction
Advanced Ceramics founded on October 17, 2014, is a high-tech enterprise committed to the research and development, production, processing, sales and technical services of ceramic relative materials and products.. Since its establishment in 2014, the company has been committed to providing customers with the best products and services, and has become a leader in the industry through continuous technological innovation and strict quality management.
Our products includes but not limited to Silicon carbide ceramic products, Boron Carbide Ceramic Products, Boron Nitride Ceramic Products, Silicon Carbide Ceramic Products, Silicon Nitride Ceramic Products, Zirconium Dioxide Ceramic Products, Quartz Products, etc. Please feel free to contact us.(nanotrun@yahoo.com)
Payment Methods
T/T, Western Union, Paypal, Credit Card etc.
Shipment Methods
By air, by sea, by express, as customers request.
5 FAQs of Corrosion Resistance Custom Ceramic 99% Alumina Ceramic Product
What is 99% alumina ceramic?
99% alumina ceramic is a high-performance material made mostly from aluminum oxide. It is produced by firing raw alumina at very high temperatures. This process creates a dense, hard structure. The material is known for its strength and durability. It is commonly used in harsh environments where resistance to wear and chemicals is critical.
How does alumina ceramic resist corrosion?
Alumina ceramic resists corrosion because of its stable chemical structure. It does not react with most acids, alkalis, or solvents. Even in high-temperature or high-pressure conditions, it maintains its integrity. This makes it ideal for use in chemical processing, medical equipment, and industrial machinery exposed to aggressive substances.
What temperatures can alumina ceramic handle?
Alumina ceramic works well in temperatures up to 1600°C (2912°F). It keeps its strength and shape under extreme heat. This property makes it suitable for furnace components, welding nozzles, and aerospace parts. It also resists thermal shock, meaning sudden temperature changes cause minimal damage.
Where is alumina ceramic commonly used?
This material is used in industries needing reliable performance in tough conditions. Examples include electronics (insulating components), automotive (sensors and seals), and medical (surgical tools). Its wear resistance also makes it useful for cutting tools, pump parts, and valves in mining or manufacturing.
How do I maintain alumina ceramic products?
Alumina ceramic requires little maintenance. Clean it with water or mild solvents to remove debris. Avoid using abrasive materials that could scratch the surface. Inspect regularly for cracks or chips, though damage is rare due to its hardness. Proper handling during installation prevents unnecessary stress on the material.
(Corrosion Resistance Custom Ceramic 99% Alumina Ceramic Product)
REQUEST A QUOTE
RELATED PRODUCTS
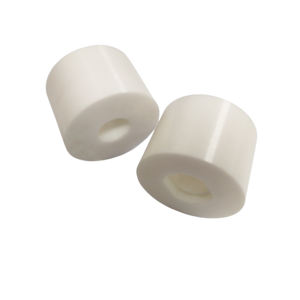
99% Alumina Ceramic Plate for Semiconductor/Medical/Electronics, High Purity, Wear Resistant, Insulating
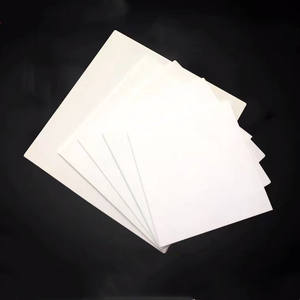
99 Ceramic Machining Parts 95 96 99 99.8 Al2O3 Alumina Ceramic
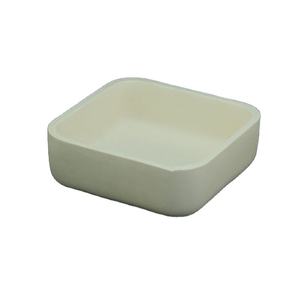
Square / Hexagon Al2o3 Alumina Ceramic Tiles and Plates
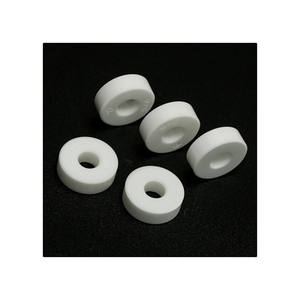
Customization 99% Alumina Ceramic Tube For Furnace Heater
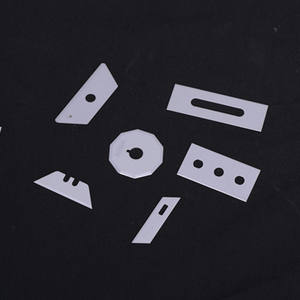
Alumina Ceramic Material and Industrial Ceramic Application Honeycomb Ceramic for RTO RCO
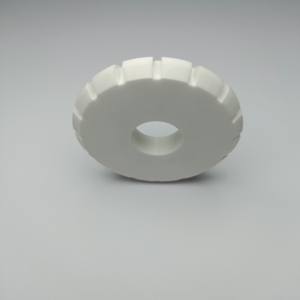