Discover Premium Ceramic Products | Durability & Elegance United | Advanced Ceramics
PRODUCT PARAMETERS
Description
Introduction to Alumina Ceramics
Alumina ceramics are known for their high hardness, wear resistance, corrosion resistance, good electrical insulation and high temperature stability. According to the different alumina content, it can be divided into different grades, such as 95 porcelain, 99 porcelain, etc., among which 99 porcelain refers to ceramic materials with an alumina content of 99%. As the alumina content increases, its mechanical strength and electrical insulation properties will also increase accordingly.
Characteristics of Alumina Ceramics
High Hardness: Alumina ceramics have extremely high hardness, which makes it very wear-resistant and suitable for manufacturing abrasive tools and parts that require wear resistance.
Wear resistance: Due to its high hardness, alumina ceramics show excellent wear resistance and are suitable for manufacturing parts for long-term use.
Corrosion resistance: Alumina ceramics have good resistance to most acids and alkalis, making them widely used in the chemical industry.
Good electrical insulation: As an excellent electrical insulating material, alumina ceramics are widely used in electronic and electrical products.
High temperature stability: Ability to withstand extremely high temperatures without significant physical or chemical changes, which makes it an ideal choice for applications in high temperature environments.
Biocompatibility: In the medical field, certain grades of alumina ceramics are used to make medical devices such as artificial joints due to their good biocompatibility.
(Advanced Molding Ceramics Custom High Temperature Alumina Zirconia Ceramic SIC Ceramics Structural Parts)
Specifications of Advanced Molding Ceramics Custom High Temperature Alumina Zirconia Ceramic SIC Ceramics Structural Parts
Our advanced molding porcelains are developed for high-performance applications requiring accuracy and longevity. These custom-made ceramic components are made from products like alumina, zirconia, and silicon carbide (SIC). They deal with severe temperature levels, mechanical stress and anxiety, and harsh environments successfully. Alumina ceramics provide high-temperature resistance approximately 1600 ° C. They are strong and wear-resistant, ideal for industrial machinery and electronics. Zirconia porcelains master durability and thermal shock resistance. They work well in temperatures up to 2400 ° C, ideal for aerospace components and clinical tools. SIC ceramics offer remarkable thermal conductivity and oxidation resistance. They carry out dependably in temperatures over 1600 ° C, excellent for heater components and power systems.
These ceramics are chemically stable. They resist deterioration from acids, antacid, and molten steels. This makes them helpful in chemical handling and metallurgy. Their low thermal expansion decreases fracturing under rapid temperature modifications. Mechanical toughness is a key feature. Alumina reaches 300-400 MPa in flexural toughness. Zirconia attains over 1000 MPa, making it remarkably sturdy. SIC maintains structural honesty under hefty lots and high stress and anxiety.
Personalization is a top priority. Parts are made to exact dimensions and forms using innovative molding techniques. Alternatives include injection molding, dry pressing, and isostatic pressing. Surface surfaces can be adjusted for smoothness or roughness. Limited resistances ensure compatibility with industrial devices. Electrical insulation homes are another advantage. Alumina and zirconia stop electric conductivity, useful in electronics and power systems.
Applications cover several sectors. Aerospace uses these porcelains for engine elements and heat shields. Automotive systems rely on them for sensing units and exhaust components. Medical tools take advantage of their biocompatibility and use resistance. Energy sectors use them in generators and solar tools. Production tools made from these porcelains last longer under unpleasant problems.
These porcelains are examined carefully for top quality. Tests include thermal biking, stress resistance, and chemical direct exposure. This ensures dependability in real-world conditions. Materials are sourced for pureness and consistency. Manufacturing procedures reduce flaws. The outcome is high-performance ceramics that satisfy rigorous sector standards.
(Advanced Molding Ceramics Custom High Temperature Alumina Zirconia Ceramic SIC Ceramics Structural Parts)
Applications of Advanced Molding Ceramics Custom High Temperature Alumina Zirconia Ceramic SIC Ceramics Structural Parts
Company Introduction
Advanced Ceramics founded on October 17, 2014, is a high-tech enterprise committed to the research and development, production, processing, sales and technical services of ceramic relative materials and products.. Since its establishment in 2014, the company has been committed to providing customers with the best products and services, and has become a leader in the industry through continuous technological innovation and strict quality management.
Our products includes but not limited to Silicon carbide ceramic products, Boron Carbide Ceramic Products, Boron Nitride Ceramic Products, Silicon Carbide Ceramic Products, Silicon Nitride Ceramic Products, Zirconium Dioxide Ceramic Products, Quartz Products, etc. Please feel free to contact us.(nanotrun@yahoo.com)
Payment Methods
T/T, Western Union, Paypal, Credit Card etc.
Shipment Methods
By air, by sea, by express, as customers request.
5 FAQs of Advanced Molding Ceramics Custom High Temperature Alumina Zirconia Ceramic SIC Ceramics Structural Parts
What materials are used in Advanced Molding Ceramics?
Alumina, zirconia, and silicon carbide (SIC) are the main materials. These ceramics handle extreme heat and wear. Alumina resists corrosion and electrical insulation. Zirconia offers high strength and toughness. SIC works well in thermal shock environments. All materials suit industrial applications needing durability.
How much heat can these ceramics withstand?
Alumina handles up to 1700°C. Zirconia withstands around 2400°C. SIC works reliably up to 1650°C. Exact limits depend on part design and conditions. These ceramics keep their shape and strength even under prolonged heat. They outperform metals and plastics in high-temperature settings.
Can these parts be customized?
Yes. Advanced molding allows complex shapes and sizes. Techniques like injection molding or dry pressing create precise components. Post-processing (grinding, polishing) ensures tight tolerances. Custom parts match specific machinery or system needs. Technical drawings or samples help tailor designs.
Where are these ceramics commonly used?
They appear in aerospace, automotive, and industrial sectors. Examples include furnace linings, turbine blades, and semiconductor tools. High-temperature sensors, cutting tools, and wear-resistant seals rely on these materials. They replace metal parts in harsh environments.
How do I choose between alumina, zirconia, and SIC?
Alumina suits moderate heat and electrical insulation needs. Zirconia fits high-stress, high-temperature applications needing fracture resistance. SIC excels in thermal conductivity and extreme thermal cycling. Consider operating conditions, mechanical loads, and budget. Testing prototypes helps confirm material performance.
(Advanced Molding Ceramics Custom High Temperature Alumina Zirconia Ceramic SIC Ceramics Structural Parts)
REQUEST A QUOTE
RELATED PRODUCTS
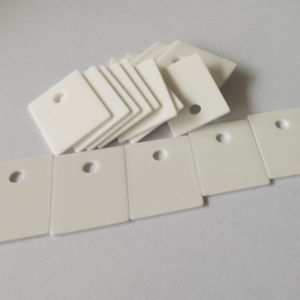
High Quality Alumina Ceramic Tiles 99.9% Purity
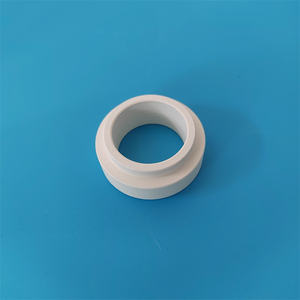
Al2o3 Crucible Alumina Ceramic High Refractoriness Alumina Al2O3 Ceramic Crucible
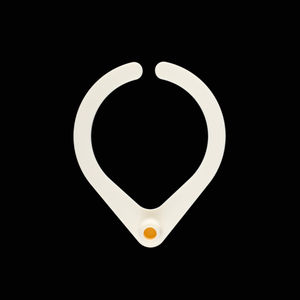
96 Alumina Ceramic Substrate
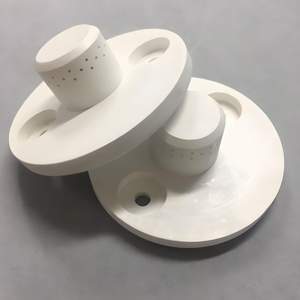
Industrial Alumina Ceramic Tube 99 Al2o3 Fireproof Alumina Tube Circle Alumina Tube
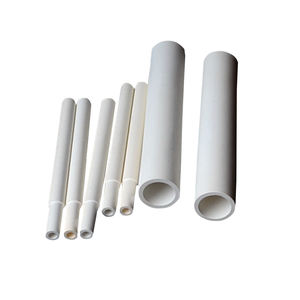
Laboratory Processes Alumina Ceramic Crucible
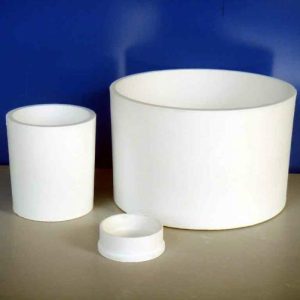