Discover Premium Ceramic Products | Durability & Elegance United | Advanced Ceramics
PRODUCT PARAMETERS
Description
Introduction to Alumina Ceramics
Alumina ceramics are known for their high hardness, wear resistance, corrosion resistance, good electrical insulation and high temperature stability. According to the different alumina content, it can be divided into different grades, such as 95 porcelain, 99 porcelain, etc., among which 99 porcelain refers to ceramic materials with an alumina content of 99%. As the alumina content increases, its mechanical strength and electrical insulation properties will also increase accordingly.
Characteristics of Alumina Ceramics
High Hardness: Alumina ceramics have extremely high hardness, which makes it very wear-resistant and suitable for manufacturing abrasive tools and parts that require wear resistance.
Wear resistance: Due to its high hardness, alumina ceramics show excellent wear resistance and are suitable for manufacturing parts for long-term use.
Corrosion resistance: Alumina ceramics have good resistance to most acids and alkalis, making them widely used in the chemical industry.
Good electrical insulation: As an excellent electrical insulating material, alumina ceramics are widely used in electronic and electrical products.
High temperature stability: Ability to withstand extremely high temperatures without significant physical or chemical changes, which makes it an ideal choice for applications in high temperature environments.
Biocompatibility: In the medical field, certain grades of alumina ceramics are used to make medical devices such as artificial joints due to their good biocompatibility.
(Alumina Ceramics Have Strong Chemical Stability and Resist Erosion in the Harsh Environment of Lime Kilns)
Specifications of Alumina Ceramics Have Strong Chemical Stability and Resist Erosion in the Harsh Environment of Lime Kilns
Alumina ceramics are crafted products understood for their exceptional performance in demanding commercial setups. These porcelains are made from high-purity aluminum oxide. They show strong chemical stability. This makes them ideal for use in environments like lime kilns where exposure to harsh chemicals and severe problems is common. The material withstands erosion brought on by antacid, acids, and unpleasant substances. This resistance ensures long-term integrity also under constant stress and anxiety.
The primary part of alumina ceramics is aluminum oxide. Content ranges from 95% to 99%. Greater pureness levels enhance rust resistance. This is vital in lime kilns. Lime kilns run at heats. They generate reactive compounds like calcium oxide. These substances attack weaker products. Alumina ceramics stay untouched. Their thick structure stops chemical penetration. Surface destruction is lessened. Upkeep expenses drop. Tools life-span expands.
Thermal stability is one more vital function. Alumina porcelains handle temperatures up to 1600 ° C. Thermal shock resistance is high. Fast temperature changes do not trigger cracking. Lime kilns commonly experience rising and falling warmth levels. Standard materials fall short under such problems. Alumina ceramics preserve honesty. Downtime lowers. Efficiency boosts.
Mechanical toughness transcends. Alumina porcelains have a hardness rating of 8-9 on the Mohs scale. They endure abrasion from resources like limestone. Wear-resistant components last longer. Replacement regularity reduces. Operational effectiveness rises.
Electrical insulation residential properties include value. Lime kilns make use of high-voltage systems. Alumina ceramics stop electrical conductivity. Security risks lower. Devices operates efficiently.
Applications consist of kiln cellular linings, thermocouple tubes, and burner nozzles. These elements deal with direct exposure to flames, dirt, and destructive gases. Alumina porcelains outshine metals and polymers. They stay clear of melting, bending, or liquifying.
Custom-made sizes and shapes are achievable. Suppliers customize alumina ceramic components to fit particular kiln layouts. Compatibility with existing systems is seamless. Installment is straightforward. No significant alterations are required.
Expense cost savings arise from decreased product waste and energy use. Alumina ceramics call for no protective layers. Power intake stays reduced. Handling rates remain high.
Lime kiln operators focus on longevity and effectiveness. Alumina ceramics meet these demands. Their mix of chemical inertness, thermal durability, and mechanical durability makes them a sensible selection for harsh industrial atmospheres.
(Alumina Ceramics Have Strong Chemical Stability and Resist Erosion in the Harsh Environment of Lime Kilns)
Applications of Alumina Ceramics Have Strong Chemical Stability and Resist Erosion in the Harsh Environment of Lime Kilns
Alumina porcelains are widely used in lime kilns. The severe conditions in these atmospheres demand materials with phenomenal toughness. Alumina ceramics satisfy this demand. Their strong chemical stability permits them to withstand destructive compounds. Lime kilns generate hostile gases and high-alkali products throughout operation. These ceramics continue to be untouched. They keep architectural honesty even under extended exposure. This makes them suitable for elements exposed to chemical reactions.
Heats prevail in lime kilns. Alumina ceramics deal with severe heat properly. They hold up against temperature levels surpassing 1600 ° C without deteriorating. Thermal shock resistance avoids splitting throughout quick temperature level adjustments. This reliability decreases downtime for maintenance.
Abrasion is an additional obstacle in lime kilns. Resources like limestone and fuel ash reason wear. Alumina ceramics have high firmness. They withstand damaging and erosion from unpleasant particles. This extends the life-span of kiln linings and tools.
Applications consist of safety cellular linings for kiln insides. These cellular linings shield the kiln structure from direct contact with rough materials. Alumina ceramic tubes and nozzles are made use of for transferring warm gases or molten substances. Their smooth surface minimizes product build-up. This makes sure constant air movement and procedure performance.
Thermocouple sheaths made from alumina ceramics give accurate temperature tracking. They shield sensors from corrosive gases and physical damage. This ensures specific control over kiln conditions.
Cost cost savings come from reduced replacement regularity. Alumina porcelains last much longer than standard materials like steel or refractory bricks. Their resistance to numerous kinds of damages lowers functional costs.
Lime manufacturing needs steady and dependable equipment. Alumina ceramics make sure continuous procedure. They execute under mechanical tension, chemical direct exposure, and thermal extremes. Industries gain from boosted productivity. Maintenance periods are extended. Downtime is minimized.
The mix of chemical inertness, thermal strength, and mechanical strength makes alumina porcelains a functional option for lime kilns. Their versatility to requiring environments sustains reliable and sustainable industrial procedures.
Company Introduction
Advanced Ceramics founded on October 17, 2014, is a high-tech enterprise committed to the research and development, production, processing, sales and technical services of ceramic relative materials and products.. Since its establishment in 2014, the company has been committed to providing customers with the best products and services, and has become a leader in the industry through continuous technological innovation and strict quality management.
Our products includes but not limited to Silicon carbide ceramic products, Boron Carbide Ceramic Products, Boron Nitride Ceramic Products, Silicon Carbide Ceramic Products, Silicon Nitride Ceramic Products, Zirconium Dioxide Ceramic Products, Quartz Products, etc. Please feel free to contact us.(nanotrun@yahoo.com)
Payment Methods
T/T, Western Union, Paypal, Credit Card etc.
Shipment Methods
By air, by sea, by express, as customers request.
5 FAQs of Alumina Ceramics Have Strong Chemical Stability and Resist Erosion in the Harsh Environment of Lime Kilns
Alumina ceramics handle harsh lime kiln environments well. People often ask how they work. Here are answers.
What makes alumina ceramics good for lime kilns? They stay stable chemically. They resist acids, alkalis, high heat. Lime kilns have corrosive gases, dust, temperature swings. Alumina ceramics don’t break down. They last longer than metals or plastics.
Do alumina ceramics handle high temperatures? Yes. They work in temperatures over 1600°C. Metals melt or warp at lower heats. Alumina keeps strength. Sudden temperature changes don’t crack them. This matters in lime kilns where heating cycles are extreme.
Which chemicals do alumina ceramics resist? They fight lime dust, alkalis, acidic fumes. Lime kilns produce these during production. Alumina doesn’t react with most chemicals. Rust or decay won’t happen.
How long do alumina parts last in lime kilns? Much longer than other materials. Metals corrode fast. Plastics melt. Alumina wears slowly. Replacements happen less often. This cuts downtime and costs.
Do alumina ceramics need special care? No. They don’t need coatings or treatments. Regular cleaning checks are enough. Their built-in resistance means less maintenance. Workers focus on other tasks.
Alumina ceramics fit lime kilns because they ignore heat, chemicals, wear. Factories save money. Production stays steady.
(Alumina Ceramics Have Strong Chemical Stability and Resist Erosion in the Harsh Environment of Lime Kilns)
REQUEST A QUOTE
RELATED PRODUCTS
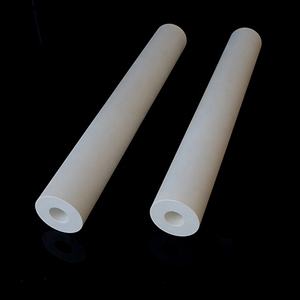
Industrial Electrical Technical Machinery Custom High Heat Resistant Ceramics Alumina Structural Parts
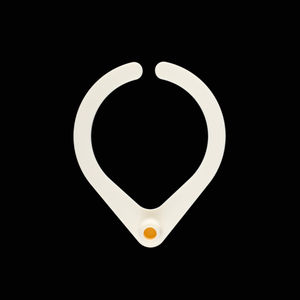
96 Alumina Ceramic Substrate
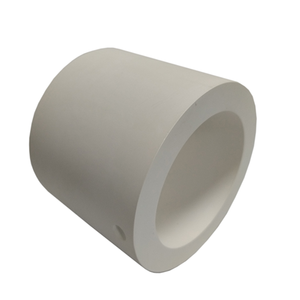
Porous Alumina Ceramic Ball Premium Ceramics Product
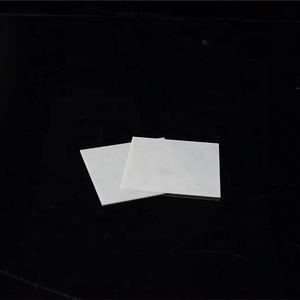
Precision 99% alumina ceramic round rod
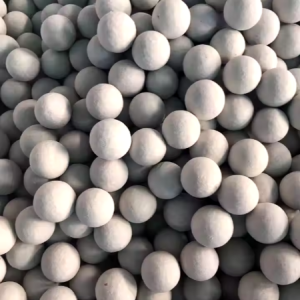
Al2O3 Ceramic 6mm,20mm Inert Alumina Ceramic Ball as Catalyst Support Media Ceramic Ball
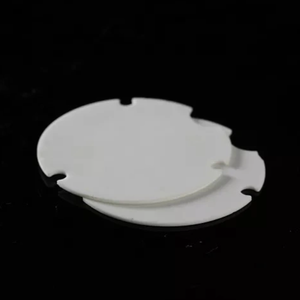