Discover Premium Ceramic Products | Durability & Elegance United | Advanced Ceramics
PRODUCT PARAMETERS
Description
Introduction to Alumina Ceramics
Alumina ceramics are known for their high hardness, wear resistance, corrosion resistance, good electrical insulation and high temperature stability. According to the different alumina content, it can be divided into different grades, such as 95 porcelain, 99 porcelain, etc., among which 99 porcelain refers to ceramic materials with an alumina content of 99%. As the alumina content increases, its mechanical strength and electrical insulation properties will also increase accordingly.
Characteristics of Alumina Ceramics
High Hardness: Alumina ceramics have extremely high hardness, which makes it very wear-resistant and suitable for manufacturing abrasive tools and parts that require wear resistance.
Wear resistance: Due to its high hardness, alumina ceramics show excellent wear resistance and are suitable for manufacturing parts for long-term use.
Corrosion resistance: Alumina ceramics have good resistance to most acids and alkalis, making them widely used in the chemical industry.
Good electrical insulation: As an excellent electrical insulating material, alumina ceramics are widely used in electronic and electrical products.
High temperature stability: Ability to withstand extremely high temperatures without significant physical or chemical changes, which makes it an ideal choice for applications in high temperature environments.
Biocompatibility: In the medical field, certain grades of alumina ceramics are used to make medical devices such as artificial joints due to their good biocompatibility.
(Alumina Ceramics Have Strong Chemical Stability and Resist Erosion in the Harsh Environment of Lime Kilns)
Specifications of Alumina Ceramics Have Strong Chemical Stability and Resist Erosion in the Harsh Environment of Lime Kilns
Alumina porcelains stand out for their exceptional chemical security. These products manage rough settings properly. Lime kilns present severe conditions. High temperatures, destructive gases, and unpleasant lime dirt are common. Alumina ceramics withstand these obstacles reliably. The primary part is aluminum oxide. Web content varieties from 92% to 99.5%. Higher pureness enhances efficiency. This makes them perfect for requiring commercial setups.
The product’s hardness is a vital advantage. It rates simply listed below diamonds on the Mohs range. This firmness ensures minimal wear over time. Elements last longer under mechanical tension. Thermal shock resistance is another critical attribute. Fast temperature level changes happen in lime kilns. Alumina ceramics withstand these changes without breaking.
Chemical resistance is vital in lime kilns. Alkaline compounds like calcium hydroxide exist. Acidic by-products may create throughout burning. Alumina ceramics stay untouched by both. They do not respond with many chemicals. This prevents degradation. The product keeps structural stability even after prolonged exposure.
High-temperature performance is similarly vital. Lime kilns operate in between 900 ° C and 1300 ° C. Alumina ceramics retain stamina at these levels. Their melting point exceeds 2000 ° C. This makes certain security in the kiln’s hottest zones. Thermal expansion is low. Dimensional accuracy remains regular throughout home heating cycles.
Surface area level of smoothness includes in their longevity. Lime fragments are extremely abrasive. Rough surface areas would put on down faster. Alumina ceramics have a polished finish. This lowers rubbing. Erosion from lime dirt reduces substantially.
Electrical insulation buildings issue in kiln settings. Electrical systems are typically close-by. Alumina ceramics protect against brief circuits. They withstand electric currents even at high temperatures.
These porcelains are adjustable. Manufacturers form them right into facility geometries. Tiles, tubes, and linings are common forms. Precision machining makes certain limited tolerances. This permits smooth assimilation right into existing kiln arrangements.
Upkeep expenses go down with alumina porcelains. Downtime is decreased. Replacement periods prolong. Operators gain from trustworthy performance year-round. Industries focus on products that reduce lasting expenses. Alumina porcelains satisfy this need.
Ecological aspects are critical. Lime manufacturing creates hostile by-products. Equipment has to endure without regular repair services. Alumina ceramics provide a lasting remedy. Waste from substitutes decreases. Functional efficiency boosts.
The mix of properties makes alumina porcelains a leading selection. Lime kilns demand products that do under stress. This product delivers constantly.
(Alumina Ceramics Have Strong Chemical Stability and Resist Erosion in the Harsh Environment of Lime Kilns)
Applications of Alumina Ceramics Have Strong Chemical Stability and Resist Erosion in the Harsh Environment of Lime Kilns
Company Introduction
Advanced Ceramics founded on October 17, 2014, is a high-tech enterprise committed to the research and development, production, processing, sales and technical services of ceramic relative materials and products.. Since its establishment in 2014, the company has been committed to providing customers with the best products and services, and has become a leader in the industry through continuous technological innovation and strict quality management.
Our products includes but not limited to Silicon carbide ceramic products, Boron Carbide Ceramic Products, Boron Nitride Ceramic Products, Silicon Carbide Ceramic Products, Silicon Nitride Ceramic Products, Zirconium Dioxide Ceramic Products, Quartz Products, etc. Please feel free to contact us.(nanotrun@yahoo.com)
Payment Methods
T/T, Western Union, Paypal, Credit Card etc.
Shipment Methods
By air, by sea, by express, as customers request.
5 FAQs of Alumina Ceramics Have Strong Chemical Stability and Resist Erosion in the Harsh Environment of Lime Kilns
Alumina ceramics stand out in harsh lime kiln environments. Here are common questions about their performance. Why choose alumina ceramics for lime kilns? Lime kilns expose materials to high heat, chemical reactions, wear. Alumina ceramics handle these conditions well. Their dense structure stops chemicals from penetrating. This keeps them stable even with constant exposure to alkalis, acids, gases. What chemicals do alumina ceramics resist? They resist most acids, alkalis, salts. Lime kilns produce corrosive substances like calcium hydroxide, sulfur compounds. Alumina ceramics do not react with these chemicals. This prevents breakdown over time. How hot can alumina ceramics handle? They work in temperatures up to 1600°C. Lime kilns often reach 1200-1400°C. Other materials warp or crack here. Alumina ceramics stay strong. Their thermal stability avoids damage from sudden temperature changes. Do alumina ceramics last longer than metal parts? Yes. Metals corrode quickly in lime kilns. Protective coatings wear off. Alumina ceramics do not rust. Their hardness resists abrasion from lime particles. This cuts replacement costs. Maintenance needs drop. Are alumina ceramics hard to install? No. They come as linings, tiles, custom shapes. Fitting them into kilns is straightforward. Their light weight helps. Workers replace old linings without major downtime. No special tools are needed. Alumina ceramics keep lime kilns running longer with less stops. Their toughness against heat, chemicals, wear makes them reliable. Industries save money by reducing part changes.
(Alumina Ceramics Have Strong Chemical Stability and Resist Erosion in the Harsh Environment of Lime Kilns)
REQUEST A QUOTE
RELATED PRODUCTS
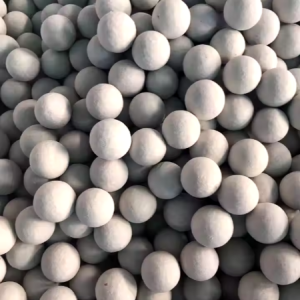
Al2O3 Ceramic 6mm,20mm Inert Alumina Ceramic Ball as Catalyst Support Media Ceramic Ball
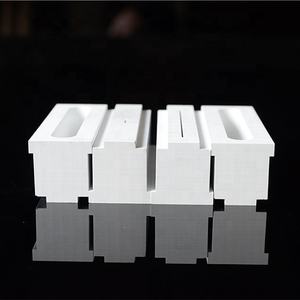
Customized Top Quality Wear Resistant Corrosion Resistant Alumina Zirconia Ceramic Industry Parts
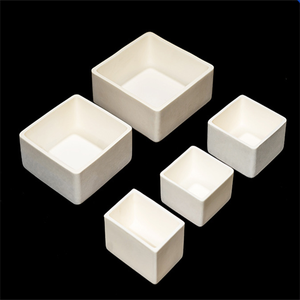
Custom Alumina Ceramic Al2o3 Boats
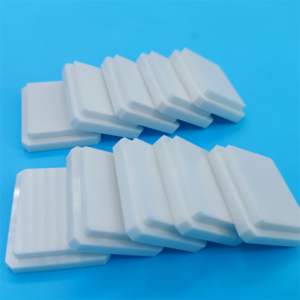
Precision Ceramic Tubes High Temperature Resistant High Hardness 99% Alumina Ceramic Parts
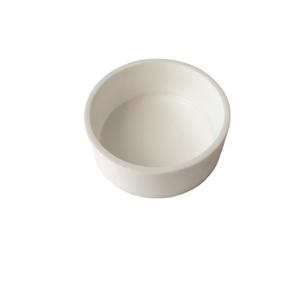
High-quality 99.7% Al2o3 Alumina Ceramic Products
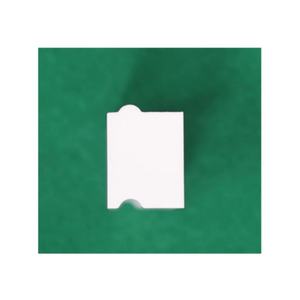