Discover Premium Ceramic Products | Durability & Elegance United | Advanced Ceramics
PRODUCT PARAMETERS
Description
Introduction to Alumina Ceramics
Alumina ceramics are known for their high hardness, wear resistance, corrosion resistance, good electrical insulation and high temperature stability. According to the different alumina content, it can be divided into different grades, such as 95 porcelain, 99 porcelain, etc., among which 99 porcelain refers to ceramic materials with an alumina content of 99%. As the alumina content increases, its mechanical strength and electrical insulation properties will also increase accordingly.
Characteristics of Alumina Ceramics
High Hardness: Alumina ceramics have extremely high hardness, which makes it very wear-resistant and suitable for manufacturing abrasive tools and parts that require wear resistance.
Wear resistance: Due to its high hardness, alumina ceramics show excellent wear resistance and are suitable for manufacturing parts for long-term use.
Corrosion resistance: Alumina ceramics have good resistance to most acids and alkalis, making them widely used in the chemical industry.
Good electrical insulation: As an excellent electrical insulating material, alumina ceramics are widely used in electronic and electrical products.
High temperature stability: Ability to withstand extremely high temperatures without significant physical or chemical changes, which makes it an ideal choice for applications in high temperature environments.
Biocompatibility: In the medical field, certain grades of alumina ceramics are used to make medical devices such as artificial joints due to their good biocompatibility.
(Alumina Ceramic Material and Industrial Ceramic Application Honeycomb Ceramic for RTO RCO)
Specifications of Alumina Ceramic Material and Industrial Ceramic Application Honeycomb Ceramic for RTO RCO
Alumina ceramic product is a high-performance industrial ceramic. It includes aluminum oxide as the major component. The purity degree usually ranges from 92% to 99.5%. This material functions well in extreme problems. It deals with temperatures up to 1600 ° C without losing strength. It resists wear, deterioration, and thermal shock. These properties make it appropriate for requiring applications. Industries utilize alumina porcelains in equipment parts, electrical insulators, and chemical handling devices.
Honeycomb ceramic frameworks prevail in RTO (Regenerative Thermal Oxidizer) and RCO (Regenerative Catalytic Oxidizer) systems. These systems regulate hazardous emissions from commercial processes. The honeycomb layout raises surface area. This improves warmth exchange efficiency. Alumina-based honeycomb ceramics soak up and store warmth properly. They ensure stable combustion of unpredictable natural substances. The product’s low thermal expansion stops cracking under fast temperature level changes.
Producers form honeycomb porcelains utilizing extrusion or pressing methods. The cells per square inch differ based upon application needs. Higher cell density enhances gas call. This improves toxin removal prices. Alumina porcelains in RTO/RCO systems lower power intake. They recover warmth from exhaust gases. This cuts gas costs and decreases exhausts.
Customizable pore sizes and geometries adjust to details commercial requirements. The material’s chemical inertness prevents responses with acidic or alkaline gases. This extends the life span of RTO/RCO parts. Routine upkeep is minimal. Substitute cycles are longer contrasted to metal options.
Industrial ceramic applications require precision design. Alumina porcelains fulfill stringent mechanical and thermal criteria. They make certain trusted efficiency in continual operations. Their duty in emission control supports environmental regulations. Manufacturing facilities achieve cleaner production processes. Energy performance straightens with sustainability goals.
(Alumina Ceramic Material and Industrial Ceramic Application Honeycomb Ceramic for RTO RCO)
Applications of Alumina Ceramic Material and Industrial Ceramic Application Honeycomb Ceramic for RTO RCO
Alumina ceramic material is commonly used in commercial setups due to its high-temperature resistance and chemical security. It deals with extreme warm without damaging down. This makes it ideal for insulation components in thermal systems. Alumina porcelains also resist deterioration from extreme chemicals. This building is crucial in atmospheres with hostile gases or fluids. Mechanical toughness is an additional vital benefit. Components made from alumina ceramics last much longer under stress. They lower upkeep demands and downtime in industrial operations. Common applications include catalyst supports, heater nozzles, and safety cellular linings. These parts make sure effective energy use and consistent efficiency in high-heat processes.
Industrial ceramic honeycomb frameworks are vital for RTO (Regenerative Thermal Oxidizer) and RCO (Regenerative Catalytic Oxidizer) systems. The honeycomb layout offers a large area. This makes best use of get in touch with in between gases and stimulants or warmth exchange media. It improves the effectiveness of contaminant removal. The ceramic product holds up against fast temperature level adjustments. This protects against breaking throughout home heating and cooling cycles. Honeycomb porcelains in RTO systems store and transfer warmth efficiently. This lowers fuel intake by reusing thermal power. In RCO systems, the honeycomb framework holds drivers that break down dangerous gases. This dual function supports cleaner exhausts and conformity with environmental policies.
Combining alumina porcelains with honeycomb designs improves efficiency in commercial applications. Alumina-based honeycombs supply higher thermal shock resistance. They preserve structural stability even under duplicated thermal stress and anxiety. These products are utilized in gas generators, chemical activators, and exhaust treatment systems. Their resilience makes certain lasting reliability popular problems. Industrial fields like petrochemicals, power generation, and metallurgy benefit from these options. The products aid markets satisfy stricter emission requirements while maximizing functional prices.
Alumina porcelains and honeycomb structures are tailored for specific industrial requirements. Personalized forms and pore sizes improve performance in various systems. Engineers choose these materials for their capacity to handle severe atmospheres. The mix of warm resistance, chemical security, and mechanical strength makes them crucial in contemporary manufacturing. Their function in RTO and RCO systems highlights their importance in lasting commercial techniques.
Company Introduction
Advanced Ceramics founded on October 17, 2014, is a high-tech enterprise committed to the research and development, production, processing, sales and technical services of ceramic relative materials and products.. Since its establishment in 2014, the company has been committed to providing customers with the best products and services, and has become a leader in the industry through continuous technological innovation and strict quality management.
Our products includes but not limited to Silicon carbide ceramic products, Boron Carbide Ceramic Products, Boron Nitride Ceramic Products, Silicon Carbide Ceramic Products, Silicon Nitride Ceramic Products, Zirconium Dioxide Ceramic Products, Quartz Products, etc. Please feel free to contact us.(nanotrun@yahoo.com)
Payment Methods
T/T, Western Union, Paypal, Credit Card etc.
Shipment Methods
By air, by sea, by express, as customers request.
5 FAQs of Alumina Ceramic Material and Industrial Ceramic Application Honeycomb Ceramic for RTO RCO
Alumina ceramic material is a high-performance industrial ceramic. It is made from aluminum oxide. It has high hardness, wear resistance, and thermal stability. These properties make it ideal for harsh environments. Industries use it in machinery components, insulators, and chemical processing equipment.
What is alumina ceramic material used for?
Alumina ceramic is used in many industrial applications. It is common in wear-resistant parts like seals and liners. It works in high-temperature settings like furnace components. Electronics use it for insulating parts. Chemical plants use it for corrosion-resistant equipment.
Why is honeycomb ceramic used in RTO and RCO systems?
Honeycomb ceramics have a porous structure. This increases surface area for chemical reactions. RTO (Regenerative Thermal Oxidizer) systems use it to trap and burn pollutants. RCO (Regenerative Catalytic Oxidizer) systems rely on it to hold catalysts. Both systems need materials that handle heat and chemical exposure.
What are the benefits of alumina ceramic in RTO/RCO applications?
Alumina ceramic resists extreme temperatures. It does not degrade under thermal cycling. It withstands corrosive gases and chemicals. Its structural stability ensures long service life. This reduces maintenance costs for industrial systems.
How does honeycomb ceramic handle harsh environments?
The honeycomb structure distributes stress evenly. This prevents cracking under thermal expansion. Alumina’s chemical inertness avoids reactions with pollutants. High porosity allows efficient gas flow. These traits ensure reliability in demanding conditions.
What factors matter when choosing alumina ceramic for industrial use?
Key factors include operating temperature and chemical exposure. Mechanical stress levels and required durability matter. Thermal conductivity and electrical insulation needs are important. Custom shapes or sizes may affect material selection. Proper testing ensures it meets application demands.
(Alumina Ceramic Material and Industrial Ceramic Application Honeycomb Ceramic for RTO RCO)
REQUEST A QUOTE
RELATED PRODUCTS
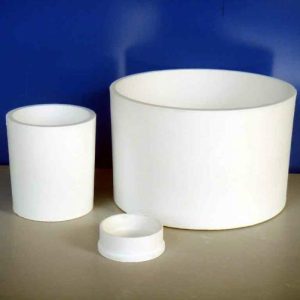
Al2O3 Ceramic HIgh Temperature Thermal Alumina Ceramic Crucible For Sale
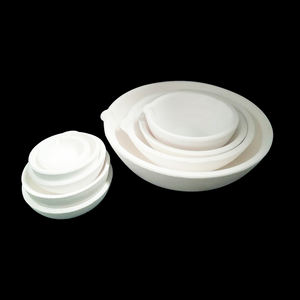
High Temperature Insulating Ceramic Tube Alumina Zirconia Ceramic
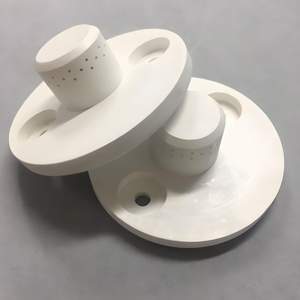
Industrial Alumina Ceramic Tube 99 Al2o3 Fireproof Alumina Tube Circle Alumina Tube
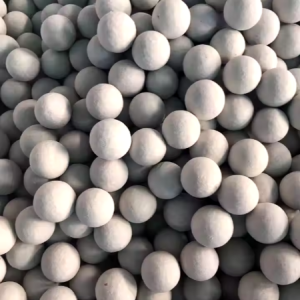
Al2O3 Ceramic 6mm,20mm Inert Alumina Ceramic Ball as Catalyst Support Media Ceramic Ball
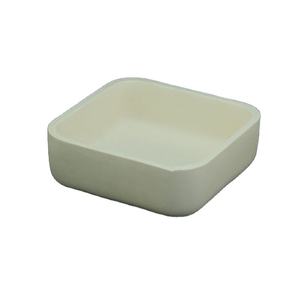
Square / Hexagon Al2o3 Alumina Ceramic Tiles and Plates
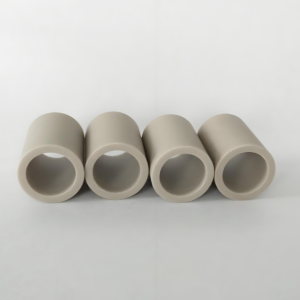