Discover Premium Ceramic Products | Durability & Elegance United | Advanced Ceramics
PRODUCT PARAMETERS
Description
Introduction to Alumina Ceramics
Alumina ceramics are known for their high hardness, wear resistance, corrosion resistance, good electrical insulation and high temperature stability. According to the different alumina content, it can be divided into different grades, such as 95 porcelain, 99 porcelain, etc., among which 99 porcelain refers to ceramic materials with an alumina content of 99%. As the alumina content increases, its mechanical strength and electrical insulation properties will also increase accordingly.
Characteristics of Alumina Ceramics
High Hardness: Alumina ceramics have extremely high hardness, which makes it very wear-resistant and suitable for manufacturing abrasive tools and parts that require wear resistance.
Wear resistance: Due to its high hardness, alumina ceramics show excellent wear resistance and are suitable for manufacturing parts for long-term use.
Corrosion resistance: Alumina ceramics have good resistance to most acids and alkalis, making them widely used in the chemical industry.
Good electrical insulation: As an excellent electrical insulating material, alumina ceramics are widely used in electronic and electrical products.
High temperature stability: Ability to withstand extremely high temperatures without significant physical or chemical changes, which makes it an ideal choice for applications in high temperature environments.
Biocompatibility: In the medical field, certain grades of alumina ceramics are used to make medical devices such as artificial joints due to their good biocompatibility.
(Custom Al2O3 Ceramics Precision Industrial CNC 99% 99.5% Alumina Ceramic Parts)
Specifications of Custom Al2O3 Ceramics Precision Industrial CNC 99% 99.5% Alumina Ceramic Parts
Customized Al2O3 ceramics precision commercial CNC components are crafted for high-performance applications. These components are made from 99% or 99.5% alumina (Al2O3). The product ensures extraordinary firmness, put on resistance, and thermal stability. They run effectively in temperatures up to 1600 ° C. This makes them appropriate for extreme environments.
The production procedure uses sophisticated CNC machining. Tight resistances are achieved, normally within ± 0.01 mm. Facility shapes and specific dimensions are feasible. Surface finishes can get to Ra 0.2 μm. This assures smooth, functional parts ready for prompt use.
Alumina porcelains master mechanical strength. They resist abrasion, corrosion, and chemical assault. Acidic or alkaline problems do not weaken them. Electric insulation buildings are high. This protects against existing leak in electronic or high-voltage systems.
Applications cover numerous industries. Semiconductor making uses them for wafer handling and plasma-resistant components. Automotive systems rely on them for sensors and insulating components. Medical gadgets benefit from their biocompatibility and sanitation compatibility. Industrial machinery uses them for wear-resistant liners or reducing devices.
Personalization is a key function. Parts are customized to certain layouts, dimensions, or performance demands. Models to automation are supported. Technical drawings or samples guide the manufacturing process.
Quality control is strenuous. Each set undergoes thickness, solidity, and dimensional checks. X-ray and ultrasonic screening spot inner imperfections. This guarantees uniformity and reliability.
Product packaging uses anti-static materials. Parts are cushioned to avoid damage during delivery. Tags consist of part numbers, requirements, and accreditations.
These alumina ceramic components satisfy demands for sturdiness, precision, and thermal management. They change steels or plastics in severe conditions. Efficiency and long life are focused on. Costs are lowered with prolonged service life and minimal upkeep.
The 99.5% quality uses a little higher purity. Density and toughness enhance partially. Applications needing severe thermal or mechanical stress and anxiety advantage the majority of. Both qualities provide steady dielectric homes. Regularity or temperature level modifications do not alter performance.
Product certificates and test records are offered. Conformity with ISO standards is basic. Personalized requirements for testing or documents are accommodated.
(Custom Al2O3 Ceramics Precision Industrial CNC 99% 99.5% Alumina Ceramic Parts)
Applications of Custom Al2O3 Ceramics Precision Industrial CNC 99% 99.5% Alumina Ceramic Parts
Custom Al2O3 porcelains are high-performance products used in lots of markets. They have 99% to 99.5% alumina, making them hard, heat-resistant, and chemically stable. These homes make them ideal for accuracy commercial parts made with CNC machining.
In electronic devices, alumina ceramic components function as insulators, substrates, and circuit parts. They handle high temperatures and protect against electric leaks. This keeps devices risk-free and efficient. Semiconductor manufacturing utilizes alumina for wafer-handling parts and plasma-resistant parts. The product stays steady in extreme problems, minimizing contamination risks.
Aerospace and vehicle markets depend on alumina porcelains for sensing units, shutoffs, and engine parts. The components withstand severe warm and friction. This boosts engine performance and life-span. Medical devices utilizes alumina for surgical devices and implants. The material is biocompatible and stands up to corrosion. This makes sure safety and security and reliability in important applications.
Industrial equipment utilizes custom-made alumina components for wear-resistant linings, reducing tools, and seals. Their firmness decreases wear in abrasive atmospheres. This reduces upkeep expenses and downtime. Chemical handling plants make use of alumina components for pumps and valves. The porcelains resist acid and alkali corrosion, guaranteeing long-lasting operation.
CNC machining enables accurate shaping of alumina porcelains. Facility geometries fulfill tight resistances for specialized uses. The procedure makes sure consistency in high-volume manufacturing. Alumina’s reduced thermal development avoids buckling under temperature level adjustments. This keeps component precision sought after settings.
Personalized Al2O3 ceramics are picked for their resilience and versatility. They solve issues in high-stress, high-temperature, or corrosive environments. Industries gain from boosted effectiveness, reliability, and expense savings.
Company Introduction
Advanced Ceramics founded on October 17, 2014, is a high-tech enterprise committed to the research and development, production, processing, sales and technical services of ceramic relative materials and products.. Since its establishment in 2014, the company has been committed to providing customers with the best products and services, and has become a leader in the industry through continuous technological innovation and strict quality management.
Our products includes but not limited to Silicon carbide ceramic products, Boron Carbide Ceramic Products, Boron Nitride Ceramic Products, Silicon Carbide Ceramic Products, Silicon Nitride Ceramic Products, Zirconium Dioxide Ceramic Products, Quartz Products, etc. Please feel free to contact us.(nanotrun@yahoo.com)
Payment Methods
T/T, Western Union, Paypal, Credit Card etc.
Shipment Methods
By air, by sea, by express, as customers request.
5 FAQs of Custom Al2O3 Ceramics Precision Industrial CNC 99% 99.5% Alumina Ceramic Parts
What are custom Al2O3 ceramics precision parts made of? These parts are made from alumina (Al2O3), a ceramic material containing 99% or 99.5% aluminum oxide. The remaining percentage includes additives for specific performance needs. High alumina content gives the material strength, electrical insulation, and heat resistance. This makes it better than lower-grade ceramics in demanding environments.
Where are custom Al2O3 ceramic parts commonly used? They are used in industries needing durable, heat-resistant components. Examples include electronics, medical devices, aerospace, and industrial machinery. Typical applications include insulating substrates, lab equipment, cutting tools, and wear-resistant seals. The material works well in high-temperature, corrosive, or high-pressure settings.
How precise can Al2O3 ceramic parts be manufactured? CNC machining allows tight tolerances, often within ±0.01 mm. Surface finishes can reach Ra 0.2 µm. Precision depends on part design, tooling, and machining processes. Advanced CNC equipment ensures consistency for complex shapes. Post-processing like grinding or polishing improves accuracy further.
Can custom Al2O3 parts be made in complex shapes? Yes. Manufacturers combine molding techniques with CNC machining for intricate designs. Injection molding or dry pressing creates near-net shapes. CNC machining adds fine details or adjusts dimensions. Custom parts include tubes, plates, rods, or components with holes, threads, or grooves. Provide detailed specifications to confirm feasibility.
How should Al2O3 ceramic parts be handled and maintained? Avoid impacts or sudden temperature changes. Alumina ceramics are hard but brittle. Use compatible cleaning agents to prevent chemical damage. Do not expose to hydrofluoric acid or strong alkalis. Follow manufacturer guidelines for installation and usage. Proper handling ensures long service life.
(Custom Al2O3 Ceramics Precision Industrial CNC 99% 99.5% Alumina Ceramic Parts)
REQUEST A QUOTE
RELATED PRODUCTS
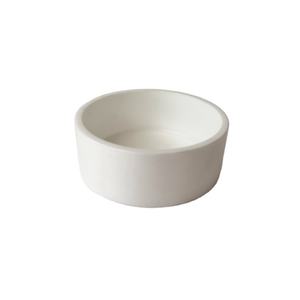
Extruded Pressed Cellular Alumina Honeycomb Ceramic Porous Ceramic
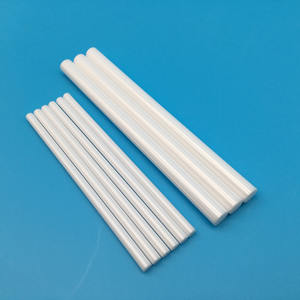
High Alumina Ceramic Heater Rod Porcelain Components 95
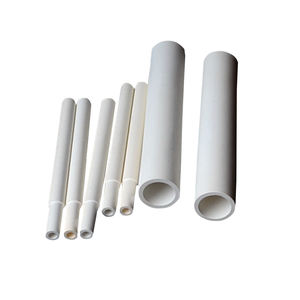
Laboratory Processes Alumina Ceramic Crucible
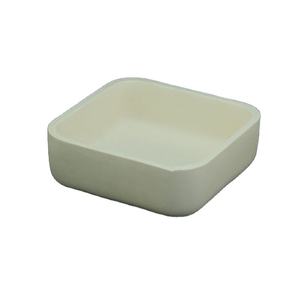
Square / Hexagon Al2o3 Alumina Ceramic Tiles and Plates
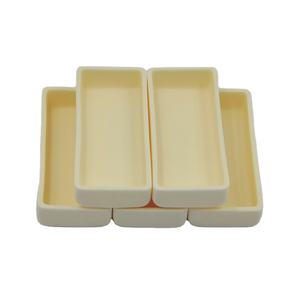
Centerless Grinding High-accuracy 99% 99.5% Al2O3 Alumina Ceramic Polished Rods
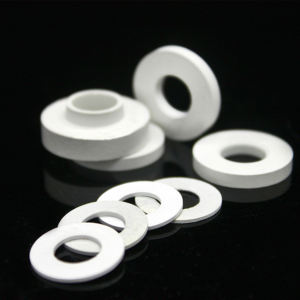