Discover Premium Ceramic Products | Durability & Elegance United | Advanced Ceramics
PRODUCT PARAMETERS
Description
Overview of Silicon Nitride Ceramics
Silicon Nitride Ceramics are high-performance materials known for their excellent mechanical properties, including strength, toughness, and resistance to wear, corrosion, and thermal shock, making them ideal for demanding applications in various industries.
Features of Silicon Nitride Ceramics
Exceptional hardness and wear resistance.
Superior mechanical strength and fracture toughness.
Excellent thermal stability and resistance to thermal shock.
High corrosion resistance in aggressive environments.
Low density contributing to lightweight components.
(Customized Fine Polished G5 Silicon Nitride Si3N4 Ceramic Grinding Ball)
Specifications of Customized Fine Polished G5 Silicon Nitride Si3N4 Ceramic Grinding Ball
Personalized Great Sleek G5 Silicon Nitride (Si3N4) Ceramic Grinding Balls are crafted for high-performance applications requiring precision and toughness. These grinding balls are made from advanced ceramic product, silicon nitride, understood for phenomenal mechanical toughness, thermal security, and resistance to wear and rust. The G5 grade ensures high pureness and consistency, making them optimal for requiring industrial settings.
The grinding rounds are offered in sizes ranging from 0.4 mm to 50mm. Personalized sizes can be generated to fulfill certain needs. Thickness is normally 3.2-3.3 g/cm SIX, offering a balance in between lightweight style and structural stability. Firmness exceeds HRA 90, ensuring minimal deformation under heavy tons. Surface roughness is maintained listed below Ra 0.2 μm after fine sprucing up, reducing rubbing and bit contamination throughout procedure.
These ceramic grinding balls operate successfully in temperature levels as much as 1200 ° C without shedding performance. They withstand chemical attack from acids, antacid, and solvents, making them suitable for extreme processing problems. Crack strength is high, protecting against splits or chips even under extreme mechanical stress.
Personalization choices consist of modifications to size resistances, surface finish levels, and set amounts. Specialized coatings or treatments can be gotten particular applications. The manufacturing process utilizes high-purity resources and precision molding techniques, complied with by sintering and brightening to achieve consistent geometry and smooth surface areas.
Applications extend markets such as aerospace, vehicle, electronics, and pharmaceuticals. They are utilized in grinding mills, mixers, and spreading tools for products such as steels, porcelains, polymers, and compounds. Compared to conventional steel or alumina spheres, silicon nitride grinding spheres use longer life span, lower power intake, and decreased upkeep prices.
Product buildings include a reduced thermal development coefficient, reducing dimensional modifications during temperature level fluctuations. Electrical insulation properties protect against undesirable conductivity in sensitive procedures. The lack of metal ions ensures purity in applications like semiconductor manufacturing or clinical gadget production.
Quality assurance includes extensive testing for thickness, solidity, and surface coating. Each batch is examined to satisfy global criteria like ISO 9001. Product packaging is adjustable, with alternatives for vacuum-sealed containers or anti-static bags to prevent damages during delivery.
These grinding rounds are compatible with the majority of industrial equipment and can change standard choices without procedure modifications. Their light-weight nature minimizes equipment wear, while their high wear resistance prolongs operational periods in between replacements.
(Customized Fine Polished G5 Silicon Nitride Si3N4 Ceramic Grinding Ball)
Applications of Customized Fine Polished G5 Silicon Nitride Si3N4 Ceramic Grinding Ball
Personalized fine polished G5 silicon nitride (Si3N4) ceramic grinding rounds offer important duties throughout multiple markets. Their high hardness, use resistance, and thermal security make them ideal for requiring environments. These grinding balls master precision grinding and crushing procedures. They minimize contamination during product handling. This makes certain consistent product quality in markets like electronic devices and semiconductors.
In electronics producing, these ceramic balls deal with fragile materials such as silicon wafers or ceramic substratums. Their smooth surface area finish reduces rubbing. This prevents damages to delicate parts. Their chemical inertness keeps materials pure. This is vital for generating high-performance electronic devices.
The aerospace industry relies on silicon nitride grinding rounds for handling advanced composites and superalloys. They endure severe temperature levels and mechanical stress. This toughness guarantees dependable efficiency in turbine elements or heat-resistant coatings. Their light-weight nature additionally supports gas efficiency goals in airplane layout.
Automotive applications consist of making precision engine parts and coverings. The grinding balls help develop consistent fragment dimensions in products like thermal obstacle finishings. This improves engine effectiveness and durability. Their resistance to corrosion and put on lowers downtime in production lines.
Pharmaceutical business use these ceramic balls for grinding active components or excipients. Their non-reactive properties prevent contamination during drug formula. They satisfy rigorous hygiene standards needed in medical-grade manufacturing. Their sturdiness makes certain consistent lead to high-volume processing.
Chemical processing plants gain from their resistance to severe acids and alkalis. They grind unpleasant materials like pigments or drivers without weakening. This extends equipment life-span and decreases maintenance expenses. Their stability in high-pressure atmospheres supports constant procedures.
Personalized sizes and surface coatings enable tailored solutions for certain equipment or products. This flexibility improves process effectiveness throughout various markets. The mix of mechanical strength and thermal shock resistance makes them above traditional steel or alumina choices.
Their reduced density decreases energy usage throughout high-speed grinding. This aligns with sustainability goals in contemporary manufacturing. Consistent efficiency under repeated anxiety makes certain long-lasting cost savings. Industries prioritizing precision and reliability progressively take on silicon nitride ceramic grinding rounds.
Company Introduction
Advanced Ceramics founded on October 17, 2014, is a high-tech enterprise committed to the research and development, production, processing, sales and technical services of ceramic relative materials and products.. Since its establishment in 2014, the company has been committed to providing customers with the best products and services, and has become a leader in the industry through continuous technological innovation and strict quality management.
Our products includes but not limited to Silicon carbide ceramic products, Boron Carbide Ceramic Products, Boron Nitride Ceramic Products, Silicon Carbide Ceramic Products, Silicon Nitride Ceramic Products, Zirconium Dioxide Ceramic Products, Quartz Products, etc. Please feel free to contact us.(nanotrun@yahoo.com)
Payment Methods
T/T, Western Union, Paypal, Credit Card etc.
Shipment Methods
By air, by sea, by express, as customers request.
5 FAQs of Customized Fine Polished G5 Silicon Nitride Si3N4 Ceramic Grinding Ball
What is a Customized Fine Polished G5 Silicon Nitride Si3N4 Ceramic Grinding Ball?
This product is a high-performance ceramic grinding ball made from silicon nitride (Si3N4). It is processed to G5 precision with a fine-polished surface. The material offers exceptional hardness, wear resistance, and thermal stability. It is ideal for demanding industrial grinding applications where precision and durability matter.
Where are these grinding balls commonly used?
They are used in industries like semiconductors, chemicals, and pharmaceuticals. They work in equipment such as ball mills or mixers for grinding or mixing materials. Their non-contaminating properties make them suitable for high-purity environments. They handle tasks like reducing particle size or blending powders efficiently.
What advantages do they have over other ceramic materials?
Silicon nitride grinding balls outperform materials like alumina or zirconia. They have higher hardness and better resistance to wear and thermal shock. Their low friction coefficient reduces energy consumption during operation. They last longer in high-speed or high-temperature conditions, lowering replacement costs.
Can these grinding balls be customized for specific needs?
Yes. Sizes range from 0.5mm to 50mm. Surface finishes can be adjusted from standard to mirror-level polish. Tight tolerances ensure consistency for precision applications. Custom packaging or labeling is available for bulk orders. Adjustments match equipment requirements or material types being processed.
How should these grinding balls be maintained?
Store them in dry conditions to prevent moisture absorption. Clean them regularly with compatible solvents to remove residue. Avoid sudden temperature changes to prevent cracking. Inspect for chips or cracks before reuse. Follow the manufacturer’s guidelines for operating pressure and speed to maximize lifespan.
(Customized Fine Polished G5 Silicon Nitride Si3N4 Ceramic Grinding Ball)
REQUEST A QUOTE
RELATED PRODUCTS
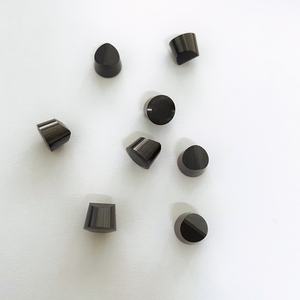
High Quality Gray Silicon Nitride Ceramic Rings High Hardness Industrial Ceramic Parts with Bending Processing Service
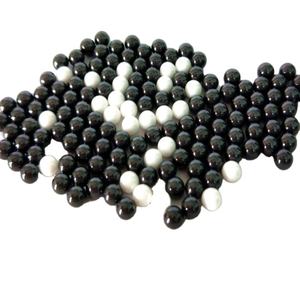
Silicon Nitride Ceramic Sheet Si3n4 High Temperature Resistant Silicon Nitride Ceramic Plate
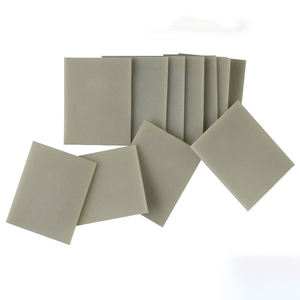
High Purity 99.9% Si3n4 Powder Silicon Nitride for Ceramic or Refractory
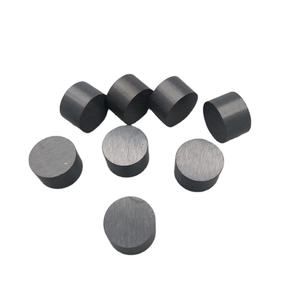
Silicon Nitride Powder Si3N4 Powder Structural Ceramic Materials
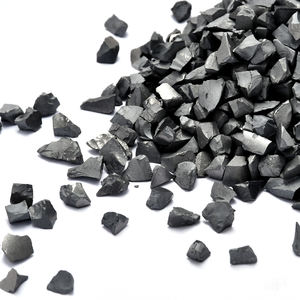
Industrial Machined Ceramics Alumina Zirconia Silicon Nitride Ceramics Precision Ceramic Parts Processing
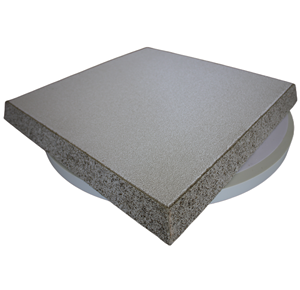