Discover Premium Ceramic Products | Durability & Elegance United | Advanced Ceramics
PRODUCT PARAMETERS
Description
Overview of Silicon Carbide Ceramics
Silicon Carbide (SiC) ceramics are renowned for their outstanding mechanical properties, including high hardness, strength at elevated temperatures, and excellent thermal shock resistance. These materials are pivotal in cutting-edge industrial applications, from abrasives to aerospace components, due to their unique combination of properties.
Features of Silicon Carbide Ceramics
High Hardness: Exceptional wear resistance.
Thermal Shock Resistance: Can withstand rapid temperature changes.
Chemical Stability: Resistant to most chemicals.
High Thermal Conductivity: Efficient heat dissipation.
Low Density: Lightweight for its strength.
(Silicon Carbide Ceramic Abrasives Resin Grits in Blast Media Form for Sanding Blasting Sand Blasting)
Specification of Silicon Carbide Ceramic Abrasives Resin Grits in Blast Media Form for Sanding Blasting Sand Blasting
Silicon carbide ceramic abrasives resin grits serve as a high-performance blast media for sanding and sandblasting applications. These grits incorporate silicon carbide’s extreme solidity with a resin-bonded layer to boost longevity during surface area treatment processes. The material’s sharp sides and angular shape give hostile cutting action, making it ideal for getting rid of hard coatings, corrosion, or impurities from steels, stone, and compounds.
The grits can be found in consistent fragment sizes ranging from rugged to great qualities. This allows users to choose the optimum grit dimension for details jobs. Coarser grits function well for hefty product elimination, while better qualities deliver smoother coatings. The material coating lowers dirt generation throughout blowing up, enhancing presence and office safety. It additionally reduces bit malfunction, prolonging the media’s multiple-use lifespan contrasted to uncoated abrasives.
Silicon carbide’s thermal stability makes sure regular efficiency under high-pressure blasting problems. It resheat fracturing also at raised temperature levels, maintaining reducing efficiency with time. The product is chemically inert, protecting against responses with treated surfaces. This makes it appropriate for delicate applications like aerospace element cleansing or electronic devices making.
These resin-bonded grits deal with common blasting tools, consisting of suction-fed and stress blast systems. They are compatible with metals, porcelains, glass, and strengthened plastics. Operators attain faster cleaning prices than with softer abrasives like crushed glass or walnut coverings. The reduced usage price lowers product costs and waste disposal requirements.
Appropriate storage space in dry problems protects the grits’ integrity. Moisture direct exposure can deteriorate the resin bond, causing premature wear. Customers need to adhere to equipment producer standards for atmospheric pressure and nozzle range to make the most of performance. Normal examination of utilized media assists identify contamination or too much wear, making sure constant results.
Silicon carbide ceramic abrasives material grits outperform alternatives like aluminum oxide or steel shot in accuracy applications. Their combination of firmness, sturdiness, and regulated aggressiveness makes them a flexible choice for industrial ending up, etching, and surface prep work tasks.
(Silicon Carbide Ceramic Abrasives Resin Grits in Blast Media Form for Sanding Blasting Sand Blasting)
Applications of Silicon Carbide Ceramic Abrasives Resin Grits in Blast Media Form for Sanding Blasting Sand Blasting
Silicon carbide ceramic abrasives resin grits in blast media form offer multiple functions in industrial surface area treatment. These grits integrate silicon carbide’s solidity with resin-bonded sturdiness. They work well for sandblasting, sanding, and surface prep work. Industries like vehicle, aerospace, metalworking, and construction rely upon them for reliable material removal.
The sharp sides of silicon carbide grits punctured difficult surface areas rapidly. They manage jobs like rust elimination, paint stripping, and deburring metal parts. Their solidity makes certain consistent efficiency under high stress. Resin-bonded grits last much longer than typical abrasives. This minimizes replacement regularity and lowers operational prices.
These abrasives fit both completely dry and damp blasting systems. They create marginal dust throughout use. This boosts visibility for operators and decreases devices wear. The reduced dust output also supports cleaner work areas. It lines up with environmental and safety and security requirements.
In automobile repair, silicon carbide grits prepare surfaces for finishings. They remove old paint without harmful underlying metal. Aerospace applications consist of smoothing turbine blades and engine elements. The precision of these grits makes certain essential parts meet strict tolerances. Metalworking shops utilize them to complete welds or polish equipment. Building and construction groups rely on them to tidy concrete or rock prior to securing.
The material matrix holds grit bits together throughout effect. This stops premature breakdown. It enables consistent abrasion throughout surface areas. Reusable in certain setups, these grits offer cost savings over time. Operators achieve faster task turn-around with much less product waste.
Silicon carbide ceramic abrasives withstand heats and chemical exposure. This makes them perfect for extreme working problems. They keep reducing efficiency even after duplicated use. Their flexibility covers coarse and great ending up demands. Readjusting grit size or blowing up stress tailors results for particular products.
These abrasives deal with steels, ceramics, glass, and composites. They leave surfaces tidy and all set for coverings or adhesives. The mix of hostile cutting and controlled product removal satisfies diverse commercial needs.
Company Introduction
Advanced Ceramics founded on October 17, 2014, is a high-tech enterprise committed to the research and development, production, processing, sales and technical services of ceramic relative materials and products.. Since its establishment in 2014, the company has been committed to providing customers with the best products and services, and has become a leader in the industry through continuous technological innovation and strict quality management.
Our products includes but not limited to Silicon carbide ceramic products, Boron Carbide Ceramic Products, Boron Nitride Ceramic Products, Silicon Carbide Ceramic Products, Silicon Nitride Ceramic Products, Zirconium Dioxide Ceramic Products, Quartz Products, etc. Please feel free to contact us.(nanotrun@yahoo.com)
Payment Methods
T/T, Western Union, Paypal, Credit Card etc.
Shipment Methods
By air, by sea, by express, as customers request.
5 FAQs of Silicon Carbide Ceramic Abrasives Resin Grits in Blast Media Form for Sanding Blasting Sand Blasting
Silicon carbide ceramic abrasives resin grits in blast media form are used for sanding and blasting. Here are 5 FAQs. What are silicon carbide ceramic abrasives resin grits? These grits mix silicon carbide with resin. They form sharp, tough grains. They work for cutting, grinding, or surface prep. They last longer than other abrasives. They handle high-pressure blasting well.
Why pick silicon carbide over other abrasives? Silicon carbide is harder than materials like aluminum oxide. It cuts faster. It creates a smoother finish. It works on metals, glass, or stone. It resheathes during use. This means fresh edges stay exposed. It keeps performance steady.
What jobs suit these grits? They work for heavy-duty tasks. Examples include removing rust from metal parts. They prep surfaces before coating. They etch glass or clean stone. They deburr machinery. They strip paint without damaging the base material. They fit industries like automotive or construction.
Are these grits safe? They create dust during blasting. Wear goggles and masks. Use proper ventilation. The resin bond reduces dust slightly. Avoid inhaling particles. Follow workplace safety rules. Store grits in dry areas. Moisture weakens the resin bond.
How to choose the right grit size? Coarse grits (like 24-60) remove material fast. They handle thick coatings or heavy rust. Medium grits (80-120) balance speed and finish. Fine grits (150-220) give smooth surfaces. Test a small area first. Adjust grit size based on material hardness. Harder surfaces need finer grits. Softer materials need coarser grits.
(Silicon Carbide Ceramic Abrasives Resin Grits in Blast Media Form for Sanding Blasting Sand Blasting)
REQUEST A QUOTE
RELATED PRODUCTS
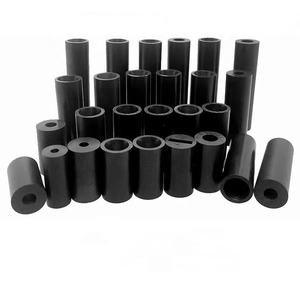
OEM Thermal Shock Resistance Advanced Ceramic Silicon Carbide SiC/SISIC Parts Components
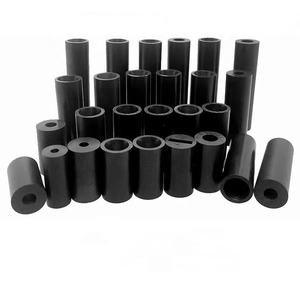
Microporous Silicon Carbide Foam Ceramic Tube Alumina Foam Ceramic Tube
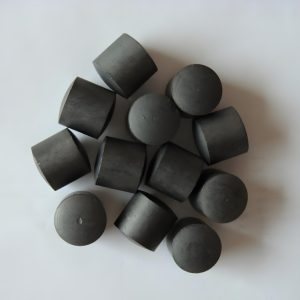
High Hardness Silicon Carbide Grinding Ball Wear Resistance SiC Grinding Ball
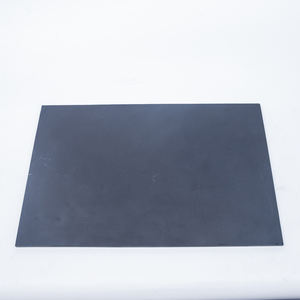
Customized SSIC Ceramic Block Plate Piece Silicon Carbide Ceramic Sheet 40*40/50*50mm

Tactical Equipment PE 3A Armored Panel Tactical Vest Insertion Plate 4IV Ceramic Plate Alumina Silicon Carbide
