Discover Premium Ceramic Products | Durability & Elegance United | Advanced Ceramics
PRODUCT PARAMETERS
Description
Overview of Silicon Carbide Ceramics
Silicon Carbide (SiC) ceramics are renowned for their outstanding mechanical properties, including high hardness, strength at elevated temperatures, and excellent thermal shock resistance. These materials are pivotal in cutting-edge industrial applications, from abrasives to aerospace components, due to their unique combination of properties.
Features of Silicon Carbide Ceramics
High Hardness: Exceptional wear resistance.
Thermal Shock Resistance: Can withstand rapid temperature changes.
Chemical Stability: Resistant to most chemicals.
High Thermal Conductivity: Efficient heat dissipation.
Low Density: Lightweight for its strength.
(Polymethylsilane Referred to As PMS Is a New Generation Silicon Carbide Ceramic Precursor)
Specification of Polymethylsilane Referred to As PMS Is a New Generation Silicon Carbide Ceramic Precursor
Polymethylsilane (PMS) is an innovative silicon carbide ceramic precursor created for high-performance applications. It acts as a key material in producing silicon carbide-based porcelains via polymer-derived ceramic courses. PMS includes a high ceramic return, typically over 80%, which makes certain marginal mass loss throughout pyrolysis. This home makes it efficient for manufacturing thick, defect-free ceramic parts. The product has low oxygen content, lowering contaminations in the end product and improving thermal stability.
PMS is synthesized to remain stable at room temperature, streamlining storage space and handling. It liquifies conveniently alike natural solvents like toluene or tetrahydrofuran, allowing versatile processing with approaches such as spin-coating, injection molding, or fiber rotating. After forming, the product undergoes pyrolysis at temperature levels in between 1000 ° C and 1400 ° C under inert environments. This transforms the polymer into amorphous or crystalline silicon carbide, depending upon handling problems.
The precursor is used in aerospace, energy, and electronic devices sectors. It creates ceramic matrix composites (CMCs) for generator blades, heat shields, and other high-temperature parts. PMS-based coatings safeguard surfaces from oxidation and rust in severe atmospheres. The product additionally develops ceramic fibers for strengthening composites, using exceptional stamina and warm resistance contrasted to conventional products.
PMS outperforms older precursors like polycarbosilane. It supplies better control over ceramic microstructure, boosting mechanical residential or commercial properties such as firmness and crack toughness. The manufacturing procedure is economical, needing lower pyrolysis temperature levels and shorter cycle times. PMS decreases power intake and waste, aligning with lasting production goals.
The material works with additive production techniques, enabling exact construction of intricate ceramic parts. It adheres well to steels, ceramics, and polymers, supporting crossbreed material systems. Security methods advise keeping PMS in great, completely dry problems away from moisture and straight sunlight. Individuals need to handle it with typical laboratory equipment, consisting of gloves and ventilation, to stay clear of breathing or skin contact.
(Polymethylsilane Referred to As PMS Is a New Generation Silicon Carbide Ceramic Precursor)
Applications of Polymethylsilane Referred to As PMS Is a New Generation Silicon Carbide Ceramic Precursor
Company Introduction
Advanced Ceramics founded on October 17, 2014, is a high-tech enterprise committed to the research and development, production, processing, sales and technical services of ceramic relative materials and products.. Since its establishment in 2014, the company has been committed to providing customers with the best products and services, and has become a leader in the industry through continuous technological innovation and strict quality management.
Our products includes but not limited to Silicon carbide ceramic products, Boron Carbide Ceramic Products, Boron Nitride Ceramic Products, Silicon Carbide Ceramic Products, Silicon Nitride Ceramic Products, Zirconium Dioxide Ceramic Products, Quartz Products, etc. Please feel free to contact us.(nanotrun@yahoo.com)
Payment Methods
T/T, Western Union, Paypal, Credit Card etc.
Shipment Methods
By air, by sea, by express, as customers request.
5 FAQs of Polymethylsilane Referred to As PMS Is a New Generation Silicon Carbide Ceramic Precursor
Polymethylsilane (PMS) is a new silicon carbide ceramic precursor. Here are answers to common questions. What is PMS? PMS is a liquid polymer. It converts to silicon carbide when heated. It is used to make advanced ceramics. Its structure allows high ceramic yields. This makes it better than older precursors.
Why is PMS better? Older precursors have lower ceramic yields. PMS gives higher purity silicon carbide. It also has lower oxygen content. This improves material performance. PMS works for complex shapes. It is easier to process.
Where is PMS used? It is used in aerospace and automotive industries. High-temperature parts need strong materials. Turbine components use PMS-derived ceramics. Electronics use it for heat-resistant parts. Semiconductors and coatings also apply PMS.
How is PMS stored? PMS reacts with moisture. Store it in sealed containers. Keep it in dry, cool environments. Use gloves and ventilation when handling. Follow safety guidelines for chemicals.
Can PMS be customized? Yes. Its properties can be adjusted. Modifying molecular weight changes viscosity. Additives enhance specific traits. Manufacturers tailor PMS for different needs. Custom grades are available.
What industries benefit most? High-tech fields gain from PMS. Energy sectors use it in reactors. Defense uses it for durable components. Research labs develop new applications. PMS supports innovation in materials science.
Is PMS cost-effective? Initial costs are higher than older precursors. Long-term benefits offset this. Higher ceramic yields reduce waste. Better performance extends product lifespans. Industries save money over time.
How is PMS processed? It is shaped before heating. Techniques include molding or spinning. Heating converts it to silicon carbide. Processing conditions affect final properties. Controlled temperatures ensure quality.
Are there environmental concerns? PMS is non-toxic but requires careful disposal. Follow local regulations for chemicals. Recycling methods are under study. Proper management minimizes environmental impact.
What is the future of PMS? Research focuses on improving its properties. New applications emerge in tech fields. Demand grows as industries adopt advanced ceramics. PMS plays a key role in material advancements.
(Polymethylsilane Referred to As PMS Is a New Generation Silicon Carbide Ceramic Precursor)
REQUEST A QUOTE
RELATED PRODUCTS
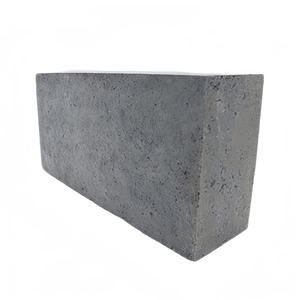
RBSIC/SISIC Silicon Carbide Ceramic Screw Thread Tube SISIC Roller for Ceramic Kiln
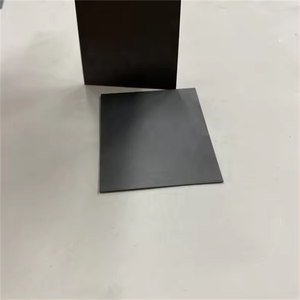
Customized Hexagonal Boron Carbide Silicon Carbide Ceramic Plate Tiles SIC Ceramic for Industrial Use Welding Cutting Services
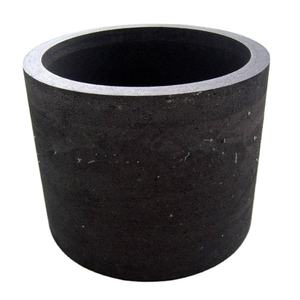
Bulletproof High Hardness Silicon Carbide Ceramic SiC Ballistic Plates
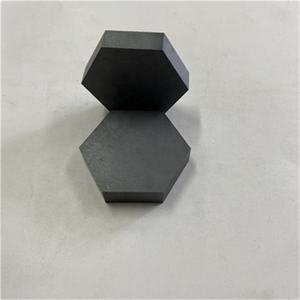
High Temperature Black Zirconia Manufacture Lab Precision Ceramic Parts Silicon Carbide Ceramics
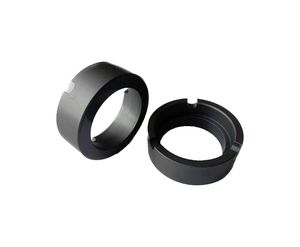
High Refractoriness SiSiC NSiC RSiC Silicon Carbide Sic Ceramic Refractory Plates / Board /batts Kiln Setter Plate
