Discover Premium Ceramic Products | Durability & Elegance United | Advanced Ceramics
PRODUCT PARAMETERS
Description
Introduction to Alumina Ceramics
Alumina ceramics are known for their high hardness, wear resistance, corrosion resistance, good electrical insulation and high temperature stability. According to the different alumina content, it can be divided into different grades, such as 95 porcelain, 99 porcelain, etc., among which 99 porcelain refers to ceramic materials with an alumina content of 99%. As the alumina content increases, its mechanical strength and electrical insulation properties will also increase accordingly.
Characteristics of Alumina Ceramics
High Hardness: Alumina ceramics have extremely high hardness, which makes it very wear-resistant and suitable for manufacturing abrasive tools and parts that require wear resistance.
Wear resistance: Due to its high hardness, alumina ceramics show excellent wear resistance and are suitable for manufacturing parts for long-term use.
Corrosion resistance: Alumina ceramics have good resistance to most acids and alkalis, making them widely used in the chemical industry.
Good electrical insulation: As an excellent electrical insulating material, alumina ceramics are widely used in electronic and electrical products.
High temperature stability: Ability to withstand extremely high temperatures without significant physical or chemical changes, which makes it an ideal choice for applications in high temperature environments.
Biocompatibility: In the medical field, certain grades of alumina ceramics are used to make medical devices such as artificial joints due to their good biocompatibility.
(96% Metallization Tube Alumina Ceramics Parts Al2o3 Alumina Ceramic)
Specifications of 96% Metallization Tube Alumina Ceramics Parts Al2o3 Alumina Ceramic
96% Metallization Tube Alumina Ceramics Components made from Al2O3 alumina ceramic provide high efficiency in demanding commercial applications. The material make-up consists of 96% light weight aluminum oxide, making certain exceptional mechanical toughness and thermal stability. These components manage extreme temperatures as much as 1600 ° C, suitable for high-heat settings. The metallization layer applied to the surface area allows trustworthy bonding with metals, enabling usage in vacuum systems or electronic settings up.
Alumina ceramic tubes stand up to corrosion from acids, alkalis, and rough chemicals. This makes them appropriate for chemical handling equipment or research laboratory tools. The dense framework reduces porosity, preventing gas or liquid leak. Electric insulation residential properties continue to be steady even under high voltage or regularity conditions, sustaining use in power transmission or semiconductor manufacturing.
Accuracy machining guarantees limited dimensional resistances, with regular precision within ± 0.5% of defined dimensions. Surface area coatings achieve Ra ≤ 0.4 μm, lowering friction and put on in relocating systems. Custom-made sizes and shapes are readily available, consisting of straight tubes, stepped layouts, or complex geometries. The metallization process uses products like molybdenum-manganese, creating strong bonds with Kovar or stainless-steel parts.
Mechanical homes consist of a hardness of Hv ≥ 1500, outshining lots of metals and polymers. Flexural toughness exceeds 300 MPa, protecting against splits under hefty tons. Thermal growth prices align carefully with steels, lowering stress and anxiety at joints during temperature changes. Applications span aerospace, auto, energy, and medical industries, such as insulators, sensing unit housings, or laser components.
Alumina porcelains maintain security in vacuum cleaner problems approximately 10 ^ -6 Pa, essential for scientific or space-related equipment. Radiation resistance makes sure performance in nuclear or imaging systems. The material’s low dielectric loss sustains high-frequency applications like RF windows or microwave gadgets.
Personalized metallization patterns are achievable via display printing or laser etching, enabling customized electric connections. Post-processing alternatives include sprucing up, grinding, or covering for boosted efficiency. Compatibility with brazing alloys like Ag-Cu-Ti makes certain secure assimilation right into metal-ceramic assemblies.
These alumina ceramic components fulfill ISO 9001 and RoHS criteria, guaranteeing high quality and ecological conformity. Lead times vary based on intricacy, with common products delivered within 2-4 weeks. Technical assistance assists with layout optimization for particular operating conditions.
(96% Metallization Tube Alumina Ceramics Parts Al2o3 Alumina Ceramic)
Applications of 96% Metallization Tube Alumina Ceramics Parts Al2o3 Alumina Ceramic
Company Introduction
Advanced Ceramics founded on October 17, 2014, is a high-tech enterprise committed to the research and development, production, processing, sales and technical services of ceramic relative materials and products.. Since its establishment in 2014, the company has been committed to providing customers with the best products and services, and has become a leader in the industry through continuous technological innovation and strict quality management.
Our products includes but not limited to Silicon carbide ceramic products, Boron Carbide Ceramic Products, Boron Nitride Ceramic Products, Silicon Carbide Ceramic Products, Silicon Nitride Ceramic Products, Zirconium Dioxide Ceramic Products, Quartz Products, etc. Please feel free to contact us.(nanotrun@yahoo.com)
Payment Methods
T/T, Western Union, Paypal, Credit Card etc.
Shipment Methods
By air, by sea, by express, as customers request.
5 FAQs of 96% Metallization Tube Alumina Ceramics Parts Al2o3 Alumina Ceramic
What is 96% metallization tube alumina ceramic?
This material is made from 96% aluminum oxide (Al2O3). A metal layer bonds to the ceramic surface. This allows joining with metals or other materials. It works in electronics, aerospace, and industrial equipment. The mix of ceramic and metal boosts performance in harsh settings.
Why pick this over other materials?
These parts handle high heat, resist wear, and insulate electricity well. Metals or plastics fail under extreme temperatures or stress. Alumina stays stable. It lasts longer in tough conditions. Costs stay reasonable for the quality provided.
How hot can these parts get?
They work up to 1600°C. Thermal shock resistance stops cracks during quick temperature shifts. This makes them fit furnaces, sensors, or high-heat machinery. Performance stays steady across repeated heating cycles.
What is metallization?
Metallization adds a metal layer (like molybdenum or manganese) to the ceramic. Techniques include plating or spraying. This layer lets the ceramic bond tightly to metal parts. The bond stays strong under stress or heat. Proper metallization ensures reliability in critical applications.
How to maintain these parts?
Clean them with mild soap and water. Avoid abrasive tools or harsh chemicals. Check for chips or cracks regularly. Replace damaged parts quickly to prevent system failures. Store them in dry areas to avoid moisture damage. Proper care extends their lifespan.
(96% Metallization Tube Alumina Ceramics Parts Al2o3 Alumina Ceramic)
REQUEST A QUOTE
RELATED PRODUCTS
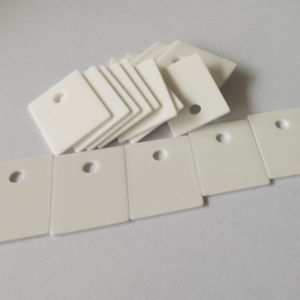
High Quality Alumina Ceramic Tiles 99.9% Purity
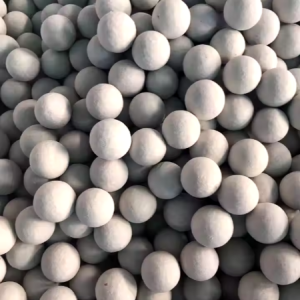
Al2O3 Ceramic 6mm,20mm Inert Alumina Ceramic Ball as Catalyst Support Media Ceramic Ball
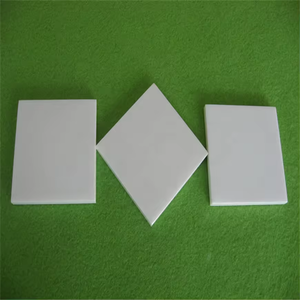
Resistance Ceramic Roughness 96 % Alumina Ceramic Rod
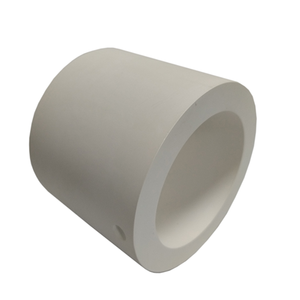
Porous Alumina Ceramic Ball Premium Ceramics Product
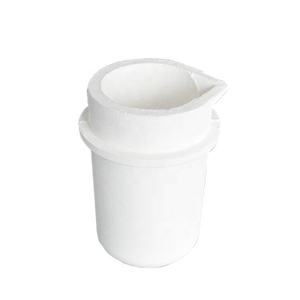
Polished High Purity 99% Alumina Ceramic Stirring Rods
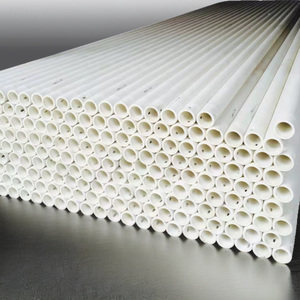