Discover Premium Ceramic Products | Durability & Elegance United | Advanced Ceramics
PRODUCT PARAMETERS
Description
Introduction to Alumina Ceramics
Alumina ceramics are known for their high hardness, wear resistance, corrosion resistance, good electrical insulation and high temperature stability. According to the different alumina content, it can be divided into different grades, such as 95 porcelain, 99 porcelain, etc., among which 99 porcelain refers to ceramic materials with an alumina content of 99%. As the alumina content increases, its mechanical strength and electrical insulation properties will also increase accordingly.
Characteristics of Alumina Ceramics
High Hardness: Alumina ceramics have extremely high hardness, which makes it very wear-resistant and suitable for manufacturing abrasive tools and parts that require wear resistance.
Wear resistance: Due to its high hardness, alumina ceramics show excellent wear resistance and are suitable for manufacturing parts for long-term use.
Corrosion resistance: Alumina ceramics have good resistance to most acids and alkalis, making them widely used in the chemical industry.
Good electrical insulation: As an excellent electrical insulating material, alumina ceramics are widely used in electronic and electrical products.
High temperature stability: Ability to withstand extremely high temperatures without significant physical or chemical changes, which makes it an ideal choice for applications in high temperature environments.
Biocompatibility: In the medical field, certain grades of alumina ceramics are used to make medical devices such as artificial joints due to their good biocompatibility.
(CNC Precision Machining Holes 99% Wear Resisting Alumina Ceramic Structural Parts Ceramic Plate)
Specifications of CNC Precision Machining Holes 99% Wear Resisting Alumina Ceramic Structural Parts Ceramic Plate
CNC Accuracy Machining Holes 99% Use Standing Up To Alumina Porcelain Structural Parts Ceramic Plate provides high-performance solutions for industrial applications calling for longevity and accuracy. The product is made from 99% pure alumina ceramic, ensuring exceptional wear resistance and firmness. Alumina ceramic’s make-up supplies a Vickers solidity of 15-18 Grade point average, making it suitable for settings with heavy abrasion or rubbing. The product density ranges between 3.8-3.9 g/cm FOUR, adding to architectural stability under mechanical stress and anxiety.
The ceramic plate undertakes CNC accuracy machining to attain limited dimensional accuracy. Opening diameters can be tailored from 0.5 mm to 50 mm, with positional resistances as reduced as ± 0.01 mm. Surface roughness is maintained at Ra ≤ 0.4 μm to reduce friction and stop product buildup. Monotony variances are regulated within ± 0.02 mm per 100 mm, guaranteeing seamless assimilation into assemblies.
Alumina ceramic’s thermal buildings include a melting factor exceeding 1750 ° C and a thermal expansion coefficient of 7.2 × 10 ⁻⁶/ ° C, enabling security in high-temperature settings. The product’s electrical insulation buildings reach a breakdown voltage of 15-20 kV/mm, ideal for digital or high-voltage applications. Chemical inertness permits resistance to acids, alkalis, and harsh gases, extending service life in severe atmospheres.
Applications cover machinery parts, semiconductor manufacturing components, clinical tool components, and wear-resistant liners. The ceramic plate reduces downtime by lessening wear-related replacements. Customized forms, sizes, and opening patterns are available to satisfy particular equipment requirements. Each batch goes through strenuous quality testing for dimensional accuracy, surface integrity, and mechanical efficiency.
The item works with common fastening systems, simplifying installment. It runs efficiently in temperature levels from -200 ° C to 1500 ° C without deterioration. No additional layers or treatments are required, decreasing maintenance costs. Packaging includes anti-scratch safety layers to stop damages during transportation. Technical assistance is attended to style optimization and application-specific changes.
(CNC Precision Machining Holes 99% Wear Resisting Alumina Ceramic Structural Parts Ceramic Plate)
Applications of CNC Precision Machining Holes 99% Wear Resisting Alumina Ceramic Structural Parts Ceramic Plate
CNC precision machining creates high-grade holes in 99% wear-resisting alumina ceramic structural components and ceramic plates. These elements manage severe conditions. Alumina ceramic deals outstanding firmness and durability. It resists use far better than the majority of steels and polymers. This makes it optimal for markets requiring lasting performance.
The machining process makes use of sophisticated CNC technology. It makes certain exact opening measurements and smooth surfaces. Tight resistances are critical for parts made use of in machinery. Even small errors can affect performance. CNC devices accomplish precision within micrometers. This reliability is essential for applications like aerospace and auto systems.
Alumina ceramic structural parts are common in high-stress settings. They work in pumps, shutoffs, and bearings. Their wear resistance minimizes downtime and upkeep expenses. Ceramic plates safeguard tools from abrasion in mining and manufacturing. Drilled holes enable secure mounting or fluid circulation. CNC machining ensures these openings match exact layout specs.
The electronics market take advantage of alumina ceramic’s electric insulation. Precision openings in ceramic plates straighten parts in circuits or sensing units. Warmth resistance maintains components secure in high-temperature procedures. This is crucial for semiconductor manufacturing. Ceramic components preserve integrity where steels would certainly stop working.
Clinical tools use alumina ceramic for biocompatibility. Machined holes in medical devices or implants call for clean and sterile, non-reactive materials. CNC accuracy guarantees clean edges and exact fitment. This minimizes threats throughout clinical treatments.
Customization is possible with CNC machining. Designers adjust opening dimensions and patterns for certain demands. Complicated geometries are possible without compromising stamina. This adaptability supports development throughout markets.
Alumina ceramic parts last longer than standard products. They hold up against corrosion, warmth, and mechanical stress. Minimized replacement regularity reduces operational expenses. Businesses conserve money in time.
These applications reveal the value of CNC-machined alumina ceramic components. They address troubles in extreme or exact environments. Efficiency and integrity make them a functional option for modern-day design challenges.
Company Introduction
Advanced Ceramics founded on October 17, 2014, is a high-tech enterprise committed to the research and development, production, processing, sales and technical services of ceramic relative materials and products.. Since its establishment in 2014, the company has been committed to providing customers with the best products and services, and has become a leader in the industry through continuous technological innovation and strict quality management.
Our products includes but not limited to Silicon carbide ceramic products, Boron Carbide Ceramic Products, Boron Nitride Ceramic Products, Silicon Carbide Ceramic Products, Silicon Nitride Ceramic Products, Zirconium Dioxide Ceramic Products, Quartz Products, etc. Please feel free to contact us.(nanotrun@yahoo.com)
Payment Methods
T/T, Western Union, Paypal, Credit Card etc.
Shipment Methods
By air, by sea, by express, as customers request.
5 FAQs of CNC Precision Machining Holes 99% Wear Resisting Alumina Ceramic Structural Parts Ceramic Plate
What makes alumina ceramic structural parts wear-resistant? Alumina ceramic has high hardness and low friction. These parts handle constant friction and harsh conditions. The material resists scratches, abrasion, and surface damage. This extends their lifespan compared to metals or plastics. Industrial equipment needing durability often uses them.
How precise are CNC-machined holes in ceramic plates? CNC machines achieve tight tolerances, often within ±0.01 mm. This precision ensures holes match exact design requirements. Advanced tools prevent cracking during drilling. Smooth edges and accurate placement improve part performance. Consistency is critical for fitting with other components.
What industries use wear-resistant ceramic plates? Mining, aerospace, and manufacturing rely on these plates. Conveyor systems, pumps, and valves face heavy wear. Ceramic plates reduce downtime and maintenance costs. High-temperature environments benefit from their stability. Electronics and medical devices also use them for insulation.
Can alumina ceramic handle high temperatures? Alumina ceramic withstands temperatures up to 1600°C. It keeps its shape and strength under heat. Thermal shock resistance prevents cracking during rapid temperature changes. This makes it suitable for furnaces, engines, and chemical processing. Metals often warp or degrade faster in similar conditions.
How does alumina compare to other ceramics or metals? Alumina is harder than steel and most plastics. It outperforms materials like zirconia in cost-effectiveness. Unlike metals, it resists corrosion and chemicals. Its lightweight nature reduces strain on machinery. For wear-heavy applications, alumina offers better long-term value.
(CNC Precision Machining Holes 99% Wear Resisting Alumina Ceramic Structural Parts Ceramic Plate)
REQUEST A QUOTE
RELATED PRODUCTS
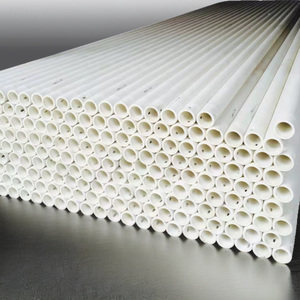
Customizable High-precision Colored Industrial Ceramics.Alumina Ceramic.zirconia Ceramic
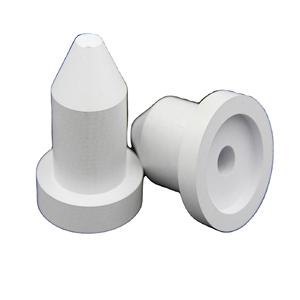
Ceramic Base Industrial Ceramics 95% Alumina Ceramic Part
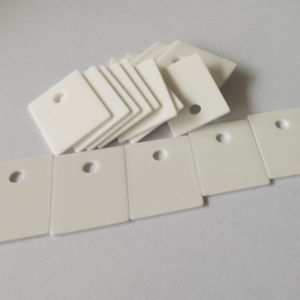
Manufacturing Dry Pressing Moulding 99% Al2O3 Alumina Ceramic Block Plate
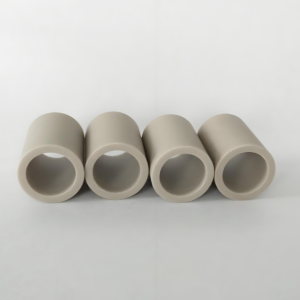
Al2O3 Ceramic mutiple size aluminium oxide ceramic tubes
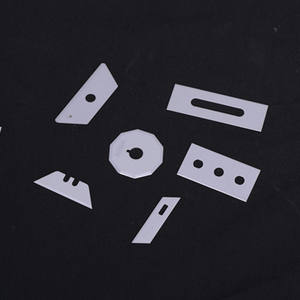
Alumina Ceramic Material and Industrial Ceramic Application Honeycomb Ceramic for RTO RCO
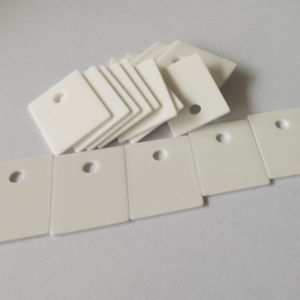