Discover Premium Ceramic Products | Durability & Elegance United | Advanced Ceramics
PRODUCT PARAMETERS
Description
Overview of Silicon Carbide Ceramics
Silicon Carbide (SiC) ceramics are renowned for their outstanding mechanical properties, including high hardness, strength at elevated temperatures, and excellent thermal shock resistance. These materials are pivotal in cutting-edge industrial applications, from abrasives to aerospace components, due to their unique combination of properties.
Features of Silicon Carbide Ceramics
High Hardness: Exceptional wear resistance.
Thermal Shock Resistance: Can withstand rapid temperature changes.
Chemical Stability: Resistant to most chemicals.
High Thermal Conductivity: Efficient heat dissipation.
Low Density: Lightweight for its strength.
(Black Silicon Carbide Is Used As a Refractory in Ceramic Production Sic)
Specification of Black Silicon Carbide Is Used As a Refractory in Ceramic Production Sic
Black silicon carbide is a synthetic material made by home heating quartz sand and oil coke in an electric heating system at high temperatures. It has a high firmness level, exceptional thermal conductivity, and strong chemical stability. These buildings make it excellent for use as a refractory product in ceramic manufacturing. The product resists extreme temperatures, thermal shock, and rust, which prevail obstacles in ceramic manufacturing procedures.
In ceramic kilns, black silicon carbide is often utilized to generate kiln furnishings, such as racks and supports. These components hold ceramic products during firing. The product’s capacity to stand up to fast temperature changes stops breaking or contorting. This ensures constant item quality and decreases downtime for kiln upkeep.
The refractory quality of black silicon carbide commonly has a purity level of 98% or higher. It is available in different bit dimensions, from great powders to rugged grains. Suppliers pick the dimension based on the application. Fine grains are made use of for finishings or ingredients in ceramic blends. Coarser grains are favored for architectural parts requiring high strength.
Black silicon carbide improves power performance in ceramic manufacturing. Its high thermal conductivity enables warmth to disperse evenly inside the kiln. This minimizes firing times and reduces energy intake. The material’s longevity additionally expands the life expectancy of kiln elements, reducing replacement prices.
Chemical resistance is an additional vital advantage. Black silicon carbide does not react with most acids, alkalis, or liquified steels. This makes it suitable for ceramic procedures entailing hostile glazes or high-purity materials. The refractory preserves its integrity even after extended direct exposure to harsh problems.
Cost-effectiveness is a major consider its popularity. While initial prices may be greater than traditional refractories, the long-term cost savings from minimized upkeep and energy use justify the financial investment. Ceramic manufacturers gain from boosted functional efficiency and product consistency.
Black silicon carbide’s role in ceramic production highlights its adaptability and reliability. It deals with important challenges in high-temperature atmospheres while sustaining lasting production methods.
(Black Silicon Carbide Is Used As a Refractory in Ceramic Production Sic)
Applications of Black Silicon Carbide Is Used As a Refractory in Ceramic Production Sic
Black silicon carbide functions as a key refractory product in ceramic production. Its high thermal conductivity and resistance to thermal shock make it perfect for extreme warmth atmospheres. Ceramic production depends on products that handle quick temperature adjustments. Black silicon carbide satisfies this need. It keeps toughness also at temperature levels over 1600 ° C. This protects against architectural failures during firing procedures.
Ceramic kilns commonly use black silicon carbide in linings. The product’s toughness decreases wear from duplicated home heating cycles. This extends the lifespan of kiln elements. Producers save prices on frequent replacements. Black silicon carbide additionally stands up to chemical deterioration. Liquified products or reactive gases in kilns cause minimal damage. This makes sure consistent performance over time.
The material is utilized in ceramic crucibles and saggers. These containers hold raw ceramic pieces throughout firing. Black silicon carbide’s thermal security safeguards products from contamination. It protects against warping or breaking under high warmth. This causes higher-quality ceramic results. Producers achieve much better dimensional accuracy in completed items.
Black silicon carbide enhances power efficiency in ceramic production. Its ability to carry out heat uniformly minimizes hot spots in kilns. This enables faster heating cycles. Energy usage drops without compromising item high quality. Manufacturing facilities lower functional prices while maintaining result requirements.
The unpleasant nature of black silicon carbide help in grinding ceramic resources. Fine powders blend more consistently. This enhances the consistency of ceramic sets. Fired products exhibit less issues.
Black silicon carbide’s versatility includes specialized porcelains. It sustains advanced technical ceramics made use of in electronic devices or aerospace. These applications demand products with severe heat resistance. The refractory residential properties of black silicon carbide meet these strenuous demands.
Ceramic manufacturers focus on dependability in refractory products. Black silicon carbide supplies this through its mechanical stamina and thermal resistance. Its function in keeping reliable, premium production procedures continues to be unparalleled.
Company Introduction
Advanced Ceramics founded on October 17, 2014, is a high-tech enterprise committed to the research and development, production, processing, sales and technical services of ceramic relative materials and products.. Since its establishment in 2014, the company has been committed to providing customers with the best products and services, and has become a leader in the industry through continuous technological innovation and strict quality management.
Our products includes but not limited to Silicon carbide ceramic products, Boron Carbide Ceramic Products, Boron Nitride Ceramic Products, Silicon Carbide Ceramic Products, Silicon Nitride Ceramic Products, Zirconium Dioxide Ceramic Products, Quartz Products, etc. Please feel free to contact us.(nanotrun@yahoo.com)
Payment Methods
T/T, Western Union, Paypal, Credit Card etc.
Shipment Methods
By air, by sea, by express, as customers request.
5 FAQs of Black Silicon Carbide Is Used As a Refractory in Ceramic Production Sic
Black silicon carbide is a synthetic material made by heating silica sand and carbon at high temperatures. It is hard, durable, and resistant to heat and chemicals. Ceramic production uses it as a refractory material because it handles extreme temperatures without breaking down.
What is black silicon carbide?
Black silicon carbide combines silicon and carbon. It forms sharp, angular crystals. The manufacturing process involves electric arc furnaces. This creates a material with high thermal conductivity and strength.
Why is it used as a refractory in ceramics?
Ceramic kilns reach very high temperatures. Black silicon carbide maintains stability under these conditions. It prevents cracks or warping in kiln linings. It also resists chemical reactions with molten materials.
What benefits does it provide in ceramic production?
It improves heat distribution in kilns. This reduces energy waste. Its hardness extends the lifespan of refractory linings. It also minimizes thermal expansion issues. These factors lower production costs over time.
How is black silicon carbide added to ceramic products?
Manufacturers mix it into ceramic raw materials before shaping. The grains are finely ground. This ensures even distribution. Typical ratios range from 5% to 30%, depending on the product. The mix is then fired to form the final ceramic.
Are there drawbacks to using black silicon carbide?
The material is abrasive. Handling it requires protective gear to avoid skin irritation. Grinding produces dust that needs proper ventilation. Initial costs are higher than some alternatives, but long-term savings offset this.
(Black Silicon Carbide Is Used As a Refractory in Ceramic Production Sic)
REQUEST A QUOTE
RELATED PRODUCTS
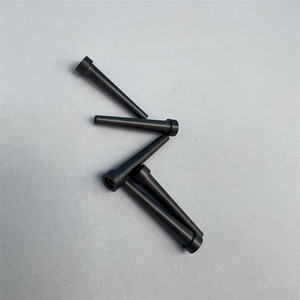
Mirror Polish Silicon Carbide Ssic Sic Ceramic Seal Ring
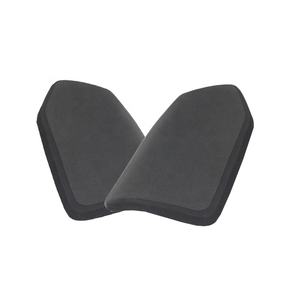
Hot Silicon Carbide of Silicon Carbide Bearing Ball Sic Ceramic Grinding Ball Silicon Carbide Balls
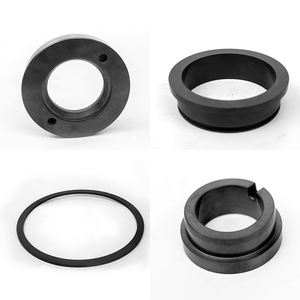
Carbide Customization Ceramic Parts OEM Silicon Carbide High Temperature Resistance Sic Silicone Precision
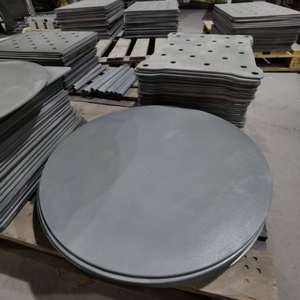
Silicon Carbide Ceramic armor Plate
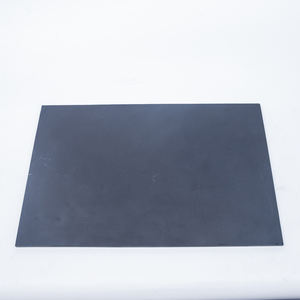
Customized SSIC Ceramic Block Plate Piece Silicon Carbide Ceramic Sheet 40*40/50*50mm
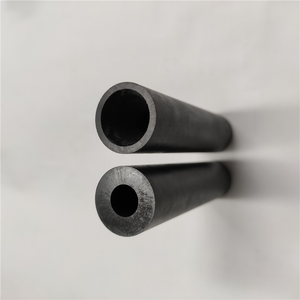