Discover Premium Ceramic Products | Durability & Elegance United | Advanced Ceramics
PRODUCT PARAMETERS
Description
Overview of Silicon Carbide Ceramics
Silicon Carbide (SiC) ceramics are renowned for their outstanding mechanical properties, including high hardness, strength at elevated temperatures, and excellent thermal shock resistance. These materials are pivotal in cutting-edge industrial applications, from abrasives to aerospace components, due to their unique combination of properties.
Features of Silicon Carbide Ceramics
High Hardness: Exceptional wear resistance.
Thermal Shock Resistance: Can withstand rapid temperature changes.
Chemical Stability: Resistant to most chemicals.
High Thermal Conductivity: Efficient heat dissipation.
Low Density: Lightweight for its strength.
(Silicon Carbide Ceramic Beam Used to Porcelain Tiles Plates Insulator Kiln)
Specification of Silicon Carbide Ceramic Beam Used to Porcelain Tiles Plates Insulator Kiln
Silicon carbide ceramic light beams are designed for usage in kilns that generate porcelain floor tiles, plates, and insulators. These beam of lights sustain heavy loads during high-temperature firing processes. The material combines silicon and carbon in a high-temperature sintering procedure. This creates a framework with outstanding toughness and thermal stability.
The beam of lights manage temperatures approximately 1600 ° C without deforming or splitting. Typical metal supports fall short under similar conditions because of reduced melting factors. Silicon carbide withstands oxidation and chemical rust. This makes sure long-term performance in severe kiln atmospheres.
Thermal shock resistance is a crucial attribute. Fast temperature adjustments cause stress and anxiety in many materials. Silicon carbide ceramic light beams stand up to abrupt heating or air conditioning. This decreases downtime for repair work or substitutes.
Load capacity is important in kiln procedures. Each light beam sustains weights going beyond 500 kilograms. The layout disperses weight uniformly throughout the kiln structure. This stops unequal stress and anxiety on floor tiles or plates during shooting.
Criterion beam of light measurements differ to match kiln dimensions. Usual lengths vary from 1.5 to 3 meters. Cross-sectional accounts are optimized for stamina and heat circulation. Customized sizes are available for specialized kiln configurations.
Surface level of smoothness decreases rubbing during loading and dumping. This safeguards delicate porcelain things from the ground up or damages. The non-porous product withstands glaze attachment. Cleaning up in between production cycles is simple.
Setup calls for aligning light beams exactly on kiln carriages. Correct spacing guarantees even heat circulation. Upkeep entails routine inspections for surface area wear. Chips or cracks are rare but should be dealt with swiftly to maintain performance.
Energy effectiveness improves with silicon carbide light beams. High thermal conductivity transfers warm properly. This minimizes shooting times and lowers energy consumption. Running costs reduce with time as a result of toughness and performance.
Compatibility with existing kiln systems is simple. Retrofitting old kilns with these beams extends devices life-span. Manufacturers provide technical assistance for setup and troubleshooting.
(Silicon Carbide Ceramic Beam Used to Porcelain Tiles Plates Insulator Kiln)
Applications of Silicon Carbide Ceramic Beam Used to Porcelain Tiles Plates Insulator Kiln
Silicon carbide ceramic beams serve key roles in producing porcelain ceramic tiles, plates, and insulators within commercial kilns. These light beams sustain items during high-temperature firing. They manage extreme warm without warping, making sure secure conditions for consistent product high quality. Their high thermal conductivity spreads warmth evenly, protecting against locations that can damage delicate things like porcelain floor tiles. This also home heating is essential for attaining consistent color and toughness in completed floor tiles.
In plate production, silicon carbide beam of lights use resilience under repeated thermal cycles. Kilns cycle between low and high temperature levels throughout production. Traditional products might break under such stress and anxiety, however silicon carbide withstands thermal shock. This lowers downtime for replacements, maintaining assembly line effective.
For insulators, accurate firing is vital to keep electrical resistance buildings. Silicon carbide beams give consistent assistance, avoiding defects throughout sintering. Their chemical inertness prevents reactions with insulator products, protecting pureness. This ensures insulators meet stringent efficiency requirements in electrical systems.
These beams additionally master heavy-load settings. Their high toughness sustains piled floor tiles or plates without flexing. This makes best use of kiln ability, enabling larger sets per cycle. The product’s resistance to oxidation and corrosion prolongs service life, even in harsh kiln environments.
Upkeep requirements are marginal. Silicon carbide light beams resist wear from abrasive particles in kiln settings. This reduces long-lasting prices, as substitutes are unusual. Energy performance improves too. The beam of lights preserve warmth efficiently, minimizing power required to preserve temperatures.
Cost-effectiveness expands with time. While initial costs are higher than typical options, durability and effectiveness cause financial savings. Producers gain from fewer interruptions, higher output, and consistent item high quality.
Silicon carbide ceramic beams are crucial in modern-day kiln operations. They address difficulties in high-temperature manufacturing, providing integrity and performance. Industries relying on porcelain, plates, and insulators rely on these beam of lights to keep affordable production criteria.
Company Introduction
Advanced Ceramics founded on October 17, 2014, is a high-tech enterprise committed to the research and development, production, processing, sales and technical services of ceramic relative materials and products.. Since its establishment in 2014, the company has been committed to providing customers with the best products and services, and has become a leader in the industry through continuous technological innovation and strict quality management.
Our products includes but not limited to Silicon carbide ceramic products, Boron Carbide Ceramic Products, Boron Nitride Ceramic Products, Silicon Carbide Ceramic Products, Silicon Nitride Ceramic Products, Zirconium Dioxide Ceramic Products, Quartz Products, etc. Please feel free to contact us.(nanotrun@yahoo.com)
Payment Methods
T/T, Western Union, Paypal, Credit Card etc.
Shipment Methods
By air, by sea, by express, as customers request.
5 FAQs of Silicon Carbide Ceramic Beam Used to Porcelain Tiles Plates Insulator Kiln
Silicon Carbide Ceramic Beam FAQs
1. What is a silicon carbide ceramic beam used for in kilns?
It’s a strong support structure for holding porcelain tiles, plates, or insulators during high-temperature firing. The beam withstands extreme heat, prevents warping, and ensures even heat distribution. This improves product quality and kiln efficiency.
2. Why pick silicon carbide ceramic beams over metal or other materials?
Silicon carbide handles higher temperatures without degrading. Metal beams warp or oxidize over time. This ceramic resists thermal shock, meaning it won’t crack if temperatures change fast. It lasts longer, reduces replacement costs, and keeps kiln operations stable.
3. What’s the maximum temperature these beams can handle?
They work reliably up to 1650°C (3000°F). Even at these temperatures, they stay strong and keep their shape. This makes them ideal for industrial kilns firing porcelain or technical ceramics needing intense heat.
4. How do I install and maintain silicon carbide beams?
Place them evenly inside the kiln, ensuring they sit flat on supports. Check alignment to avoid uneven stress. Clean beams after each use to remove debris or glaze residues. Inspect for cracks or surface damage regularly. Replace beams if flaws appear to prevent kiln issues.
5. Do these beams wear out quickly in harsh conditions?
No. Silicon carbide is highly resistant to abrasion, chemicals, and heat. With proper care, beams last years. Avoid sudden temperature drops or physical impacts to extend their life. Storing them in dry conditions when not in use also helps prevent damage.
(Silicon Carbide Ceramic Beam Used to Porcelain Tiles Plates Insulator Kiln)
REQUEST A QUOTE
RELATED PRODUCTS
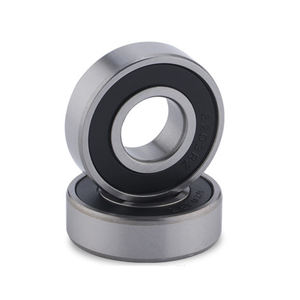
OEM Customized Refractory Material Industrial Furnace Sintered Silicon Carbide Ceramic Plate
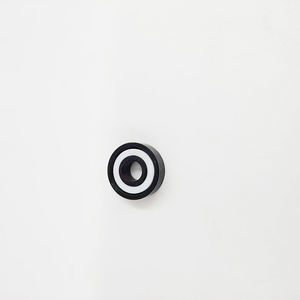
Mirror Polished Silicon Carbide SSIC SiC Ceramic Plate
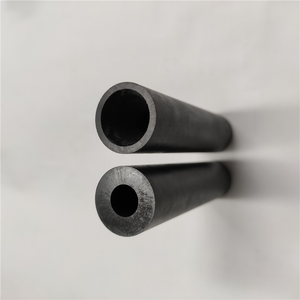
Engineering Ceramic Silicon Carbide Ceramic Bushing
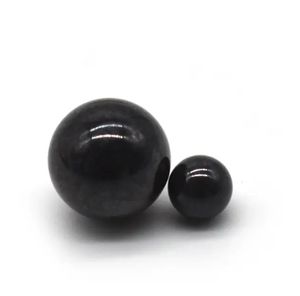
High Temperature Resistance Silicon Carbide Ceramic Pipe Sisic Sic Silicon Carbided Sic
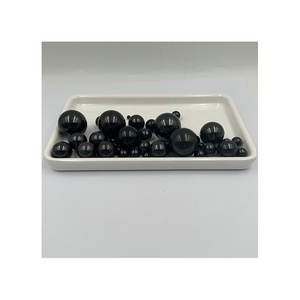
Factory Hexagonal Boron-carbide Silicon Carbide Ceramic Sheet
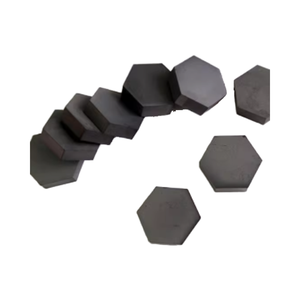