Discover Premium Ceramic Products | Durability & Elegance United | Advanced Ceramics
PRODUCT PARAMETERS
Description
Overview of Silicon Carbide Ceramics
Silicon Carbide (SiC) ceramics are renowned for their outstanding mechanical properties, including high hardness, strength at elevated temperatures, and excellent thermal shock resistance. These materials are pivotal in cutting-edge industrial applications, from abrasives to aerospace components, due to their unique combination of properties.
Features of Silicon Carbide Ceramics
High Hardness: Exceptional wear resistance.
Thermal Shock Resistance: Can withstand rapid temperature changes.
Chemical Stability: Resistant to most chemicals.
High Thermal Conductivity: Efficient heat dissipation.
Low Density: Lightweight for its strength.
(Combination of Reaction Sintered Silicon Carbide Ceramic Structural Components)
Specification of Combination of Reaction Sintered Silicon Carbide Ceramic Structural Components
Reaction sintered silicon carbide ceramic architectural components use high performance in severe problems. These components take care of temperature levels approximately 1600 ° C without shedding stamina. They resist thermal shock far better than the majority of ceramics. This makes them excellent for applications including quick temperature level changes. The material has a low thermal expansion coefficient. This decreases the danger of breaking under heat stress. Its thermal conductivity is more than conventional ceramics. Warmth disperses equally throughout the surface area.
The parts excel in mechanical sturdiness. They offer outstanding firmness near to diamond. Wear resistance transcends to metals and common porcelains. This prolongs service life in abrasive settings. Flexural stamina reaches 450 MPa. This permits usage in high-stress mechanical systems. Compressive stamina goes beyond 3000 MPa. They stand up to heavy loads without contortion.
Chemical security is an additional essential advantage. The product resists acids, antacid, and molten salts. It executes reliably in harsh industrial settings. Oxidation resistance continues to be solid also at peak temperature levels. This prevents destruction in oxygen-rich atmospheres.
Dimensional accuracy is maintained during production. Reaction sintering creates near-net-shape components. This reduces the requirement for substantial machining. Resistances remain within ± 0.5% of defined measurements. Surface area surfaces achieve Ra values below 1.6 micrometers. This satisfies demands for precision engineering applications.
Electric buildings consist of high dielectric strength. The product acts as an effective insulator in electronic systems. It stands up to arcing and electrical disintegration. This matches high-voltage applications.
Weight financial savings contrasted to steel options are significant. Thickness arrays between 3.02-3.10 g/cm FIVE. This helps reduce energy consumption in relocating components. The parts work in aerospace, energy manufacturing, and semiconductor manufacturing. They perform in pumps, seals, bearings, and furnace fixtures.
Personalized sizes and shapes are attainable via controlled sintering. Product pureness surpasses 99.5%. This makes certain constant performance throughout batches. Running settings consist of vacuum cleaner problems and high-pressure systems. No lubes are needed for sliding applications. Rubbing coefficients stay reduced under load.
Long-lasting dependability decreases upkeep expenses. The material does not require protective finishings. Efficiency remains steady over hundreds of thermal cycles. These attributes make reaction sintered silicon carbide a practical option for requiring industrial applications.
(Combination of Reaction Sintered Silicon Carbide Ceramic Structural Components)
Applications of Combination of Reaction Sintered Silicon Carbide Ceramic Structural Components
Response sintered silicon carbide (RS-SiC) ceramic architectural elements are used extensively across sectors. Their high hardness, thermal conductivity, and resistance to put on make them ideal for tough settings. In commercial machinery, RS-SiC components like seals, bearings, and nozzles take care of heavy lots and friction. They last longer than standard materials. They minimize downtime and maintenance expenses. Their ability to remain secure in high warmth avoids contortion throughout operation.
Aerospace and protection industries rely on RS-SiC for parts revealed to extreme conditions. Generator parts, heat shields, and rocket nozzles made from RS-SiC make it through heats and mechanical stress. The material’s light-weight nature improves fuel effectiveness. It withstands oxidation and erosion much better than metals. This ensures dependability in essential applications.
Power production uses RS-SiC in solar and nuclear systems. Photovoltaic panel manufacturing requires crucibles to melt silicon. RS-SiC crucibles deal with molten silicon without breaking down. They improve process performance. In atomic power plants, RS-SiC parts take care of warmth and radiation. Their stability under neutron irradiation makes them ideal for reactor cores.
Semiconductor producing requirements materials that stand up to plasma and chemicals. RS-SiC components like wafer managing components and etching parts keep accuracy in extreme procedures. Their low thermal development protects against warping. This ensures regular performance in chip manufacturing.
Chemical handling equipment deals with destructive substances. RS-SiC pumps, valves, and activator cellular linings withstand acids and alkalis. They reduce contamination threats. Their toughness cuts substitute expenses. They guarantee safe operation in hostile atmospheres.
Automotive systems benefit from RS-SiC in brake discs and engine components. The product’s warm resistance enhances stopping performance. It lowers wear in high-speed conditions. Electric vehicles utilize RS-SiC in battery thermal management. This improves security and durability.
RS-SiC’s flexibility originates from its unique residential properties. It adjusts to demanding applications. It provides affordable services where traditional products fail. Industries select RS-SiC for integrity and effectiveness.
Company Introduction
Advanced Ceramics founded on October 17, 2014, is a high-tech enterprise committed to the research and development, production, processing, sales and technical services of ceramic relative materials and products.. Since its establishment in 2014, the company has been committed to providing customers with the best products and services, and has become a leader in the industry through continuous technological innovation and strict quality management.
Our products includes but not limited to Silicon carbide ceramic products, Boron Carbide Ceramic Products, Boron Nitride Ceramic Products, Silicon Carbide Ceramic Products, Silicon Nitride Ceramic Products, Zirconium Dioxide Ceramic Products, Quartz Products, etc. Please feel free to contact us.(nanotrun@yahoo.com)
Payment Methods
T/T, Western Union, Paypal, Credit Card etc.
Shipment Methods
By air, by sea, by express, as customers request.
5 FAQs of Combination of Reaction Sintered Silicon Carbide Ceramic Structural Components
What is reaction sintered silicon carbide ceramic?
Reaction sintered silicon carbide (RSSC) ceramic forms through a high-temperature process combining silicon and carbon. This method creates a dense material with strong mechanical properties. RSSC parts handle extreme environments better than many metals or standard ceramics. They resist wear, heat, and corrosion effectively.
Why choose RSSC structural components over other materials?
RSSC parts last longer under stress. They work in temperatures up to 1650°C without losing strength. Metals often warp or corrode in similar conditions. RSSC stays stable chemically and physically. It costs less than some advanced alloys but performs better in harsh settings.
What temperature limits apply to RSSC components?
RSSC withstands continuous use up to 1380°C. Short-term exposure can reach 1650°C. It resists thermal shock better than oxide ceramics. Sudden temperature changes cause minimal damage. This makes RSSC ideal for furnaces, turbines, or aerospace systems.
Are RSSC parts suitable for corrosive environments?
Yes. Acids, alkalis, and molten salts rarely affect RSSC. It outperforms stainless steel and alumina in chemical resistance. This suits industries like chemical processing, mining, or wastewater treatment. RSSC parts need less frequent replacement in aggressive settings.
How do RSSC components handle mechanical wear?
RSSC has high hardness, close to diamonds. It resists abrasion from particles, slurries, or friction. Components like seals, bearings, or nozzles last longer with RSSC. Maintenance costs drop due to reduced part replacement.
(Combination of Reaction Sintered Silicon Carbide Ceramic Structural Components)
REQUEST A QUOTE
RELATED PRODUCTS
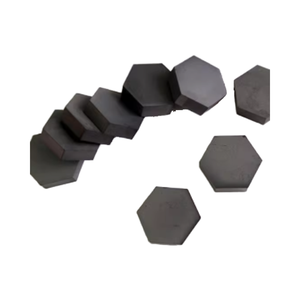
Ultrafine Silicon Carbide Powder Black/Green Silicon Carbide (SiC) Powder for Ceramic Manufacturing
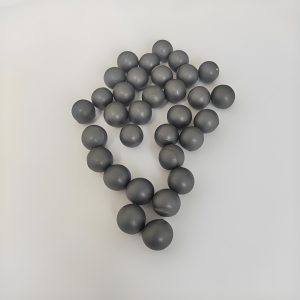
High Purity Silicon Carbide Fine Ball Customize Ceramic SiC Ball
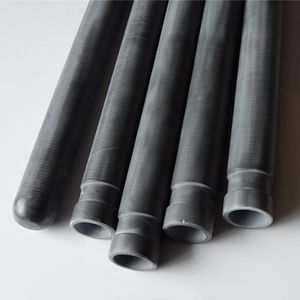
High Hardness Silicon Carbide Ceramic Hexagon Type SiC Ballistic Plates
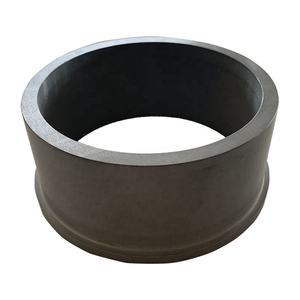
Hot Silicon Carbide Ceramic Sheet Boron Carbide Ceramic Plates B4C Tiles for Sample
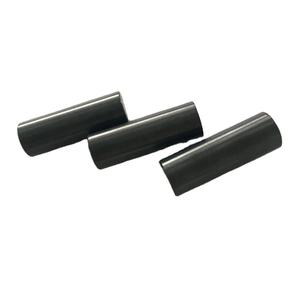
Square Silicon Carbide Ceramic for Ballistic Plate
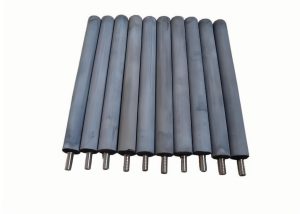