Discover Premium Ceramic Products | Durability & Elegance United | Advanced Ceramics
PRODUCT PARAMETERS
Description
Introduction to Alumina Ceramics
Alumina ceramics are known for their high hardness, wear resistance, corrosion resistance, good electrical insulation and high temperature stability. According to the different alumina content, it can be divided into different grades, such as 95 porcelain, 99 porcelain, etc., among which 99 porcelain refers to ceramic materials with an alumina content of 99%. As the alumina content increases, its mechanical strength and electrical insulation properties will also increase accordingly.
Characteristics of Alumina Ceramics
High Hardness: Alumina ceramics have extremely high hardness, which makes it very wear-resistant and suitable for manufacturing abrasive tools and parts that require wear resistance.
Wear resistance: Due to its high hardness, alumina ceramics show excellent wear resistance and are suitable for manufacturing parts for long-term use.
Corrosion resistance: Alumina ceramics have good resistance to most acids and alkalis, making them widely used in the chemical industry.
Good electrical insulation: As an excellent electrical insulating material, alumina ceramics are widely used in electronic and electrical products.
High temperature stability: Ability to withstand extremely high temperatures without significant physical or chemical changes, which makes it an ideal choice for applications in high temperature environments.
Biocompatibility: In the medical field, certain grades of alumina ceramics are used to make medical devices such as artificial joints due to their good biocompatibility.
(96% Metallization Tube Alumina Ceramics Parts Al2o3 Alumina Ceramic)
Specifications of 96% Metallization Tube Alumina Ceramics Parts Al2o3 Alumina Ceramic
The 96% metallization tube alumina ceramics parts are engineered for high-performance applications. These components are made from aluminum oxide (Al2O3), a material understood for its toughness and resistance to severe problems. The 96% alumina structure guarantees a balance in between cost-effectiveness and technical capacity, appropriate for markets calling for accuracy and integrity. Metallization involves covering the ceramic surface with a steel layer, generally molybdenum or manganese, making it possible for solid bonds with metals for brazing or soldering. This process guarantees protected integration right into digital, mechanical, or vacuum systems. Key specs include a high melting point of approximately 1700 ° C, making these components suitable for high-temperature atmospheres. The product exhibits superb electrical insulation, with a dielectric strength going beyond 10 kV/mm. Its thermal conductivity varieties between 20-30 W/m · K, enabling effective heat dissipation in demanding configurations. Mechanical residential or commercial properties are durable, with a solidity of 80-90 HRA and a flexural strength of 300-400 MPa. The low thermal development coefficient (7-8 × 10 ^ -6/ ° C) minimizes dimensional modifications under thermal stress and anxiety. Surface surface options are available, with roughness levels as reduced as Ra 0.4 μm for applications requiring smooth user interfaces. Criterion tube measurements differ, with external sizes from 2mm to 50mm and sizes as much as 300mm. Custom shapes and sizes can be made to meet details layout requirements. These porcelains stand up to chemical deterioration, maintaining stability when revealed to acids, alkalis, and natural solvents. They are vacuum-tight, making them ideal for hermetic sealing in semiconductor and aerospace devices. Applications consist of vacuum cleaner interrupters, laser tubes, sensors, and high-voltage insulators. The metallized layer permits straight accessory to metal housings or electrodes, streamlining assembly in electronic bundles. Manufacturing sticks to rigorous high quality standards, with resistances as limited as ± 0.5% on vital dimensions. X-ray and ultrasonic testing guarantee defect-free elements. The material is RoHS-compliant, satisfying ecological policies. Correct handling is recommended to avoid surface area contamination prior to metallization. Storage suggestions consist of keeping parts in completely dry, room-temperature conditions to maintain performance. Technical support is available for product choice, design optimization, and post-processing support.
(96% Metallization Tube Alumina Ceramics Parts Al2o3 Alumina Ceramic)
Applications of 96% Metallization Tube Alumina Ceramics Parts Al2o3 Alumina Ceramic
96% metallization tube alumina ceramics components made from Al2O3 are commonly made use of in industries requiring high-performance products. These components incorporate alumina’s natural benefits with a metallized layer for much better capability. Alumina ceramics provide high thermal conductivity, excellent electrical insulation, and resistance to put on, warm, and chemicals. The metallization process includes a steel finishing, frequently molybdenum or manganese, to the ceramic surface area. This enables solid bonding with steels, making the components ideal for assemblies calling for both ceramic and steel components.
In electronics, these tubes serve as insulators or substrates in circuits. They deal with high voltages and temperatures, making certain steady efficiency in devices like sensors or power components. The metallized layer enables dependable connections between ceramic parts and steel electrodes, minimizing power loss.
Industrial devices uses these porcelains in harsh environments. They operate in pumps, valves, or seals revealed to corrosive chemicals or severe heat. The product’s firmness reduces wear, extending part lifespan. Metallized tubes additionally act as safety real estates for thermocouples or sensors in high-temperature procedures.
The auto market relies on them for ignition systems or exhaust sensors. They stand up to engine warm and resonances while preserving electric insulation. Metallized surface areas allow smooth assimilation with metal engine components, enhancing toughness.
Clinical gadgets use these ceramics for their biocompatibility and sanitation resistance. They are located in imaging devices or medical tools where precision and dependability issue. The metallized layer makes certain secure links in portable medical electronics.
Aerospace applications consist of sensing units or communication components. The ceramics endure severe temperature levels and radiation precede or high-speed flight. Metallization makes sure steady performance in essential systems.
These components are customizable in size, form, and metallization patterns. This flexibility supports tailored services for certain technical demands. Suppliers choose 96% alumina for its equilibrium of expense and efficiency, supplying a useful option for demanding applications.
Company Introduction
Advanced Ceramics founded on October 17, 2014, is a high-tech enterprise committed to the research and development, production, processing, sales and technical services of ceramic relative materials and products.. Since its establishment in 2014, the company has been committed to providing customers with the best products and services, and has become a leader in the industry through continuous technological innovation and strict quality management.
Our products includes but not limited to Silicon carbide ceramic products, Boron Carbide Ceramic Products, Boron Nitride Ceramic Products, Silicon Carbide Ceramic Products, Silicon Nitride Ceramic Products, Zirconium Dioxide Ceramic Products, Quartz Products, etc. Please feel free to contact us.(nanotrun@yahoo.com)
Payment Methods
T/T, Western Union, Paypal, Credit Card etc.
Shipment Methods
By air, by sea, by express, as customers request.
5 FAQs of 96% Metallization Tube Alumina Ceramics Parts Al2o3 Alumina Ceramic
96% metallization tube alumina ceramics parts (Al2O3) are high-performance components used in industries requiring durability, thermal stability, and electrical insulation. Below are answers to common questions.
What are 96% metallization tube alumina ceramics parts?
These parts are made from alumina ceramic containing 96% aluminum oxide. A metal layer is applied to the surface through metallization. This allows bonding with metals or other materials. They are used in electronics, aerospace, and industrial machinery for their strength and heat resistance.
How is the metallization process done on alumina ceramics?
Metallization involves coating the ceramic surface with a metal paste, usually molybdenum or manganese. The part is heated in a high-temperature furnace. This creates a strong bond between the ceramic and metal layer. The process ensures reliable connections in assemblies requiring welding or brazing.
What temperatures can these parts handle?
96% alumina ceramics withstand temperatures up to 1600°C. The metallized layer remains stable under extreme heat. This makes them suitable for high-temperature environments like vacuum furnaces or semiconductor manufacturing.
Are they good for electrical insulation?
Yes. Alumina ceramics are excellent electrical insulators. The metallization layer adds conductivity only where needed. This combination is ideal for applications like insulators in spark plugs or high-voltage equipment.
Can they be customized in size and shape?
Yes. Manufacturers produce these parts in various sizes and shapes. The metallization pattern is adjusted based on application needs. Custom designs ensure compatibility with specific machinery or electronic systems. Always confirm requirements with the supplier to ensure performance.
(96% Metallization Tube Alumina Ceramics Parts Al2o3 Alumina Ceramic)
REQUEST A QUOTE
RELATED PRODUCTS
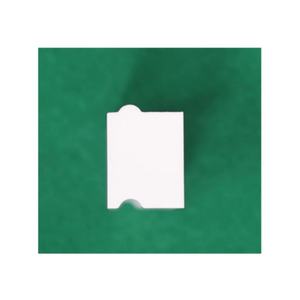
99.6 % Alumina Ceramic Sheet
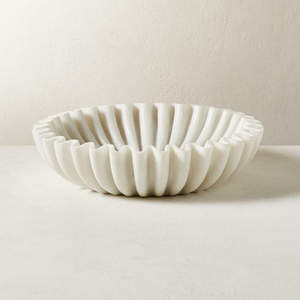
99.6 % Alumina Ceramic Sheet
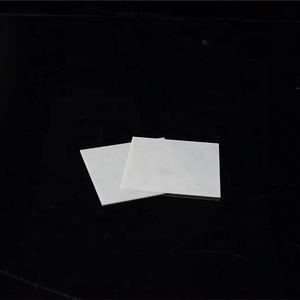
Precision 99% alumina ceramic round rod
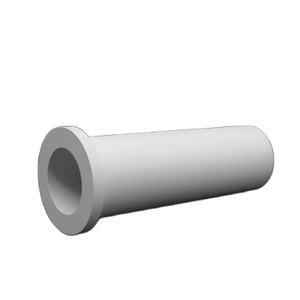
92%/95% High Wear Resistant Hexagonal Alumina Ceramic Tile
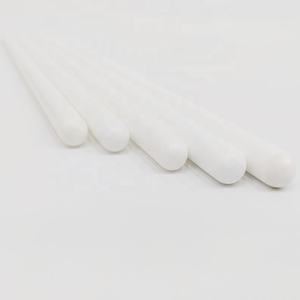
Customizable Alumina 99 Porcelain Ceramic Tube Insulated Al2O3 Ceramic Tubes Moulded Ceramic Plates
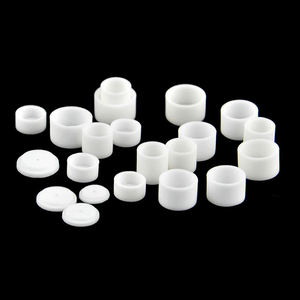