Discover Premium Ceramic Products | Durability & Elegance United | Advanced Ceramics
PRODUCT PARAMETERS
Description
Introduction to Alumina Ceramics
Alumina ceramics are known for their high hardness, wear resistance, corrosion resistance, good electrical insulation and high temperature stability. According to the different alumina content, it can be divided into different grades, such as 95 porcelain, 99 porcelain, etc., among which 99 porcelain refers to ceramic materials with an alumina content of 99%. As the alumina content increases, its mechanical strength and electrical insulation properties will also increase accordingly.
Characteristics of Alumina Ceramics
High Hardness: Alumina ceramics have extremely high hardness, which makes it very wear-resistant and suitable for manufacturing abrasive tools and parts that require wear resistance.
Wear resistance: Due to its high hardness, alumina ceramics show excellent wear resistance and are suitable for manufacturing parts for long-term use.
Corrosion resistance: Alumina ceramics have good resistance to most acids and alkalis, making them widely used in the chemical industry.
Good electrical insulation: As an excellent electrical insulating material, alumina ceramics are widely used in electronic and electrical products.
High temperature stability: Ability to withstand extremely high temperatures without significant physical or chemical changes, which makes it an ideal choice for applications in high temperature environments.
Biocompatibility: In the medical field, certain grades of alumina ceramics are used to make medical devices such as artificial joints due to their good biocompatibility.
(Customized Alumina Ceramic Part High Temperature Resistant Industrial Ceramic Part)
Specifications of Customized Alumina Ceramic Part High Temperature Resistant Industrial Ceramic Part
Personalized alumina ceramic components are crafted for high-temperature commercial applications. These components make use of light weight aluminum oxide as the main material. The alumina material ranges from 95% to 99.5%, making sure strong performance. They stand up to temperatures as much as 1700 ° C without losing architectural honesty. This makes them perfect for severe warm environments. The product has high solidity, placing simply below rubies on the Mohs scale. It stands up to wear efficiently, expanding the lifespan of elements. Alumina porcelains preserve security under mechanical stress. They deal with hefty lots without warping. Thermal shock resistance is a vital attribute. Rapid temperature level adjustments do not cause cracking. This reliability fits applications with changing heat conditions. Electric insulation buildings stay constant even at heats. The material does not conduct electrical energy, protecting against brief circuits. Chemical resistance is an additional advantage. Alumina ceramics stand up to rust from acids, antacid, and molten steels. They do well in extreme chemical atmospheres. Customization options consist of complicated forms and precise measurements. Components can be customized to fulfill details design needs. Surface surfaces differ from polished to rough appearances. Resistances are limited, making certain specific fits in machinery. These porcelains are machined making use of advanced techniques like grinding or laser cutting. Applications span numerous markets. They are used in furnace cellular linings, kiln furnishings, and welding nozzles. Semiconductor manufacturing relies upon alumina components for wafer handling. Automotive systems utilize them in sensors and ignition components. Clinical tools gain from their biocompatibility and sturdiness. The components are light-weight compared to metal choices. This reduces energy usage in relocating systems. Setup is uncomplicated due to their dimensional precision. Upkeep needs are very little, reducing functional expenses. Alumina ceramics are environmentally stable. They do not weaken under UV exposure or moisture. Customized orders include models and bulk manufacturing. Evaluating guarantees each set meets market criteria. Technical assistance is readily available for material option and style optimization. These components enhance effectiveness sought after commercial settings.
(Customized Alumina Ceramic Part High Temperature Resistant Industrial Ceramic Part)
Applications of Customized Alumina Ceramic Part High Temperature Resistant Industrial Ceramic Part
Personalized alumina ceramic parts handle extreme warmth. They operate in difficult commercial settings. These parts remain steady at temperatures over 1600 ° C. Factories utilize them in heaters, kilns, and activators. Alumina ceramics resist wear, corrosion, and chemical damages. This makes them last longer than metal or plastic components.
Aerospace industries rely upon alumina porcelains. Jet engines and wind turbines require heat-resistant components. Alumina parts minimize failing dangers during high-speed trips. They protect electric systems in spacecraft. This prevents brief circuits in extreme conditions.
Automotive manufacturers utilize alumina ceramics in engines. Sensors and spark plugs made from alumina deal with high heat. Electric automobiles use these components in battery systems. They secure versus overheating and boost safety and security.
Energy production needs long lasting products. Alumina parts line burning chambers in nuclear power plant. They hold up against fires and gas disintegration. Photovoltaic panel and nuclear reactors utilize alumina insulators. These components make sure secure energy output under tension.
Clinical equipment requires tidy, non-toxic products. Alumina ceramics make medical tools and implants. They resist body fluids and sanitation processes. Dental crowns and joint substitutes utilize alumina for toughness and biocompatibility.
Electronic devices take advantage of alumina’s insulation buildings. Circuit card and semiconductors utilize ceramic substratums. Alumina protects against overheating in silicon chips. This boosts gadget efficiency and life expectancy.
Custom sizes and shapes fit particular equipments. Designers design alumina parts for precise demands. This reduces waste and boosts efficiency. Factories save cash with fewer substitutes.
Alumina porcelains work in rough chemical atmospheres. Pumps, shutoffs, and pipelines made from alumina resist acids and antacids. Mining and oil industries use them to avoid deterioration.
These components fit high-precision devices. Reducing blades and grinding discs make use of alumina for sharp edges. They stay efficient under heavy usage.
Customized alumina ceramics solve commercial difficulties. Their warmth resistance and resilience satisfy stringent demands. Industries count on them for important applications.
Company Introduction
Advanced Ceramics founded on October 17, 2014, is a high-tech enterprise committed to the research and development, production, processing, sales and technical services of ceramic relative materials and products.. Since its establishment in 2014, the company has been committed to providing customers with the best products and services, and has become a leader in the industry through continuous technological innovation and strict quality management.
Our products includes but not limited to Silicon carbide ceramic products, Boron Carbide Ceramic Products, Boron Nitride Ceramic Products, Silicon Carbide Ceramic Products, Silicon Nitride Ceramic Products, Zirconium Dioxide Ceramic Products, Quartz Products, etc. Please feel free to contact us.(nanotrun@yahoo.com)
Payment Methods
T/T, Western Union, Paypal, Credit Card etc.
Shipment Methods
By air, by sea, by express, as customers request.
5 FAQs of Customized Alumina Ceramic Part High Temperature Resistant Industrial Ceramic Part
What is the maximum temperature customized alumina ceramic parts can handle? Alumina ceramic parts handle temperatures up to 1800°C. The exact limit depends on material purity and environmental conditions. They maintain structural strength and shape under high heat. This makes them suitable for furnaces, kilns, and reactors.
Can these parts be customized for specific industrial needs? Yes. Manufacturers adjust shapes, sizes, and features to match requirements. Customization includes holes, grooves, or complex geometries. Precision machining ensures parts fit exact applications. This flexibility supports industries like aerospace, automotive, and energy.
What industries use high-temperature alumina ceramic parts? Common users include metallurgy, chemical processing, and electronics. They work in environments where metals fail. Examples include furnace linings, heat shields, and semiconductor components. Their stability under stress and heat makes them ideal for harsh settings.
How do alumina ceramics compare to metal parts in high-heat situations? Alumina ceramics outperform metals in extreme temperatures. Metals warp or oxidize. Ceramics resist thermal shock, wear, and corrosion. They last longer in continuous high-heat use. This reduces downtime and replacement costs.
What factors affect the performance of customized alumina ceramic parts? Material quality matters. High-purity alumina improves heat resistance. Design accuracy ensures proper fit and function. Surface finish and density impact durability. Testing under real-world conditions confirms performance. Proper installation and maintenance extend service life.
(Customized Alumina Ceramic Part High Temperature Resistant Industrial Ceramic Part)
REQUEST A QUOTE
RELATED PRODUCTS
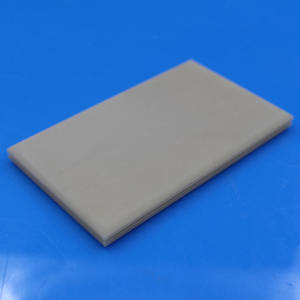
Al2o3 Crucible Alumina Ceramic High Refractoriness Alumina Al2O3 Ceramic Crucible
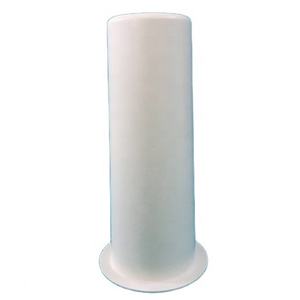
Thickness 0.635mm to 1mm 99% Al2o3 Alumina Ceramic Substrate Ceramic Plate Zirconia Plate
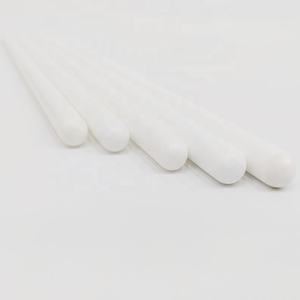
High Quality Industrial Ceramic Alumina Ceramics for Textile Whole Polishing and Wear Resistance Application
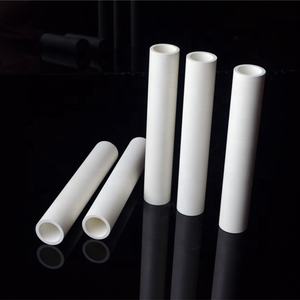
High Temperature Chemical Industrial 92 95 Al2o3 High Alumina Ceramic Plate
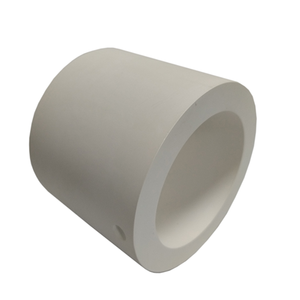
Porous Alumina Ceramic Ball Premium Ceramics Product
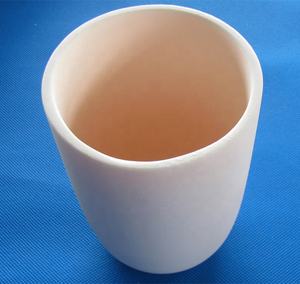