Discover Premium Ceramic Products | Durability & Elegance United | Advanced Ceramics
Ceramics is a kind of dense solid mainly made of aluminum silicate formed after a series of technological treatments such as fine crushing, mixing, molding, drying, and high-temperature sintering with clay, minerals, and other inorganic compounds as the main raw materials. Depending on the raw materials used and the texture, ceramic products can be divided into two main categories: advanced or fine ceramics and traditional ceramics.
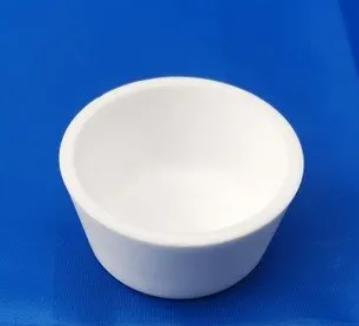
Traditional ceramics
Traditional ceramics are based on natural mineral raw materials, such as clay, quartz, and feldspar, which are processed and made into products. It is generally used for daily-use ceramics, building sanitary ceramics, industrial ceramics, decorative art ceramics, etc. For example, tableware, tea sets, vases, and other household items; wall and floor tiles, toilets, wash basins, etc.; insulators, chemical containers, etc.; or sculptures and handicrafts. Among them, clay provides plasticity and adhesion during sintering, quartz (SiO2) increases hardness and abrasion resistance and helps to reduce the coefficient of thermal expansion, and feldspar (KAlSi3O8 – NaAlSi3O8 – CaAl2Si2O8) serves as a melting agent to help lower the sintering temperature and give the product a glassy luster. Other ingredients that may be added include limestone, dolomite, talc, etc., to adjust properties or color. Traditional ceramics are sintered at a wide range of temperatures, depending on the specific formulation and desired properties. There are three general categories: low-fire ceramics (e.g., earthenware), between about 900°C and 1,200°C; medium-fire ceramics, between about 1,200°C and 1,350°C; and high-fire ceramics (e.g., porcelain): usually requiring more than 1,350°C, and sometimes up to 1,400°C.
Traditional ceramics are relatively hard but not as hard as fine ceramics, and the density varies according to the type; pottery is lighter, and porcelain is denser, so pottery has a high water absorption rate, while porcelain hardly absorbs water. In terms of heat resistance and mechanical strength, traditional ceramics’ heat resistance is good, but sharp temperature differences may lead to rupture, and its mechanical strength can range from medium to high, depending on the type of ceramics and production process. The chemical stability is relatively good, showing good resistance to most acids and alkalis.
In general, traditional ceramics are cheaper to produce, easier to mass-produce, have excellent corrosion resistance and aesthetics, exhibit excellent thermal insulation in some applications, and have a long tradition of skill and great cultural value. However, compared to fine ceramics, traditional ceramics have lower mechanical strength and abrasion resistance and are more susceptible to thermal shock and breakage. They also consume more energy during production and are more difficult to mold for complex shapes.
Advanced ceramics
Advanced ceramics, also known as technical ceramics, engineering ceramics, or high-performance ceramics, are ceramic materials with excellent properties made from high-purity, synthetic raw materials and through precision-controlled production processes. Compared with traditional ceramics, advanced ceramics are significantly different in terms of composition selection, manufacturing process, and the performance of the final product. For example, oxides [alumina (Al₂O₃), zirconia (ZrO₂), etc.] are commonly used in structural and functional ceramics; nitrides [e.g., silicon nitride (Si₃N₄)], which are widely used in high-temperature environments because of their high strength and high-temperature resistance; and carbides [silicon carbide (SiC)], which are extremely hard and wear-resistant and are suitable for extreme conditions; borides [boron carbide (B₄C) and titanium diboride (TiB₂)] have excellent wear resistance and thermal stability; and other materials, such as phosphates, fluorides, and other specialty compounds, are selected for specific needs. These materials often need to be finely processed to ensure purity and particle size distribution for better performance.
Sintering temperatures for advanced ceramics are generally higher than for conventional ceramics, depending on the material type, e.g., sintering of alumina ceramics requires about 1600°C to 1800°C; silicon nitride ceramics about 1700°C to 2000°C; silicon carbide ceramics about 2000°C to 2200°C; and zirconium oxide ceramics about 1450°C to 1600°C.
Because advanced ceramics have very high melting points, special sintering methods such as hot press sintering, reaction sintering, discharge plasma sintering (SPS), and microwave sintering are often used to promote densification and improve the microstructure. As a result, the high strength and hardness of advanced ceramics far exceed that of metals and other traditional materials, and certain advanced ceramic materials (e.g., silicon carbide) have a lower density specific gravity, making them suitable for lightweight designs. In addition, many advanced ceramics are excellent electrical insulators and are stable at very high temperatures, making them suitable for use in aerospace and engine components; they are highly resistant to corrosion and oxidation and show good resistance to most chemicals. Some materials (such as hydroxyapatite) are biocompatible and can be used in medical implants. Its special functionality, such as piezoelectricity, ferroelectricity, magnetism, etc., can be used in electronic components and other high-tech fields.
Advanced ceramics offer excellent mechanical properties such as high strength, hardness, and wear resistance; good thermal and chemical stability; customizable physical and chemical properties for specific applications; long life and reliability; reduced maintenance costs; and are environmentally friendly, non-toxic, and recyclable. However, the manufacturing process is complex and costly; the material is brittle and fragile, limiting certain application scenarios; machining is difficult, especially for parts with complex shapes; and the scale of production is relatively small, with limited market availability.
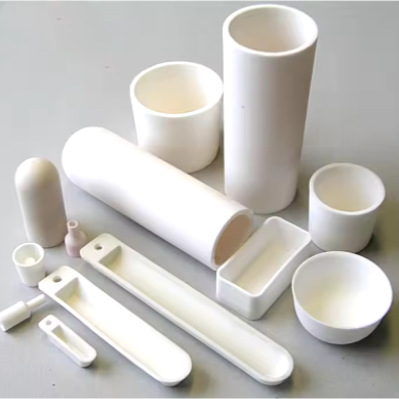
Overall, despite the challenges, advanced ceramics play an integral role in a number of high-tech fields due to their excellent performance and continue to expand into new applications as technology advances.
Supplier
Advanced Ceramics founded on October 17, 2012, is a high-tech enterprise committed to the research and development, production, processing, sales and technical services of ceramic relative materials and products. Our products includes but not limited to Boron Carbide Ceramic Products, Boron Nitride Ceramic Products, Silicon Carbide Ceramic Products, Silicon Nitride Ceramic Products, Zirconium Dioxide Ceramic Products, etc. If you are interested, please feel free to contact us.(nanotrun@yahoo.com)