Discover Premium Ceramic Products | Durability & Elegance United | Advanced Ceramics
The global commercial landscape is observing the unmatched need for boron carbide balls, driven by rising needs in defense, energy, and advanced production. As a leading supplier, we report a 45% year-on-year surge in orders for B4C boron carbide components, particularly in regions prioritizing ballistic protection and high-wear applications. Renowned for their extreme hardness (second only to diamond) and neutron absorption capabilities, these ceramic spheres are critical in armor systems, nuclear reactors, and precision machining tools.
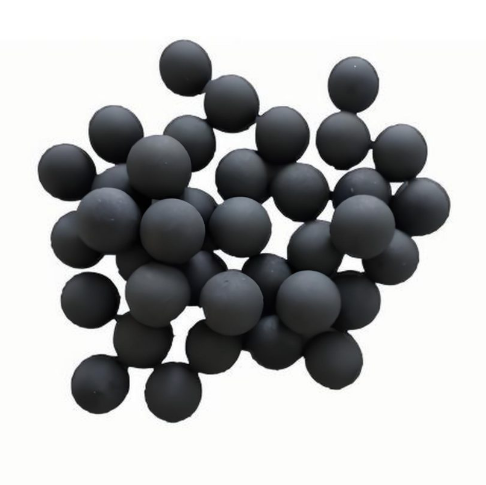
Boron Carbide B4C Balls
Boron carbide’s unique properties—low density (2.52 g/cm³), thermal stability up to 2,400°C, and resistance to chemical corrosion—make it indispensable for modern defense solutions. For instance, composite armor panels integrating B4C boron carbide tiles with ultra-high-molecular-weight polyethylene (UHMWPE) have become the gold standard for military vehicles and personnel protection, achieving NIJ Level IV ballistic standards. Recent geopolitical tensions have accelerated investments in lightweight, survivable armor, with NATO nations alone projected to spend $12 billion on advanced materials by 2026.
Industrial sectors are equally reliant on boron carbide balls for abrasive and wear-resistant applications. Kärcher’s adoption of boron carbide nozzles for high-pressure water jets (1,000+ liters/hour) highlights their dominance in machinery requiring zero erosion under extreme operational stress. Similarly, semiconductor manufacturers utilize these balls in precision grinding processes to maintain sub-micron tolerances for silicon wafers—a market growing at 9% CAGR due to AI and 5G expansion.
The boron carbide rate continues to be unpredictable, affected by resource deficiency and energy-intensive manufacturing procedures. Present market prices float in between $6,000–$15,000 per statistics load, with high-purity qualities (> 99.5%) commanding premiums. To mitigate costs, suppliers are adopting reactive sintering techniques and recycling post-industrial scrap, achieving 20% cost reductions without compromising ASTM E1461 thermal conductivity standards.
China’s manufacturing ecosystem now leads in scalable B4C boron carbide production, leveraging automated hot-pressing systems and ISO 9001-certified quality controls. Significant suppliers offer bulk prices as low as $0.85 per round (3mm size) for orders surpassing 100,000 units, cementing partnerships with European aerospace firms and North American defense professionals. The 2025 International Armored Automobiles Meeting in London will certainly spotlight these improvements, including live demonstrations of boron carbide-reinforced lorry hulls.
Emerging applications in green energy further amplify demand. Nuclear fusion projects, such as ITER, require boron carbide balls as neutron moderators in reactor shielding—a sector poised to consume 500+ tons annually by 2030. Concurrently, EV battery recyclers deploy boron carbide grinding media to recover lithium and cobalt, aligning with EU circular economy mandates.
In this age of business reengineering, boron carbide, as a calculated asset, can allow the marketplace to break through operational constraints and guarantee its technological forefront. Distributors who grasp the synthesis and application of boron carbide will certainly not just manage the marketplace but also shape the future of global infrastructure.
Supplier
If you are looking for Boron Carbide Balls, please send an email to: sales1@rboschco.com
Tags: boron carbide,b4c boron carbide,boron carbide price