Discover Premium Ceramic Products | Durability & Elegance United | Advanced Ceramics
Alumina and zirconia ceramics are two advanced and durable materials, and their unique characteristics make them highly versatile for industrial applications. The purity of alumina ceramic (Al two O FOUR) is 88-99.9%, which controls high-temperature insulation and wear-resistant components. On the other hand, zirconia ceramics (ZrO TWO) have achieved fracture toughness 3-4x higher than alumina through phase transformation toughening, which is a savior for biomedical implants and precision ball valves.
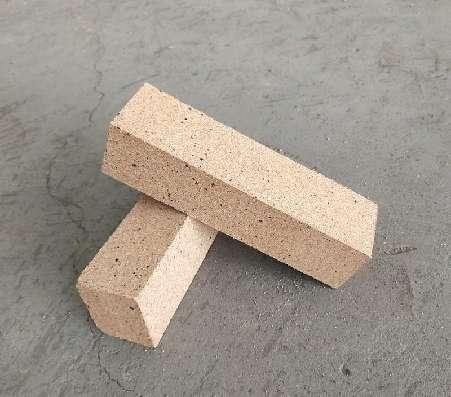
Alumina ceramics
The manufacturing divergence begins at raw material synthesis. Alumina ceramics use Bayer-processed aluminum oxide powders sintered at 1,600-1,800°C, yielding Vickers hardness of 1,500-2,000 HV. Zirconia requires stabilizers like yttria (3Y-TZP) or ceria (Ce-TZP) to prevent catastrophic phase changes during cooling. Suppliers such as Shenzhen Hard Precision Ceramics Co., Ltd. now provide laser diffraction-certified zirconia powder with D50 ≤ 0.5 μ m, which can achieve a density of 99.5% after sintering at 1450 ° C.
Thermal shock resistance divides their utility maps. Alumina’s lower thermal expansion coefficient (8×10 ⁻⁶/ ° C vs. zirconia’s 10.5 x10 ⁻⁶/ ° C )makes it ideal for kiln furnishings and molten metal handling. However, the working temperature of 1200 ° C+ for zirconia (compared to 1650 ° C for alumina) is sufficient for oral crowns, and its 1200 MPa bending toughness can prevent microfracture under occlusal pressure. Japanese automaker Denso recently switched to using aluminum oxide spark plug insulators, reducing premature ignition failures in turbocharged engines by 73%.
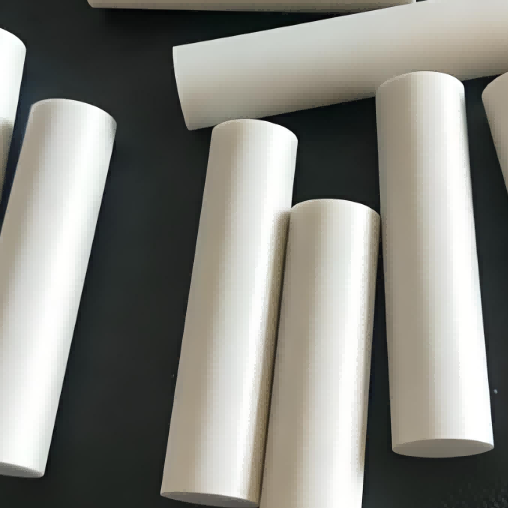
Zirconia ceramics
Wear performance reveals another trade-off. Alumina’s 9 Mohs hardness outperforms zirconia’s 8.5, making it the go-to for coal slurry pump liners. But zirconia’s self-lubricating phase transition under stress (tetragonal → monoclinic) grants it dominance in hip joint bearings. South Korean supplier Samhwa Ceramics’ ZTA (zirconia-toughened alumina) hybrid now serves 38% of global mining screen mesh demand, blending 15% zirconia into alumina matrices for a 30% longer service life.
Electrical properties further demarcate their territories. Alumina’s 10¹⁴ Ω·cm volume resistivity anchors its role in high-voltage insulators for 500kV transmission lines. Zirconia’s oxygen ion conductivity at 400-600°C (0.1 S/cm) makes it irreplaceable in solid oxide fuel cell (SOFC) electrolytes. Guangdong Fenghua Advanced Technology’s 8YSZ (8% yttria-stabilized zirconia) wafers now power 60% of China’s SOFC prototypes, achieving 0.15W/cm² at 750°C.
Cost structures diverge sharply. Alumina ceramic components cost $0.5-5/piece for standard shapes, thanks to abundant bauxite reserves. Zirconia’s $20-200/piece price reflects rare zircon sand sourcing and energy-intensive sintering. However, the new water-based injection molding of Zhengzhou Skyline Ceramics reduces zirconia processing waste from 40% to 12%, making dental abutments 18% cheaper for EU importers.
Surface finish capabilities tilt toward zirconia. Its finer grain structure (0.2-0.5μm vs. alumina’s 1-3μm) permits Ra 0.02μm mirror polishing—critical for optical fiber ferrules. Alumina compensates with laser-drilled microholes (50μm diameter) in semiconductor wafer chucks. Shanghai Unipretec’s latest 99.7% alumina gas distribution plates achieve ±1% hole diameter tolerance across 300mm wafers, slashing thin-film deposition defects by 55%.
Rust resistance profiles vary starkly. Alumina holds up against focused acids (except HF) as much as 1,000 ° C, safeguarding its area in chemical reactor linings. Zirconia catches HCl above 200 ° C yet stands up to molten antacid– for this reason, its frequency in lightweight aluminum electrolysis cell cathodes. Canadian aluminum giant Rio Tinto Alcan now makes use of H.C. Starck’s MgO-partially stabilized zirconia in smelters, lowering cathode disintegration by 11% annually.
Machining challenges separate the two. Alumina’s brittleness needs ruby grinding, with tool wear rates 3x more than zirconia. Yet zirconia’s phase instability throughout reduces calls for cryogenic air conditioning. Shenzhen MVP Industrial’s ultrasonic-assisted milling currently creates zirconia turbine blade cores with ± 5μm dimensional precision, halving post-sintering shrinking differences.
Regulatory landscapes shape adoption curves. Alumina’s GRAS (Generally Recognized As Safe) FDA status enables food-grade rollers in chocolate conching machines. Zirconia faces stricter EU MDR 2017/745 scrutiny for implants due to potential low-level radioactivity—a hurdle overcome by Malaysia’s I-Berhad via ISO 13356-certified medical zirconia with <0.01 Bq/g U-238 content.
Supply chain innovations are reshaping accessibility. Alumina suppliers like Shandong Sinocera now offer 72-hour rapid prototyping for custom crucibles via binder jetting. Zirconia’s logistics leap comes from Vietnam’s Viglacera, whose Ho Chi Minh port warehouse stocks 500+ pre-sintered “green” zirconia blanks, enabling Asian clients to cut lead times from 8 weeks to 5 days.
Environmental impacts diverge. Alumina production emits 1.8t CO₂ per ton vs. zirconia’s 3.5t, but zirconia’s 5x longer lifespan in cutting tools offsets this. Germany’s CeramTec now markets LCA-certified alumina-zirconia composite grinding media that reduces cement plant CO₂ by 9% through 40% energy savings in comminution.
Military/aerospace demands push boundaries. Alumina’s EMI shielding (60dB attenuation at 10GHz) protects missile guidance systems, while zirconia’s 5.6g/cm³ density (vs. alumina’s 3.9g/cm³) enables armor-piercing projectile tips. Lockheed Martin’s F-35 program now sources 92% alumina radomes from Kyocera, surviving Mach 1.6 thermal shocks without signal loss.
The future lies in hybrid systems. Tokyo-based NGK Insulators’ ALZIRCOR ™ (alumina-zirconia-carbon) composite withstands 1,850 ° C in blast furnace tuyeres, outliving pure alumina by 8 months. At the same time, Saint-Gobain’s ZirPro ® grains combine zirconia’s strength with alumina’s price account for the precision polishing of 5G mobile phone coverings.
As global sectors face rising functional extremes– from deep-sea oil exploration to combination activator containment– the alumina-zirconia harmony offers a product lexicon for 21st-century design. Suppliers mastering both ceramics’ DNA while demystifying their selection matrices will empower buyers to navigate this bifurcated landscape with precision.
Supplier
If you need high quality Alumina ceramics and Zirconia ceramics, please feel free to contact us. You can click on the product to contact us. (sales8@nanotrun.com)
Tags: Alumina ceramics, Zirconia ceramics,alumina