Discover Premium Ceramic Products | Durability & Elegance United | Advanced Ceramics
PRODUCT PARAMETERS
Description
Overview of aluminum nitride ceramics
Aluminum Nitride Ceramic is an advanced ceramic material with aluminum nitride as the main component. It has been widely used in electronics, optics, and mechanics due to its unique properties.
Features of aluminum nitride ceramics
High thermal conductivity: Aluminum nitride ceramics have relatively high thermal conductivity, usually between 170-260 W/m·K, which makes it an excellent heat dissipation material. It is especially suitable for electronic devices that require efficient heat dissipation, such as substrate materials for power semiconductor devices.
Good electrical insulation: Despite its high thermal conductivity, aluminum nitride ceramics are excellent insulators of electricity, which can effectively prevent current leakage and ensure the safe operation of electronic components.
Low dielectric constant and dielectric loss: These characteristics make aluminum nitride ceramics very suitable for use in high-frequency circuits because it can reduce energy loss during signal transmission.
High temperature resistance: Aluminum nitride ceramics can maintain structural stability and strength at extremely high temperatures. Its melting point is about 2800°C, so it is suitable for applications in high temperature environments.
Low thermal expansion coefficient: Compared with semiconductor materials such as silicon, aluminum nitride has a lower thermal expansion coefficient, which means it has better dimensional stability when the temperature changes, which helps improve packaging reliability.
Corrosion resistance: Aluminum nitride ceramics have good chemical stability to most molten metals and are not easily oxidized or corroded, allowing them to perform well in harsh environments.
High mechanical strength: Although not as hard as some other types of ceramic materials, aluminum nitride ceramics still provide enough mechanical strength to allow them to be used in many structural applications.
(Excellent Thermal Conductivity Aluminium Nitride AlN Ceramic Substrate)
Specifications of Excellent Thermal Conductivity Aluminium Nitride AlN Ceramic Substrate
Exceptional Thermal Conductivity Aluminium Nitride (AlN) Ceramic Substratum uses superior efficiency for sophisticated digital applications. It gives high thermal conductivity, generally varying between 170-220 W/m · K. This makes certain effective heat dissipation, essential for tools needing thermal administration. The product preserves stable efficiency also under high-temperature problems, making it perfect for power electronics, LED lighting, and semiconductor components.
AlN ceramic substratums include low electrical conductivity, serving as dependable insulators in circuits. Their dielectric toughness surpasses 15 kV/mm, stopping electrical leakage. This mix of thermal and electrical residential properties sustains safe operation in high-power atmospheres.
The product demonstrates strong mechanical sturdiness. It has a flexural toughness of 300-400 MPa, resisting splits under mechanical stress and anxiety. Its hardness gets to 12 GPa, ensuring wear resistance. This effectiveness expands the life expectancy of elements popular commercial settings.
AlN substrates exhibit a thermal expansion coefficient near silicon (4.5 × 10 ⁻⁶/ ° C). This compatibility minimizes thermal tension when adhered to silicon-based semiconductors, lessening failing risks throughout temperature cycles.
Surface area coating quality is precise, with roughness below 0.2 µm. Smooth surface areas enable accurate deposition of circuits and soldering of components. The substrates are available in customized thicknesses (0.25-1.5 mm) and sizes, accommodating varied style requirements.
Chemical security is an additional key advantage. AlN stands up to rust from acids, alkalis, and moisture, making sure reliability in severe environments. It operates efficiently in temperature levels as much as 1000 ° C without deterioration.
Applications consist of high-frequency communication tools, automotive power control devices, and aerospace systems. Its ability to handle heat in compact areas makes it appropriate for miniaturized electronics. Makers value AlN for improving tool efficiency, lowering power loss, and enhancing thermal cycling performance.
The product is compatible with thin-film and thick-film metallization processes. This enables assimilation with gold, silver, or copper layers for enhanced electrical links. AlN substratums satisfy RoHS and REACH standards, ensuring environmental compliance.
Personalized processing alternatives consist of laser cutting, exploration, and polishing. These services fit specialized geometries or surface therapies for specific niche applications.
(Excellent Thermal Conductivity Aluminium Nitride AlN Ceramic Substrate)
Applications of Excellent Thermal Conductivity Aluminium Nitride AlN Ceramic Substrate
Aluminum nitride (AlN) ceramic substrates are recognized for their outstanding thermal conductivity. This makes them optimal for high-performance digital applications. They relocate warm far from components successfully. This protects against overheating. AlN substratums work much better than traditional materials like alumina. They manage greater power densities. They keep gadgets secure under severe conditions.
AlN ceramic substrates are extensively utilized in power electronic devices. They serve as base products for semiconductor tools. These include protected gate bipolar transistors (IGBTs) and power components. The high thermal conductivity of AlN ensures warm spreads swiftly. This improves gadget dependability. It extends the life expectancy of digital systems.
LED lighting systems take advantage of AlN substratums. LEDs generate substantial heat during procedure. AlN substrates aid dissipate this warmth. They preserve optimum LED efficiency. They stop color shifts. They reduce the threat of early failing. This is essential for high-brightness LEDs in commercial or automobile lights.
RF and microwave parts rely upon AlN substrates. These substratums provide reduced signal loss. They take care of high-frequency procedures. They are made use of in radar systems, satellite communication devices, and 5G infrastructure. The thermal buildings of AlN make certain secure procedure also under long term use.
Automotive electronic devices utilize AlN substratums for electrical lorries (EVs) and crossbreed systems. Power control devices and onboard battery chargers call for efficient thermal administration. AlN substrates manage heat in small areas. They support the change towards greater performance and smaller components in modern-day cars.
AlN ceramic substrates are likewise applied in laser diodes and optoelectronic gadgets. They supply exact thermal control. This is required for preserving wavelength stability. It makes sure consistent result in clinical lasers or fiber-optic interaction systems.
The material’s electrical insulation homes add to its flexibility. AlN substrates separate circuits while transferring warm. They are chemically resistant. They perform well in rough settings. This includes aerospace applications or high-temperature industrial setups.
AlN substratums work with thin-film innovations. They permit the assimilation of complicated circuits. This sustains developments in miniaturized electronic devices. Their thermal growth coefficient matches products like silicon. This reduces mechanical anxiety during temperature adjustments. It avoids cracking or delamination in multilayer arrangements.
Producers pick AlN ceramic substratums for demanding applications. The mix of thermal efficiency, electrical insulation, and longevity fulfills the demands of modern-day innovation. It addresses obstacles in power thickness, warm monitoring, and tool integrity.
Company Introduction
Advanced Ceramics founded on October 17, 2014, is a high-tech enterprise committed to the research and development, production, processing, sales and technical services of ceramic relative materials and products.. Since its establishment in 2014, the company has been committed to providing customers with the best products and services, and has become a leader in the industry through continuous technological innovation and strict quality management.
Our products includes but not limited to Silicon carbide ceramic products, Boron Carbide Ceramic Products, Boron Nitride Ceramic Products, Silicon Carbide Ceramic Products, Silicon Nitride Ceramic Products, Zirconium Dioxide Ceramic Products, Quartz Products, etc. Please feel free to contact us.(nanotrun@yahoo.com)
Payment Methods
T/T, Western Union, Paypal, Credit Card etc.
Shipment Methods
By air, by sea, by express, as customers request.
5 FAQs of Excellent Thermal Conductivity Aluminium Nitride AlN Ceramic Substrate
What makes aluminium nitride ceramic substrates good for thermal management? Aluminium nitride (AlN) has high thermal conductivity, around 170-200 W/mK. This is much better than alumina or other ceramics. It moves heat away from electronic parts fast. This stops overheating. It works well in high-power devices like LED chips or power modules.
Where are AlN substrates mostly used? These substrates are common in electronics needing heat control. Examples include LED lighting, semiconductor packaging, and power electronics. They handle heat in circuits for telecom, automotive, and aerospace systems. They also work in laser diodes and radio-frequency devices.
How does temperature affect AlN substrates? AlN stays stable in high temperatures. It works in environments up to 1000°C. Its structure doesn’t break down easily under heat stress. Thermal expansion is low. This means parts don’t warp or crack when temperatures change fast.
Can AlN substrates be machined into complex shapes? Machining AlN is hard. It needs diamond-cutting tools. The material is brittle. Tight controls are required during grinding or drilling. Custom shapes are possible. But it’s best done by experts. Most suppliers offer pre-machined sizes or surface finishes.
Why are AlN substrates more expensive than alumina? Raw materials for AlN cost more. Production needs advanced processes. High purity and dense sintering are required for top thermal performance. The price is higher. But the performance in critical applications justifies the cost. Long-term reliability often offsets initial expenses.
(Excellent Thermal Conductivity Aluminium Nitride AlN Ceramic Substrate)
REQUEST A QUOTE
RELATED PRODUCTS
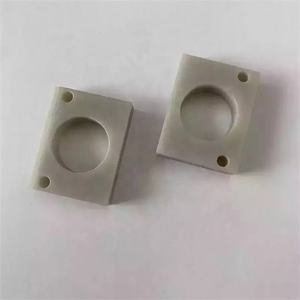
High Purity Aluminum Nitride Ceramic ALN Granule 70-120um 99.95%
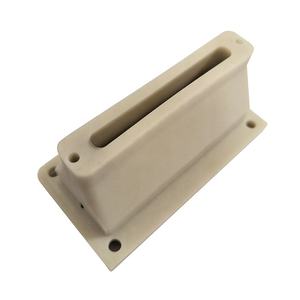
Wear Resistance Insulation ALN Aluminum Nitride Ceramic Ring/ Spacer/Insulator
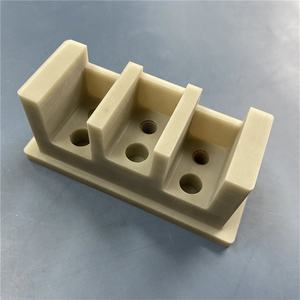
Semiconductor Ceramic Single Crystal 170 180w High Thermal Conductivity Aln Aluminum Nitride Ceramic Substrate
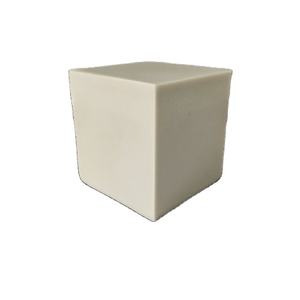
High Heat Conductivity AlN Aluminum Nitride Ceramic Sheet
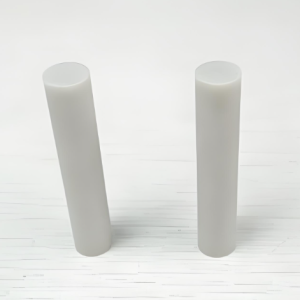
High Precision AlN Bar Aluminum Nitride Ceramic Rod
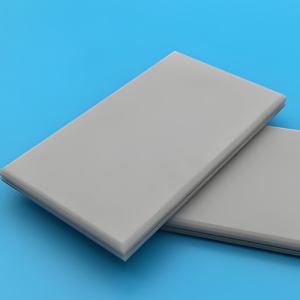