Discover Premium Ceramic Products | Durability & Elegance United | Advanced Ceramics
PRODUCT PARAMETERS
Description
Introduction to Alumina Ceramics
Alumina ceramics are known for their high hardness, wear resistance, corrosion resistance, good electrical insulation and high temperature stability. According to the different alumina content, it can be divided into different grades, such as 95 porcelain, 99 porcelain, etc., among which 99 porcelain refers to ceramic materials with an alumina content of 99%. As the alumina content increases, its mechanical strength and electrical insulation properties will also increase accordingly.
Characteristics of Alumina Ceramics
High Hardness: Alumina ceramics have extremely high hardness, which makes it very wear-resistant and suitable for manufacturing abrasive tools and parts that require wear resistance.
Wear resistance: Due to its high hardness, alumina ceramics show excellent wear resistance and are suitable for manufacturing parts for long-term use.
Corrosion resistance: Alumina ceramics have good resistance to most acids and alkalis, making them widely used in the chemical industry.
Good electrical insulation: As an excellent electrical insulating material, alumina ceramics are widely used in electronic and electrical products.
High temperature stability: Ability to withstand extremely high temperatures without significant physical or chemical changes, which makes it an ideal choice for applications in high temperature environments.
Biocompatibility: In the medical field, certain grades of alumina ceramics are used to make medical devices such as artificial joints due to their good biocompatibility.
(92% 95% Whole Ceramic Plates Alumina Ceramic Alumina hexagonal plain tile)
Specifications of 92% 95% Whole Ceramic Plates Alumina Ceramic Alumina hexagonal plain tile
The 92% and 95% entire ceramic plates alumina ceramic alumina hexagonal simple floor tiles are engineered for high-performance commercial applications. These floor tiles are made from high-purity alumina ceramic. They provide exceptional wear resistance, thermal security, and mechanical toughness. The material composition makes sure long-lasting sturdiness in severe atmospheres.
The hexagonal form offers consistent coverage and reliable interlocking. This design lowers voids in between floor tiles. It enhances security against effect and abrasion. The plain surface area reduces friction during product handling. Tiles are available in two alumina grades: 92% and 95%. Higher alumina content boosts solidity and deterioration resistance.
Criterion density varies from 10mm to 50mm. Custom-made dimensions can be created based upon needs. Ceramic tile length and width range 100mm and 300mm. Density is normally 3.6 g/cm six for 92% alumina and 3.7 g/cm six for 95% alumina. Water absorption prices stay below 0.1%. This guarantees minimal dampness penetration. Surface roughness is managed to preserve level of smoothness.
These ceramic floor tiles run efficiently in temperature levels up to 1600 ° C. Thermal shock resistance avoids fracturing throughout rapid temperature level modifications. Chemical inertness makes them suitable for acidic or alkaline problems. They stand up to oxidation and chemical disintegration.
Applications include lining for commercial equipment like chutes, receptacles, and pipelines. They secure machinery in mining, concrete production, and power generation. The tiles are used in chemical handling plants for corrosion-prone locations. They function as wear-resistant components in steel mills and shops.
Installation is simple. Tiles can be adhered making use of epoxy or mechanical bolts. Routine upkeep involves checking for surface area wear. Damaged tiles are easily replaced without interfering with whole systems.
Personalization choices consist of readjusting tile measurements, density, and edge style. Bulk orders are sustained for large tasks. Samples are available for testing performance in certain conditions.
The tiles satisfy worldwide criteria for industrial ceramics. Quality checks make sure consistency in density, firmness, and dimensional accuracy. Each set goes through extensive screening prior to delivery.
(92% 95% Whole Ceramic Plates Alumina Ceramic Alumina hexagonal plain tile)
Applications of 92% 95% Whole Ceramic Plates Alumina Ceramic Alumina hexagonal plain tile
92% and 95% entire ceramic plates constructed from alumina ceramic are extensively made use of in sectors calling for high wear resistance and resilience. These hexagonal plain floor tiles are designed for durable applications. Their structure guarantees durable performance in extreme environments.
The primary use of these alumina ceramic plates is in commercial tools protection. They line chutes, hoppers, and pipes in mining, power plants, and cement markets. The tiles soak up effect and decrease wear caused by abrasive materials like coal, ore, and crushed rock. Their high solidity stands up to scratching and disintegration. This extends equipment life-span and reduces maintenance expenses.
These ceramic plates are chemically steady. They stand up to direct exposure to acids, antacid, and heats as much as 1600 ° C. This makes them suitable for chemical processing plants and steel mills. The hexagonal shape allows limited interlocking during installment. Spaces in between ceramic tiles are decreased, avoiding product leakage and ensuring smooth surface area protection.
The 92% alumina floor tiles balance expense and efficiency for modest wear problems. They are suitable for applications where severe abrasion is not an everyday concern. The 95% alumina floor tiles provide greater thickness and strength. They do better in severe environments with constant hefty effect or extreme rubbing.
Setup is simple. The ceramic tiles can be bound making use of epoxy or safeguarded with bolts. Their lightweight design lowers structural lots on equipment. Customized sizes and thicknesses are offered to satisfy specific task requirements.
These alumina ceramic plates are likewise made use of in power generation systems. They shield devices dealing with fly ash and various other abrasive by-products. In the concrete industry, they secure crushers and grinders from raw material abrasion. Their thermal stability protects against cracking under rapid temperature adjustments.
The non-metallic nature of alumina ceramic gets rid of stimulate threats. This adds safety and security in explosive or flammable environments. The product does not rust, ensuring consistent performance in damp or harsh setups.
Services pick these tiles for their integrity and cost-effectiveness. Decreased downtime and substitute frequency boost operational effectiveness. The ceramic tiles are compatible with existing equipment, needing minimal alteration throughout installation.
Both 92% and 95% alumina ceramic plates are confirmed options for industrial wear troubles. Their adaptability throughout markets makes them a functional selection for securing vital facilities.
Company Introduction
Advanced Ceramics founded on October 17, 2014, is a high-tech enterprise committed to the research and development, production, processing, sales and technical services of ceramic relative materials and products.. Since its establishment in 2014, the company has been committed to providing customers with the best products and services, and has become a leader in the industry through continuous technological innovation and strict quality management.
Our products includes but not limited to Silicon carbide ceramic products, Boron Carbide Ceramic Products, Boron Nitride Ceramic Products, Silicon Carbide Ceramic Products, Silicon Nitride Ceramic Products, Zirconium Dioxide Ceramic Products, Quartz Products, etc. Please feel free to contact us.(nanotrun@yahoo.com)
Payment Methods
T/T, Western Union, Paypal, Credit Card etc.
Shipment Methods
By air, by sea, by express, as customers request.
5 FAQs of 92% 95% Whole Ceramic Plates Alumina Ceramic Alumina hexagonal plain tile
What is the material of 92% 95% alumina ceramic plates made of? The plates use alumina (aluminum oxide) as the main component. The 92% or 95% refers to the alumina content. The rest includes clay and other oxides. These materials are mixed and fired at high temperatures. This creates a dense, hard ceramic structure.
What are the key benefits of alumina ceramic plates? The plates resist wear and corrosion very well. They handle high temperatures up to 1600°C. They are chemically stable and do not react with acids or alkalis. Their hardness is much higher than metal or plastic. This makes them last longer in tough conditions.
Where are these ceramic plates commonly used? They are used in industrial machinery, mining equipment, and power plants. They protect surfaces from abrasion or impact. They are also used in electronics for insulation. Some applications include liners for pipelines or chutes. They work as wear-resistant parts in pumps or valves.
How do these plates compare to other materials? Metals like steel wear out faster under friction. Plastics melt or deform with heat. Alumina ceramics stay stable in heat and resist scratching. They are lighter than steel but stronger than most ceramics. Their lifespan is longer in harsh environments.
How are the hexagonal plain tiles installed? The tiles are attached using bolts, adhesives, or welding. The hexagonal shape allows tight fitting with minimal gaps. Surface preparation is important. Clean the area and ensure it is flat. Apply adhesive evenly or drill holes for bolts. Press the tiles firmly. Allow time for adhesives to set before use.
(92% 95% Whole Ceramic Plates Alumina Ceramic Alumina hexagonal plain tile)
REQUEST A QUOTE
RELATED PRODUCTS
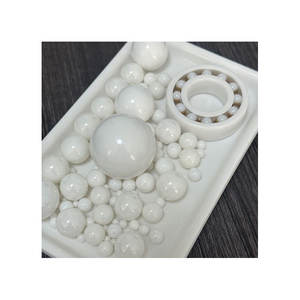
Wear-resistant Alumina Ceramic Sheets Industrial Wear-resistant Ceramics Alumina Ceramics
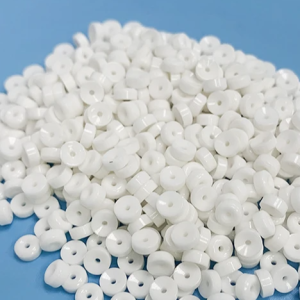
Long Service Life Materials Made of Ceramics 95 99 Al2o3 Insulator Alumina Ceramic Ring
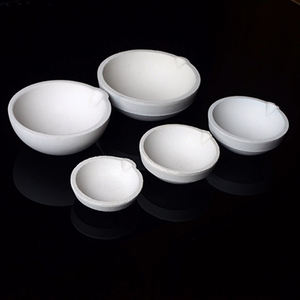
95% 99% Ceramic Pipe High Purity Heat Resistance Alumina Ceramic Tube
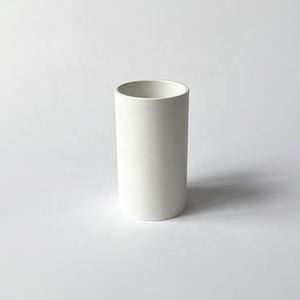
Custom Al2O3 Ceramics Precision Industrial CNC 99% 99.5% Alumina Ceramic Parts
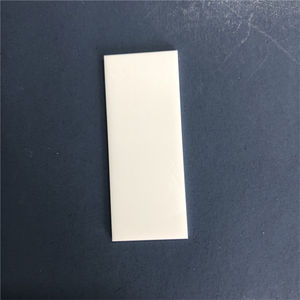
Factory Direct Alumina Ceramic – Wear-resistant and High-temperature Resistant Ceramic for Customized Processing
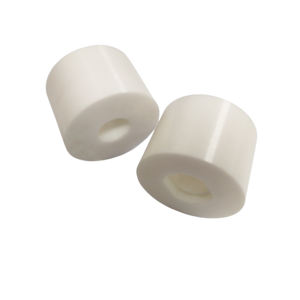