Discover Premium Ceramic Products | Durability & Elegance United | Advanced Ceramics
PRODUCT PARAMETERS
Description
Introduction to Alumina Ceramics
Alumina ceramics are known for their high hardness, wear resistance, corrosion resistance, good electrical insulation and high temperature stability. According to the different alumina content, it can be divided into different grades, such as 95 porcelain, 99 porcelain, etc., among which 99 porcelain refers to ceramic materials with an alumina content of 99%. As the alumina content increases, its mechanical strength and electrical insulation properties will also increase accordingly.
Characteristics of Alumina Ceramics
High Hardness: Alumina ceramics have extremely high hardness, which makes it very wear-resistant and suitable for manufacturing abrasive tools and parts that require wear resistance.
Wear resistance: Due to its high hardness, alumina ceramics show excellent wear resistance and are suitable for manufacturing parts for long-term use.
Corrosion resistance: Alumina ceramics have good resistance to most acids and alkalis, making them widely used in the chemical industry.
Good electrical insulation: As an excellent electrical insulating material, alumina ceramics are widely used in electronic and electrical products.
High temperature stability: Ability to withstand extremely high temperatures without significant physical or chemical changes, which makes it an ideal choice for applications in high temperature environments.
Biocompatibility: In the medical field, certain grades of alumina ceramics are used to make medical devices such as artificial joints due to their good biocompatibility.
(99 Ceramic Machining Parts 95 96 99 99.8 Al2O3 Alumina Ceramic)
Specifications of 99 Ceramic Machining Parts 95 96 99 99.8 Al2O3 Alumina Ceramic
The 99 ceramic machining components are made from high-purity alumina (Al2O3) porcelains, including qualities 95%, 96%, 99%, and 99.8%. These materials are crafted for accuracy performance sought after industrial applications. Alumina porcelains are recognized for their extraordinary firmness, use resistance, and thermal security. The differing pureness degrees satisfy different technological requirements. The 95% Al2O3 grade supplies a cost-efficient option with great mechanical stamina. It appropriates for applications like seals, insulators, and wear-resistant elements. The 96% Al2O3 quality provides enhanced density and surface area finish, ideal for digital substrates and cutting devices. The 99% Al2O3 quality supplies higher purity, boosting corrosion resistance and electrical insulation. This makes it a preferred selection for semiconductor devices and high-temperature environments. The 99.8% Al2O3 quality stands for premium-quality alumina with marginal pollutants. It masters severe conditions, such as aerospace or clinical implants, because of its remarkable biocompatibility and thermal shock resistance. All qualities feature a density variety of 3.6-3.9 g/cm six and a Vickers firmness above 1500 HV. They hold up against running temperature levels approximately 1600 ° C, preserving architectural honesty under thermal anxiety. The low thermal growth coefficient makes certain dimensional stability during fast temperature adjustments. These ceramics are chemically inert, withstanding acids, alkalis, and natural solvents. Precision machining allows limited resistances ( ± 0.01 mm) and complex geometries, consisting of strings, holes, and custom-made shapes. Surface finishes can be brightened to Ra ≤ 0.1 µm for lowered rubbing and enhanced securing. Applications cover electronics, automotive, power, and clinical sectors. Usual usages consist of ceramic nozzles, bearings, shutoff parts, and laboratory equipment. Personalization is available for dimensions, layers, and post-treatment procedures. The material’s dielectric residential or commercial properties make it ideal for high-voltage insulation. It likewise reduces particle generation in cleanroom environments. These alumina parts are examined for performance under mechanical tons, thermal cycling, and chemical exposure. They satisfy market standards for integrity and longevity.
(99 Ceramic Machining Parts 95 96 99 99.8 Al2O3 Alumina Ceramic)
Applications of 99 Ceramic Machining Parts 95 96 99 99.8 Al2O3 Alumina Ceramic
99 ceramic machining parts made from 95, 96, 99, and 99.8 Al2O3 alumina ceramic offer crucial functions across industries. These materials use high solidity, warmth resistance, electric insulation, and chemical security. They take care of severe conditions better than many steels or plastics.
In electronic devices, 99.8% alumina ceramic prevails. It makes substratums for circuits, insulators, and semiconductor components. The high pureness ensures very little signal loss. It likewise withstands deterioration from severe chemicals. Reduced qualities like 95% and 96% Al2O3 benefit less requiring components. These consist of real estates for sensors or ports.
Clinical devices counts on 99% alumina ceramic. It is biocompatible and wear-resistant. Surgical tools, oral implants, and joint replacements utilize it. The product stays steady throughout sanitation. It does not react with physical liquids.
Industrial machinery makes use of alumina ceramic parts for longevity. High-purity qualities like 99.8% Al2O3 develop wear-resistant linings, seals, and reducing tools. They decrease rubbing in pumps and shutoffs. Reduced qualities like 95% Al2O3 operate in grinding media or nozzles. These parts last longer than metal options in unpleasant settings.
Automotive and aerospace sectors utilize these ceramics for sensors and engine elements. They manage high temperatures in exhaust systems or turbochargers. Alumina ceramic parts enhance gas efficiency. They decrease wear in relocating parts.
Power industries utilize 99% and 99.8% Al2O3 for insulators in power transmission. They work in solar panels and battery systems. The product withstands electrical leakage. It remains stable in high-voltage atmospheres.
Alumina ceramics adjust to personalized shapes via accuracy machining. They suit components requiring tight resistances. Common types consist of poles, tubes, plates, and complex geometries. The option of pureness depends upon efficiency requirements. Greater qualities set you back even more but perform far better in critical applications. Reduced grades offer price financial savings for basic usages.
These ceramics change conventional products in several areas. They improve efficiency, reduce maintenance, and expand equipment life. Industries prioritize them for requiring environments. Their flexibility makes them important in contemporary production.
Company Introduction
Advanced Ceramics founded on October 17, 2014, is a high-tech enterprise committed to the research and development, production, processing, sales and technical services of ceramic relative materials and products.. Since its establishment in 2014, the company has been committed to providing customers with the best products and services, and has become a leader in the industry through continuous technological innovation and strict quality management.
Our products includes but not limited to Silicon carbide ceramic products, Boron Carbide Ceramic Products, Boron Nitride Ceramic Products, Silicon Carbide Ceramic Products, Silicon Nitride Ceramic Products, Zirconium Dioxide Ceramic Products, Quartz Products, etc. Please feel free to contact us.(nanotrun@yahoo.com)
Payment Methods
T/T, Western Union, Paypal, Credit Card etc.
Shipment Methods
By air, by sea, by express, as customers request.
5 FAQs of 99 Ceramic Machining Parts 95 96 99 99.8 Al2O3 Alumina Ceramic
What are 99 Ceramic Machining Parts made from? These parts use Al2O3 alumina ceramic. The numbers 95, 96, 99, and 99.8 show the percentage of alumina in the material. Higher numbers mean more alumina. More alumina improves strength, heat resistance, and insulation.
Where are these ceramic parts commonly used? They work in electronics, machinery, and medical devices. They handle high temperatures, wear, and corrosion. Examples include insulating components, cutting tools, and lab equipment.
Why choose alumina ceramic over metal or plastic? Alumina resists heat better than metal. It stays stable up to 1600°C. It lasts longer in abrasive environments. It does not rust or react with chemicals. It insulates electricity, unlike metals.
Can these parts be customized? Yes. CNC machines shape alumina into precise sizes and designs. Complex geometries are possible. Holes, threads, and tight tolerances are achievable. Custom parts match specific project needs.
How do grades 95, 96, 99, and 99.8 differ? Higher grades have more alumina. 99.8% alumina offers the best performance. It is harder and handles higher temperatures. Lower grades like 95% or 96% cost less. They suit less demanding applications. The right grade depends on your budget and performance needs.
(99 Ceramic Machining Parts 95 96 99 99.8 Al2O3 Alumina Ceramic)
REQUEST A QUOTE
RELATED PRODUCTS
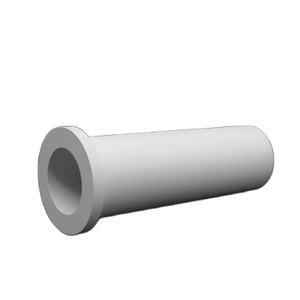
Extruded Pressed Cellular Alumina Honeycomb Ceramic Porous Ceramic
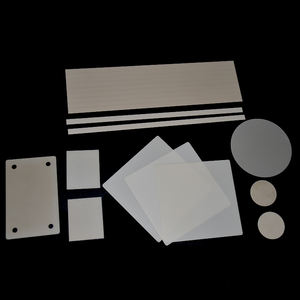
Alumina Ceramic Substrate High Temperature And Wear Resistance Ceramic Substrate Customized Alumina Ceramic Substrate Parts
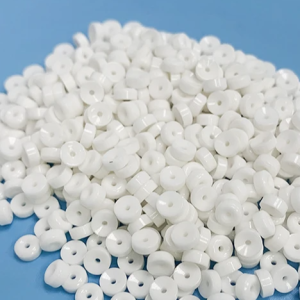
Long Service Life Materials Made of Ceramics 95 99 Al2o3 Insulator Alumina Ceramic Ring
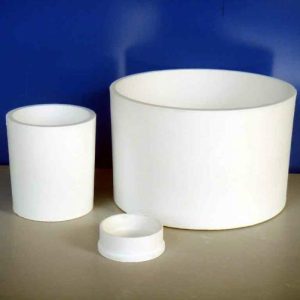
Al2O3 Ceramic HIgh Temperature Thermal Alumina Ceramic Crucible For Sale
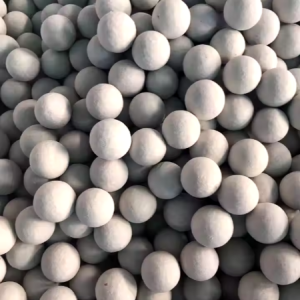
Al2O3 Ceramic 6mm,20mm Inert Alumina Ceramic Ball as Catalyst Support Media Ceramic Ball
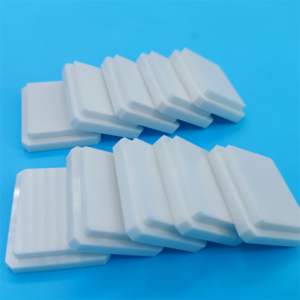