Discover Premium Ceramic Products | Durability & Elegance United | Advanced Ceramics
PRODUCT PARAMETERS
Description
Introduction to Alumina Ceramics
Alumina ceramics are known for their high hardness, wear resistance, corrosion resistance, good electrical insulation and high temperature stability. According to the different alumina content, it can be divided into different grades, such as 95 porcelain, 99 porcelain, etc., among which 99 porcelain refers to ceramic materials with an alumina content of 99%. As the alumina content increases, its mechanical strength and electrical insulation properties will also increase accordingly.
Characteristics of Alumina Ceramics
High Hardness: Alumina ceramics have extremely high hardness, which makes it very wear-resistant and suitable for manufacturing abrasive tools and parts that require wear resistance.
Wear resistance: Due to its high hardness, alumina ceramics show excellent wear resistance and are suitable for manufacturing parts for long-term use.
Corrosion resistance: Alumina ceramics have good resistance to most acids and alkalis, making them widely used in the chemical industry.
Good electrical insulation: As an excellent electrical insulating material, alumina ceramics are widely used in electronic and electrical products.
High temperature stability: Ability to withstand extremely high temperatures without significant physical or chemical changes, which makes it an ideal choice for applications in high temperature environments.
Biocompatibility: In the medical field, certain grades of alumina ceramics are used to make medical devices such as artificial joints due to their good biocompatibility.
(Advanced Molding Ceramics Custom High Temperature Alumina Zirconia Ceramic SIC Ceramics Structural Parts)
Specifications of Advanced Molding Ceramics Custom High Temperature Alumina Zirconia Ceramic SIC Ceramics Structural Parts
Advanced Molding Ceramics offers custom-made high-temperature alumina, zirconia, and silicon carbide (SIC) ceramic architectural components crafted for extreme conditions. These products deal with intense warm, hefty wear, and rough chemical settings. They match markets such as aerospace, automotive, energy, and electronics where efficiency matters.
Alumina ceramics operate accurately approximately 1700 ° C. They resist rust, wear, and electric currents. Their high hardness and stamina make them ideal for insulators, cutting tools, and heating system elements. Alumina parts remain stable in shape and dimension under thermal stress and anxiety, making certain long-term precision.
Zirconia ceramics withstand temperature levels approximately 2400 ° C. They use phenomenal toughness and reduced thermal conductivity. These residential properties function well in thermal obstacles, engine components, and medical implants. Zirconia stands up to fractures under fast temperature level shifts, excellent for high-stress applications.
SIC porcelains excel in temperature levels over 1600 ° C. They integrate high thermal conductivity with reduced thermal development. This balance works for warmth exchangers, burner nozzles, and semiconductor tools. SIC withstands oxidation and chemical assault, keeping efficiency in aggressive setups.
All ceramics are personalized in shape, dimension, and surface finish. Precision machining makes certain tight tolerances for complicated geometries. Components go through rigorous top quality checks to satisfy industry standards. They integrate smoothly right into existing systems, minimizing downtime.
These ceramics replace metals and plastics in high-heat situations. They last longer, reduce upkeep, and improve performance. Their lightweight nature cuts power usage in moving components. Electrical insulation homes stop brief circuits in digital gadgets.
Applications consist of wind turbine blades, securing rings, sensing units, and laser components. They deal with rough bits, harsh gases, and extreme stress without weakening. Advanced molding methods permit automation or small batches, depending upon needs.
Product homes like thickness, porosity, and hardness are customized for certain uses. Information sheets supply exact metrics for engineers to match components to functional needs. Checking includes thermal biking, lots resistance, and chemical exposure simulations.
Advanced Molding Ceramics functions closely with clients to fine-tune layouts and material options. Prototyping solutions confirm efficiency before full-scale production. Rapid turn-around times fulfill urgent job deadlines without sacrificing quality.
(Advanced Molding Ceramics Custom High Temperature Alumina Zirconia Ceramic SIC Ceramics Structural Parts)
Applications of Advanced Molding Ceramics Custom High Temperature Alumina Zirconia Ceramic SIC Ceramics Structural Parts
Advanced molding porcelains are made use of in many markets due to the fact that they handle high heat and wear. Customized high-temperature alumina porcelains function well in severe conditions. They stand up to corrosion and maintain their shape under stress. These parts prevail in aerospace for engine parts. They are also used in semiconductor manufacturing for wafer handling. The electronic devices industry uses alumina for shielding components in high-power gadgets.
Zirconia ceramics are strong and flexible. They manage thermal shock much better than several materials. Clinical devices like surgical blades typically utilize zirconia because it remains sharp. Oral implants benefit from its biocompatibility. Industrial pumps and valves utilize zirconia seals to last longer. The auto sector uses zirconia in sensing units for exhaust systems.
Silicon carbide (SiC) porcelains deal with extremely heats and chemical direct exposure. They are optimal for heater parts in steel handling. SiC is made use of in warmth exchangers for energy plants. It improves efficiency in systems needing quick warm transfer. The product’s firmness makes it suitable for unpleasant environments. Mining tools utilizes SiC for parts subjected to heavy wear.
Custom-made ceramic architectural parts are made to fit specific needs. Accuracy molding makes certain tight resistances for intricate shapes. High-purity products decrease contamination in delicate applications. These porcelains are chosen for their security over long periods. They change steels in areas where weight or warm is a trouble. Suppliers depend on them for dependability in rough settings.
Each type of ceramic offers one-of-a-kind duties based upon its homes. Alumina focuses on electrical insulation and warmth resistance. Zirconia offers strength and sturdiness under mechanical tension. SiC excels in thermal monitoring and chemical stability. Industries choose the product that matches their operational needs. The ideal ceramic component improves performance and decreases downtime.
Company Introduction
Advanced Ceramics founded on October 17, 2014, is a high-tech enterprise committed to the research and development, production, processing, sales and technical services of ceramic relative materials and products.. Since its establishment in 2014, the company has been committed to providing customers with the best products and services, and has become a leader in the industry through continuous technological innovation and strict quality management.
Our products includes but not limited to Silicon carbide ceramic products, Boron Carbide Ceramic Products, Boron Nitride Ceramic Products, Silicon Carbide Ceramic Products, Silicon Nitride Ceramic Products, Zirconium Dioxide Ceramic Products, Quartz Products, etc. Please feel free to contact us.(nanotrun@yahoo.com)
Payment Methods
T/T, Western Union, Paypal, Credit Card etc.
Shipment Methods
By air, by sea, by express, as customers request.
5 FAQs of Advanced Molding Ceramics Custom High Temperature Alumina Zirconia Ceramic SIC Ceramics Structural Parts
What materials are in advanced molding ceramics?
The main materials are alumina, zirconia, and silicon carbide (SIC). These ceramics are picked for strength, heat resistance, and durability. Alumina handles high wear. Zirconia resists cracks under stress. SIC works in extreme temperatures.
How hot can these ceramics get without breaking?
Alumina works up to 1600°C. Zirconia handles 2400°C short-term. SIC manages 1650°C long-term. The exact limit depends on part design and use. Thermal shock resistance varies by material. Testing specific conditions is best.
Can these parts be made in custom shapes?
Yes. Advanced molding methods allow complex designs. Injection molding, dry pressing, and CNC machining create precise shapes. Custom tooling is needed for unique geometries. Prototyping checks fit and function before full production.
What industries use these ceramics?
Aerospace uses them for engine parts. Energy sectors apply them in turbines and reactors. Electronics rely on them for insulating components. Industrial equipment needs them for high-wear zones. Medical devices use zirconia for biocompatibility.
How do I keep these ceramic parts working well?
Avoid sudden temperature changes to prevent cracks. Clean surfaces with non-abrasive methods. Check for wear or damage regularly. Replace parts showing cracks or erosion. Follow maker guidelines for specific care steps.
(Advanced Molding Ceramics Custom High Temperature Alumina Zirconia Ceramic SIC Ceramics Structural Parts)
REQUEST A QUOTE
RELATED PRODUCTS
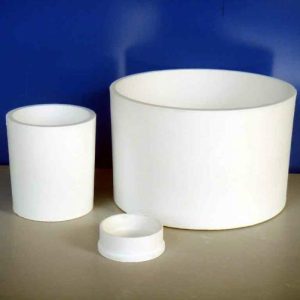
Al2O3 Ceramic HIgh Temperature Thermal Alumina Ceramic Crucible For Sale
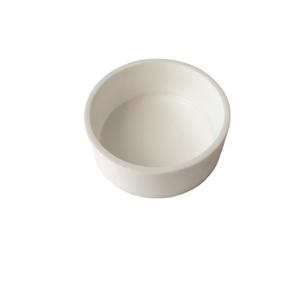
High-quality 99.7% Al2o3 Alumina Ceramic Products
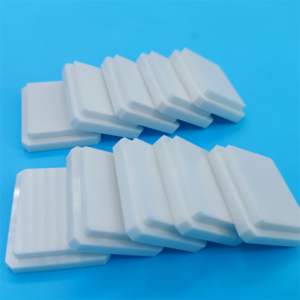
Precision Ceramic Tubes High Temperature Resistant High Hardness 99% Alumina Ceramic Parts
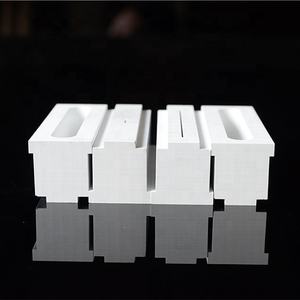
Customized Top Quality Wear Resistant Corrosion Resistant Alumina Zirconia Ceramic Industry Parts
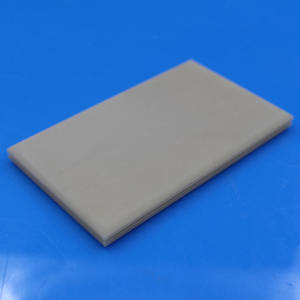
Al2o3 Crucible Alumina Ceramic High Refractoriness Alumina Al2O3 Ceramic Crucible
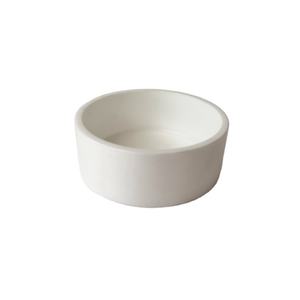