Discover Premium Ceramic Products | Durability & Elegance United | Advanced Ceramics
PRODUCT PARAMETERS
Description
Introduction to Alumina Ceramics
Alumina ceramics are known for their high hardness, wear resistance, corrosion resistance, good electrical insulation and high temperature stability. According to the different alumina content, it can be divided into different grades, such as 95 porcelain, 99 porcelain, etc., among which 99 porcelain refers to ceramic materials with an alumina content of 99%. As the alumina content increases, its mechanical strength and electrical insulation properties will also increase accordingly.
Characteristics of Alumina Ceramics
High Hardness: Alumina ceramics have extremely high hardness, which makes it very wear-resistant and suitable for manufacturing abrasive tools and parts that require wear resistance.
Wear resistance: Due to its high hardness, alumina ceramics show excellent wear resistance and are suitable for manufacturing parts for long-term use.
Corrosion resistance: Alumina ceramics have good resistance to most acids and alkalis, making them widely used in the chemical industry.
Good electrical insulation: As an excellent electrical insulating material, alumina ceramics are widely used in electronic and electrical products.
High temperature stability: Ability to withstand extremely high temperatures without significant physical or chemical changes, which makes it an ideal choice for applications in high temperature environments.
Biocompatibility: In the medical field, certain grades of alumina ceramics are used to make medical devices such as artificial joints due to their good biocompatibility.
(Customized High Precision Alumina Ceramic Tube)
Specifications of Customized High Precision Alumina Ceramic Tube
Personalized High Precision Alumina Porcelain Tubes are engineered for industrial applications needing sturdiness, thermal stability, and electrical insulation. The product composition is high-purity alumina (Al ₂ O FIVE), commonly varying from 95% to 99.5%. This guarantees exceptional mechanical stamina and resistance to wear, deterioration, and extreme temperatures. Televisions run reliably in settings approximately 1600 ° C, maintaining architectural integrity under thermal stress.
Dimensions are customized to meet specific task requirements. External diameters range from 1 mm to 200 mm, with sizes adjustable in between 10 mm and 1000 mm. Wall thickness differs from 0.5 mm to 20 mm, maximized for stabilizing strength and weight. Tolerances are tightly managed, attaining ± 0.1% on sizes and ± 0.2 mm on lengths. Surface surfaces are adjustable, consisting of polished, ground, or as-sintered choices, relying on application needs.
Electrical insulation homes are exceptional, with a dielectric toughness surpassing 15 kV/mm. This makes televisions appropriate for high-voltage applications. Thermal conductivity is modest, around 30 W/m · K, ensuring efficient heat dissipation without compromising thermal shock resistance. Chemical inertness allows usage in hostile environments, withstanding acids, antacid, and molten metals.
Mechanical efficiency includes a solidity of 9 on the Mohs scale, similar to sapphire. Flexural toughness goes beyond 300 MPa, with compressive stamina over 2000 MPa. These residential properties make certain longevity in high-stress applications like semiconductor processing, laser systems, and aerospace elements. Customization includes intricate geometries, consisting of conical ends, flanges, or inner channels.
Applications span multiple industries. In electronic devices, televisions function as insulators for burner or thermocouple protection. Medical devices uses them for their biocompatibility and accuracy in medical devices. Industrial heating systems rely on their thermal stability for thermocouple sheaths or radiant tubes. Automotive and energy markets use them in sensors and fuel cell parts.
Examining and quality control follow global requirements. Each batch undertakes extensive look for dimensional accuracy, thickness, and flaw discovery. X-ray and ultrasonic testing make sure interior uniformity. Custom orders consist of thorough documents, such as material certificates and examination reports. Packaging is made to prevent damages during transportation, using shock-absorbent products for vulnerable arrangements.
(Customized High Precision Alumina Ceramic Tube)
Applications of Customized High Precision Alumina Ceramic Tube
Custom-made high accuracy alumina ceramic tubes are widely utilized in numerous markets. These tubes master high-temperature environments. They withstand rust. They use solid electrical insulation. Their mechanical toughness is trusted. This makes them suitable for specialized applications.
Semiconductor manufacturing counts on these tubes. They handle severe heat during procedures. They safeguard delicate components. Their security ensures constant efficiency. They avoid contamination in cleanrooms. This is important for creating integrated circuits.
Medical equipment gain from alumina ceramic tubes. They are biocompatible. They endure duplicated sanitation. They are used in imaging tools. They act as insulators in surgical tools. Their precision makes certain precision in clinical treatments.
Aerospace applications utilize these tubes for sensing units and instrumentation. They withstand harsh conditions. They offer thermal insulation in engines. Their light-weight nature decreases total system weight. This assists boost fuel effectiveness.
Power sectors employ alumina ceramic tubes in photovoltaic panels and nuclear reactors. They manage high thermal stress. They shield electrical systems. Their toughness expands tools life expectancy. They are crucial in renewable resource innovations.
Industrial machinery uses these tubes for wear-resistant components. They decrease downtime in high-friction environments. They are located in pumps and valves. Their chemical resistance protects against degradation. This preserves operational performance.
Laboratory devices includes alumina ceramic tubes for precise experiments. They manage corrosive compounds. They keep honesty under quick temperature adjustments. Their dimensional precision sustains trustworthy information collection.
Customized layouts meet specific requirements. Tubes are tailored in shapes and size. Surface surfaces are changed for different uses. This adaptability addresses one-of-a-kind industrial difficulties. Makers function carefully with customers to provide optimum solutions.
The product’s residential or commercial properties ensure long-term efficiency. Alumina ceramic tubes decrease upkeep needs. They reduce replacement prices. Their adaptability makes them a functional option throughout fields.
Company Introduction
Advanced Ceramics founded on October 17, 2014, is a high-tech enterprise committed to the research and development, production, processing, sales and technical services of ceramic relative materials and products.. Since its establishment in 2014, the company has been committed to providing customers with the best products and services, and has become a leader in the industry through continuous technological innovation and strict quality management.
Our products includes but not limited to Silicon carbide ceramic products, Boron Carbide Ceramic Products, Boron Nitride Ceramic Products, Silicon Carbide Ceramic Products, Silicon Nitride Ceramic Products, Zirconium Dioxide Ceramic Products, Quartz Products, etc. Please feel free to contact us.(nanotrun@yahoo.com)
Payment Methods
T/T, Western Union, Paypal, Credit Card etc.
Shipment Methods
By air, by sea, by express, as customers request.
5 FAQs of Customized High Precision Alumina Ceramic Tube
What is a high precision alumina ceramic tube? High precision alumina ceramic tubes are advanced components made from aluminum oxide. They are known for high hardness, wear resistance, and stability in extreme environments. These tubes are manufactured using specialized processes to meet tight dimensional tolerances. They are used in industries requiring reliable performance under stress, heat, or chemical exposure.
Why choose customized alumina ceramic tubes over standard sizes? Standard sizes may not fit specific applications. Customized tubes are tailored to exact measurements, shapes, or surface finishes. This ensures compatibility with unique machinery or processes. Industries like aerospace, medical devices, or semiconductor manufacturing often require bespoke solutions. Customization avoids compromises in performance or design efficiency.
What applications use high precision alumina ceramic tubes? These tubes are common in semiconductor processing equipment, where they handle high temperatures and corrosive gases. They are used in thermocouple protection, laser systems, and laboratory instruments. Automotive sensors and medical devices also rely on them for insulation or structural support. Their durability makes them suitable for harsh industrial environments.
How temperature-resistant are alumina ceramic tubes? Alumina ceramic tubes withstand temperatures up to 1800°C. They maintain structural integrity under rapid thermal cycling. This makes them ideal for furnaces, kilns, or high-heat manufacturing processes. Their low thermal expansion reduces cracking risk. They outperform metals or plastics in extreme heat applications.
How is precision ensured in customized alumina ceramic tubes? Precision is achieved through advanced molding, sintering, and machining techniques. Computer-controlled tools guarantee accurate dimensions. Quality checks include laser measurement and microscopy. Material purity and density are tested to meet industry standards. Manufacturers work closely with clients to verify specifications at every production stage.
(Customized High Precision Alumina Ceramic Tube)
REQUEST A QUOTE
RELATED PRODUCTS
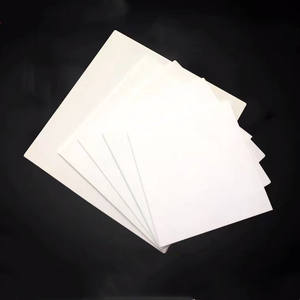
99 Ceramic Machining Parts 95 96 99 99.8 Al2O3 Alumina Ceramic
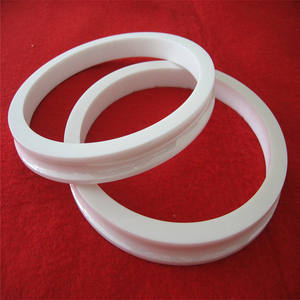
Customized Precision Industrial Ceramic Structural Parts Insulation High Temperature Resistant 99.7% Alumina Ceramic Base
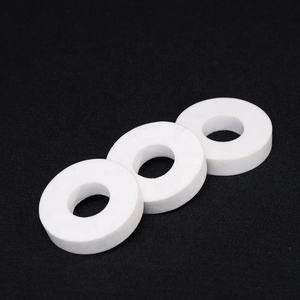
Excellent Performance Alumina Ceramic China Factory Customized Size Refractory
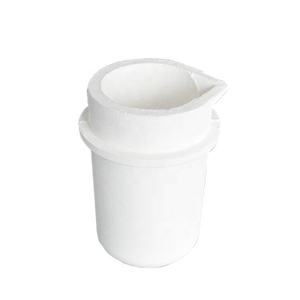
Polished High Purity 99% Alumina Ceramic Stirring Rods
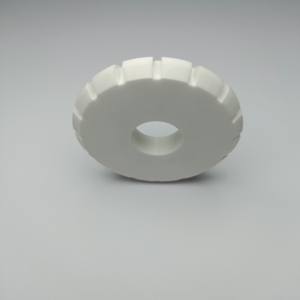
Made In China Industrial Heater Insulators Alumina/Zirconia Ceramic Ring/Tube/Rod/Plate Thread Part
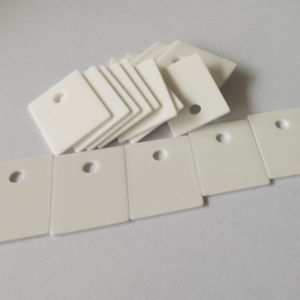