Discover Premium Ceramic Products | Durability & Elegance United | Advanced Ceramics
PRODUCT PARAMETERS
Description
Introduction to Alumina Ceramics
Alumina ceramics are known for their high hardness, wear resistance, corrosion resistance, good electrical insulation and high temperature stability. According to the different alumina content, it can be divided into different grades, such as 95 porcelain, 99 porcelain, etc., among which 99 porcelain refers to ceramic materials with an alumina content of 99%. As the alumina content increases, its mechanical strength and electrical insulation properties will also increase accordingly.
Characteristics of Alumina Ceramics
High Hardness: Alumina ceramics have extremely high hardness, which makes it very wear-resistant and suitable for manufacturing abrasive tools and parts that require wear resistance.
Wear resistance: Due to its high hardness, alumina ceramics show excellent wear resistance and are suitable for manufacturing parts for long-term use.
Corrosion resistance: Alumina ceramics have good resistance to most acids and alkalis, making them widely used in the chemical industry.
Good electrical insulation: As an excellent electrical insulating material, alumina ceramics are widely used in electronic and electrical products.
High temperature stability: Ability to withstand extremely high temperatures without significant physical or chemical changes, which makes it an ideal choice for applications in high temperature environments.
Biocompatibility: In the medical field, certain grades of alumina ceramics are used to make medical devices such as artificial joints due to their good biocompatibility.
(Manufacturing Dry Pressing Moulding 99% Al2O3 Alumina Ceramic Block Plate)
Specifications of Manufacturing Dry Pressing Moulding 99% Al2O3 Alumina Ceramic Block Plate
This item is made using dry pushing molding modern technology. The key material is 99% aluminum oxide (Al2O3). The alumina material makes sure high pureness. The procedure includes condensing ceramic powder under high stress. This produces a thick, uniform framework. The finished ceramic block plate has superb mechanical stamina. It stands up to wear, rust, and heats. The density varies in between 3.8 and 3.9 g/cm SIX. The firmness reaches Mohs 9. This makes it suitable for abrasive atmospheres. The flexural stamina goes beyond 300 MPa. The compressive toughness is above 2500 MPa. These buildings guarantee long-lasting toughness.
The item operates successfully in temperature levels approximately 1600 ° C. It maintains security under thermal biking. The reduced thermal growth coefficient protects against splitting. The dielectric stamina mores than 15 kV/mm. This makes it excellent for electric insulation. The surface area finish is smooth. Regular roughness (Ra) is below 0.4 μm. Custom dimensions and densities are readily available. Requirement dimensions consist of sizes from 50 to 500 mm. Widths variety from 50 to 300 mm. Density alternatives span 5 to 50 mm. Tolerances are securely managed. Dimensional precision is within ± 0.5%.
The manufacturing process guarantees minimal porosity. This improves resistance to chemical assault. The material does not respond with acids or alkalis. It carries out well in extreme industrial setups. Applications consist of heating system cellular linings, wear-resistant parts, and electronic substrates. The product meets industry requirements for alumina ceramics. Quality checks include X-ray fluorescence for make-up. Density and firmness examinations verify performance. Each set undergoes rigorous assessment.
Personalized forms or holes can be added. Machining post-sintering attains exact geometries. The item is compatible with grinding and splashing. Packaging makes use of anti-impact materials. This stops damage throughout transportation. Storage space requires a completely dry atmosphere. Moisture exposure need to be avoided. Taking care of ought to comply with conventional ceramic safety methods.
(Manufacturing Dry Pressing Moulding 99% Al2O3 Alumina Ceramic Block Plate)
Applications of Manufacturing Dry Pressing Moulding 99% Al2O3 Alumina Ceramic Block Plate
Production completely dry pushing moulding 99% Al2O3 alumina ceramic block plates involves forming high-purity alumina powder under high pressure. This technique guarantees dense, consistent frameworks. The result is a ceramic item with phenomenal hardness, put on resistance, and thermal security. These homes make it appropriate for requiring commercial applications.
In electronic devices, 99% alumina ceramic plates work as shielding substratums. They sustain circuits in high-frequency gadgets. The product’s reduced electrical conductivity prevents power loss. It additionally endures heats during procedure. This dependability is vital for components like semiconductor places.
Industrial machinery benefits from alumina ceramic’s wear resistance. The blocks are used in pump seals, valve seats, and reducing devices. They minimize rubbing and prolong tools life. Rough atmospheres with rough products create very little damages. Maintenance prices drop as replacement frequency decreases.
Clinical tools makes use of these porcelains for their biocompatibility. They form components of medical devices and implants. Sterilization processes need materials that tolerate repeated high warmth. Alumina ceramic maintains structural integrity under such conditions. It withstands chemical reactions with physical liquids.
Chemical handling markets rely on alumina ceramic plates for rust resistance. Activators and piping systems take care of hostile acids and antacids. The product’s inert nature stops contamination. It guarantees lasting performance in harsh settings.
High-temperature applications include heater linings and thermocouple tubes. Alumina ceramic blocks withstand thermal shocks. Quick heating or air conditioning does not cause breaking. This stability sustains constant operation in metal handling or glass production.
The vehicle market makes use of alumina ceramic in sensing units and ignition systems. Engine parts deal with severe heat and vibration. The material’s resilience ensures exact readings and reliable ignition. It adds to enhanced automobile effectiveness.
99% Al2O3 alumina ceramic block plates adjust to customized sizes and shapes. Precision moulding allows limited tolerances. Industries worth this flexibility for specialized tools. The mix of efficiency and versatility drives prevalent fostering.
Company Introduction
Advanced Ceramics founded on October 17, 2014, is a high-tech enterprise committed to the research and development, production, processing, sales and technical services of ceramic relative materials and products.. Since its establishment in 2014, the company has been committed to providing customers with the best products and services, and has become a leader in the industry through continuous technological innovation and strict quality management.
Our products includes but not limited to Silicon carbide ceramic products, Boron Carbide Ceramic Products, Boron Nitride Ceramic Products, Silicon Carbide Ceramic Products, Silicon Nitride Ceramic Products, Zirconium Dioxide Ceramic Products, Quartz Products, etc. Please feel free to contact us.(nanotrun@yahoo.com)
Payment Methods
T/T, Western Union, Paypal, Credit Card etc.
Shipment Methods
By air, by sea, by express, as customers request.
5 FAQs of Manufacturing Dry Pressing Moulding 99% Al2O3 Alumina Ceramic Block Plate
What is the alumina content in these ceramic blocks? The alumina content is 99%. This high percentage makes the blocks extremely hard and durable. They resist wear and corrosion better than lower-grade ceramics. This makes them suitable for harsh environments like heavy machinery or high-temperature setups.
What applications are these blocks used for? They are commonly used in industrial settings. Examples include wear-resistant linings, electrical insulators, and high-temperature furnace parts. Their strength and thermal stability make them ideal for machinery components exposed to stress or heat. They also work in chemical processing equipment due to their corrosion resistance.
How does dry pressing moulding improve quality? Dry pressing uses high pressure to compact ceramic powder into precise shapes. This method reduces air pockets and uneven density. The result is a uniform, dense product with consistent performance. It also allows tight control over dimensions, minimizing the need for post-production machining.
Can these blocks handle extreme temperatures? Yes. They withstand temperatures up to 1600°C. Their low thermal expansion prevents cracking under rapid temperature changes. This makes them reliable for applications like kiln furniture or thermal barriers. They maintain structural integrity even during prolonged heat exposure.
Are custom sizes and shapes available? Yes. Manufacturers offer customization based on technical drawings or samples. Production molds can be adjusted to create specific dimensions or surface textures. Lead times vary depending on design complexity. Custom orders typically require minimum quantities to ensure cost efficiency.
What makes these blocks better than metal alternatives? They outperform metals in high-wear and high-temperature scenarios. Metals may deform or corrode under stress or heat. Alumina ceramics stay stable, reducing replacement frequency. They are also lighter, lowering energy costs in moving parts. Their electrical insulation properties add value in electronic or power systems.
Do they require special handling during installation? Avoid impact during installation. While highly durable, sudden force can cause chipping. Use tools compatible with ceramic materials to prevent surface damage. Follow manufacturer guidelines for fitting and fastening. Proper installation ensures long-term performance without premature failure.
How long do these blocks last compared to other materials? Lifespan depends on application conditions. In abrasive environments, they last 3-5 times longer than steel or plastic. Their resistance to chemical erosion further extends service life. Regular inspections help identify wear patterns, allowing timely replacements before critical failure.
(Manufacturing Dry Pressing Moulding 99% Al2O3 Alumina Ceramic Block Plate)
REQUEST A QUOTE
RELATED PRODUCTS
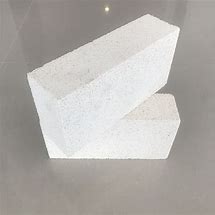
Al2O3 Ceramic Hot Selling Refractory Alumina Brick Kiln Rotary Kiln Building Making Clay Brick For Oven
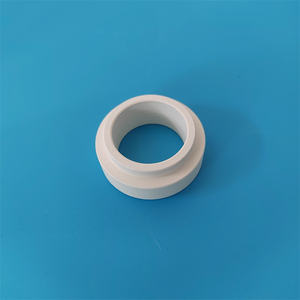
Al2o3 Crucible Alumina Ceramic High Refractoriness Alumina Al2O3 Ceramic Crucible
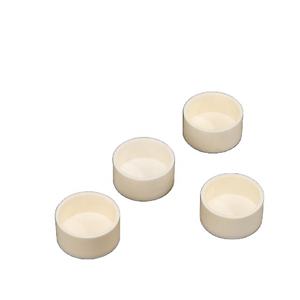
Corrosion Resistance Insulating Al2O3 Alumina Ceramic Plunger Shaft Ceramic Rod Zirconia Ceramic Pipe

Processing Custom Textile Ceramic Fitting Al2O3 High Precision Insulating Alumina Ceramic Parts
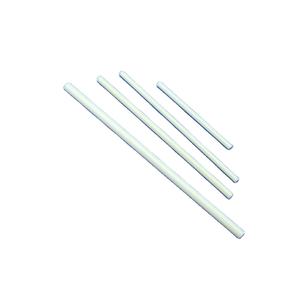
Al2o3 High Precision 95 99 Ceramic Plate Wear Resistant Alumina Ceramic Plate
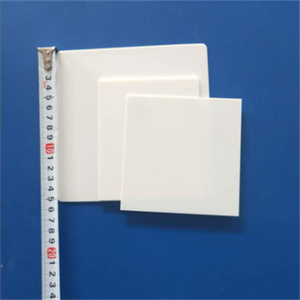