Discover Premium Ceramic Products | Durability & Elegance United | Advanced Ceramics
PRODUCT PARAMETERS
Description
Introduction of Boron Carbide Ceramics
Boron carbide ceramics is an inorganic, non-metallic material with carbon and boron as its main components, and its chemical formula is B4C. Since its discovery in the early 20th century, this material has attracted a great deal of attention because of its unique physical and chemical properties. Boron carbide ceramics have an extremely high hardness, second only to diamond and cubic boron nitride, which makes it important in the field of wear-resistant materials. It also exhibits excellent corrosion resistance, high-temperature stability and low-density properties, attributes that make it ideal for the manufacture of bullet-proof vests, nozzles, bearings and other mechanical components that require high wear resistance. Boron carbide ceramics can also be prepared in a variety of shapes and sizes through different processes to meet the needs of different industries.
Characteristics of Boron Carbide Ceramics
Boron carbide ceramics are known for their excellent performance characteristics, starting with their ultra-high hardness and strength, which makes them resistant to severe abrasion and scratching, making them ideal for use in cutting tools and abrasives. Secondly, the material possesses excellent chemical stability and is less likely to react with chemicals such as acids and alkalis, even in extreme environments, making it widely used in certain key components in the chemical industry. In addition, the superior thermal stability of boron carbide ceramics and their ability to maintain structural and property stability at extremely high temperatures makes them one of the key materials in the aerospace and nuclear industries. Finally, it is worth mentioning its lightweight properties, which, due to its low density, make boron carbide ceramics an ideal option for application scenarios that require light weight but high strength. Together, these characteristics give boron carbide ceramics a wide range of applications.
(Boron Carbide Ceramic Wet Sandblasting Blasting Nozzle)
Specification of Boron Carbide Ceramic Wet Sandblasting Blasting Nozzle
Boron carbide ceramic wet sandblasting nozzles are built for high-performance unpleasant applications. The material is boron carbide (B4C), recognized for extreme firmness and wear resistance. It rates 3rd on the Mohs scale, behind just ruby and cubic boron nitride. This makes it excellent for taking care of unpleasant media like silicon carbide, aluminum oxide, and glass grains. The nozzles stand up to constant usage in damp blasting settings, where water blends with abrasives to minimize dust and warm.
The design focuses on longevity. Boron carbide resists disintegration far better than tungsten carbide or alumina nozzles. It lasts approximately 10 times much longer in rough conditions. The internal bore keeps a smooth surface area over time, ensuring constant fragment speed and blasting accuracy. This decreases downtime for nozzle substitutes and boosts workflow efficiency.
These nozzles operate successfully under pressures varying from 50 to 150 psi. They manage temperature levels as much as 400 ° C without cracking or contortion. The chemical stability of boron carbide avoids corrosion from acidic or alkaline services frequently utilized in damp blowing up setups.
Compatibility is broad. The nozzles fit typical wet blasting equipment throughout industries like aerospace, automobile, and metal construction. They help surface cleansing, deburring, and finishing prep work. The portable, light-weight style reduces driver fatigue throughout prolonged usage.
Upkeep is simple. Routine cleaning with water prevents rough buildup. Evaluating the bore for wear guarantees constant efficiency. While the preliminary price is more than basic nozzles, the prolonged lifespan reduces long-term costs.
Security features consist of lowered dirt exposure and quieter procedure contrasted to completely dry blowing up. The product’s non-conductive residential properties make it safe for electric components. Boron carbide nozzles satisfy industrial requirements for precision and integrity, making them a functional option for requiring blowing up tasks.
(Boron Carbide Ceramic Wet Sandblasting Blasting Nozzle)
Applications of Boron Carbide Ceramic Wet Sandblasting Blasting Nozzle
Boron carbide ceramic damp sandblasting nozzles are made use of in industries needing high-performance surface area treatment. These nozzles manage tough materials like metal, glass, and rock. They work in damp blasting configurations where water blends with unpleasant media. The water minimizes dirt and warm, making the process more secure. Boron carbide sticks out since it resists use far better than steel or tungsten carbide. This material lasts much longer, cutting downtime and replacement prices.
The nozzles match high-pressure settings. They stay steady under severe conditions. This is crucial for consistent cause tasks like cleaning, etching, or coating. Boron carbide’s firmness protects against erosion from rough bits. This keeps the nozzle’s form precise in time. Accuracy issues for ending up parts in aerospace, auto, or electronics.
Chemical resistance is another benefit. Boron carbide deals with acidic or alkaline services in wet blasting. It prevents deterioration, maintaining efficiency steady. This serves in markets dealing with harsh chemicals, like metal processing or recycling.
Warm resistance matters in constant procedures. The nozzles take care of high temperatures without cracking. They work in automated systems requiring non-stop use. Manufacturing facilities value this for meeting production targets without devices failings.
These nozzles fit several industries. Aerospace utilizes them for smoothing generator blades. Automotive plants rely upon them for cleansing engine components. Electronics manufacturers use them to prepare motherboard. Oil and gas industries use them to deal with pipes. Each situation requires longevity and precision.
Maintenance is simple. Routine look for wear or clogs maintain them efficient. Proper care prolongs their lifespan additionally. Operators save cash by staying clear of constant replacements.
Boron carbide ceramic damp sandblasting nozzles improve performance. They integrate stamina, long life, and integrity. Industries pick them to increase efficiency and cut expenses. Their function in precision surface area treatment makes them important for contemporary production.
Company Introduction
Advanced Ceramics founded on October 17, 2014, is a high-tech enterprise committed to the research and development, production, processing, sales and technical services of ceramic relative materials and products.. Since its establishment in 2014, the company has been committed to providing customers with the best products and services, and has become a leader in the industry through continuous technological innovation and strict quality management.
Our products includes but not limited to Silicon carbide ceramic products, Boron Carbide Ceramic Products, Boron Nitride Ceramic Products, Silicon Carbide Ceramic Products, Silicon Nitride Ceramic Products, Zirconium Dioxide Ceramic Products, Quartz Products, etc. Please feel free to contact us.(nanotrun@yahoo.com)
Payment Methods
T/T, Western Union, Paypal, Credit Card etc.
Shipment Methods
By air, by sea, by express, as customers request.
5 FAQs of Boron Carbide Ceramic Wet Sandblasting Blasting Nozzle
What makes boron carbide ceramic nozzles better than other materials? Boron carbide is one of the hardest materials available. It resists wear better than tungsten carbide, steel, or aluminum oxide. This hardness reduces erosion from abrasive particles. It keeps the nozzle’s shape longer, improving blasting accuracy. Maintenance costs drop due to less frequent replacements.
How long do boron carbide ceramic nozzles typically last? Lifespan depends on usage conditions like pressure and abrasive type. Under similar conditions, boron carbide nozzles last up to 10 times longer than steel nozzles. With regular use, they often operate effectively for hundreds of hours. High-pressure environments or coarse abrasives may shorten this period.
Are boron carbide nozzles suitable for wet sandblasting? Yes. They perform well in wet blasting applications. The material resists corrosion from water and chemicals. It handles the combined impact of water and abrasives without cracking. This makes them ideal for industries like shipbuilding or metal cleaning.
How should I maintain a boron carbide ceramic nozzle? Clean the nozzle after each use to remove abrasive residue. Check for chips or cracks regularly. Store it in a dry place to prevent moisture damage. Avoid dropping or striking the nozzle against hard surfaces. Replace it if the internal bore shows significant wear.
Why are boron carbide nozzles more expensive than other types? The raw material and manufacturing process cost more. Boron carbide is harder to produce than metals or standard ceramics. The higher price balances with longer service life and reduced downtime. Over time, fewer replacements lower total operational costs.
(Boron Carbide Ceramic Wet Sandblasting Blasting Nozzle)
REQUEST A QUOTE
RELATED PRODUCTS
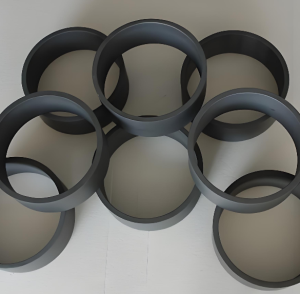
Silicon Carbide Boron Carbide Alumina Ceramic Armor Plate
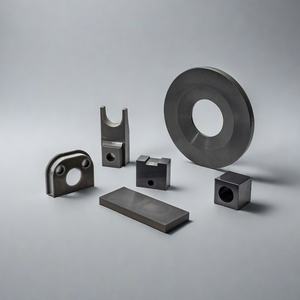
High Temperature Resistance Boron Carbide Sand Tube B4C Ceramic Sandblasting Nozzle

High Purity B4C Boron Carbide Ceramic Grinding Balls
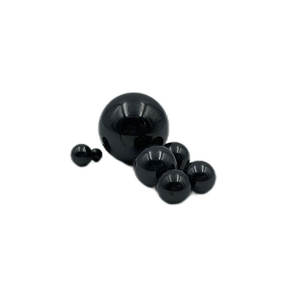
Ultra Hard Boron Carbide Ceramic Hexes
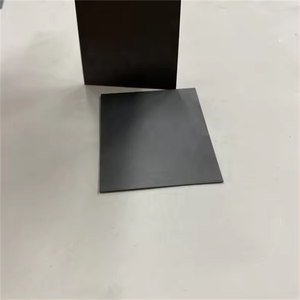
Best Boron Carbide Ceramic Nozzle for Sand Blasting
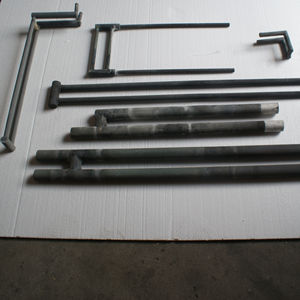