Discover Premium Ceramic Products | Durability & Elegance United | Advanced Ceramics
PRODUCT PARAMETERS
Description
Overview of Boron Nitride Ceramic
Boron Nitride (BN) ceramic is a unique material renowned for its exceptional properties, making it highly valuable in various industrial applications. It exists in multiple forms, primarily hexagonal boron nitride (h-BN), cubic boron nitride (c-BN), and wurtzite boron nitride (w-BN). Hexagonal BN, the most common form, is often compared to graphite due to its lubricious and thermally conductive yet electrically insulating nature. Boron Nitride ceramics are synthesized under high temperatures and pressures, offering a rare combination of properties not found in many other materials.
Features of Boron Nitride Ceramic
Thermal Conductivity: Excellent thermal conductivity, especially in the hexagonal form, allowing efficient heat dissipation.
Electrical Insulation: Outstanding electrical insulation properties make it ideal for electrical applications requiring thermal management.
Chemical Stability: Highly resistant to chemical attacks, including strong acids and bases, ensuring durability in harsh environments.
Thermal Shock Resistance: Superior resistance to thermal shock, enabling it to withstand rapid temperature changes without cracking.
Mechanical Strength: Good mechanical strength at both room and elevated temperatures, although this can vary with the form of BN.
Lubricity: Self-lubricating property due to its layered structure, which reduces friction and wear in moving parts.
Non-Toxic: Safe to use in various settings, including medical and food processing industries, due to its non-toxic nature.
High-Temperature Performance: Maintains stability at extremely high temperatures, exceeding 1000°C in inert atmospheres, making it suitable for refractory applications.
(Advanced Machining Corrosion Resistant Aluminum Nitride Composite Boron Nitride Ceramic Part)
Specification of Advanced Machining Corrosion Resistant Aluminum Nitride Composite Boron Nitride Ceramic Part
The Advanced Machining Corrosion Resistant Aluminum Nitride Compound Boron Nitride Ceramic Component delivers high efficiency in extreme conditions. This item incorporates aluminum nitride and boron nitride, producing a product suitable for requiring industrial applications. It withstands deterioration successfully, also when subjected to rough chemicals or high-temperature settings. The composite framework guarantees security, preventing deterioration over time.
The ceramic part excels in thermal management. It performs warmth efficiently, making it appropriate for applications calling for fast warm dissipation. Its reduced thermal growth price reduces form adjustments under temperature variations. This feature makes certain dependability in systems exposed to repeated heating and cooling cycles.
Electric insulation is one more crucial advantage. The product blocks electrical currents, reducing risks of short circuits or component failure. It does well in high-voltage settings, keeping honesty under electrical stress and anxiety. This makes it a safe option for electronic devices, power transmission, and aerospace systems.
Mechanical strength is focused on in the design. The ceramic part holds up against heavy tons and unpleasant pressures without breaking or using down. Precision machining allows tight resistances, guaranteeing compatibility with complicated settings up. Its sturdiness extends service life, decreasing substitute costs.
Surface area smoothness is optimized to minimize rubbing in moving parts. This reduces power loss and put on in mechanical systems. The product’s non-porous framework stops contamination from dampness, gases, or bits. Tidiness is preserved also in sensitive atmospheres like semiconductor production or medical devices.
The item matches industries such as auto, energy, and chemical handling. It functions in components like warm sinks, insulators, nozzles, and reducing tools. Personalized sizes and shapes are readily available to satisfy particular requirements. Testing confirms consistent quality, with certifications for product safety and performance.
Compatibility with innovative machining techniques allows detailed layouts without jeopardizing architectural integrity. The ceramic component operates reliably in temperatures varying from -200 ° C to 1800 ° C. It stands up to oxidation in air environments, making sure lasting performance. Very little upkeep is needed, lowering downtime in industrial operations.
Ecological resistance covers acids, antacid, and molten steels. The material’s inert nature prevents chain reactions that might weaken efficiency. It meets stringent market standards for thermal, electric, and mechanical residential properties.
(Advanced Machining Corrosion Resistant Aluminum Nitride Composite Boron Nitride Ceramic Part)
Applications of Advanced Machining Corrosion Resistant Aluminum Nitride Composite Boron Nitride Ceramic Part
Advanced machining corrosion-resistant aluminum nitride composite boron nitride ceramic components serve essential roles throughout several industries. These materials integrate high thermal conductivity with strong electrical insulation. They deal with extreme temperature levels and withstand chemical deterioration properly. Industries requiring resilient and trusted elements under rough conditions gain from these residential or commercial properties.
In semiconductor manufacturing, these ceramic parts handle heat in high-power electronic tools. They make certain steady performance by dissipating warmth efficiently. Their electric insulation protects against brief circuits. This makes them excellent for wafer handling tools and substrate materials.
Aerospace applications count on these ceramics for engine components and thermal shields. They withstand intense warmth and mechanical anxiety during flight. Their lightweight nature minimizes fuel intake. Deterioration resistance ensures durability in tough environments.
The energy industry makes use of these components in nuclear reactors and solar energy systems. They supply insulation in high-radiation zones. Thermal stability enables consistent operation in turbines and heat exchangers. Resistance to chemical degradation prolongs element life in hostile settings.
Clinical tools producers make use of these ceramics for imaging tools and surgical devices. Safe buildings and biocompatibility fulfill stringent health requirements. Precision machining makes sure limited resistances for sensitive instruments. Electrical insulation protects against disturbance in diagnostic equipments.
Chemical handling plants use these products in pumps, shutoffs, and reactors. They withstand exposure to corrosive acids and alkalis. Reduced thermal expansion decreases wear during temperature level shifts. This minimizes downtime and maintenance costs.
Automotive engineers integrate these ceramics right into electric lorry battery systems. They handle warm in high-voltage circuits. Electrical insulation improves safety. Durability supports long-term efficiency in demanding driving problems.
These ceramic components adjust to specialized demands through sophisticated machining methods. Personalized sizes and shapes meet specific market requirements. Their adaptability addresses challenges in state-of-the-art and industrial applications.
Company Introduction
Advanced Ceramics founded on October 17, 2014, is a high-tech enterprise committed to the research and development, production, processing, sales and technical services of ceramic relative materials and products.. Since its establishment in 2014, the company has been committed to providing customers with the best products and services, and has become a leader in the industry through continuous technological innovation and strict quality management.
Our products includes but not limited to Silicon carbide ceramic products, Boron Carbide Ceramic Products, Boron Nitride Ceramic Products, Silicon Carbide Ceramic Products, Silicon Nitride Ceramic Products, Zirconium Dioxide Ceramic Products, Quartz Products, etc. Please feel free to contact us.(nanotrun@yahoo.com)
Payment Methods
T/T, Western Union, Paypal, Credit Card etc.
Shipment Methods
By air, by sea, by express, as customers request.
5 FAQs of Advanced Machining Corrosion Resistant Aluminum Nitride Composite Boron Nitride Ceramic Part
What are the main uses of advanced machining corrosion-resistant aluminum nitride composite boron nitride ceramic parts?
These parts work in tough conditions. They handle high heat, chemicals, and wear. Common uses are in aerospace, electronics, and semiconductors. Examples include engine parts, cutting tools, and heat sinks. They suit places needing thermal stability and long-lasting performance.
How does the material handle extreme temperatures?
Aluminum nitride and boron nitride both resist heat. The composite handles up to 1800°C in non-reactive gases. In air, it works up to 1000°C. This makes it good for furnaces, reactors, and high-temperature sensors.
Does it resist corrosion from chemicals?
Yes. The materials are inert. They resist acids, alkalis, and molten metals. Sulfuric acid, sodium hydroxide, and molten aluminum cause little damage. Long exposure to strong acids or bases may slowly wear the surface.
Is machining this material difficult?
Machining needs care. The material is hard but brittle. Diamond tools are required for precision. Speed, pressure, and cooling must stay controlled to avoid cracks. Skilled technicians ensure accuracy.
How does it compare to metals or standard ceramics?
It outperforms metals in heat and corrosion resistance. It beats standard ceramics in thermal conductivity and mechanical strength. It lasts longer under stress, reducing replacements. Industries like electronics and energy prefer it for efficiency.
(Advanced Machining Corrosion Resistant Aluminum Nitride Composite Boron Nitride Ceramic Part)
REQUEST A QUOTE
RELATED PRODUCTS
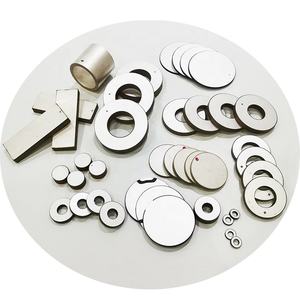
99% Borazon Boron Nitride Ceramic Bushing Bush Sleeve BN Sealing Ring Cubic boron nitride
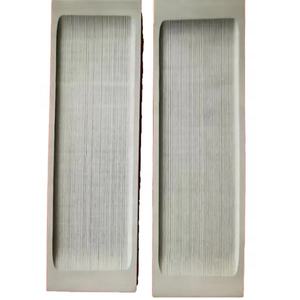
High Purity 99.9% Boron Nitride Ceramic Heater element
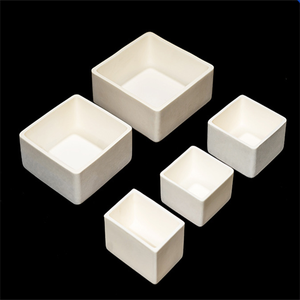
High Purity Boron Nitride (BN) Ceramic Parts Customized Industrial Ceramic Round Block Rod Plunger Bar
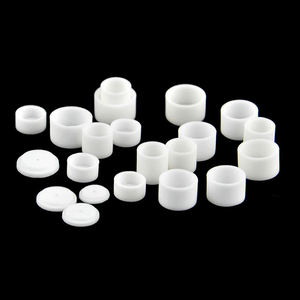
Customized Industrial High Purity High Temperature Boron Nitride Ceramic Tube
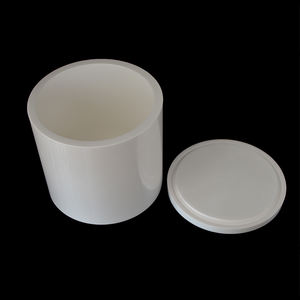
High Quality Boron Nitride Ceramic Boat Evaporation Boats Ceramics Boron Nitride Crucible Boat
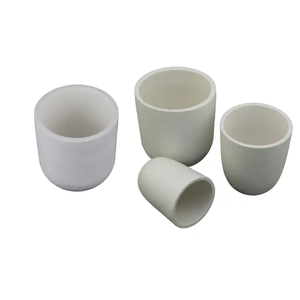