Discover Premium Ceramic Products | Durability & Elegance United | Advanced Ceramics
PRODUCT PARAMETERS
Description
Overview of Boron Nitride Ceramic
Boron Nitride (BN) ceramic is a unique material renowned for its exceptional properties, making it highly valuable in various industrial applications. It exists in multiple forms, primarily hexagonal boron nitride (h-BN), cubic boron nitride (c-BN), and wurtzite boron nitride (w-BN). Hexagonal BN, the most common form, is often compared to graphite due to its lubricious and thermally conductive yet electrically insulating nature. Boron Nitride ceramics are synthesized under high temperatures and pressures, offering a rare combination of properties not found in many other materials.
Features of Boron Nitride Ceramic
Thermal Conductivity: Excellent thermal conductivity, especially in the hexagonal form, allowing efficient heat dissipation.
Electrical Insulation: Outstanding electrical insulation properties make it ideal for electrical applications requiring thermal management.
Chemical Stability: Highly resistant to chemical attacks, including strong acids and bases, ensuring durability in harsh environments.
Thermal Shock Resistance: Superior resistance to thermal shock, enabling it to withstand rapid temperature changes without cracking.
Mechanical Strength: Good mechanical strength at both room and elevated temperatures, although this can vary with the form of BN.
Lubricity: Self-lubricating property due to its layered structure, which reduces friction and wear in moving parts.
Non-Toxic: Safe to use in various settings, including medical and food processing industries, due to its non-toxic nature.
High-Temperature Performance: Maintains stability at extremely high temperatures, exceeding 1000°C in inert atmospheres, making it suitable for refractory applications.
(Boron Nitride+Silicon Nitride Ceramic Break Ring for Horizontal Continuous Casting)
Specification of Boron Nitride+Silicon Nitride Ceramic Break Ring for Horizontal Continuous Casting
The Boron Nitride + Silicon Nitride Porcelain Break Ring is developed for horizontal continuous casting. It manages molten metal circulation in molds. The combination of boron nitride and silicon nitride ensures high efficiency under severe problems. The product structure gives thermal stability, mechanical toughness, and chemical resistance. This makes the break ring suitable for demanding industrial processes.
The break ring runs successfully between 1000 ° C and 1400 ° C. It manages quick temperature adjustments without fracturing. The reduced thermal growth coefficient lowers stress and anxiety throughout heating or cooling. This function extends the product’s lifespan in high-temperature settings.
Mechanical residential or commercial properties consist of a hardness score of Hv 1800-2200. The flexural stamina exceeds 500 MPa. These values guarantee the ring endures mechanical tension throughout spreading. The material withstands wear, disintegration, and deformation even under extended usage.
Standard outer sizes vary from 80 mm to 300 mm. Internal diameters vary between 40 mm and 200 mm. Density choices are 10 mm to 30 mm. Personalized sizes are readily available to satisfy particular tools demands.
The surface area coating is smooth, minimizing rubbing with molten metal. This prevents sticking and guarantees consistent steel circulation. The non-wetting home of boron nitride lowers adhesion of liquified alloys. This keeps tidy operation and lowers downtime for maintenance.
Applications consist of steel, copper, and aluminum casting. The break ring works with non-ferrous and ferrous steels. It does reliably in high-speed casting lines. The product is utilized in industries such as auto, aerospace, and building.
The break ring is chemically inert. It does not respond with liquified metals or slags. This avoids contamination of the end product. The material’s resistance to oxidation ensures stability in oxygen-rich environments.
Installment is simple as a result of specific dimensional resistances. The ring fits firmly into casting mold and mildews. It calls for marginal adjustments throughout configuration. Operators gain from minimized setup time and boosted procedure performance.
The Boron Nitride + Silicon Nitride Ceramic Break Ring deals longevity and accuracy. It satisfies the demands of contemporary continuous spreading operations. Customers experience fewer disruptions and higher-quality result. The item is a trusted option for keeping efficient, high-volume production.
(Boron Nitride+Silicon Nitride Ceramic Break Ring for Horizontal Continuous Casting)
Applications of Boron Nitride+Silicon Nitride Ceramic Break Ring for Horizontal Continuous Casting
Boron nitride and silicon nitride ceramic break rings play crucial functions in horizontal continuous spreading. These products deal with severe conditions in metal spreading procedures. They handle heats, thermal anxiety, and chemical reactions. This ensures steady procedures and boosts product quality.
Boron nitride ceramic break rings attract attention for their thermal shock resistance. They sustain quick temperature level modifications without breaking. Molten metal streams through the break ring during casting. Boron nitride’s reduced wettability stops steel adhesion. This lowers downtime for cleansing. It likewise preserves precise control over metal circulation. The result is smoother surface areas on cast products.
Silicon nitride ceramic break rings use high mechanical stamina. They stand up to wear and contortion under heavy loads. Straight continuous casting includes consistent rubbing from relocating steel. Silicon nitride’s firmness minimizes wear. This expands the break ring’s service life. It also minimizes substitute costs. The material’s oxidation resistance maintains it secure in oxygen-rich atmospheres. This is essential for lengthy spreading runs.
Combining boron nitride and silicon nitride develops crossbreed remedies. Designers customize break rings to specific casting needs. For example, boron nitride layers can layer silicon nitride cores. This combines thermal stability with structural toughness. Such designs manage complicated casting setups. They work well with reactive steels like aluminum or copper alloys.
These ceramic break rings enhance effectiveness in steel mills and shops. They reduced power usage by keeping regular process temperatures. Less defects mean much less material waste. Production speeds rise without giving up quality. Industries like vehicle and aerospace depend on high-precision steel components. Damage rings made from these ceramics aid satisfy strict requirements.
Operators gain from simpler maintenance. The non-reactive nature of both porcelains minimizes slag buildup. Cleaning up cycles shorten. Process disruptions go down. Training time for new team decreases. The break rings’ reliability simplifies workflow planning.
Straight continual casting needs products that carry out under tension. Boron nitride and silicon nitride ceramics satisfy these needs. Their unique buildings attend to common challenges in metal spreading. This makes them important for modern-day industrial applications.
Company Introduction
Advanced Ceramics founded on October 17, 2014, is a high-tech enterprise committed to the research and development, production, processing, sales and technical services of ceramic relative materials and products.. Since its establishment in 2014, the company has been committed to providing customers with the best products and services, and has become a leader in the industry through continuous technological innovation and strict quality management.
Our products includes but not limited to Silicon carbide ceramic products, Boron Carbide Ceramic Products, Boron Nitride Ceramic Products, Silicon Carbide Ceramic Products, Silicon Nitride Ceramic Products, Zirconium Dioxide Ceramic Products, Quartz Products, etc. Please feel free to contact us.(nanotrun@yahoo.com)
Payment Methods
T/T, Western Union, Paypal, Credit Card etc.
Shipment Methods
By air, by sea, by express, as customers request.
5 FAQs of Boron Nitride+Silicon Nitride Ceramic Break Ring for Horizontal Continuous Casting
What is a boron nitride + silicon nitride ceramic break ring used for in horizontal continuous casting?
It separates molten metal from cooling water during casting. It ensures smooth metal flow, prevents leaks, controls solidification. The combo of boron nitride and silicon nitride handles extreme heat, resists wear, reduces sticking.
Why choose boron nitride and silicon nitride for break rings?
Boron nitride resists heat, acts as a lubricant. Silicon nitride adds strength, fights cracks. Together, they last longer under high stress. They handle thermal shock better than metals or other ceramics.
What temperatures can these break rings withstand?
They work up to 1500°C. Boron nitride keeps stability in rapid heating or cooling. Silicon nitride maintains strength at high temps. This combo avoids melting or warping in casting conditions.
How do these break rings improve casting efficiency?
They cut downtime for replacements. Low friction means smoother metal flow, fewer defects. Less sticking means easier cleanup. Consistent performance lowers production costs over time.
How to maintain boron nitride + silicon nitride break rings?
Inspect regularly for cracks or wear. Clean surfaces after use to remove residue. Avoid impacts during handling. Store dry to prevent moisture damage. Follow manufacturer guidelines for installation pressure and alignment.
(Boron Nitride+Silicon Nitride Ceramic Break Ring for Horizontal Continuous Casting)
REQUEST A QUOTE
RELATED PRODUCTS
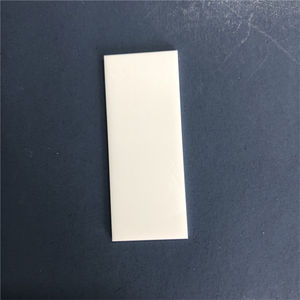
Hexagonal 99% Boron Nitride Ceramic Sheet BN Ceramic Disc Board Pbn Plate Piece
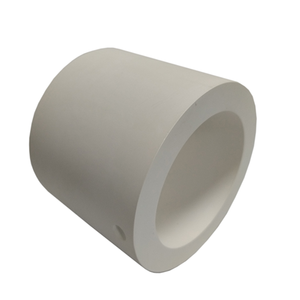
Ceramic Cubic Boron Nitride (CBN) Grinding Wheel Resin-Bonded Universal Joint Ball Cage Gear Disc for Aluminum Compressor Parts
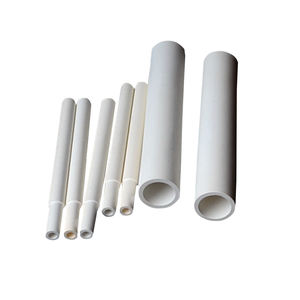
The Erosion-Resistant Sentinel of Chemical Processes – Boron Nitride Ceramic Tube
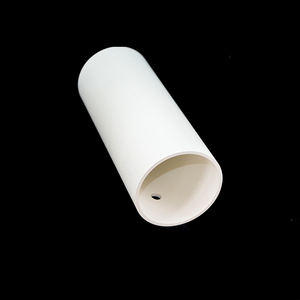
square or Rectangular 99% Boron Nitride Ceramic Plate BN Sheet
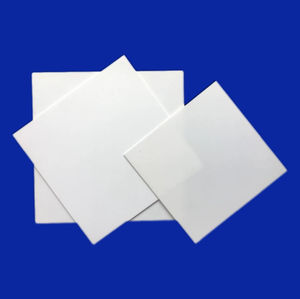
High Purity 99% Insulator Hexagonal Boron Nitride Ceramic Parts Boron Nitride Rod Tube Plate Disc for PVD and Plasma Systems
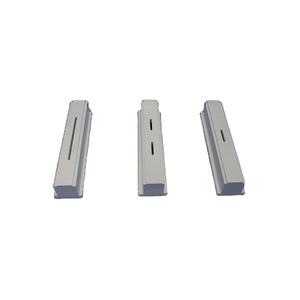