Discover Premium Ceramic Products | Durability & Elegance United | Advanced Ceramics
PRODUCT PARAMETERS
Description
Introduction to Quartz Ceramic Products
Quartz ceramic, also known as fused quartz ceramic or pure silicon ceramic, is an advanced ceramic material made of pure silicon dioxide (SiO₂). It is made by melting high-purity quartz sand at high temperature and then cooling and solidifying it. It has unique physical and chemical properties, making it an ideal choice for many high-tech applications. Quartz ceramic products are widely used in semiconductor manufacturing, optics, electronics, chemical industry and high-temperature industries.
Characteristics and advantages of quartz ceramics
Extremely high thermal stability: Quartz ceramics can remain stable under extreme temperature conditions. They are not only resistant to high temperatures, but also show excellent thermal shock resistance in rapid temperature changes.
Low thermal expansion coefficient: Due to its low thermal expansion coefficient, quartz ceramics have good dimensional stability when the temperature changes and are not easy to deform or crack.
Excellent electrical insulation: Provides excellent electrical insulation performance and is suitable for applications requiring high voltage isolation.
High transparency: It has good light transmittance in a wide band from ultraviolet to infrared, and is particularly suitable for applications such as optical windows and lenses.
Chemical stability: Excellent resistance to most acids, alkalis and other corrosive substances, and almost unaffected by other chemicals except hydrofluoric acid and phosphoric acid.
Mechanical strength: Although quartz ceramic is not as hard as some other types of ceramics, it still has enough mechanical strength to meet the needs of many application scenarios.
High UV transmittance: It has high transmittance in the ultraviolet region, which makes it very useful in UV curing equipment and UV spectrometers.
(99.96% Fused Quartz Metallurgical Silica 100-200mesh Ceramic Casting High Purity 100% Silica Product)
Specifications of 99.96% Fused Quartz Metallurgical Silica 100-200mesh Ceramic Casting High Purity 100% Silica Product
This item is made of 99.96% merged quartz metallurgical silica. The product is processed into a great granular type with a mesh size of 100-200. It is perfect for ceramic casting applications as a result of its high purity. The silica web content gets to 100%, ensuring minimal contaminations. This makes it appropriate for industries needing strict quality control.
The mesh dimension of 100-200 enables also distribution in mold and mildews. This improves the architectural stability of finished ceramic products. The granules fuse efficiently under heats. They create dense, durable ceramic components. The low thermal expansion coefficient minimizes breaking during heating or air conditioning. This security is important for accuracy casting processes.
High-purity silica stands up to chemical corrosion. It performs well in acidic or alkaline atmospheres. This prolongs the life-span of ceramic parts in harsh problems. The product’s refractory homes permit it to withstand temperatures over 1600 ° C. It maintains strength and form under extreme warm.
The production procedure includes melting all-natural quartz at heats. The molten material is cooled rapidly to form integrated quartz. This approach eliminates interior bubbles or defects. The result is an uniform framework with consistent fragment dimension. Each batch undertakes strenuous screening for pureness and mesh accuracy.
This item is used in aerospace, vehicle, and commercial production. It serves as a basic material for innovative porcelains like insulators or crucibles. The great mesh dimension makes sure smooth surface area finishes in cast items. It minimizes the requirement for post-processing grinding or brightening.
Individuals must store the product in completely dry, closed containers. Moisture absorption can influence flowability during spreading. Handling requires basic protective equipment to avoid breathing of great particles. The product adheres to worldwide security and top quality requirements.
Adjustable mesh sizes are offered for particular applications. Mass orders include in-depth technical support for combination into assembly line. The material is compatible with the majority of ceramic binding agents. It makes certain reliable performance in automated or hands-on spreading systems.
Industries focusing on accuracy and sturdiness benefit from this silica. Its thermal and chemical stability supports lasting functional effectiveness. The high pureness decreases contamination risks in delicate procedures. Consistent high quality across sets warranties repeatable outcomes.
(99.96% Fused Quartz Metallurgical Silica 100-200mesh Ceramic Casting High Purity 100% Silica Product)
Applications of 99.96% Fused Quartz Metallurgical Silica 100-200mesh Ceramic Casting High Purity 100% Silica Product
The 99.96% fused quartz metallurgical silica 100-200mesh ceramic casting high-purity silica item serves several commercial purposes. Its high pureness and thermal stability make it ideal for requiring settings. The material works well in metallurgical procedures. It endures severe temperature levels during steel smelting and refining. The fine 100-200mesh bit dimension makes sure even circulation in molds and mixes. This boosts performance in applications like refractory cellular linings for furnaces.
The product is widely made use of in ceramic casting. Its low thermal development stops breaking under rapid temperature modifications. Ceramic molds made with this silica keep precision throughout spreading. This is critical for aerospace and vehicle parts. The high pureness decreases issues in finished items.
Semiconductor making relies on this silica. Pollutants can destroy electronic parts. The 99.96% pureness meets rigorous industry criteria. It is made use of in crucibles for melting silicon. These crucibles have to withstand heat and chemical reactions.
Chemical processing equipment gain from the material’s rust resistance. It deals with aggressive acids and antacids without weakening. Containers, pipelines, and valves made with this silica last longer. Maintenance prices decline.
The glass industry utilizes it for top notch optical glass. Pollutants affect clarity. The silica ensures openness and toughness. It is also contributed to specialized glasses for labs and electronics.
High-temperature insulation is one more crucial use. The silica’s stability at over 1000 ° C makes it appropriate for kilns and reactors. It protects efficiently while withstanding wear.
The 100-200mesh size aids bonding in ceramic and refractory applications. Smaller fragments fill spaces much better. This creates denser, more powerful structures.
This silica item is flexible. It meets demands across markets requiring warmth resistance, pureness, and longevity. Manufacturers select it for regular results.
Company Introduction
Advanced Ceramics founded on October 17, 2014, is a high-tech enterprise committed to the research and development, production, processing, sales and technical services of ceramic relative materials and products.. Since its establishment in 2014, the company has been committed to providing customers with the best products and services, and has become a leader in the industry through continuous technological innovation and strict quality management.
Our products includes but not limited to Silicon carbide ceramic products, Boron Carbide Ceramic Products, Boron Nitride Ceramic Products, Silicon Carbide Ceramic Products, Silicon Nitride Ceramic Products, Zirconium Dioxide Ceramic Products, Quartz Products, etc. Please feel free to contact us.(nanotrun@yahoo.com)
Payment Methods
T/T, Western Union, Paypal, Credit Card etc.
Shipment Methods
By air, by sea, by express, as customers request.
5 FAQs of 99.96% Fused Quartz Metallurgical Silica 100-200mesh Ceramic Casting High Purity 100% Silica Product
What is 99.96% Fused Quartz Metallurgical Silica?
This product is high-purity silica processed into 100-200 mesh particles. It is made by melting quartz at extreme temperatures. The result is a material with 99.96% SiO₂ content. It is used in high-temperature industrial applications.
What industries use this product?
Metal casting and ceramics manufacturing rely on it. Foundries add it to molds for heat resistance. Refractory producers mix it into linings for furnaces. Electronics companies use it in components needing insulation. Labs apply it for precision tools.
Why choose 100-200 mesh size?
The particle size balances flow and packing density. Fine grains fill gaps in molds. They create smooth surfaces in castings. Coarser grains maintain structure under stress. The range ensures consistent performance in high-heat settings.
How does high purity matter?
Impurities below 0.04% prevent contamination. Metals stay clean during melting. Ceramics avoid cracks from unwanted reactions. Thermal stability improves. Products last longer under harsh conditions.
Is it safe to handle?
The material is chemically inert. It does not react with most substances. Wear gloves and masks to avoid dust inhalation. Store it dry to prevent clumping. Follow standard industrial safety guidelines.
Where can I buy this product?
Contact suppliers directly for bulk orders. Custom packaging is available. Samples are offered for quality testing. Check certifications for purity and mesh size. Ensure the supplier provides technical support.
What are the storage requirements?
Keep it in sealed containers. Moisture causes particles to stick. Store in a cool, dry area. Avoid mixing with other materials. Use within six months for best results.
Does it work with all casting methods?
It suits most ceramic and sand casting processes. Adjust binder ratios for specific needs. Test small batches first. High-purity silica reduces defects in final products.
Can it replace other silica types?
It outperforms lower-purity alternatives. Thermal shock resistance is better. Contamination risks drop. Costs may be higher but improve output quality.
What technical specs are critical?
Confirm SiO₂ content meets 99.96%. Verify mesh size distribution. Check moisture content below 0.5%. Request data sheets for thermal expansion rates. Compare melting points with your process requirements.
(99.96% Fused Quartz Metallurgical Silica 100-200mesh Ceramic Casting High Purity 100% Silica Product)
REQUEST A QUOTE
RELATED PRODUCTS
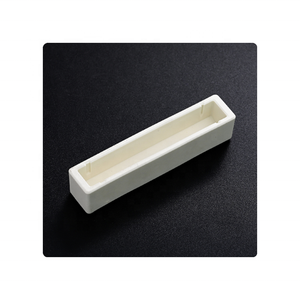
Lab Melting Used Fused Silica Quartz SiO2 Ceramic Crucible Cup
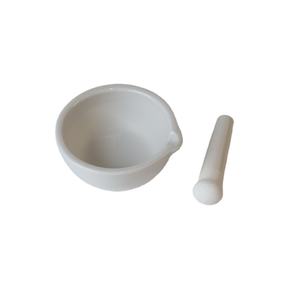
Lab Melting Used Fused Silica Quartz Sio2 Ceramic Crucible
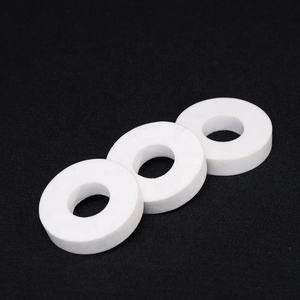
OD130mm H120mm 99% High Purity Fused Quartz Silica SiO2 Ceramic Cylindrical Crucible
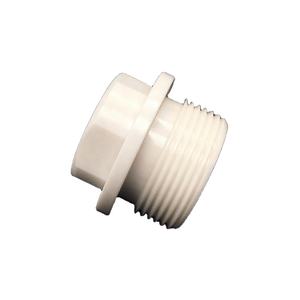
Factory Direct Supply China Quartzite Stone Porcelain Slab Luxury Pandora Brazil Countertop Sintered Stone
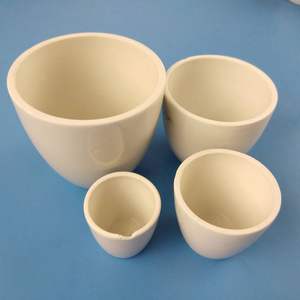
100g/250g/500g/1000g/1500g/2500g Casting Ceramic Crucible Quartz Melting Dishes Pot for Sliver Gold Platinum Refining
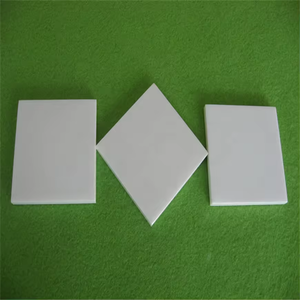