Discover Premium Ceramic Products | Durability & Elegance United | Advanced Ceramics
PRODUCT PARAMETERS
Description
Overview of Silicon Carbide Grinding Ball
The main component of silicon carbide grinding balls is silicon carbide (SiC). Silicon carbide is a compound formed by covalent bonds between silicon (Si) and carbon (C). Its crystal structure gives it many excellent properties. This structure makes silicon carbide grinding balls have high hardness and good chemical stability.
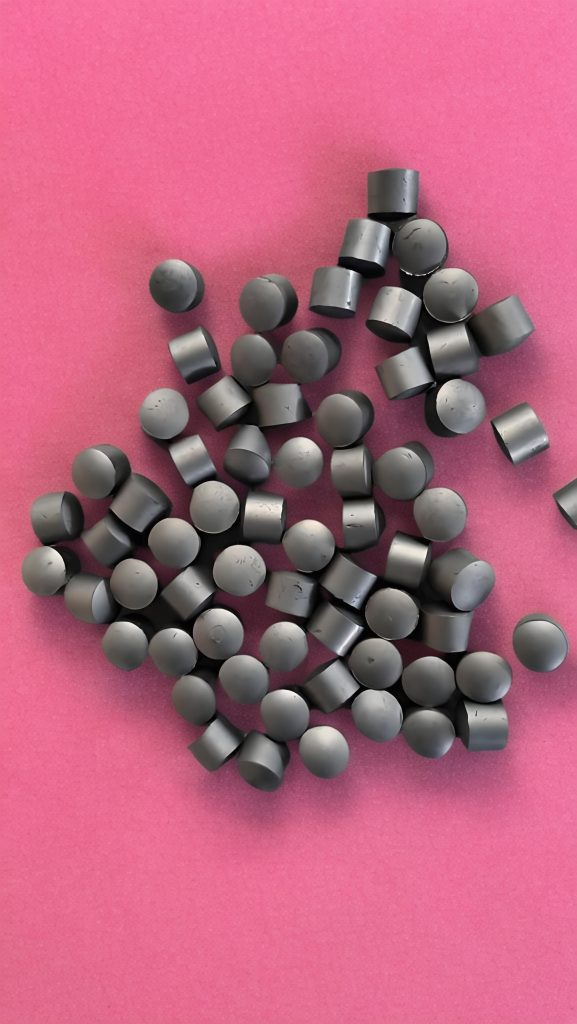
Silicon Carbide Grinding Ball
Features of Silicon Carbide Grinding Ball
1.High Hardness
Silicon carbide grinding balls are very hard, second only to diamond on the Mohs hardness scale. This high hardness allows them to grind a variety of materials, including hard ceramics, hard alloys (such as tungsten carbide), and some super-hard alloys. For example, in the ceramic production process, silicon carbide grinding balls can grind the newly formed ceramic blanks to make their surfaces flat and smooth. Moreover, during the grinding process, they wear slowly and can maintain the stability of shape and size for a long time, thus ensuring the consistency of grinding performance.
2.Excellent wear resistance
Its excellent wear resistance comes from its high hardness and stable covalent bond crystal structure. During the grinding operation, it can withstand continuous friction and impact. Taking the ball mill as an example, the grinding balls constantly collide with the ground material and other grinding balls during the grinding process, but silicon carbide grinding balls can maintain their spherical shape and surface quality for a long time. This not only reduces the frequency of grinding ball replacement but also helps to ensure the quality and precision of the ground products.
3.Low coefficient of friction
The surface of silicon carbide grinding balls is relatively smooth, which makes it have a low coefficient of friction. This property reduces the energy required for grinding when in contact with the material being ground. It also reduces the heat generated during the grinding process, which is very beneficial for preventing overheating of the material being ground and the grinding balls themselves. In high-speed grinding applications, such as some precision grinders, the low friction characteristics of silicon carbide grinding balls help achieve more efficient and stable grinding operations.
4.High density and good impact resistance
Silicon carbide grinding balls have a relatively high density, usually around 3.2 – 3.3g/cm³. This high density gives it good impact resistance, allowing it to withstand the strong impact forces generated during grinding, such as when the grinding ball falls or collides at high speed without being easily damaged. Its density also ensures that there is enough kinetic energy during the grinding process to break and grind the material effectively. In a ball mill, this property allows the grinding balls to work better and improve grinding efficiency.
5.Good thermal stability
It has a low thermal expansion coefficient, so it has good thermal stability. Silicon carbide grinding balls are able to maintain their physical and mechanical properties over a wide temperature range. In high-temperature grinding applications, such as grinding refractory materials, it can withstand high temperatures without significant deformation or damage. In addition, its good thermal conductivity allows it to dissipate heat quickly, further enhancing stability during the grinding process.
6. Chemical Inertness
Silicon carbide grinding balls are largely chemically inert and have excellent resistance to acids, bases and many other chemicals. This property makes them suitable for grinding a wide variety of materials, including those that may release corrosive substances during the grinding process. For example, when grinding ores that may contain acidic or alkaline components, silicon carbide grinding balls are able to resist chemical corrosion and continue to perform effectively.
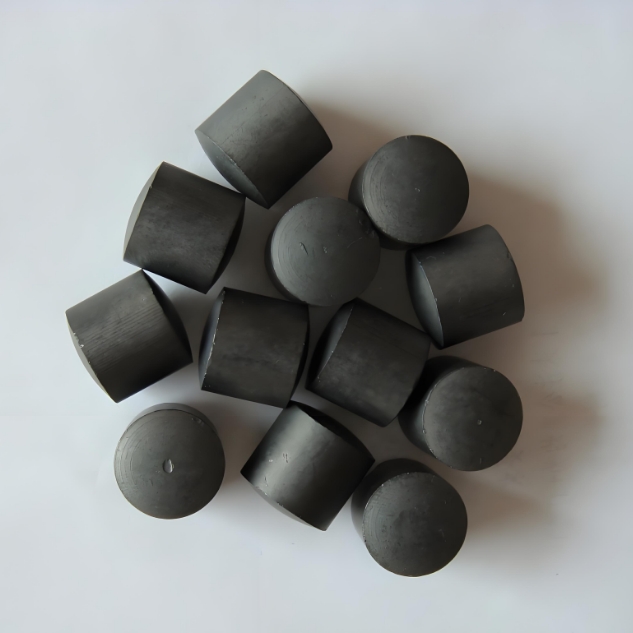
Silicon Carbide Grinding Ball
Specifications of Silicon Carbide Grinding Ball
Parameter | Specification Details |
Material | Silicon Carbide (SiC) |
Grade | Various grades available (e.g., SGSiC, RBSiC) |
Purity | ≥ 98% SiC |
Hardness (Vickers) | ~2500-3000 HV |
Density | ~3.21 g/cm³ |
Sphericity | > 99% roundness |
Surface Finish | Polished or ground, with surface roughness Ra |
Diameter Tolerance | ±0.001 mm to ±0.005 mm (varies by size) |
Sphericity Tolerance | < 0.5 µm to < 2 µm (depending on grade) |
Roundness Tolerance | < 0.5 µm to < 2 µm (depending on grade) |
Size Range | Typically from 1 mm to 50 mm |
Coating Options | Available, e.g., TiN, DLC (if applicable) |
Temperature Resistance | Up to ~1600°C in inert atmosphere |
Corrosion Resistance | Excellent in many environments |
Electrical Conductivity | Can be electrically conductive or insulating |
Magnetic Properties | Non-magnetic |
Fracture Toughness | High, suitable for high-stress applications |
Abrasion Resistance | Excellent, minimizes wear during grinding |
Thermal Conductivity | High, aids in heat dissipation |
Chemical Stability | Resistant to most acids and alkalis |
Application | Grinding media, ball mills, industrial valves, |
nozzles, bearings, etc. |
Additional Notes:
Grades: Different grades of silicon carbide grinding balls are available, each optimized for specific applications. For example, sintered silicon carbide (SGSiC) and reaction-bonded silicon carbide (RBSiC) have different properties that make them suitable for various uses.
Surface Finish: The surface finish can be customized based on the application. Polished balls offer a smoother surface, while ground balls may have a slightly rougher texture.
Custom Sizes: Some manufacturers offer custom sizes outside the typical range upon request.
Coatings: Coatings like titanium nitride (TiN) or diamond-like carbon (DLC) can enhance certain properties, such as wear resistance or lubricity.
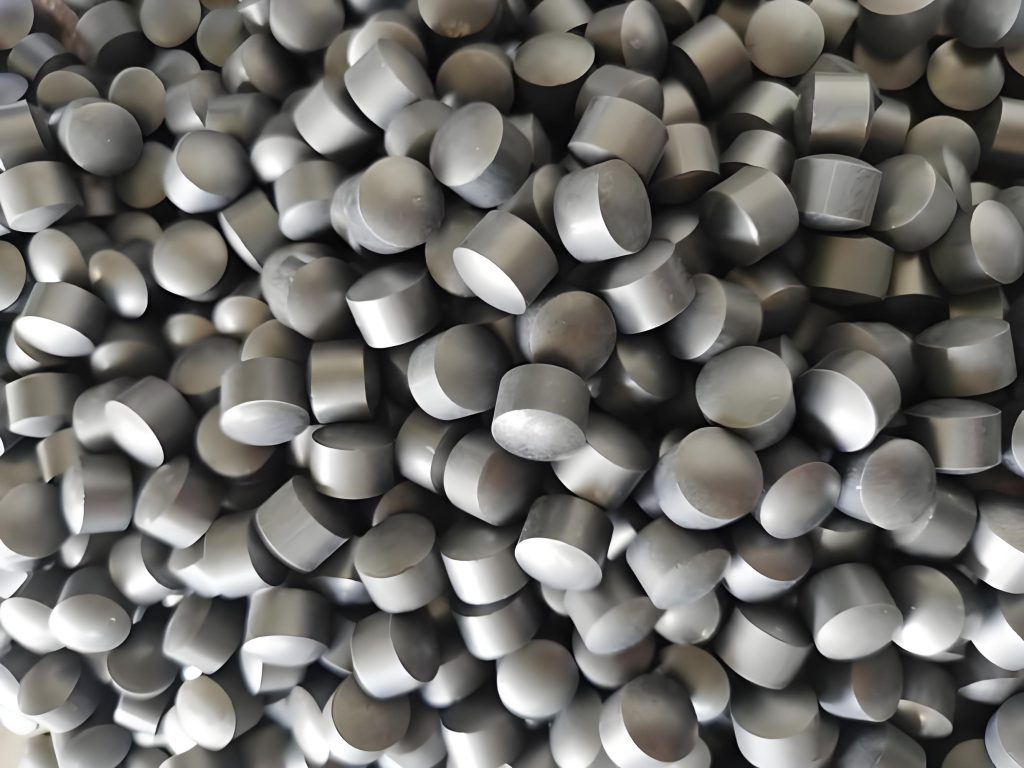
Silicon Carbide Grinding Ball
Applications of Silicon Carbide Grinding Ball
1.Ceramic industry
In the grinding and polishing process of ceramic blanks, silicon carbide grinding balls are indispensable tools. Due to the high hardness of ceramic materials, grinding balls with matching hardness are required for processing. For example, in tile production, silicon carbide grinding balls can be used to grind the surface of tiles to achieve the required flatness and glossiness. In the manufacturing process of fine ceramic products such as ceramic tableware and artistic ceramics, it can also accurately grind the surface of ceramics, remove tiny defects, and improve product quality.
For special ceramics, such as electronic ceramics and high-temperature ceramics, the application of silicon carbide grinding balls is more critical. These special ceramics often have extremely high requirements for dimensional accuracy and surface quality. Silicon carbide grinding balls can effectively grind these ceramic materials with their high hardness, good wear resistance and low friction coefficient while ensuring that their physical and chemical properties are not damaged.
2.Mining field
In the grinding and beneficiation of ores, silicon carbide grinding balls play an important role. For ores with higher hardness, such as quartz stone and corundum ore, silicon carbide grinding balls can grind the ore into fine powder for subsequent beneficiation and refining. In the ball mill, its high density and good impact resistance allow it to withstand strong impact when grinding ore, and due to its chemical inertness, it will not be corroded when grinding ores containing corrosive components (such as sulfide ores), thus ensuring the continuous and effective progress of the grinding process.
In addition, in some high-precision ore analysis experiments, silicon carbide grinding balls can be used to prepare ore samples. It can grind the ore into a uniform powder, meet the strict requirements of the experiment on sample particle size and purity, and help to analyze the composition and properties of the ore accurately.
3.Metal processing industry
Silicon carbide grinding balls are also widely used in the grinding and polishing of metal materials. For some metals with higher hardness, such as stainless steel, carbide steel, etc., silicon carbide grinding balls can effectively grind their surfaces, remove defects such as oxide layers and burrs, and improve the flatness and finish of the metal surface. For example, in the manufacturing process of mechanical parts, after grinding metal parts with silicon carbide grinding balls, the surface of the parts can achieve higher precision and meet the requirements of precision mechanical assembly.
In the preparation of metal powder, silicon carbide grinding balls are also important tools. It can grind block metal into fine powder, and by controlling factors such as grinding time and the size of grinding balls, the particle size of metal powder can be precisely controlled to provide high-quality raw materials for processes such as powder metallurgy.
4.Chemical industry
In the grinding and crushing process of chemical raw materials, silicon carbide grinding balls are an ideal grinding medium. For some chemical raw materials with higher hardness, such as certain pigments, catalysts, etc., it can grind them to the required fineness. And because of its chemical inertness, no chemical reaction will occur when grinding chemical raw materials that may be corrosive, ensuring the stability of the chemical properties of chemical raw materials.
In the quality inspection of chemical products, silicon carbide grinding balls can also be used to prepare samples. For example, when testing the purity or composition of certain solid chemical products, the product needs to be ground into a uniform powder. Silicon carbide grinding balls can accomplish this task well and provide reliable samples for accurate chemical analysis.
5.Electronic materials industry
In the grinding and polishing process of electronic materials, the application of silicon carbide grinding balls is becoming more and more widespread. For electronic materials such as silicon wafers and sapphires, extremely high surface flatness and finish are required. Silicon carbide grinding balls can accurately grind the surface of these materials through processes such as chemical mechanical polishing (CMP) to achieve the accuracy required by electronic processes such as semiconductor manufacturing. For example, in the chip manufacturing process, the surface flatness of the silicon wafer directly affects the performance of the chip. Silicon carbide grinding balls can effectively remove tiny defects on the surface of the silicon wafer, creating good conditions for subsequent processes such as lithography and etching.
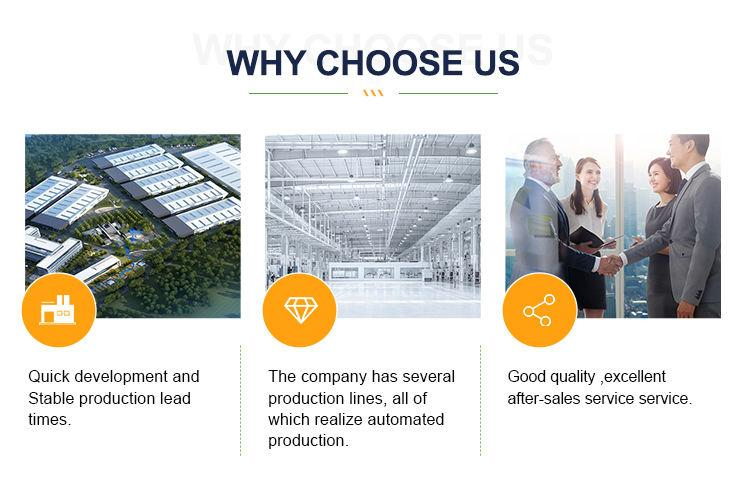
Company Profile
Advanced Ceramics founded on October 17, 2014, is a high-tech enterprise committed to the research and development, production, processing, sales and technical services of ceramic relative materials and products.. Since its establishment in 2014, the company has been committed to providing customers with the best products and services, and has become a leader in the industry through continuous technological innovation and strict quality management.
Our products includes but not limited to Silicon carbide ceramic products, Boron Carbide Ceramic Products, Boron Nitride Ceramic Products, Silicon Carbide Ceramic Products, Silicon Nitride Ceramic Products, Zirconium Dioxide Ceramic Products, Quartz Products, etc. Please feel free to contact us.(nanotrun@yahoo.com)
Payment Methods
T/T, Western Union, Paypal, Credit Card etc.
Shipment Methods
By air, by sea, by express, as customers request.
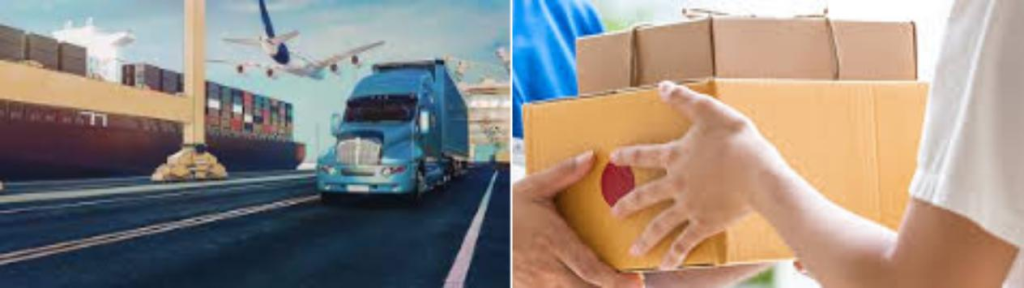
FAQs of Silicon Carbide Grinding Ball
1. What is the typical size range of silicon carbide grinding balls?
A: Silicon carbide grinding balls come in a wide range of sizes. The diameter can vary from a few millimeters to several centimeters. For fine-grinding applications such as polishing optical lenses or semiconductor wafers, the balls may have a diameter as small as 1 – 3 mm. In applications for grinding coarser materials like ores or large-scale metal parts, the diameter can be 10 – 50 mm or even larger to provide more efficient grinding due to their greater mass and impact force.
2. How do you choose the right size of silicon carbide grinding balls for a specific application?
A: The choice of size depends on several factors. For precision grinding of delicate materials with a need for high – surface – quality, smaller balls are usually preferred. Their smaller size allows for more precise control and finer grinding. When grinding materials that are hard and require a lot of force to break down, larger balls can be used. Larger balls have more mass and kinetic energy, which is beneficial for grinding tough materials like ores. Additionally, the size of the grinding equipment and the desired grinding speed also play a role. For example, in a small-capacity ball mill with a relatively low rotation speed, smaller balls might be more suitable to ensure proper movement and grinding action.
3. What is the difference between silicon carbide grinding balls and other types of grinding media (like alumina grinding balls)?
A: Silicon carbide grinding balls have higher hardness compared to alumina grinding balls. Silicon carbide is second only to diamond in hardness, while alumina is relatively softer. This means silicon carbide grinding balls can grind harder materials more effectively and have a slower wear rate. A: Silicon carbide also has a lower friction coefficient than alumina, resulting in less heat generation during grinding. Additionally, silicon carbide grinding balls have better chemical resistance to a wide range of substances, making them more suitable for grinding materials that may release corrosive chemicals during the grinding process.
4. How long do silicon carbide grinding balls last?
A: The lifespan of silicon carbide grinding balls depends on several factors. The hardness and abrasiveness of the material being ground play a significant role. If the material is relatively soft and non-abrasive, the grinding balls can last a long time. For example, when grinding some soft polymers, the silicon carbide grinding balls may maintain their performance for months or even years. However, when grinding hard and abrasive materials like tungsten carbide or quartz, the wear rate will be higher. The operating conditions, such as the grinding speed, the ratio of balls to the material being ground, and the presence of any contaminants, also affect their lifespan. Under normal industrial grinding conditions with moderately hard materials, silicon carbide grinding balls can last from several weeks to a few months.
5. Can silicon carbide grinding balls be used in wet-grinding applications?
A: Yes, silicon carbide grinding balls can be used in wet-grinding applications. In fact, wet-grinding can have several advantages. The presence of a liquid medium (such as water or a chemical solvent) can help to cool the grinding balls and the material being ground, reducing the risk of overheating. It can also help to carry away the ground particles, preventing them from re – adhering to the material or the grinding balls. However, it’s important to consider the chemical compatibility of the liquid medium with the silicon carbide grinding balls. While silicon carbide has good chemical resistance, some strong acids or alkalis may still have a certain impact on it.
6. How do you maintain silicon carbide grinding balls to ensure their performance?
A: Regular cleaning is essential. After each grinding session, the grinding balls should be cleaned to remove the ground material and any debris. This can be done using a suitable cleaning agent and a mechanical cleaning method such as ultrasonic cleaning or agitation in a cleaning solution. It’s also important to store the grinding balls properly. They should be stored in a dry and clean environment to prevent contamination and damage. Additionally, monitoring the wear of the grinding balls during use and replacing them when the wear reaches a certain level is crucial to maintaining consistent grinding performance.
7. What safety precautions should be taken when using silicon carbide grinding balls?
A: When handling silicon carbide grinding balls, it’s important to wear appropriate personal protective equipment such as gloves and safety glasses. The high hardness of the balls means that if they are dropped or mishandled, they can cause injury. In the grinding equipment, proper safeguards should be in place to prevent the balls from flying out due to mechanical failure or improper operation. Also, when cleaning the balls, if using chemical cleaners, make sure to follow the safety instructions for the chemicals to avoid any chemical hazards.
REQUEST A QUOTE
RELATED PRODUCTS
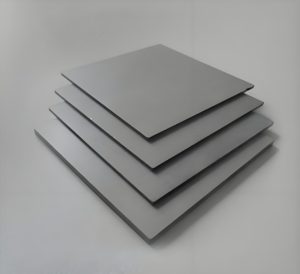
Silicon Carbide Plate High Quality SiC Sheet Manufacturer
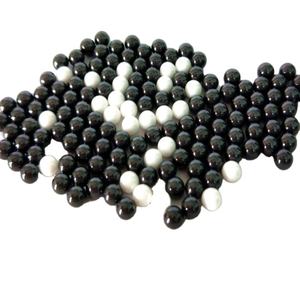
Silicon Nitride Ceramic Ball, Alumina Custom Industry White Black Moulding Silicon Carbide Industrial Ceramic Chian Roundness
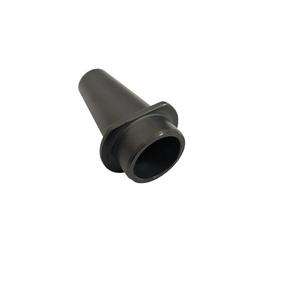
Custom Machining Silicon Carbide Hexagonal Plate High Temperature Resistant Ceramics Purity Ceramic Parts for Welding & Cutting
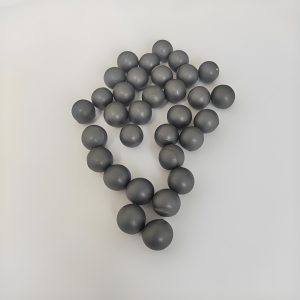
High Purity Silicon Carbide Fine Ball Customize Ceramic SiC Ball
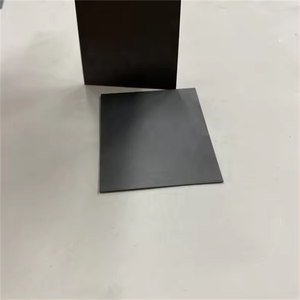
Customized Hexagonal Boron Carbide Silicon Carbide Ceramic Plate Tiles SIC Ceramic for Industrial Use Welding Cutting Services
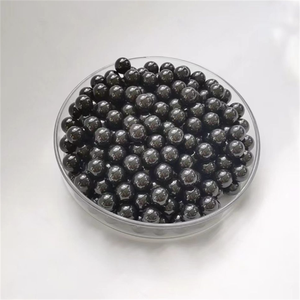