Discover Premium Ceramic Products | Durability & Elegance United | Advanced Ceramics
PRODUCT PARAMETERS
Description
Overview of Silicon Carbide Ceramics
Silicon Carbide (SiC) ceramics are renowned for their outstanding mechanical properties, including high hardness, strength at elevated temperatures, and excellent thermal shock resistance. These materials are pivotal in cutting-edge industrial applications, from abrasives to aerospace components, due to their unique combination of properties.
Features of Silicon Carbide Ceramics
High Hardness: Exceptional wear resistance.
Thermal Shock Resistance: Can withstand rapid temperature changes.
Chemical Stability: Resistant to most chemicals.
High Thermal Conductivity: Efficient heat dissipation.
Low Density: Lightweight for its strength.
(High Temperature Black Zirconia Manufacture Lab Precision Ceramic Parts Silicon Carbide Ceramics)
Specification of High Temperature Black Zirconia Manufacture Lab Precision Ceramic Parts Silicon Carbide Ceramics
High Temperature Black Zirconia ceramic parts are engineered for requiring applications requiring extreme warm resistance and mechanical sturdiness. These precision components are produced in specialized labs using innovative processing strategies to ensure consistent quality and efficiency. The product structure integrates zirconia with maintaining representatives, improving thermal stability while preserving structural integrity in settings up to 1600 ° C.
Silicon Carbide Ceramics are integrated right into the design for applications requiring superior wear resistance and high thermal conductivity. The combination of zirconia and silicon carbide creates a crossbreed material efficient in holding up against fast temperature level changes without cracking or deteriorating. This makes the components perfect for industries such as aerospace, automotive, and energy, where components face intense warm and mechanical anxiety.
Manufacturing involves accuracy molding and sintering procedures to accomplish limited dimensional resistances, often within ± 0.5% of defined dimensions. Surface area coatings are brightened to decrease friction and wear, essential for components utilized in high-speed equipment or corrosive settings. Customized sizes and shapes are available, customized to fulfill particular operational demands.
The black pigmentation of the zirconia is attained through controlled additives during manufacturing, providing an uniform appearance without endangering product properties. This attribute is advantageous for applications where looks or light absorption are important. Electric insulation properties are maintained even at elevated temperature levels, making these porcelains ideal for digital or semiconductor devices.
High Temperature Black Zirconia components exhibit excellent rust resistance versus acids, antacid, and molten metals. Mechanical stamina stays high under load, with a Vickers hardness ranking going beyond 1200 HV. The reduced thermal development coefficient guarantees very little dimensional adjustments during temperature variations, preserving precision in critical assemblies.
These porcelains are examined carefully for performance under simulated operating problems, ensuring dependability before shipment. Industries such as metallurgy, chemical handling, and medical technology use these components for furnace cellular linings, reducing tools, and implantable tools. Compatibility with advanced machining methods enables post-sintering alterations if needed.
Customized services are available for distinct difficulties, sustained by technological experience in ceramic design. The focus continues to be on supplying components that extend devices life expectancy, decrease downtime, and maximize effectiveness in high-stress settings.
(High Temperature Black Zirconia Manufacture Lab Precision Ceramic Parts Silicon Carbide Ceramics)
Applications of High Temperature Black Zirconia Manufacture Lab Precision Ceramic Parts Silicon Carbide Ceramics
High-temperature black zirconia is a solid ceramic product constructed to take care of extreme warmth. It plays a vital role in making accuracy parts for laboratories and industrial settings. These parts typically face high tension and temperatures without damaging down. In aerospace, black zirconia is utilized in engine components and sensing units. These parts remain steady in hot settings where steels may fall short.
One more major use remains in semiconductor production. Parts right here need to stand up to warm and chemical corrosion. Black zirconia works well because it stays stable under high warmth and does not respond with harsh chemicals. This keeps production procedures reliable and decreases equipment downtime.
Silicon carbide ceramics share comparable toughness. They are difficult and perform warmth better than lots of metals. In the automobile sector, both materials are used for components like brake discs and engine parts. They aid automobiles perform much better under high stress and anxiety and heat.
The power field relies upon these ceramics for systems in atomic power plants and photovoltaic panels. They manage severe problems much better than standard materials, last much longer, and boost safety and security. Medical devices also advantages. Devices made from black zirconia and silicon carbide can be disinfected at heats without damages. This makes them ideal for surgical tools and implants needing precision and resilience.
In labs, high-temperature black zirconia is utilized for crucibles and sample holders. These products sustain duplicated home heating and cooling down cycles. Silicon carbide ceramics are utilized in high-performance seals and bearings. Their hardness prevents use also under heavy use.
Industrial equipment makes use of wear-resistant parts made from these ceramics. They minimize friction, last much longer, and reduced substitute expenses. This maintains makers running smoothly and saves money.
These materials are chosen for their reliability in tough settings. They fulfill the requirements of sectors where failure is not an alternative. Their use expands as innovation demands far better efficiency. Electrical insulation is one more key feature. In electronics producing, components made from these ceramics prevent electrical leakages. This is essential for devices exposed to high voltages or temperatures.
Company Introduction
Advanced Ceramics founded on October 17, 2014, is a high-tech enterprise committed to the research and development, production, processing, sales and technical services of ceramic relative materials and products.. Since its establishment in 2014, the company has been committed to providing customers with the best products and services, and has become a leader in the industry through continuous technological innovation and strict quality management.
Our products includes but not limited to Silicon carbide ceramic products, Boron Carbide Ceramic Products, Boron Nitride Ceramic Products, Silicon Carbide Ceramic Products, Silicon Nitride Ceramic Products, Zirconium Dioxide Ceramic Products, Quartz Products, etc. Please feel free to contact us.(nanotrun@yahoo.com)
Payment Methods
T/T, Western Union, Paypal, Credit Card etc.
Shipment Methods
By air, by sea, by express, as customers request.
5 FAQs of High Temperature Black Zirconia Manufacture Lab Precision Ceramic Parts Silicon Carbide Ceramics
High Temperature Black Zirconia and Silicon Carbide Ceramics are used in extreme conditions. Below are common questions about these materials.
What temperatures can these ceramics handle?
Black Zirconia works up to 800°C. Silicon Carbide handles over 1600°C. Both keep strength under heat. They resist thermal shock. This prevents cracking during rapid temperature changes.
Where are these ceramics used?
They suit aerospace, automotive, and energy industries. Black Zirconia works in seals, bearings, and cutting tools. Silicon Carbide fits furnace parts, turbine blades, and heat exchangers. Both survive harsh chemicals and wear.
How do Black Zirconia and Silicon Carbide differ?
Black Zirconia has higher mechanical strength. It resists wear better. Silicon Carbide conducts heat more efficiently. It handles higher temperatures. Choose based on application needs.
Can these parts have smooth surfaces?
Yes. Precision grinding and polishing create smooth finishes. Surface roughness can reach Ra 0.1 microns. Smooth surfaces reduce friction. This improves performance in moving parts.
Are custom shapes possible?
Yes. Labs use CNC machining and molding for complex designs. Tolerances as tight as ±0.001 mm are achievable. Custom parts meet specific industrial requirements.
These ceramics offer durability in extreme environments. Their properties make them ideal for demanding applications.
(High Temperature Black Zirconia Manufacture Lab Precision Ceramic Parts Silicon Carbide Ceramics)
REQUEST A QUOTE
RELATED PRODUCTS
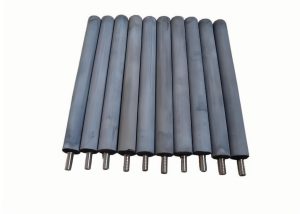
Silicon Carbide Rod High Hardness And High Strength SiC Rod
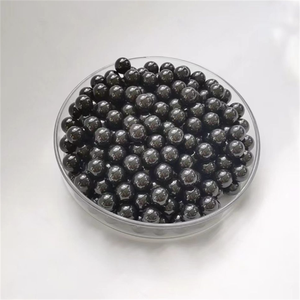
Polished High Purity Silicon Carbide Nitride Si3N4 Ceramic Rod
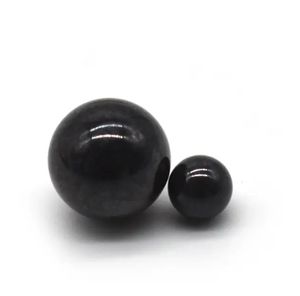
High Temperature Resistance Silicon Carbide Ceramic Pipe Sisic Sic Silicon Carbided Sic
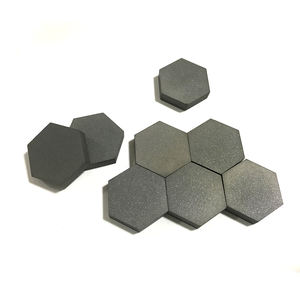
Silicon Carbide Ceramic Disc Ceramic Disc Wear Resistant Corrosion Resistant High Temperature Ring Mechanical Parts
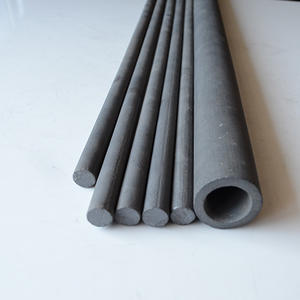
Customized Surface Polished Silicon Carbide Ceramic Rod Sic Ceramic Shaft
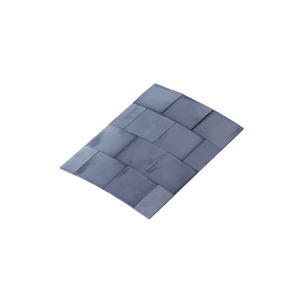