Discover Premium Ceramic Products | Durability & Elegance United | Advanced Ceramics
PRODUCT PARAMETERS
Description
Overview of Silicon Carbide Ceramics
Silicon Carbide (SiC) ceramics are renowned for their outstanding mechanical properties, including high hardness, strength at elevated temperatures, and excellent thermal shock resistance. These materials are pivotal in cutting-edge industrial applications, from abrasives to aerospace components, due to their unique combination of properties.
Features of Silicon Carbide Ceramics
High Hardness: Exceptional wear resistance.
Thermal Shock Resistance: Can withstand rapid temperature changes.
Chemical Stability: Resistant to most chemicals.
High Thermal Conductivity: Efficient heat dissipation.
Low Density: Lightweight for its strength.
(OEM Customized Refractory Material Industrial Furnace Sintered Silicon Carbide Ceramic Plate)
Specification of OEM Customized Refractory Material Industrial Furnace Sintered Silicon Carbide Ceramic Plate
The OEM Custom-made Refractory Product Industrial Furnace Sintered Silicon Carbide Porcelain Plate is designed for high-temperature commercial applications. It works as a durable lining or architectural component in heaters, kilns, and activators. The product is made from high-purity silicon carbide processed with sophisticated sintering technology. This makes sure a dense, non-porous structure efficient in withstanding extreme heat and mechanical tension.
The ceramic plate supplies superb thermal stability. It operates properly in temperatures as much as 1650 ° C without shedding structural integrity. Its high mechanical stamina withstands splitting under quick temperature level changes. The material also withstands rust from acids, antacid, and molten metals. This makes it appropriate for rough industrial environments.
Modification options include variable thickness, length, and size. Requirement thickness varies from 10mm to 50mm. Dimensions can be gotten used to fit certain heating system layouts. Home plate is offered in flat, bent, or grooved forms. Surface coatings are customized to boost heat reflection or abrasion resistance based upon application requirements.
Thermal conductivity is optimized to stabilize warm retention and power performance. The reduced thermal growth coefficient reduces contortion throughout heating cycles. This lengthens the service life of heating system elements. The product’s light-weight nature simplifies installment while preserving toughness.
Applications span steelmaking, glass manufacturing, and non-ferrous steel handling. It is made use of in burners, chemical activators, and semiconductor production. The ceramic plate lowers downtime by withstanding prolonged exposure to hostile conditions.
OEM companions get tailored remedies for special heater setups. Technical assistance covers design adjustments, efficiency testing, and product optimization. Quality control consists of rigorous checks for thickness, hardness, and dimensional accuracy. Each set undergoes thermal shock and lots resistance screening.
Packaging choices safeguard the plates throughout delivery. Wooden dog crates or foam-secured pallets stop transit damages. Bulk orders are sustained with regular lead times.
The item enhances heater effectiveness by decreasing warmth loss. It reduces upkeep expenses via extended replacement intervals. Functional security boosts due to reliable performance under extreme conditions. Energy savings result from improved thermal management.
(OEM Customized Refractory Material Industrial Furnace Sintered Silicon Carbide Ceramic Plate)
Applications of OEM Customized Refractory Material Industrial Furnace Sintered Silicon Carbide Ceramic Plate
OEM customized refractory material commercial heating system sintered silicon carbide ceramic plates offer crucial roles in high-temperature commercial processes. These plates are crafted to stand up to severe heat, corrosion, and mechanical stress and anxiety. They are commonly used in sectors like metallurgy, chemical production, and power generation. Their primary function is to line commercial furnaces, kilns, and activators, guaranteeing efficient warmth retention and structural stability.
In metallurgical applications, these ceramic plates work as safety barriers in steelmaking and light weight aluminum smelting heaters. They stand up to molten steel disintegration and thermal shock. This extends heater lifespan and decreases downtime for repair services. Chemical plants depend on them for activators and incinerators. The product’s resistance to acidic and alkaline settings prevents degradation. This makes sure regular efficiency in aggressive chemical handling.
Energy industries make use of sintered silicon carbide plates in coal gasifiers and power generation systems. Their high thermal conductivity improves heat transfer performance. This reduces power consumption and boosts functional outcome. Home plates likewise operate in glass manufacturing. They hold up against temperature levels over 1600 ° C without bending. This maintains specific glass-forming conditions and product high quality.
Customization is key. Manufacturers tailor measurements, forms, and porosity to fit certain heater layouts. This versatility maximizes installment and efficiency. The material’s reduced thermal growth lessens breaking throughout quick temperature modifications. Its mechanical stamina supports heavy loads in large industrial setups.
Toughness is a significant advantage. These plates outlast standard refractory products like alumina or fireclay. Minimized replacement regularity cuts upkeep costs. Their light-weight nature simplifies managing and installation. This saves labor time and operational expenses.
Environmental benefits exist. Enhanced thermal effectiveness decreases gas intake and greenhouse gas exhausts. The material’s longevity reduces industrial waste from constant substitutes. Industries prioritize these plates for sustainable, high-performance operations.
The sintered silicon carbide ceramic plates fulfill rigorous commercial criteria. They are checked for thermal security, put on resistance, and chemical inertness. Global manufacturers trust them for vital high-temperature applications. Their dependability supports continual production cycles popular settings.
Company Introduction
Advanced Ceramics founded on October 17, 2014, is a high-tech enterprise committed to the research and development, production, processing, sales and technical services of ceramic relative materials and products.. Since its establishment in 2014, the company has been committed to providing customers with the best products and services, and has become a leader in the industry through continuous technological innovation and strict quality management.
Our products includes but not limited to Silicon carbide ceramic products, Boron Carbide Ceramic Products, Boron Nitride Ceramic Products, Silicon Carbide Ceramic Products, Silicon Nitride Ceramic Products, Zirconium Dioxide Ceramic Products, Quartz Products, etc. Please feel free to contact us.(nanotrun@yahoo.com)
Payment Methods
T/T, Western Union, Paypal, Credit Card etc.
Shipment Methods
By air, by sea, by express, as customers request.
5 FAQs of OEM Customized Refractory Material Industrial Furnace Sintered Silicon Carbide Ceramic Plate
What are the main benefits of using sintered silicon carbide ceramic plates in industrial furnaces?
Sintered silicon carbide ceramic plates offer high thermal conductivity. They resist thermal shock effectively. These plates handle extreme temperatures without cracking. They show strong resistance to chemical corrosion. Their mechanical strength ensures long-term durability in harsh furnace environments.
Can these ceramic plates be customized for specific furnace designs?
Yes. OEM customization allows adjustments in size, shape, and thickness. Surface finishes or special features like grooves can be added. Custom designs match exact furnace requirements. Technical specifications are tailored to fit unique operational needs.
What temperature range do these plates withstand?
The plates operate reliably up to 1600°C in oxidizing atmospheres. In reducing environments, they handle temperatures near 1800°C. Their stability prevents deformation under prolonged heat exposure. This makes them suitable for high-intensity industrial processes.
How do these plates compare to traditional refractory materials?
Silicon carbide plates outperform materials like alumina or fireclay. They last longer under thermal stress. Their lightweight nature reduces furnace structural load. Energy efficiency improves due to better heat distribution. Maintenance costs drop over time.
Are there special installation or maintenance requirements?
Installation follows standard refractory material procedures. Proper alignment ensures optimal performance. Minimal maintenance is needed. Regular inspections check for surface wear or damage. Cleaning removes debris to prevent operational interference.
What factors influence the cost of customized ceramic plates?
Cost depends on customization complexity. Order size affects pricing. Higher purity raw materials increase expenses. Advanced processing techniques may raise costs. Bulk orders often reduce per-unit prices. Competitive pricing balances quality and budget needs.
(OEM Customized Refractory Material Industrial Furnace Sintered Silicon Carbide Ceramic Plate)
REQUEST A QUOTE
RELATED PRODUCTS
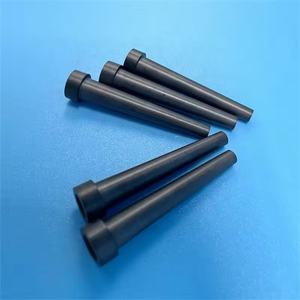
Silicon Carbide Boron Carbide Alumina Ceramic Armor Plate
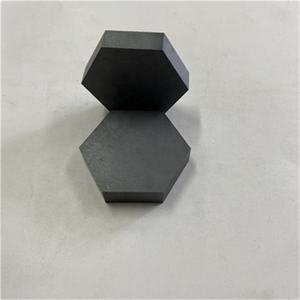
High Temperature Black Zirconia Manufacture Lab Precision Ceramic Parts Silicon Carbide Ceramics
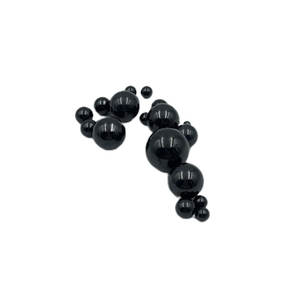
High Impact Resistance Sic Silicon Carbide Ceramic Rectangle Block for
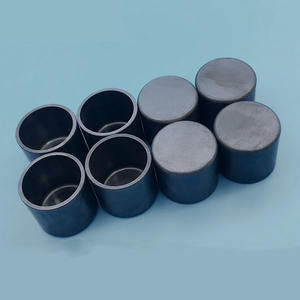
Refractory SSiC Sintered Silicon Carbide Ceramic Plates SiC Kiln Plate
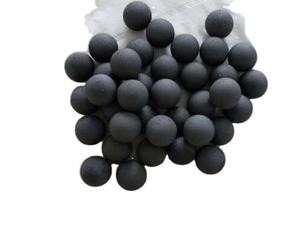
High Quality and High-temperature Resistant Silicon Carbide Ceramic Plate and Sic Plate
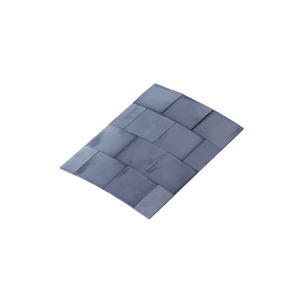