Discover Premium Ceramic Products | Durability & Elegance United | Advanced Ceramics
PRODUCT PARAMETERS
Description
Overview of Silicon Carbide Ceramics
Silicon Carbide (SiC) ceramics are renowned for their outstanding mechanical properties, including high hardness, strength at elevated temperatures, and excellent thermal shock resistance. These materials are pivotal in cutting-edge industrial applications, from abrasives to aerospace components, due to their unique combination of properties.
Features of Silicon Carbide Ceramics
High Hardness: Exceptional wear resistance.
Thermal Shock Resistance: Can withstand rapid temperature changes.
Chemical Stability: Resistant to most chemicals.
High Thermal Conductivity: Efficient heat dissipation.
Low Density: Lightweight for its strength.
(OEM Thermal Shock Resistance Advanced Ceramic Silicon Carbide SiC/SISIC Parts Components)
Specification of OEM Thermal Shock Resistance Advanced Ceramic Silicon Carbide SiC/SISIC Parts Components
OEM Thermal Shock Resistance Advanced Porcelain Silicon Carbide (SiC/SiSiC) parts provide high-performance options for extreme atmospheres. These parts manage fast temperature shifts without splitting. They suit industries needing products that endure intense thermal stress and anxiety. The material make-up incorporates silicon carbide with sintered silicon carbide (SiSiC). This mix increases stamina and thermal security.
Secret specifications consist of a maximum operating temperature of 1650 ° C. Thermal conductivity ranges in between 120-200 W/m · K. The low thermal growth coefficient (4.0 x10 ⁻⁶/ ° C) minimizes form adjustments under heat. Mechanical strength stays high, with flexural stamina getting to 400-600 MPa. Hardness matches 2500-2800 kgf/mm ² (Vickers). These characteristics make sure resistance to use, abrasion, and contortion.
The components resist chemical corrosion from acids, antacid, and molten metals. This makes them ideal for harsh industrial setups. Electrical conductivity alternatives exist for applications requiring antistatic homes. Surface surfaces can be tailored for smoothness or texture. Resistances fulfill ± 0.5% of measurements. Custom forms, sizes, and geometries are offered.
Applications span aerospace, energy, metallurgy, and semiconductor sectors. Use cases consist of furnace parts, heat exchangers, and turbine blades. They work in kiln furnishings, heater nozzles, and wear-resistant liners. The components minimize downtime by lasting longer than conventional ceramics or metals.
Production makes use of innovative sintering and machining strategies. These approaches ensure accurate measurements and regular top quality. OEM services support tailored designs for specific machinery or processes. Prototyping and bulk orders are accommodated. Evaluating includes thermal biking, stress resistance, and tons capability checks.
Advantages consist of minimized maintenance prices and improved operational effectiveness. The parts operate accurately in problems where metals or polymers stop working. Modification ensures compatibility with existing systems. Performance data is provided for assimilation preparation.
The product’s light-weight nature lowers power intake in relocating components. Compatibility with vacuum and high-pressure atmospheres increases use. No additional layers are needed for a lot of harsh setups. Long-lasting stability protects against efficiency destruction gradually.
(OEM Thermal Shock Resistance Advanced Ceramic Silicon Carbide SiC/SISIC Parts Components)
Applications of OEM Thermal Shock Resistance Advanced Ceramic Silicon Carbide SiC/SISIC Parts Components
OEM thermal shock resistance progressed ceramic silicon carbide (SiC/SiSiC) components are engineered to carry out in extreme temperature level settings. These products take care of quick temperature level changes without splitting or shedding architectural stability. Industries like metallurgy, aerospace, energy, and vehicle count on them for high-stress applications.
In metallurgy, SiC/SiSiC components are made use of in heating systems, crucibles, and heating elements. They withstand temperatures over 1600 ° C while standing up to thermal fatigue. This makes sure longer service life contrasted to typical steels. The low thermal growth of silicon carbide prevents deformation during duplicated home heating and cooling down cycles.
Aerospace applications consist of turbine blades, nozzles, and heat shields. These parts face extreme warmth throughout propulsion or re-entry. SiC/SiSiC products maintain strength at heats. They lower weight contrasted to metal alloys, improving fuel performance. Their resistance to oxidation and corrosion includes integrity in harsh operating problems.
Power markets use SiC/SiSiC parts in atomic power plants, solar thermal systems, and gas wind turbines. In nuclear atmospheres, they supply radiation resistance and stability under thermal stress and anxiety. Solar energy systems benefit from their capacity to take in and transfer warmth effectively. Gas turbines with SiC components accomplish higher operating temperature levels, boosting power output.
Automotive makers integrate these ceramics right into brake systems, exhaust components, and engine components. High-performance cars call for materials that withstand fast warmth changes. SiC-based brake discs supply better warm dissipation than conventional products. Exhaust systems making use of SiC/SiSiC decrease discharges by managing higher combustion temperature levels.
Modification for OEM needs is a crucial advantage. Producers customize measurements, finishes, and composite frameworks to fit certain applications. This flexibility makes sure optimum performance throughout different markets. The sturdiness of SiC/SiSiC parts decreases maintenance expenses and downtime. Their combination of thermal security, mechanical stamina, and chemical resistance makes them important for advanced design options.
Company Introduction
Advanced Ceramics founded on October 17, 2014, is a high-tech enterprise committed to the research and development, production, processing, sales and technical services of ceramic relative materials and products.. Since its establishment in 2014, the company has been committed to providing customers with the best products and services, and has become a leader in the industry through continuous technological innovation and strict quality management.
Our products includes but not limited to Silicon carbide ceramic products, Boron Carbide Ceramic Products, Boron Nitride Ceramic Products, Silicon Carbide Ceramic Products, Silicon Nitride Ceramic Products, Zirconium Dioxide Ceramic Products, Quartz Products, etc. Please feel free to contact us.(nanotrun@yahoo.com)
Payment Methods
T/T, Western Union, Paypal, Credit Card etc.
Shipment Methods
By air, by sea, by express, as customers request.
5 FAQs of OEM Thermal Shock Resistance Advanced Ceramic Silicon Carbide SiC/SISIC Parts Components
What makes silicon carbide parts good for thermal shock resistance?
Silicon carbide (SiC) has low thermal expansion and high thermal conductivity. Heat spreads quickly through the material. Sudden temperature changes cause less stress. This reduces cracking or damage. SiC parts handle extreme heat shifts better than metals or other ceramics.
Where are SiC/SiSiC parts commonly used?
These parts work in harsh environments. Examples include aerospace engines, industrial furnaces, and semiconductor manufacturing. High-temperature zones need materials that stay stable. SiC components last longer in these conditions. They also fit energy systems like gas turbines and heat exchangers.
How do SiC and SiSiC differ?
SiC is pure silicon carbide. SiSiC combines silicon carbide with silicon metal. The added silicon fills tiny gaps in the structure. This makes SiSiC easier to produce in complex shapes. Pure SiC offers slightly better heat resistance. SiSiC improves mechanical strength for certain applications.
Can these parts withstand chemical exposure?
Yes. Silicon carbide resists acids, alkalis, and molten metals. It does not corrode easily. This makes it ideal for chemical processing equipment. Parts stay durable in aggressive environments. Oxidation resistance also prevents degradation at high temperatures.
Are custom shapes and sizes possible?
Manufacturers use advanced molding and machining to create custom designs. CNC grinding ensures precise dimensions. Complex geometries meet specific engineering needs. Production scales from prototypes to large batches. Testing confirms each part meets performance standards.
(OEM Thermal Shock Resistance Advanced Ceramic Silicon Carbide SiC/SISIC Parts Components)
REQUEST A QUOTE
RELATED PRODUCTS
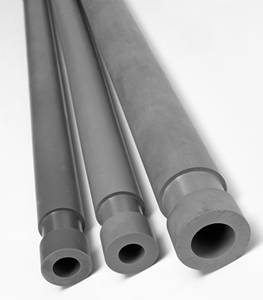
Long fiber CCB silicon carbide coated carbon ceramic disc for Audi R35 Gtr Gt63 bmw X3 X4 X5 f30 350i
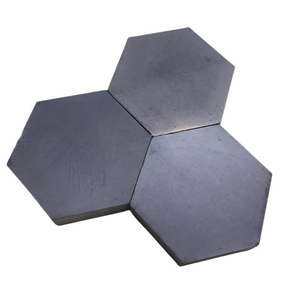
Custom Processing SIC Silicon Carbide Ceramic Strip Article for Industry Ceramic Parts SISIC Rods
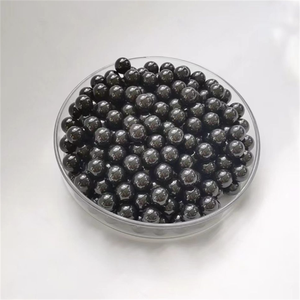
High Quality Ceramic Flap Disc Aluminium Oxid Wheel Abrasive Flap Disc OEM for Grinding Silicon Carbide Aluminum Oxide Steel
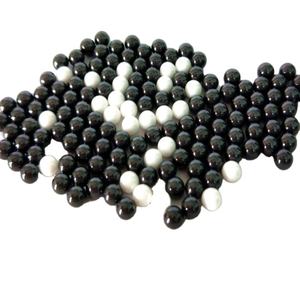
High Temperature Silicon Carbide Ceramic Ring Wear and Corrosion Resistant Insert for Industrial Mechanical Parts
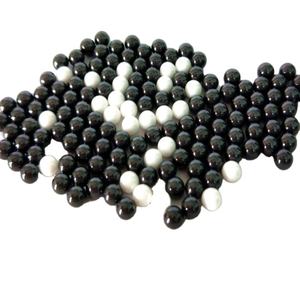
SiC, Silicon Carbide Ceramic Ring, High-performance Ceramic Parts, Customized
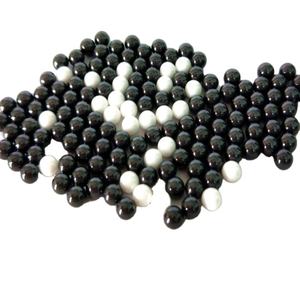