Discover Premium Ceramic Products | Durability & Elegance United | Advanced Ceramics
PRODUCT PARAMETERS
Description
Overview of Silicon Carbide Ceramics
Silicon Carbide (SiC) ceramics are renowned for their outstanding mechanical properties, including high hardness, strength at elevated temperatures, and excellent thermal shock resistance. These materials are pivotal in cutting-edge industrial applications, from abrasives to aerospace components, due to their unique combination of properties.
Features of Silicon Carbide Ceramics
High Hardness: Exceptional wear resistance.
Thermal Shock Resistance: Can withstand rapid temperature changes.
Chemical Stability: Resistant to most chemicals.
High Thermal Conductivity: Efficient heat dissipation.
Low Density: Lightweight for its strength.
(SiC, Silicon Carbide Ceramic Ring, High-performance Ceramic Parts, Customized)
Specification of SiC, Silicon Carbide Ceramic Ring, High-performance Ceramic Parts, Customized
Silicon Carbide (SiC) ceramic rings are high-performance elements designed for requiring industrial applications. These rings integrate extraordinary product residential properties with precision engineering. The primary material is silicon carbide, known for extreme hardness, thermal security, and resistance to wear. Secret specifications include a density of 3.1-3.2 g/cm THREE, a hardness score of 9.5 on the Mohs scale, and a maximum operating temperature of 1650 ° C. The thermal conductivity is high, getting to 120 W/m · K, ensuring efficient warmth dissipation in high-temperature settings.
The chemical resistance of SiC ceramic rings is superior. They stand up to corrosive acids, antacid, and rough media. This makes them perfect for usage in chemical handling, semiconductor production, and harsh industrial settings. Mechanical stamina is one more vital function. The flexural toughness exceeds 400 MPa, and compressive strength exceeds 2000 MPa. These properties ensure long-term longevity under heavy loads.
Customization choices are offered to fulfill certain application requirements. Rings can be generated in diameters from 10 mm to 500 mm, with tolerances as limited as ± 0.01 mm. Surface area coatings are adjustable, varying from common polished to ultra-smooth structures for specialized usages. Grooves, holes, or special geometries are included based on customer requirements.
High-performance ceramic components made from SiC offer benefits over conventional materials. They outshine steels in high-temperature scenarios, avoiding deformation or oxidation. Compared to alumina or zirconia porcelains, SiC supplies much better thermal shock resistance. This permits quick temperature changes without fracturing.
Applications span numerous markets. In aerospace, SiC rings offer in generator elements and seals. Automotive systems utilize them for bearings and brake components. Energy fields deploy these rings in pump seals and activator elements. Electronic devices take advantage of their electrical insulation and warm monitoring buildings.
Manufacturing makes use of innovative methods like pressureless sintering or reaction bonding. These strategies make certain consistent microstructure and regular efficiency. Quality control consists of dimensional checks, thickness examinations, and x-ray inspection. Every set satisfies worldwide criteria for commercial porcelains.
Custom-made SiC services reduce downtime and maintenance costs. Engineers function carefully with clients to enhance styles for details operating problems. Material qualities are selected based on thermal, chemical, or mechanical concerns. This tailored strategy guarantees integrity in essential applications.
(SiC, Silicon Carbide Ceramic Ring, High-performance Ceramic Parts, Customized)
Applications of SiC, Silicon Carbide Ceramic Ring, High-performance Ceramic Parts, Customized
Silicon Carbide (SiC) ceramic rings stick out as high-performance parts in demanding commercial setups. Their distinct residential properties make them perfect for applications where extreme conditions challenge traditional products. These porcelains master taking care of heats, resisting wear, and maintaining security under mechanical tension. Industries like aerospace, auto, and power rely on SiC rings for crucial operations.
In industrial machinery, SiC ceramic rings act as seals, bearings, and nozzles. They do reliably in environments with intense warm or harsh chemicals. Their reduced thermal expansion guarantees very little form modifications throughout temperature level shifts. This lowers downtime and upkeep expenses. Automotive systems use SiC rings in brake parts and engine parts. Their light-weight nature boosts fuel efficiency without sacrificing toughness.
The energy industry take advantage of SiC’s electrical conductivity and thermal administration. Solar inverters, wind generators, and power grids use these ceramics to improve efficiency. SiC parts stand up to high voltages and reduce energy loss. Semiconductor production utilizes SiC rings in wafer handling. Their resistance to plasma erosion expands tools life in cleanroom settings.
Personalized SiC ceramic parts address specialized needs across industries. Suppliers customize dimensions, surface area coatings, and material qualities to match particular applications. Custom-made shapes or finishings enhance efficiency in distinct setups. For example, clinical tools use precision-machined SiC elements for imaging systems. The ability to modify residential or commercial properties like porosity or hardness ensures compatibility with varied operational demands.
High-performance ceramics like SiC rings surpass metals and polymers in extreme problems. They withstand oxidation, chain reactions, and rough wear. This long life makes them cost-efficient in spite of greater preliminary expenses. Advancements in sintering strategies have actually broadened style opportunities. Complex geometries and tighter resistances are now achievable.
Need for SiC ceramics grows as markets focus on efficiency and sustainability. Their role in electrical automobiles, renewable energy, and advanced production highlights their adaptability. Customized options drive adoption in niche markets. Designers increasingly pick SiC for jobs needing reliability under stress.
Company Introduction
Advanced Ceramics founded on October 17, 2014, is a high-tech enterprise committed to the research and development, production, processing, sales and technical services of ceramic relative materials and products.. Since its establishment in 2014, the company has been committed to providing customers with the best products and services, and has become a leader in the industry through continuous technological innovation and strict quality management.
Our products includes but not limited to Silicon carbide ceramic products, Boron Carbide Ceramic Products, Boron Nitride Ceramic Products, Silicon Carbide Ceramic Products, Silicon Nitride Ceramic Products, Zirconium Dioxide Ceramic Products, Quartz Products, etc. Please feel free to contact us.(nanotrun@yahoo.com)
Payment Methods
T/T, Western Union, Paypal, Credit Card etc.
Shipment Methods
By air, by sea, by express, as customers request.
5 FAQs of SiC, Silicon Carbide Ceramic Ring, High-performance Ceramic Parts, Customized
What is Silicon Carbide (SiC)?
Silicon Carbide is a ceramic material made from silicon and carbon. It has high hardness, thermal conductivity, and resistance to heat and corrosion. These properties make it suitable for demanding industrial applications.
Why choose SiC ceramic rings over metal or plastic parts?
SiC ceramic rings handle extreme temperatures and harsh chemicals better than metals or plastics. They wear down slower, last longer, and reduce maintenance costs. They perform reliably in high-stress environments where other materials fail.
What industries use high-performance SiC ceramic parts?
Industries like aerospace, automotive, energy, and semiconductor manufacturing rely on SiC parts. They are used in pumps, seals, bearings, and cutting tools. Their stability under heat and corrosion makes them ideal for machinery exposed to tough conditions.
Can SiC ceramic parts be customized?
Yes. Manufacturers offer custom shapes, sizes, and surface finishes. Precision machining ensures parts meet exact specifications. Customization allows integration into existing systems without redesigning equipment.
How do SiC ceramics handle high-temperature environments?
SiC ceramics maintain strength and shape at temperatures over 1600°C. They resist thermal shock, meaning sudden temperature changes cause minimal damage. This makes them suitable for furnaces, turbines, and other high-heat applications.
(SiC, Silicon Carbide Ceramic Ring, High-performance Ceramic Parts, Customized)
REQUEST A QUOTE
RELATED PRODUCTS
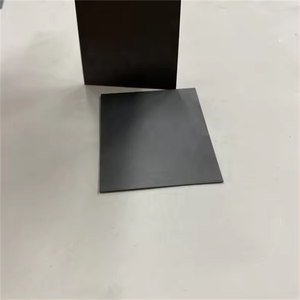
Customized Hexagonal Boron Carbide Silicon Carbide Ceramic Plate Tiles SIC Ceramic for Industrial Use Welding Cutting Services
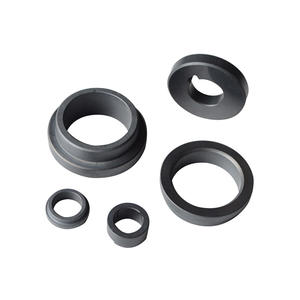
Square Silicon Carbide Ceramic Foam Filter Plate Sic Honeycomb Ceramic
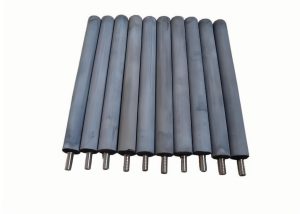
Silicon Carbide Rod High Hardness And High Strength SiC Rod
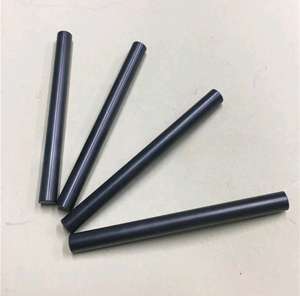
Refractory Nitride Bonded Silicon Carbide Sintered Sanitary Ware NSIC Ceramic Kiln Shelves
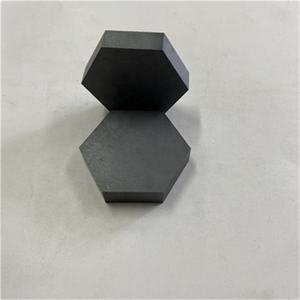
Polished Wear-resistant Silicon Carbide Ceramic Rod Shaft/bar
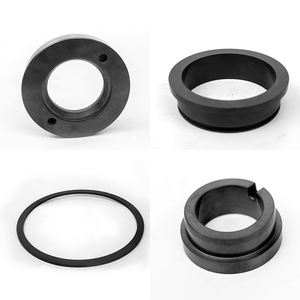