Discover Premium Ceramic Products | Durability & Elegance United | Advanced Ceramics
PRODUCT PARAMETERS
Description
Overview of Silicon Nitride Ceramics
Silicon Nitride Ceramics are high-performance materials known for their excellent mechanical properties, including strength, toughness, and resistance to wear, corrosion, and thermal shock, making them ideal for demanding applications in various industries.
Features of Silicon Nitride Ceramics
Exceptional hardness and wear resistance.
Superior mechanical strength and fracture toughness.
Excellent thermal stability and resistance to thermal shock.
High corrosion resistance in aggressive environments.
Low density contributing to lightweight components.
(Precision Ceramic Parts of Semiconductor Process Equipment Si3N4 Silicon Nitride Ceramic Substrate Plates Silicon Nitride)
Specifications of Precision Ceramic Parts of Semiconductor Process Equipment Si3N4 Silicon Nitride Ceramic Substrate Plates Silicon Nitride
Accuracy ceramic components for semiconductor procedure equipment are created for high-performance applications. The material utilized is Si3N4 silicon nitride ceramic substratum plates. Silicon nitride provides outstanding thermal security. It endures extreme temperature levels approximately 1,200 ° C without losing structural stability. This residential property is important in semiconductor manufacturing. High-temperature procedures like etching and deposition need materials that withstand thermal shock. Silicon nitride preserves stamina under fast temperature adjustments. Mechanical resilience is one more advantage. The material has high fracture strength. It resists wear and abrasion in extreme operating settings. Chemical resistance is necessary for semiconductor devices. Silicon nitride executes well versus harsh gases and plasmas. It avoids contamination in cleanroom settings. Surface area finish high quality is precise. Substrate plates have ultra-smooth surfaces. This minimizes fragment generation during wafer processing. Dimensional accuracy is snugly controlled. Tolerances satisfy strict sector criteria for monotony and density. Consistency makes sure trusted integration right into tools. Customized shapes and sizes are available. Components like insulators, heaters, and susceptors are tailored to details tooling demands. Electrical insulation residential properties are exceptional. Silicon nitride prevents current leak in high-voltage applications. Thermal conductivity is modest. It stabilizes heat dissipation and thermal management needs. Lengthy service life lowers devices downtime. Substitute cycles are extended compared to steel or polymer choices. Compatibility with vacuum cleaner settings is confirmed. Outgassing rates are negligible. This maintains vacuum integrity in procedure chambers. Applications include wafer handling robotics, plasma-resistant parts, and chamber liners. Semiconductor suppliers rely on silicon nitride for procedure stability. Efficiency metrics line up with market demands for accuracy and dependability.
(Precision Ceramic Parts of Semiconductor Process Equipment Si3N4 Silicon Nitride Ceramic Substrate Plates Silicon Nitride)
Applications of Precision Ceramic Parts of Semiconductor Process Equipment Si3N4 Silicon Nitride Ceramic Substrate Plates Silicon Nitride
Precision ceramic parts play an important role in semiconductor process devices. Silicon nitride (Si3N4) ceramic substratum plates attract attention because of their one-of-a-kind properties. These components manage extreme problems in semiconductor production. They make certain high performance and integrity in innovative processes.
Silicon nitride offers excellent thermal security. It resists contortion under heats common in semiconductor devices. This residential property stops tools failure during rapid home heating or cooling cycles. The material maintains architectural honesty also above 1000 ° C. This makes it excellent for high-temperature phases like wafer annealing or diffusion.
Chemical resistance is another crucial advantage. Silicon nitride endures destructive gases and plasmas utilized in etching or deposition. It stays clear of deterioration when subjected to hostile chemicals like fluorides or chlorides. This prolongs the life expectancy of procedure chambers and lowers contamination dangers.
Mechanical stamina matters in semiconductor tools. Silicon nitride ceramic substratum plates are highly durable. They resist use from friction or fragment effect during wafer handling. Their hardness protects against scrapes on delicate surfaces. This guarantees consistent performance in robot arms or vacuum cleaner chucks.
Electric insulation properties are crucial. Silicon nitride stops present leakage in high-voltage atmospheres. It supports exact control in plasma generation or ion implantation. This security boosts process precision and repeatability.
Silicon nitride ceramic components are made use of in numerous semiconductor tools. They work as heating system plates, showerheads, or susceptors in CVD and ALD systems. Their reduced thermal growth matches silicon wafers, lowering tension throughout handling. This alignment reduces defects in final products.
The product’s light-weight nature aids devices layout. It enables faster activity in automated systems without compromising durability. This enhances throughput in construction lines.
Silicon nitride’s purity satisfies semiconductor sector requirements. It avoids introducing contaminations into delicate procedures. This is important for creating high-grade chips with nanometer-scale attributes.
Semiconductor suppliers rely on silicon nitride ceramic parts for effectiveness. The material’s mix of thermal, chemical, and mechanical residential or commercial properties guarantees reliable procedure. It supports the growth of next-generation electronic devices by enabling innovative manufacture strategies.
Company Introduction
Advanced Ceramics founded on October 17, 2014, is a high-tech enterprise committed to the research and development, production, processing, sales and technical services of ceramic relative materials and products.. Since its establishment in 2014, the company has been committed to providing customers with the best products and services, and has become a leader in the industry through continuous technological innovation and strict quality management.
Our products includes but not limited to Silicon carbide ceramic products, Boron Carbide Ceramic Products, Boron Nitride Ceramic Products, Silicon Carbide Ceramic Products, Silicon Nitride Ceramic Products, Zirconium Dioxide Ceramic Products, Quartz Products, etc. Please feel free to contact us.(nanotrun@yahoo.com)
Payment Methods
T/T, Western Union, Paypal, Credit Card etc.
Shipment Methods
By air, by sea, by express, as customers request.
5 FAQs of Precision Ceramic Parts of Semiconductor Process Equipment Si3N4 Silicon Nitride Ceramic Substrate Plates Silicon Nitride
Semiconductor process equipment relies on precision ceramic parts. Silicon nitride (Si3N4) ceramic substrate plates are widely used. Below are 5 FAQs about these components.
1. Why choose silicon nitride ceramic plates for semiconductor equipment?
Silicon nitride handles high heat and rapid temperature changes. It resists corrosion from harsh chemicals in etching or deposition processes. The material’s strength prevents cracks under mechanical stress. This ensures stable performance in vacuum or high-pressure environments.
2. What key properties make silicon nitride suitable?
The ceramic has excellent thermal conductivity. It minimizes heat buildup during processes. Its low thermal expansion matches silicon wafers. This reduces alignment errors. Silicon nitride also resists wear. This extends the lifespan of parts like wafer chucks or susceptors.
3. Are there handling precautions for these plates?
Avoid dropping or impacting the plates. Chips or cracks affect performance. Clean surfaces with compatible solvents. Do not use abrasive tools. Store plates in dry environments. Moisture can cause contamination in sensitive processes.
4. How does silicon nitride compare to alumina or zirconia?
Silicon nitride performs better under thermal stress. It lasts longer in cyclic heating-cooling conditions. Alumina cracks faster in extreme temperatures. Zirconia has lower thermal conductivity. Silicon nitride’s strength-to-weight ratio is higher. This suits high-speed semiconductor machinery.
5. Can these plates be customized for specific tools?
Yes. Manufacturers adjust dimensions, hole patterns, or surface finishes. Tolerances reach ±0.01mm for precision fit. Coatings like diamond-like carbon (DLC) add extra protection. Share tool specifications early. This ensures compatibility with deposition chambers or etching systems.
Silicon nitride ceramic plates meet strict semiconductor industry demands. Proper selection and care optimize process efficiency.
(Precision Ceramic Parts of Semiconductor Process Equipment Si3N4 Silicon Nitride Ceramic Substrate Plates Silicon Nitride)
REQUEST A QUOTE
RELATED PRODUCTS
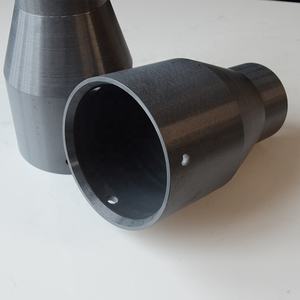
Wear-resistant Si3N4 / Silicon Nitride Ceramic Plate / Block / Sheet
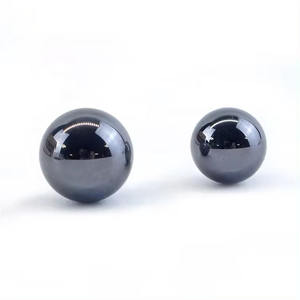
Silicon Nitride Ceramic Sheet Ultrathin Substrate Si3n4 Silicon Nitride Ceramic Plate
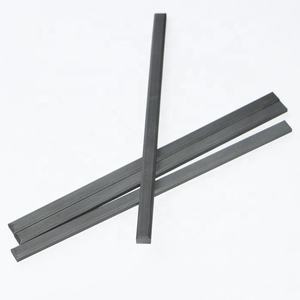
Ultra Thin Customized Black Silicon Nitride Si3N4 Ceramic Substrate Sheet mm Grade
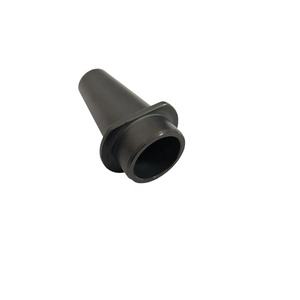
High Precision G5 G10 Silicon Nitride Ceramic Bearing Ball
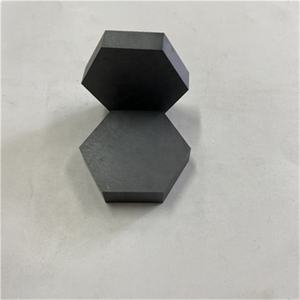
Customized Wear-Resistant and High-Temperature Resistant Precision Si3n4 Silicon Nitride Ceramic Parts Processing
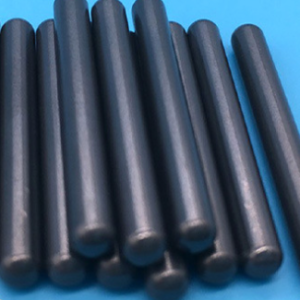