Discover Premium Ceramic Products | Durability & Elegance United | Advanced Ceramics
PRODUCT PARAMETERS
Description
Overview of Zirconium Dioxide Ceramics
Zirconium Dioxide Ceramics, known for their toughness and ability to withstand extreme temperatures, are widely used in medical, automotive, and industrial applications due to their unique properties.
Features of Zirconium Dioxide Ceramics
Exceptional fracture toughness
High thermal expansion
Excellent resistance to wear and corrosion
Biocompatibility for medical implants
(95% 99% 99.5% 99.6% 99.8% Al2O3 Alumina Zirconia ZTA Ceramic Piece Sheet Substrate High Quality)
Specifications of 95% 99% 99.5% 99.6% 99.8% Al2O3 Alumina Zirconia ZTA Ceramic Piece Sheet Substrate High Quality
This product offers ceramic items, sheets, and substrates made from alumina (Al2O3) and zirconia-toughened alumina (ZTA) in varying purity degrees: 95%, 99%, 99.5%, 99.6%, and 99.8%. These materials combine high-performance residential properties for commercial and technological applications. Alumina offers outstanding hardness, use resistance, and thermal stability. Zirconia includes durability, enhancing fracture resistance and durability. The result is a ceramic item ideal for demanding settings.
The 95% alumina quality balances expense and efficiency. It matches general-purpose usages like wear-resistant linings or insulating elements. Higher pureness qualities (99% and above) deliver enhanced efficiency. They reveal much better thermal conductivity, electric insulation, and resistance to deterioration. These grades function well in high-temperature heating systems, semiconductor manufacturing, or medical tools. The 99.8% alumina variant master severe conditions due to minimal pollutants. It maintains architectural honesty under extended heat or chemical exposure.
ZTA porcelains blend alumina with zirconia (typically 10-20%). This mix boosts toughness without compromising hardness. ZTA parts take care of hefty mechanical stress and anxiety much better than standard alumina. They are made use of in reducing devices, bearings, or aerospace parts. All ceramic sheets and substratums are available in thicknesses from 0.5 mm to 50mm. Custom sizes and shapes are sustained. Surface area coatings vary from as-sintered to polished, satisfying accuracy needs for electronic devices or optical applications.
These ceramics resist temperature levels approximately 1600 ° C. They remain stable in acidic or alkaline atmospheres. Electric insulation properties make them appropriate for circuit substrates or sensor real estates. Each set goes through extensive testing. Thickness, solidity, and dimensional precision are confirmed. X-ray and ultrasonic examinations make certain defect-free materials.
The item fulfills global requirements for industrial porcelains. It serves markets like automotive, energy, and chemical handling. Engineers select these porcelains for integrity under stress, warmth, or use. Custom setups are offered for specialized needs. The product’s versatility supports technologies in modern technology and production.
Quality control warranties uniformity across all purity degrees. Basic material are sourced from certified vendors. Advanced sintering methods maximize microstructure. This makes sure uniform homes in every ceramic item. Performance data and technical support are given to aid consumers select the best quality. The emphasis continues to be on providing long lasting, premium services for important applications.
(95% 99% 99.5% 99.6% 99.8% Al2O3 Alumina Zirconia ZTA Ceramic Piece Sheet Substrate High Quality)
Applications of 95% 99% 99.5% 99.6% 99.8% Al2O3 Alumina Zirconia ZTA Ceramic Piece Sheet Substrate High Quality
Alumina (Al2O3) ceramic materials with purity degrees like 95%, 99%, 99.5%, 99.6%, and 99.8% are widely made use of in sectors requiring high efficiency. These ceramics handle extreme conditions. Alumina at 95% purity is common in industrial wear-resistant parts. It stands up to abrasion in machinery parts like seals and linings. Greater pureness alumina (99% and over) works in electronics. It functions as substrates for circuits as a result of its electrical insulation and thermal conductivity.
Zirconia (ZrO2) ceramics include toughness. They stop splits from dispersing. This makes them optimal for medical tools like dental implants. They are biocompatible and resilient. Zirconia components additionally operate in cutting devices. They stay sharp under heavy use.
ZTA (Zirconia Toughened Alumina) incorporates alumina’s solidity with zirconia’s fracture resistance. This mix matches applications needing both strength and resilience. ZTA is utilized in auto elements. Examples consist of engine components exposed to high warmth and rubbing.
Ceramic sheets and substrates made from these products satisfy strict top quality standards. They are flat and smooth. This makes sure reputable performance in accuracy tools. High-purity alumina sheets (99.6% or 99.8%) are vital in semiconductor manufacturing. They take care of high temperatures during chip production.
These porcelains withstand chemicals. They do not corrode in extreme settings. This makes them ideal for chemical handling equipment. Valves and pumps made from alumina or zirconia last longer.
Medical devices gain from alumina’s security. Surgical instruments made with 99.5% alumina keep sterilized. They hold up against duplicated sterilization cycles. Zirconia’s tooth-like shade makes it popular in oral crowns. It looks natural and resists wear.
The aerospace industry uses these ceramics for lightweight, heat-resistant parts. Elements like generator blades deal with extreme temperature levels. Alumina and zirconia maintain toughness without including weight.
Customized ceramic items are readily available in numerous forms. Sheets, rods, and tubes can be machined to accurate dimensions. This adaptability sustains specialized commercial requirements.
Quality assurance makes sure uniformity. Each batch is evaluated for thickness and purity. This assures dependability in critical applications.
High-performance porcelains are affordable over time. Their toughness decreases replacement regularity. Industries save money on maintenance while improving efficiency.
Company Introduction
Advanced Ceramics founded on October 17, 2014, is a high-tech enterprise committed to the research and development, production, processing, sales and technical services of ceramic relative materials and products.. Since its establishment in 2014, the company has been committed to providing customers with the best products and services, and has become a leader in the industry through continuous technological innovation and strict quality management.
Our products includes but not limited to Silicon carbide ceramic products, Boron Carbide Ceramic Products, Boron Nitride Ceramic Products, Silicon Carbide Ceramic Products, Silicon Nitride Ceramic Products, Zirconium Dioxide Ceramic Products, Quartz Products, etc. Please feel free to contact us.(nanotrun@yahoo.com)
Payment Methods
T/T, Western Union, Paypal, Credit Card etc.
Shipment Methods
By air, by sea, by express, as customers request.
5 FAQs of 95% 99% 99.5% 99.6% 99.8% Al2O3 Alumina Zirconia ZTA Ceramic Piece Sheet Substrate High Quality
What purity levels do these ceramic substrates offer? The ceramic substrates come in 95%, 99%, 99.5%, 99.6%, and 99.8% Al2O3 purity grades. Higher purity means better performance in high-temperature or corrosive environments. Lower grades balance cost and function for less demanding uses. Each grade suits specific industrial needs based on durability and resistance requirements.
How does alumina differ from zirconia in these ceramics? Alumina (Al2O3) offers high hardness and thermal stability. Zirconia adds toughness and crack resistance. Alumina-zirconia composites (ZTA) combine both strengths. The choice depends on whether hardness, durability, or stress resistance is prioritized. ZTA is ideal for heavy wear applications.
What is ZTA ceramic? ZTA stands for zirconia-toughened alumina. It mixes alumina’s hardness with zirconia’s fracture resistance. This hybrid material handles extreme mechanical stress better than pure alumina. It’s used in cutting tools, medical implants, and industrial wear parts. The blend improves lifespan under harsh conditions.
Where are these ceramics typically applied? These substrates work in electronics, machinery, medical devices, and aerospace. High-purity alumina insulates circuits or resists corrosion in chemical plants. Zirconia parts are used in pumps, valves, or joint replacements. ZTA suits high-stress roles like mining equipment or cutting blades.
How is quality ensured for these ceramics? Quality checks include density tests, X-ray analysis, and microstructure exams. Each batch undergoes strength, hardness, and thermal shock tests. Certifications like ISO 9001 confirm consistency. Precise manufacturing controls minimize defects. This ensures reliability for critical industrial applications.
(95% 99% 99.5% 99.6% 99.8% Al2O3 Alumina Zirconia ZTA Ceramic Piece Sheet Substrate High Quality)
REQUEST A QUOTE
RELATED PRODUCTS
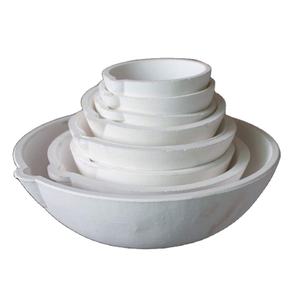
Zirconium Powder Ceramic Industries Grade Monoclinic Zirconia Powder For Insert
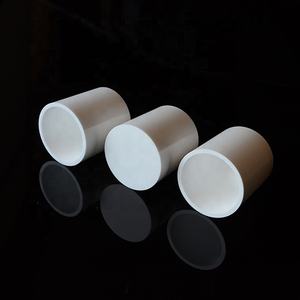
Professional High Quality Advanced Pure Zirconia Structural Ceramics ZrO2 Industrial Ceramic Parts
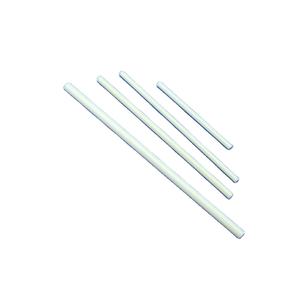
Customized Zirconia Structural Ceramics/zirconia Ceramic Sealing Rings/high Wear Resistant Ceramic Components
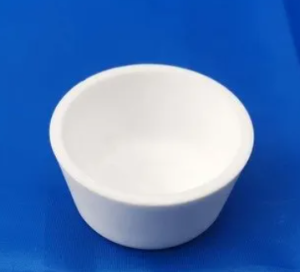
ZrO2 Zirconia Sintering Ceramic Crucible
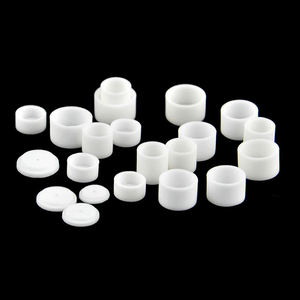
Black Precision yttria stabilized zirconium Plate Zirconia oxide/ZrO2 Ceramic Sheet
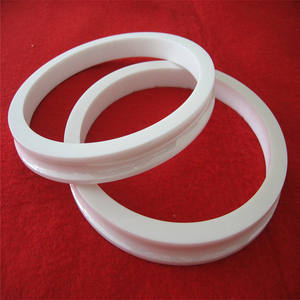