Discover Premium Ceramic Products | Durability & Elegance United | Advanced Ceramics
PRODUCT PARAMETERS
Description
Overview of Zirconium Dioxide Ceramics
Zirconium Dioxide Ceramics, known for their toughness and ability to withstand extreme temperatures, are widely used in medical, automotive, and industrial applications due to their unique properties.
Features of Zirconium Dioxide Ceramics
Exceptional fracture toughness
High thermal expansion
Excellent resistance to wear and corrosion
Biocompatibility for medical implants
(Custom Industrial High Precision High Hardness Polish Zirconia Ceramic Parts Zirconium Oxide Ceramic)
Specifications of Custom Industrial High Precision High Hardness Polish Zirconia Ceramic Parts Zirconium Oxide Ceramic
Customized Industrial High Accuracy High Hardness Polish Zirconia Porcelain Parts are engineered for demanding applications calling for longevity, precision, and resistance to severe problems. Made from zirconium oxide ceramic, these components integrate remarkable mechanical buildings with tight manufacturing resistances. The product uses a Vickers hardness of over 1200 HV, making it harder than numerous metals and perfect for wear-prone environments. Its high fracture durability lowers fracturing under anxiety, making certain lasting integrity.
These ceramic parts operate successfully in temperatures as much as 1500 ° C, maintaining structural security in high-heat settings. They resist chemical rust from acids, alkalis, and solvents, suitable for hostile commercial environments. The low thermal conductivity of zirconia decreases warmth transfer, beneficial in thermal insulation applications.
Precision machining guarantees dimensional accuracy, with resistances as tight as ± 0.001 mm. Advanced grinding and brightening methods attain surface finishes down to Ra 0.01 μm, vital for reducing rubbing and protecting against contamination in delicate systems. Elements consist of rods, tubes, plates, and complex custom-made geometries, customized to specific equipment or tooling requirements.
Applications extend aerospace, medical gadgets, auto, and semiconductor manufacturing. Typical uses consist of accuracy shutoffs, bearings, cutting tools, pump seals, and implantable medical components. The material’s biocompatibility meets medical market requirements for security in body call.
Modification choices cover size, shape, opening patterns, and surface area therapies. Coatings like diamond-like carbon (DLC) enhance wear resistance. Laser engraving or metallization includes practical or identification attributes. Components undertake strenuous quality checks, consisting of dimensional verification with CMM makers and material purity testing by means of XRD analysis.
Production adheres to ISO 9001 requirements, guaranteeing consistency and traceability. Basic material are sourced from certified suppliers, guaranteeing high-purity zirconia powder. Final components fulfill RoHS and REACH compliance for global market availability.
The combination of high hardness, thermal stability, and accuracy machining makes these zirconia ceramic components a practical solution for markets focusing on efficiency and longevity. Personalized orders suit models and large-scale production, with preparations maximized for urgent job requirements.
(Custom Industrial High Precision High Hardness Polish Zirconia Ceramic Parts Zirconium Oxide Ceramic)
Applications of Custom Industrial High Precision High Hardness Polish Zirconia Ceramic Parts Zirconium Oxide Ceramic
Custom-made commercial high-precision high-hardness polish zirconia ceramic parts made from zirconium oxide ceramic serve essential duties throughout multiple sectors. These parts excel in settings requiring durability, resistance to use, and security under severe problems. Their applications extend machinery, electronic devices, medical tools, aerospace, and auto markets.
In machinery production, zirconia ceramic parts manage high-stress operations. They replace typical metal parts in bearings, shutoffs, and reducing tools. Their high firmness reduces wear, extending tools life expectancy. The sleek surface area lessens friction, boosting performance in high-speed systems.
The electronics sector relies on these ceramics for insulating parts and semiconductor processing tools. Zirconia’s thermal stability prevents contortion throughout high-temperature processes. Its electric insulation properties make certain safety and security in circuits and sensing units. Accuracy sprucing up ensures smooth surface areas, critical for microelectronic applications.
Clinical gadgets use zirconia ceramic parts for implants and surgical tools. The material’s biocompatibility makes it secure for human contact. High firmness allows accurate machining for oral crowns and joint substitutes. Refined surface areas lower bacterial bond, improving hygiene in medical settings.
Aerospace applications benefit from zirconia’s resistance to extreme temperatures and rust. These components operate in jet engine components and satellite systems. They keep performance under quick thermal changes and mechanical tension. The lightweight nature of zirconia adds to fuel effectiveness in airplane.
Automotive systems incorporate zirconia porcelains in sensors, gas injectors, and engine components. They endure high-pressure problems and minimize wear in moving parts. The material’s thermal insulation residential or commercial properties enhance combustion efficiency. Polished surface areas ensure tight seals in fuel shipment systems.
Customization allows zirconia ceramic parts to satisfy precise specifications. Producers readjust measurements, shapes, and surface coatings for specialized requirements. Advanced sintering methods attain tight tolerances, making sure compatibility with complicated settings up. The combination of high solidity, accuracy, and adaptability makes zirconia ceramics a preferred option for industrial obstacles.
Company Introduction
Advanced Ceramics founded on October 17, 2014, is a high-tech enterprise committed to the research and development, production, processing, sales and technical services of ceramic relative materials and products.. Since its establishment in 2014, the company has been committed to providing customers with the best products and services, and has become a leader in the industry through continuous technological innovation and strict quality management.
Our products includes but not limited to Silicon carbide ceramic products, Boron Carbide Ceramic Products, Boron Nitride Ceramic Products, Silicon Carbide Ceramic Products, Silicon Nitride Ceramic Products, Zirconium Dioxide Ceramic Products, Quartz Products, etc. Please feel free to contact us.(nanotrun@yahoo.com)
Payment Methods
T/T, Western Union, Paypal, Credit Card etc.
Shipment Methods
By air, by sea, by express, as customers request.
5 FAQs of Custom Industrial High Precision High Hardness Polish Zirconia Ceramic Parts Zirconium Oxide Ceramic
What is zirconia ceramic?
Zirconia ceramic is a material made from zirconium oxide. It is known for high strength, toughness, and resistance to wear. It works well in extreme conditions like high temperatures, corrosion, or heavy friction. These properties make it ideal for industrial parts needing precision and durability.
Why choose zirconia ceramic parts over metal or plastic?
Zirconia ceramic lasts longer than metal or plastic in harsh environments. It does not rust, handles high heat better, and resists chemical damage. Its hardness reduces wear over time, lowering replacement costs. It is lighter than metal, improving efficiency in moving parts.
What industries use these parts?
Industries like aerospace, medical devices, automotive, and electronics rely on zirconia ceramic parts. Common uses include bearings, valves, cutting tools, and implants. Its biocompatibility makes it safe for medical applications. Its precision suits machinery requiring tight tolerances.
Can these parts be customized?
Yes. Manufacturers adjust size, shape, and surface finish to meet specific needs. Advanced grinding and polishing ensure micron-level accuracy. Custom designs fit unique machinery or experimental projects. Technical support helps optimize part performance for different applications.
How should zirconia ceramic parts be handled?
Avoid dropping or striking parts on hard surfaces. While tough, sudden impacts may cause cracks. Clean parts with non-abrasive materials to prevent surface scratches. Store them in dry conditions to avoid contamination. Follow manufacturer guidelines for installation and maintenance.
(Custom Industrial High Precision High Hardness Polish Zirconia Ceramic Parts Zirconium Oxide Ceramic)
REQUEST A QUOTE
RELATED PRODUCTS
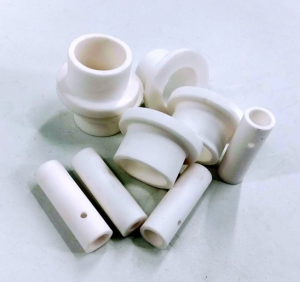
High Wear Resistance Zirconia Ceramic Tube ZrO2 Ceramic Pipe
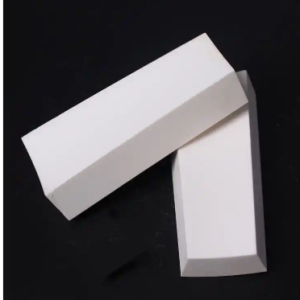
Zirconia AZS Refractory Brick sintered zirconia brick
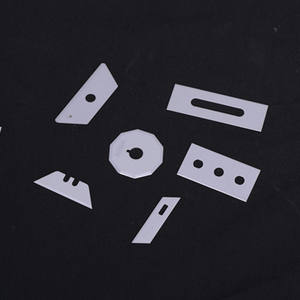
Ultra Precise Machining White Zirconia ZrO2 Tiny Ceramic Tube High End Zirconium Oxide Ceramic Small Components
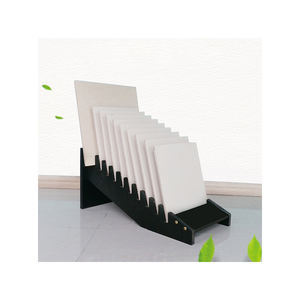
High Hardness Polished Zirconia Ceramic Plate Zirconium Oxide Porcelain Parts Zro2 Ceramic Sleeve
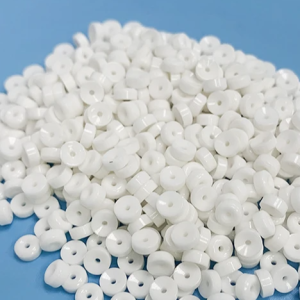
Refractory zirconia ceramic nozzle for Tundish Nozzles
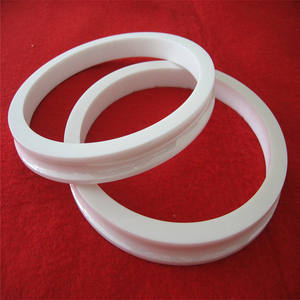