Discover Premium Ceramic Products | Durability & Elegance United | Advanced Ceramics
PRODUCT PARAMETERS
Description
Overview of zirconia brick
Zirconia bricks are a type of advanced refractory material that is highly valued for its excellent thermal stability, high-temperature strength, and resistance to chemical attack. These properties make zirconia bricks indispensable in various industrial applications, especially those involving extreme temperatures and corrosive environments.
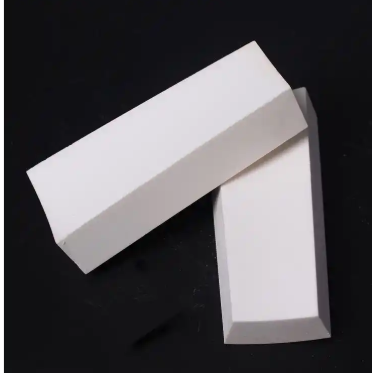
Features of zirconia brick
High Refractoriness
Temperature Resistance: Capable of withstanding extremely high temperatures, typically up to 2400°C (4352°F) or more, depending on composition.
Minimal Deformation: Maintains structural integrity under prolonged exposure to high temperatures without significant deformation.
Excellent Thermal Shock Resistance
Rapid Temperature Changes: Can endure sudden and extreme temperature fluctuations without cracking or spalling.
Low Coefficient of Thermal Expansion: Minimizes thermal stresses during heating and cooling cycles.
Superior Chemical Stability
Resistance to Corrosion: Highly resistant to most molten metals, slags, acids, and alkalis.
Inertness: Does not react with many chemicals, making it ideal for use in corrosive environments.
Low Thermal Conductivity
Heat Retention: Acts as an effective insulator, helping to retain heat within furnaces and reducing energy losses.
Energy Efficiency: Contributes to improved energy efficiency by minimizing the amount of heat escaping from the system.
High Mechanical Strength
Compressive Strength: Exhibits excellent resistance to crushing forces, ensuring durability under heavy loads.
Wear Resistance: Resistant to wear and abrasion, extending the service life of the refractory lining.
Phase Stability
Stabilized Zirconia: Through the addition of stabilizers like yttria (Y2O3), magnesia (MgO), or calcium (CaO), the phase transformation of zirconia is prevented, maintaining its volume stability at high temperatures.
Precision Manufacturing
Tight Tolerances: Can be manufactured to precise dimensions and shapes, ensuring accurate fit and minimal gaps in construction.
Surface Finish: Available with smooth surfaces that can reduce material adhesion and facilitate cleaning.
Environmental Compatibility
Non-Toxic: Generally non-toxic and environmentally friendly, suitable for use in various industrial applications.
Recyclability: Some forms of zirconia bricks can be recycled or reused, contributing to sustainability efforts.
Versatility
Wide Range of Applications: Suitable for a broad spectrum of industries, including metallurgy, glass manufacturing, ceramics, chemical processing, and advanced materials research.
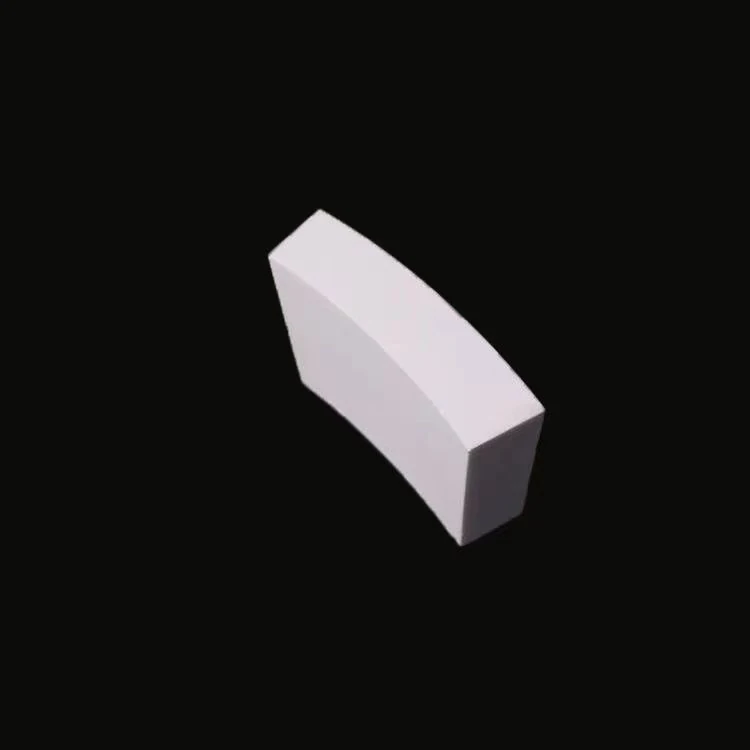
Specifications of zirconia brick
Parameter | Description | Typical Values/Range |
Chemical Composition | Primary components | ZrO2 ≥ 92%, Stabilizers (Y2O3, MgO, CaO) |
Density | Mass per unit volume | 5.8 – 6.1 g/cm³ |
Apparent Porosity | Percentage of void space | ≤ 15% |
Refractoriness Under Load (RUL) | Temperature at which the brick deforms under load | > 1700°C |
Cold Crushing Strength (CCS) | Resistance to crushing at room temperature | 100 – 300 MPa |
Thermal Expansion Coefficient | Rate of expansion with temperature increase | 7 – 10 × 10⁻⁶ /°C |
Thermal Conductivity | Ability to conduct heat | Low, typically < 2.0 W/m·K at 1000°C |
Thermal Shock Resistance | Ability to withstand rapid temperature changes | Excellent |
Resistance to Slag Erosion | Resistance to erosion by molten slag | High |
Corrosion Resistance | Resistance to chemical attack | Excellent resistance to acids, alkalis, and molten metals |
Size and Shape | Dimensions and shapes available | Standard brick sizes, custom shapes available |
Surface Finish | Smoothness or roughness of the surface | Smooth finish, can be customized |
Phase Stability | Stability of zirconia phases at high temperatures | Tetragonal or cubic phase stabilized |
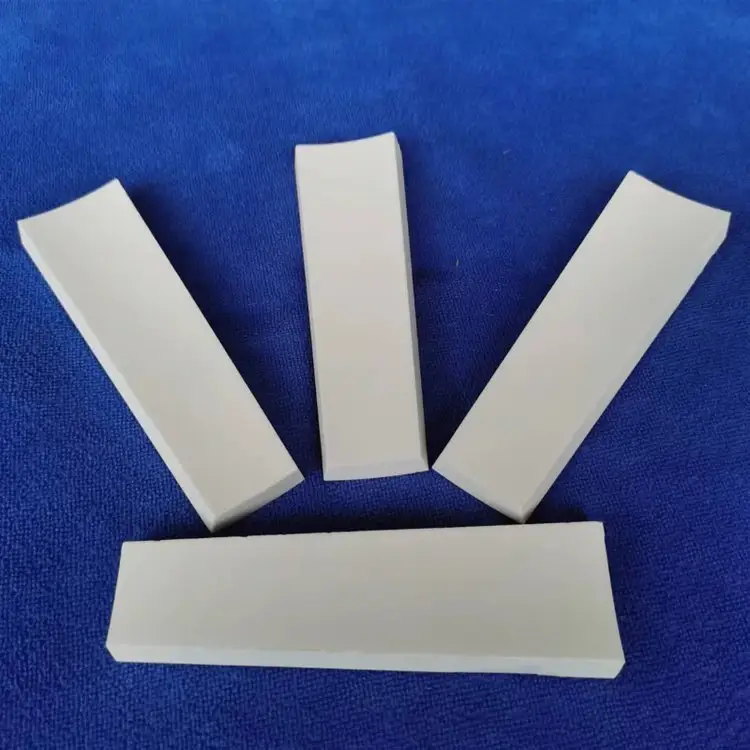
Zirconia ball
Manufacturing Methods of Zirconia Brick
Mixing: High-purity zirconia powder is mixed with stabilizers and binders.
Forming: The mixture is then formed into brick shapes using methods like pressing, extrusion, or slip casting.
Drying: The green bodies are dried to remove any residual moisture.
Sintering: The dried bricks undergo sintering at very high temperatures (typically between 1500°C and 1700°C) to achieve high density and strength.
Finishing: Depending on the application, the bricks may be machined or polished to precise dimensions and tolerances.
Applications of zirconia brick
Metallurgical Industry
Furnace Linings: Used in linings of metallurgical furnaces, including electric arc furnaces (EAF), blast furnaces, and ladles, due to their high refractoriness and resistance to molten metals.
Slag Lines and Taps: Installed in areas exposed to slag and metal flows, where they provide excellent protection against erosion and corrosion.
Glass Industry
Melting Tanks: Ideal for constructing glass melting tanks because of their resistance to glass corrosion and chemical attack.
Channels and Forehearths: Used in channels and forehearths where molten glass flows, ensuring minimal contamination and extended service life.
Ceramic Industry
Kilns and Firing Chambers: Employed in kilns and firing chambers where ceramics are processed at high temperatures, providing thermal stability and low thermal conductivity.
Crucibles and Muffles: Utilized in crucibles and muffle furnaces for ceramic processing, offering superior durability and heat retention.
Chemical Processing
Reactors and Vessels: Applied in reactors and vessels that handle aggressive chemicals, thanks to their chemical inertness and resistance to corrosive environments.
Pipes and Ducts: Used in pipes and ducts exposed to corrosive gases and liquids, providing long-lasting protection.
Advanced Materials Research
Experimental Furnaces: Used in experimental setups requiring stable, high-performance refractories, such as research on new materials or processes.
High-Temperature Testing: Essential for testing materials under extreme conditions, ensuring accurate and reliable results.
Petroleum and Petrochemical Industry
Reformer Tubes: Used in reformer tubes where they withstand high temperatures and corrosive gases.
Catalytic Converters: Applied in catalytic converters for their ability to handle harsh operating conditions.
Environmental Engineering
Incinerators: Utilized in incinerators designed to handle hazardous waste, providing resistance to corrosive ash and fumes.
Waste Gas Treatment: Used in systems for treating waste gases, ensuring durability and efficiency.
Specialty Applications
Nuclear Industry: Employed in certain nuclear applications where high-temperature stability and radiation resistance are critical.
Aerospace and Defense: Used in specialized components requiring high performance under extreme conditions, such as engine parts and heat shields.
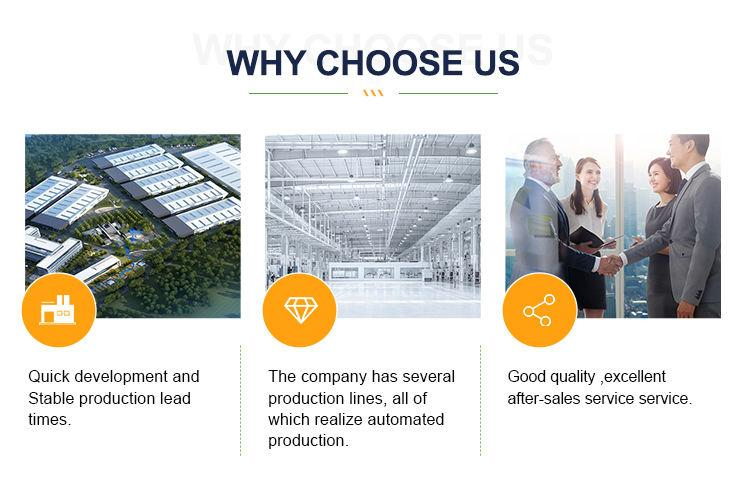
Company Profile
Advanced Ceramics founded on October 17, 2014, is a high-tech enterprise committed to the research and development, production, processing, sales and technical services of ceramic relative materials and products.. Since its establishment in 2014, the company has been committed to providing customers with the best products and services, and has become a leader in the industry through continuous technological innovation and strict quality management.
Our products includes but not limited to Silicon carbide ceramic products, Boron Carbide Ceramic Products, Boron Nitride Ceramic Products, Silicon Carbide Ceramic Products, Silicon Nitride Ceramic Products, Zirconium Dioxide Ceramic Products, Quartz Products, etc. Please feel free to contact us.(nanotrun@yahoo.com)
Payment Methods
T/T, Western Union, Paypal, Credit Card etc.
Shipment Methods
By air, by sea, by express, as customers request.
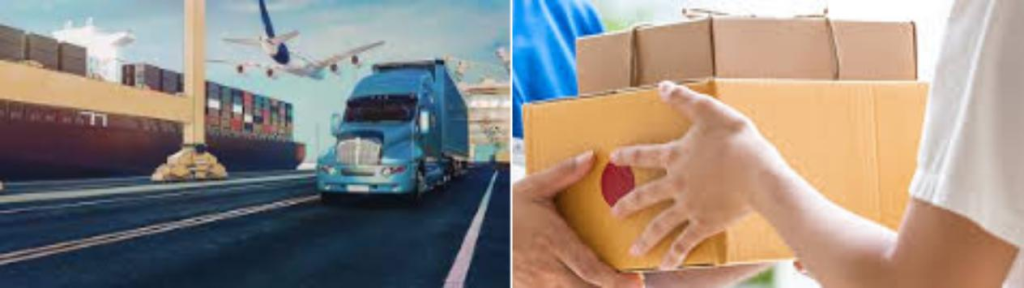
FAQs of Zirconia brick
1. What are zirconia bricks?
A: Zirconia bricks are advanced refractory materials primarily composed of zirconium dioxide (ZrO2), often stabilized with additives like yttria (Y2O3), magnesia (MgO), or calcium (CaO). They are known for their high refractoriness, excellent thermal shock resistance, and superior chemical stability.
2. Why are zirconia bricks stabilized?
A: Stabilization prevents the phase transformation of zirconia from tetragonal or cubic phases back to the monoclinic phase, which can cause volume changes and potential cracking. Stabilizers help maintain structural integrity at high temperatures.
3. How do zirconia bricks compare to other refractory materials?
A: Zirconia bricks generally offer superior performance compared to traditional refractories, especially in terms of durability, thermal shock resistance, and chemical stability. However, they can be more expensive.
4. Are zirconia bricks environmentally friendly?
A: Generally, zirconia bricks are non-toxic and environmentally friendly. Some forms can be recycled or reused, contributing to sustainability efforts.
5. What are the key properties of zirconia bricks?
A: Key properties include high refractoriness (up to 2400°C), excellent thermal shock resistance, superior chemical stability, low thermal conductivity, and high mechanical strength.
REQUEST A QUOTE
RELATED PRODUCTS

High Polishing Insulator Yttrium Stabilized Zirconia Ceramic Rod Zirconia Industrial Ceramic Column
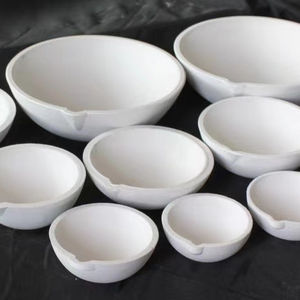
High Temperature Y2O3 Zro2 Zirconia Ceramic Crucible
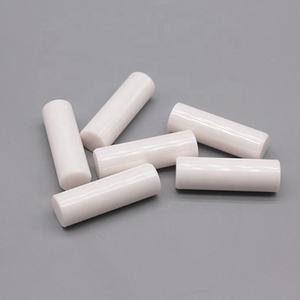
ZrO2 Zirconia Ceramic Plunger With Metal
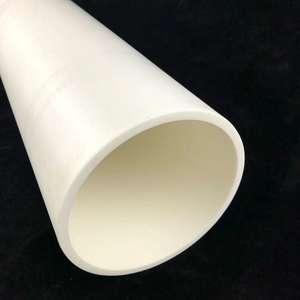
Industrial Grade Zirconia Zirconium Dioxide (Zro2) at 99.95% High Purity for Piezoelectric Ceramics
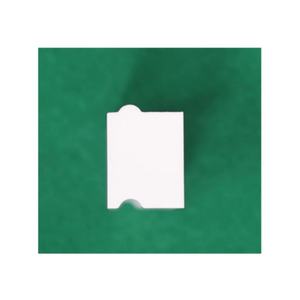
2mm 3mm 4mm Polished Alumina And Zirconia Ceramic Rods
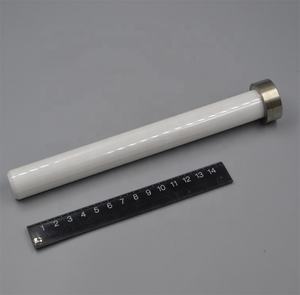